Die Casting Mold
Our experienced engineers leverage the latest CAD/CAM and CNC machining to produce high-quality, durable molds optimized for your application. We offer complete mold design services including manufacturability analysis, simulation, and prototyping to ensure flawless mold performance. With advanced equipment and expertise, Moldie delivers complex, tight-tolerance die casting molds tailored to your specifications. Our molds enable quick, efficient production of premium die cast parts in large quantities.
Contact Moldie today to get started on your custom die casting mold project.
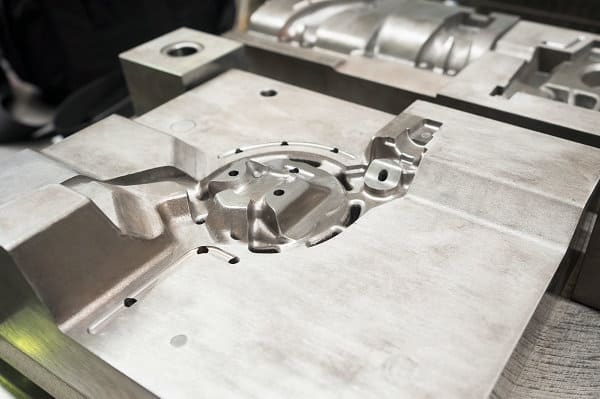
Request a Quote
What is a Die Casting Mold?
A die casting mold is a precision tool used to produce metal parts through die casting, an efficient manufacturing process where molten metal is injected under high pressure into the mold cavity. The mold consists of two halves – a fixed half and a movable half. When closed, the cavity between them forms the desired shape of the casting part.
Die casting molds are made from tool steel or aluminum and can produce complex geometries with excellent accuracy, repeatability, and surface finishes. They are widely used to produce metal parts for the automotive, aerospace, and consumer products industries.
Die Casting Mold Design
The design of a die casting mold requires advanced engineering to achieve the tight tolerances needed for quality castings. Key design factors include:
- Parting lines: The separation line between the two mold halves must allow for easy part ejection. Parting lines are placed to avoid undercuts.
- Draft angles: All vertical surfaces must have a slight taper (draft angle) to facilitate ejection. Common draft angles are 1-3 degrees.
- Ejection system: Ejector pins and sleeves are incorporated into the mold to push the solidified casting out of the cavity.
- Cooling system: Channels are drilled in the mold to circulate water or oil to extract heat and solidify the casting quickly.
- Clamping system: Clamps hold the two halves aligned under tremendous pressure during injection.
- Gate and runner system: Channels that deliver molten metal into the cavity.
Die Casting Mold Manufacturing
Quality die casting molds require expert machining and polishing to achieve micron level precision. The manufacturing steps include:
- Creation of CAD models based on part drawings.
- CNC machining of mold blocks from steel or aluminum.
- Additional CNC processes like milling, drilling, and grinding to achieve final mold geometry.
- Hand polishing and benching to obtain the required surface finish.
- Assembly of the two mold halves and incorporation of ejectors, cooling, and clamping.
The whole mold making process can take weeks or months for complex molds. Proper mold design and machining is critical for producing accurate, consistent die cast parts.
Benefits of Die Casting Molds
- High-volume production with faster cycles and lower labor compared to other processes.
- Excellent dimensional accuracy and repeatability.
- Smooth surface finishes without secondary machining.
- Ability to produce complex shapes not possible with other methods.
- Variety of alloy options including aluminum, zinc, and magnesium.
- Lower tooling costs compared to plastic injection molding.
With careful design and machining, die casting molds can produce millions of precision metal parts over many years of service. They are one of the most efficient and cost-effective ways to manufacture metal components.
Contact Moldie today to get started on your custom die casting mold project.