Molde de fundición a presión
Nuestros ingenieros experimentados aprovechan lo último en mecanizado CAD/CAM y CNC para producir moldes duraderos y de alta calidad optimizados para su aplicación. Ofrecemos servicios completos de diseño de moldes que incluyen análisis de capacidad de fabricación, simulación y creación de prototipos para garantizar un rendimiento impecable del molde. Con equipos avanzados y experiencia, Moldie ofrece moldes de fundición a presión complejos y de tolerancia estricta adaptados a sus especificaciones. Nuestros moldes permiten una producción rápida y eficiente de piezas fundidas a presión de primera calidad en grandes cantidades.
Póngase en contacto con Moldie hoy para comenzar con su proyecto de molde de fundición a presión personalizado.
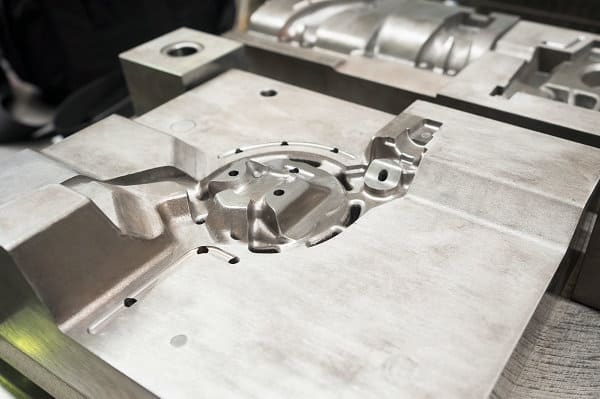
Solicitar presupuesto
¿Qué es un molde de fundición a presión?
Un molde de fundición a presión es una herramienta de precisión que se utiliza para producir piezas de metal mediante fundición a presión, un proceso de fabricación eficiente en el que se inyecta metal fundido a alta presión en la cavidad del molde. El molde consta de dos mitades: una mitad fija y una mitad móvil. Cuando está cerrado, la cavidad entre ellas forma la forma deseada de la pieza fundida.
Los moldes de fundición a presión están hechos de acero para herramientas o aluminio y pueden producir geometrías complejas con excelente precisión, repetibilidad y acabados superficiales. Se utilizan ampliamente para producir piezas metálicas para las industrias automotriz, aeroespacial y de productos de consumo.
Diseño de moldes de fundición a presión
El diseño de un molde de fundición a presión requiere ingeniería avanzada para lograr las estrictas tolerancias necesarias para piezas fundidas de calidad. Los factores clave de diseño incluyen:
- líneas de separación: La línea de separación entre las dos mitades del molde debe permitir una fácil expulsión de la pieza. Se colocan líneas de separación para evitar socavaduras.
- Ángulos de salida: Todas las superficies verticales deben tener una ligera inclinación (ángulo de tiro) para facilitar la expulsión. Los ángulos de inclinación comunes son de 1 a 3 grados.
- Sistema de expulsión: Se incorporan pasadores eyectores y manguitos al molde para empujar la pieza solidificada fuera de la cavidad.
- Sistema de refrigeración: Se perforan canales en el molde para hacer circular agua o aceite para extraer calor y solidificar la pieza fundida rápidamente.
- Sistema de sujeción: Las abrazaderas mantienen las dos mitades alineadas bajo una tremenda presión durante la inyección.
- Sistema de puerta y corredor: Canales que entregan metal fundido a la cavidad.
Fabricación de moldes de fundición a presión
Los moldes de fundición a presión de calidad requieren un mecanizado y pulido expertos para lograr una precisión de nivel micrométrico. Los pasos de fabricación incluyen:
- Creación de modelos CAD basados en dibujos de piezas.
- Mecanizado CNC de bloques de molde de acero o aluminio.
- Procesos CNC adicionales como fresado, taladrado y rectificado para lograr la geometría final del molde.
- Pulido y banqueado a mano para obtener el acabado superficial requerido.
- Montaje de las dos mitades del molde e incorporación de eyectores, refrigeración y sujeción.
Todo el proceso de fabricación de moldes puede tardar semanas o meses en el caso de moldes complejos. El diseño y el mecanizado adecuados del molde son fundamentales para producir piezas fundidas a presión precisas y consistentes.
Beneficios de los moldes de fundición a presión
- Producción de alto volumen con ciclos más rápidos y menor mano de obra en comparación con otros procesos.
- Excelente precisión dimensional y repetibilidad.
- Acabados superficiales lisos sin mecanizado secundario.
- Capacidad para producir formas complejas que no es posible con otros métodos.
- Variedad de opciones de aleaciones que incluyen aluminio, zinc y magnesio.
- Costos de herramientas más bajos en comparación con el moldeo por inyección de plástico.
Con un diseño y mecanizado cuidadosos, los moldes de fundición a presión pueden producir millones de piezas metálicas de precisión durante muchos años de servicio. Son una de las formas más eficientes y rentables de fabricar componentes metálicos.
Póngase en contacto con Moldie hoy para comenzar con su proyecto de molde de fundición a presión personalizado.