Stampo per pressofusione
I nostri ingegneri esperti sfruttano le più recenti lavorazioni CAD/CAM e CNC per produrre stampi durevoli e di alta qualità ottimizzati per la vostra applicazione. Offriamo servizi completi di progettazione di stampi, tra cui analisi di producibilità, simulazione e prototipazione per garantire prestazioni impeccabili dello stampo. Con attrezzature e competenze avanzate, Moldie fornisce stampi per pressofusione complessi e con tolleranze strette su misura per le vostre specifiche. I nostri stampi consentono una produzione rapida ed efficiente di parti pressofuse di alta qualità in grandi quantità.
Contatta Moldie oggi stesso per iniziare il tuo progetto di stampo per pressofusione personalizzato.
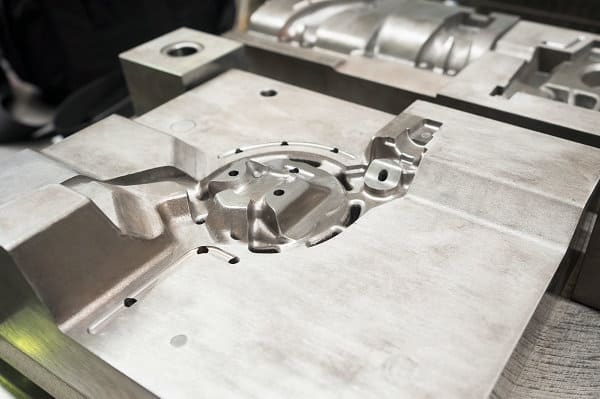
Richiedi un preventivo
Cos'è uno stampo per pressofusione?
Uno stampo per pressofusione è uno strumento di precisione utilizzato per produrre parti metalliche tramite pressofusione, un processo di produzione efficiente in cui il metallo fuso viene iniettato ad alta pressione nella cavità dello stampo. Lo stampo è costituito da due metà: una metà fissa e una metà mobile. Quando è chiusa, la cavità tra di esse forma la forma desiderata della parte di fusione.
Gli stampi per pressofusione sono realizzati in acciaio per utensili o alluminio e possono produrre geometrie complesse con precisione, ripetibilità e finiture superficiali eccellenti. Sono ampiamente utilizzati per produrre parti metalliche per l'industria automobilistica, aerospaziale e dei prodotti di consumo.
Progettazione di stampi per pressofusione
La progettazione di uno stampo per pressofusione richiede un'ingegneria avanzata per ottenere le tolleranze strette necessarie per getti di qualità. I fattori chiave di progettazione includono:
- Linee di divisione: La linea di separazione tra le due metà dello stampo deve consentire una facile espulsione del pezzo. Le linee di divisione sono posizionate per evitare sottosquadri.
- Angoli di sformo: Tutte le superfici verticali devono avere una leggera rastremazione (angolo di sformo) per facilitare l'espulsione. Gli angoli di sformo comuni sono 1-3 gradi.
- Sistema di espulsione: I perni e i manicotti dell'espulsore sono incorporati nello stampo per spingere il getto solidificato fuori dalla cavità.
- Sistema di raffreddamento: Nello stampo vengono praticati dei canali per far circolare l'acqua o l'olio per estrarre il calore e solidificare rapidamente la fusione.
- Sistema di bloccaggio: I morsetti mantengono le due metà allineate sotto un'enorme pressione durante l'iniezione.
- Sistema di cancelli e guide: Canali che trasportano il metallo fuso nella cavità.
Produzione di stampi per pressofusione
Gli stampi per pressofusione di qualità richiedono lavorazione e lucidatura esperte per ottenere una precisione a livello di micron. Le fasi di produzione includono:
- Creazione di modelli CAD basati sui disegni delle parti.
- Lavorazione CNC di blocchi di stampi in acciaio o alluminio.
- Ulteriori processi CNC come fresatura, foratura e rettifica per ottenere la geometria finale dello stampo.
- Lucidatura e pancatura manuale per ottenere la finitura superficiale richiesta.
- Assemblaggio delle due metà dello stampo e incorporazione di espulsori, raffreddamento e bloccaggio.
L'intero processo di realizzazione degli stampi può richiedere settimane o mesi per stampi complessi. La corretta progettazione e lavorazione dello stampo sono fondamentali per la produzione di parti pressofuse precise e uniformi.
Vantaggi degli stampi per pressofusione
- Produzione ad alto volume con cicli più rapidi e manodopera inferiore rispetto ad altri processi.
- Eccellente precisione dimensionale e ripetibilità.
- Finiture superficiali lisce senza lavorazione secondaria.
- Capacità di produrre forme complesse non possibili con altri metodi.
- Varietà di opzioni di leghe tra cui alluminio, zinco e magnesio.
- Costi di attrezzaggio inferiori rispetto allo stampaggio a iniezione di plastica.
Con un'attenta progettazione e lavorazione, gli stampi per pressofusione possono produrre milioni di parti metalliche di precisione nel corso di molti anni di servizio. Sono uno dei modi più efficienti ed economici per produrre componenti metallici.
Contatta Moldie oggi stesso per iniziare il tuo progetto di stampo per pressofusione personalizzato.