Moule de coulée sous pression
Nos ingénieurs expérimentés exploitent les derniers usinages CAO/FAO et CNC pour produire des moules durables et de haute qualité optimisés pour votre application. Nous proposons des services complets de conception de moules, y compris l'analyse de fabricabilité, la simulation et le prototypage pour garantir des performances irréprochables du moule. Avec un équipement et une expertise avancés, Moldie fournit des moules de coulée sous pression complexes et à tolérances serrées, adaptés à vos spécifications. Nos moules permettent une production rapide et efficace de pièces moulées sous pression de qualité supérieure en grande quantité.
Contactez Moldie dès aujourd'hui pour commencer votre projet de moule de moulage sous pression personnalisé.
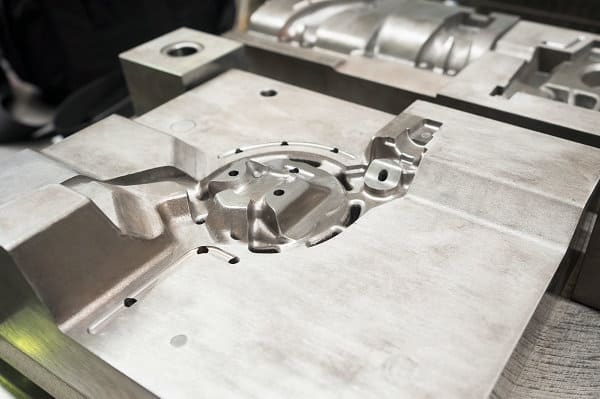
Demander un devis
Qu'est-ce qu'un moule de moulage sous pression ?
Un moule de moulage sous pression est un outil de précision utilisé pour produire des pièces métalliques par moulage sous pression, un processus de fabrication efficace où le métal en fusion est injecté sous haute pression dans la cavité du moule. Le moule se compose de deux moitiés : une moitié fixe et une moitié mobile. Une fois fermée, la cavité entre les deux forme la forme souhaitée de la pièce moulée.
Les moules de moulage sous pression sont fabriqués en acier à outils ou en aluminium et peuvent produire des géométries complexes avec une excellente précision, répétabilité et finitions de surface. Ils sont largement utilisés pour produire des pièces métalliques destinées aux secteurs de l’automobile, de l’aérospatiale et des produits de consommation.
Conception de moules de moulage sous pression
La conception d'un moule de coulée sous pression nécessite une ingénierie avancée pour atteindre les tolérances serrées nécessaires à des pièces moulées de qualité. Les principaux facteurs de conception comprennent :
- Lignes de séparation: La ligne de séparation entre les deux moitiés du moule doit permettre une éjection aisée des pièces. Les lignes de séparation sont placées pour éviter les contre-dépouilles.
- Angles de dépouille: Toutes les surfaces verticales doivent avoir une légère conicité (angle de dépouille) pour faciliter l'éjection. Les angles de dépouille courants sont de 1 à 3 degrés.
- Système d'éjection: Des broches et des manchons d'éjection sont incorporés dans le moule pour pousser la pièce moulée solidifiée hors de la cavité.
- Système de refroidissement: Des canaux sont percés dans le moule pour faire circuler de l'eau ou de l'huile afin d'extraire la chaleur et de solidifier rapidement la pièce moulée.
- Système de serrage: Les pinces maintiennent les deux moitiés alignées sous une pression énorme pendant l'injection.
- Système de portail et de coulisse: Canaux qui amènent le métal en fusion dans la cavité.
Fabrication de moules de moulage sous pression
Les moules de moulage sous pression de qualité nécessitent un usinage et un polissage experts pour atteindre une précision au micron. Les étapes de fabrication comprennent :
- Création de modèles CAO basés sur des dessins de pièces.
- Usinage CNC de blocs de moules en acier ou en aluminium.
- Processus CNC supplémentaires tels que le fraisage, le perçage et le meulage pour obtenir la géométrie finale du moule.
- Polissage à la main et mise au banc pour obtenir la finition de surface requise.
- Assemblage des deux moitiés de moule et incorporation des éjecteurs, refroidissement et serrage.
L’ensemble du processus de fabrication des moules peut prendre des semaines, voire des mois pour les moules complexes. Une conception et un usinage appropriés du moule sont essentiels pour produire des pièces moulées sous pression précises et cohérentes.
Avantages des moules de moulage sous pression
- Production en grand volume avec des cycles plus rapides et une main d'œuvre réduite par rapport aux autres processus.
- Excellente précision dimensionnelle et répétabilité.
- Finitions de surface lisses sans usinage secondaire.
- Capacité à produire des formes complexes impossibles avec d’autres méthodes.
- Variété d'options d'alliages, notamment l'aluminium, le zinc et le magnésium.
- Coûts d’outillage inférieurs à ceux du moulage par injection plastique.
Avec une conception et un usinage soignés, les moules de moulage sous pression peuvent produire des millions de pièces métalliques de précision sur de nombreuses années de service. Ils constituent l’un des moyens les plus efficaces et les plus rentables de fabriquer des composants métalliques.
Contactez Moldie dès aujourd'hui pour commencer votre projet de moule de moulage sous pression personnalisé.