Moulage par injection personnalisé
Avec des outils d'usinage haut de gamme, nous fabriquons des pièces de manière experte pour correspondre à vos tolérances et normes de qualité requises. Nous testons tous les produits pour nous assurer qu'ils correspondent aux spécifications de votre secteur et de votre application.
Nos capacités et nos capacités nous permettent de fournir les meilleurs services de moulage par injection personnalisés de leur catégorie. Nous travaillons en étroite collaboration avec chaque client pour comprendre son projet et les guider dans la sélection des moules et des conceptions personnalisés appropriés.
Que vous ayez besoin d'un petit lot de pièces prototypes ou d'une production à grande échelle, nous proposons des solutions personnalisées adaptées à vos besoins. Notre expertise en moulage sur mesure nous permet de fabriquer de manière constante des composants de haute qualité qui soutiennent le succès de votre entreprise.
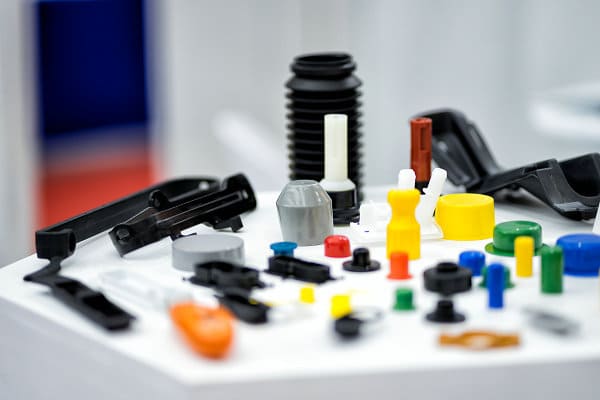
Demander un devis
Moulage par injection personnalisé
Le moulage par injection est un processus de fabrication rentable pour de grands volumes de pièces en plastique personnalisées. Le processus de moulage par injection consiste à insérer du plastique fondu dans un outil de moulage et à retirer ensuite la section solidifiée. Le cycle se répète plusieurs fois, abaissant le coût du moulage et, par conséquent, le prix de chaque unité.
Parce que le processus de moulage par injection utilise un outil de moulage similaire pour chaque pièce, il offre une qualité constante dans chaque produit. De plus, le moulage par injection a une grande variété de vernis, de matériaux, de cosmétiques et de couleurs par rapport à l'impression 3D ou à l'usinage CNC.
Les services de moulage par injection de plastique personnalisés de Moldie sont uniques en leur genre. Nous offrons des services exceptionnels qui dépassent les attentes de nos clients. Après avoir reçu votre commande, nous trouvons le fournisseur de moulage par injection approprié pour mouler les pièces comme vous le souhaitez, au prix approprié et sans compromettre la conception.
De plus, nous offrons des services flexibles. Nous avons des outils sophistiqués, une équipe de professionnels et des ressources qui fournissent des pièces personnalisées à des clients de diverses industries. De plus, nous travaillons dans des délais courts. Tous nos processus sont rationalisés. Cela garantit que vous recevez votre commande dans les délais souhaités.
Les avantages du moulage par injection personnalisé
Le moulage par injection de plastique offre de nombreux avantages, notamment :
1. C'est rentable
Le moulage par injection de plastique est un processus automatisé. Par conséquent, les coûts de main-d'œuvre sont relativement faibles par rapport aux autres méthodes de fabrication du plastique. De plus, le moulage par injection produit les pièces à un niveau élevé avec un rendement élevé, réduisant ainsi les coûts de fabrication grâce à son efficacité.
2. Le moulage par injection de plastique offre une résistance améliorée
Les pièces moulées par injection de plastique résultantes du processus d'injection ont une résistance accrue. En effet, vous pouvez utiliser des charges dans des moules à injection. Ces charges réduisent la densité plastique lors du moulage et ajoutent une plus grande résistance aux pièces moulées.
3. Il offre une flexibilité dans le matériau et la couleur
De nos jours, de nombreux matériaux sont compatibles avec le procédé de moulage par injection plastique. Avec toutes les options disponibles, vous pouvez facilement choisir un matériau avec les propriétés chimiques, physiques et mécaniques appropriées. En dehors de cela, vous pouvez colorer les plastiques en utilisant plusieurs systèmes de coloration.
4. Le moulage par injection de plastique prend en charge des géométries complexes avec des tolérances serrées
Le moulage par injection sur mesure permet la génération de pièces complexes à grand volume et cohérentes. Pour maximiser l'efficacité du moulage par injection à grand volume et optimiser la précision et la qualité de vos portions, vous devez tenir compte des éléments de conception. Avec la conception appropriée, vous pouvez produire des pièces de haute qualité de manière constante.
Avec le moulage par injection, vous pouvez obtenir rapidement des pièces reproductibles avec des tolérances serrées, vous fournissant des produits précis pour de nombreuses applications et comparables aux pièces de machines CNC.
5. Conduit à une réduction des déchets
Le processus de moulage par injection de plastique génère moins de déchets de matériaux post-production que la fabrication conventionnelle. En outre, vous pouvez réaffûter et recycler tout déchet de plastique pour une utilisation future.
6. Le moulage en plastique personnalisé offre plusieurs finitions
La plupart des pièces moulées présentent une finition de surface douce, presque identique à l'aspect final souhaité. Cependant, une apparence lisse ne convient que pour certaines applications. En fonction des propriétés du matériau, la méthode de moulage par injection produit des finitions qui ne nécessitent pas d'actions secondaires. Vous pouvez ajouter des textures uniques, avoir des finitions mates ou des gravures.
7. Il offre une grande répétabilité
Un autre avantage important du moulage par injection personnalisé est qu'il est hautement reproductible. Après avoir créé votre moule, vous pouvez générer de nombreuses pièces similaires avant de procéder à la maintenance de votre outil. Cela se traduit par un faible coût de production.
8. C'est très efficace avec une production rapide
Le moulage par injection personnalisé fait partie des méthodes de production les plus rapides. La production est élevée, ce qui la rend plus efficace et rentable. Généralement, la vitesse dépend de la complexité de la conception et de la taille de votre moule, mais un moule typique prend environ 5 à 20 minutes.
Cela favorise la production de plus de moules en un temps limité, augmentant ainsi les marges bénéficiaires. De plus, certains moules ont plusieurs cavités, ce qui entraîne la production de plus de pièces en un seul cycle de moulage.
Capacités de moulage par injection
En ce qui concerne les capacités d'injection plastique personnalisées, nous sommes fiers d'être parmi les meilleures entreprises de moulage par injection qui fournissent des pièces uniques et définies avec précision qui peuvent améliorer les machines et les procédures dans diverses entreprises essentielles à l'échelle mondiale.
Nos capacités de moulage par injection nous permettent de produire des pièces de forme distincte qui ne peuvent pas être créées à l'aide d'autres méthodes. Nous utilisons des machines à cavités multiples, simples et familiales pour produire des produits moulés par injection de haute qualité de manière rentable.
De plus, nous travaillons en étroite collaboration avec vous pour planifier et organiser des solutions innovantes. Nous sommes experts dans la conversion métal-plastique, la durabilité et la conception de composants, réduisant le temps et les coûts de production tout en améliorant l'efficacité. Nous sommes connus pour notre procédure particulière visant à réduire les coûts et les délais et à augmenter les capacités de production de différentes industries.
Processus de moulage par injection
Le moulage par injection de plastique sur mesure nécessite trois éléments fondamentaux : une matière plastique brute, une machine de moulage par injection et un moule. Les moules pour l'injection de plastique sont constitués d'éléments en acier et en aluminium à haute résistance programmés pour fonctionner en deux moitiés. Chaque moitié s'assemble à l'intérieur de la machine de moulage pour former une pièce en plastique sur mesure.
Après cela, la machine injecte du plastique fondu dans le moule, où il se solidifie pour former le produit final. Le processus de moulage par injection sur mesure suit des spécifications strictes et se déroule selon les étapes suivantes :
1. Serrage
La première étape du procédé de moulage par injection est le serrage. Généralement, les moules à injection sont constitués de deux moitiés. Dans cette étape, la machine ferme ces moitiés avant que le plastique ne soit inséré dans le moule pour empêcher le moule de s'ouvrir pendant l'étape d'injection.
2. Injection
Dans cette étape, le plastique brut, généralement sous la forme de petites pastilles, est inséré dans la machine de moulage par injection au niveau de la section de la zone d'alimentation d'une vis alternative. La température et la compression chauffent la matière plastique lorsque la vis transmet les granulés de plastique à travers les zones chauffées du cylindre de la machine.
La quantité de plastique fondu transmise à l'avant de la vis est mesurée avec précision puisque c'est la quantité qui formera la pièce finale après injection.
Lorsque la quantité appropriée de granulés de plastique fondus arrive à l'avant de la vis et que le moule est bien serré, la machine l'insère dans le moule, le conduisant à la dernière partie de la cavité sous haute pression.
3. Refroidissement
Une fois que le plastique fondu touche les surfaces internes du moule, il refroidit. La méthode de refroidissement solidifie la forme et la ténacité de la pièce en plastique fraîchement moulée. Le temps de refroidissement requis pour chaque pièce moulée en plastique dépend de l'épaisseur de la paroi, des propriétés thermodynamiques du plastique et des besoins dimensionnels des pièces personnalisées.
4. Éjection
Après refroidissement, la machine débride et ouvre le moule d'injection plastique. Le dispositif est équipé de dispositifs mécaniques qui fonctionnent avec des composants développés dans le moule d'injection plastique pour retirer la pièce. À ce stade, la pièce moulée sur mesure est expulsée et le moule est prêt pour le mouvement suivant lorsque la nouvelle pièce est complètement éjectée.
Matériaux de moulage par injection plastique personnalisés
Les matériaux de moulage par injection de plastique personnalisés sont classés de la manière suivante :
1. Matières plastiques rigides
Voici quelques matériaux dans cette catégorie :
- Polyacrylamide (PARA)
Ceci est principalement mélangé avec des remplissages comme des fibres minérales ou du verre. Il génère des sections rigides avec un faible fluage et un taux d'absorption d'eau plus lent que le nylon. PARA est parfait pour les éléments structurels de l'électronique médicale et des appareils portables.
- Polycarbonate (PC)
Le PC est une alternative matérielle légère, transparente et durable au verre. En raison de sa grande durabilité et de sa résistance extrême aux chocs, la plupart des industries utilisent les PC dans plusieurs applications, notamment les appareils électroniques, les objectifs, les équipements de sécurité, etc.
- Polyéthylène (PE)
Il s'agit d'un polymère de qualité grand public que vous pouvez choisir en fonction de sa densité, ce qui en fait l'un des plastiques les plus utilisés au monde. Vous pouvez avoir une basse densité (LDPE), une haute densité (HDPE) ou du polyéthylène téréphtalate (PET, PETE).
Les plastiques PE ont une élasticité, une résistance à l'abrasion et une résistance chimique élevées. Ils sont mieux utilisés pour mouler par injection des articles plus surdimensionnés, souvent utilisés dans les bouteilles, les films, les tubes, les emballages, etc.
- Acrylonitrile butadiène styrène (ABS)
Il s'agit d'un matériau thermoplastique amorphe à bas point de fusion. Il est compatible avec les colorants et contient une myriade d'options de textures et de finitions. L'ABS est très résistant aux chocs et robuste. Cependant, il a une faible résistance aux frottements élevés, aux rayons UV, aux solvants et aux intempéries. De plus, il dégage une forte fumée lorsqu'il est brûlé.
L'ABS est mieux utilisé dans les biens de consommation, les composants et revêtements électroniques, les équipements sportifs et les pièces automobiles.
- Polypropylène (PP)
C'est aussi un autre plastique couramment utilisé dans le monde. Il est principalement similaire au PE mais est plus résistant à la chaleur et légèrement plus dur. Dans le moulage par injection, vous pouvez recycler ce matériau et le combiner avec d'autres matières plastiques. En raison de sa faible densité, le PP est utilisé pour les conteneurs de stockage, les charnières vivantes pour les bouteilles en plastique, les outils électriques et les articles de sport.
- Polyuréthane thermoplastique (TPU)
Le TPU est connu pour sa résistance aux huiles, à l'abrasion et aux produits chimiques et sa capacité à supporter des températures élevées. Il se décline en différentes qualités, y compris médicale, industrielle et commerciale. Ainsi, il convient mieux aux roues, aux chaussures, aux appareils médicaux et aux boîtiers électroniques.
- Polyphtalamide (PPA)
Le PPA est un sous-groupe de nylons qui ont généralement une faible absorption d'humidité et des points de fusion élevés. Il est utilisé dans les applications automobiles et industrielles car il peut résister aux produits chimiques agressifs. De plus, il est bon dans les boîtiers de phares et les collecteurs de carburant.
- Fluorure de polyvinylidène (PVDF)
Il s'agit d'un matériau chimiquement inerte résistant aux hautes températures. En raison de son faible frottement, le PCDF est utilisé dans les roulements, les tubes, les pièces de plomberie, l'isolation des fils électriques et la manipulation de produits chimiques.
- Polyoléfine thermoplastique (TPO)
Le TPO a une bonne résistance chimique et est flexible, mais a une résistance à la température inférieure à celle du PP.
- Styrène acrylonitrile (SNA)
Le SNA est un polystyrène transparent et résistant à la chaleur. Il est populaire dans les ustensiles de cuisine, les poignées de porte et les articles ménagers.
- Chlorure de polyvinyle (PVC)
Il s'agit d'un plastique rigide polyvalent utilisé dans les garnitures, les emballages non alimentaires et la plomberie.
- Sulfure de polyphénylène, Ryton (PPS)
Le PPS est un thermoplastique haute performance très résistant aux solvants.
- Acétal polyoxyméthylène (POM)
Celui-ci a une résistance élevée à l'usure, un faible frottement et une bonne résistance à l'humidité.
- Polystyrène-polyphényléthers (PS-PPE)
Le PS-PPE présente une résistance élevée à la chaleur et aux flammes. De plus, il a une résistance à la traction et une rigidité élevée même lorsqu'il est soumis à des températures élevées.
- Acrylonitrile styrène acrylate (ASA)
Ce matériau est presque le même que l'ABS mais a une plus grande résistance à la décoloration et est donc utilisé à des fins extérieures.
- Polyéthylène basse densité (LDPE)
Un matériau flexible et dur qui ne réagit pas aux alcools, acides et bases. Il convient mieux aux couvercles à pression, aux contenants à usage général et aux plateaux.
- Acétate de cellulose (AC)
CA est un matériau flexible qui peut être utilisé dans le film, les lunettes ou le contact alimentaire.
- Polymère à cristaux liquides (LCP)
LCP offre des caractéristiques uniques pour les composants à parois minces et le micro-moulage. C'est courant dans les dispositifs médicaux, les interconnexions et les connecteurs électriques.
- Polyéthylène haute densité (HDPE)
Il a un rapport résistance/poids et une résistivité chimique parfaits. Le PEHD est principalement utilisé pour les isolateurs de connecteurs, les récipients alimentaires et les réservoirs de carburant. Il peut également être utilisé dans des équipements extérieurs tels que des terrains de jeux.
- Polyamide 6/6, nylon 6 (PA 6/6)
Cela offre une résistance mécanique améliorée, une excellente stabilité à la chaleur, une rigidité et une résistance chimique.
- Polytéréphtalate de butylène (PBT)
Il s'agit d'un isolateur électronique populaire à base de polyester. Il est principalement appliqué dans l'automobile en tant qu'option d'usure plus longue que le nylon.
- Polyéther éther cétone (PEEK)
Le PEEK offre une résistance à la traction exceptionnelle qui dépasse la plupart des plastiques. Pour cette raison, il est principalement utilisé comme alternative légère aux pièces métalliques dans les applications à fortes contraintes et à hautes températures.
- Polycarbonate-acrylonitrile butadiène styrène (PC-ABS)
Comme son nom l'indique, il s'agit d'une combinaison de PC et d'ABS qui donne un thermoplastique technique plus résistant et plus flexible que le polycarbonate ordinaire.
- Polyétherimide (PEI)
Ceci est connu pour sa haute résistance aux flammes et à la chaleur. Il est appliqué dans la plupart des utilisations médicales et est plus rentable que le PEEK.
- Polyéthersulfone (PES)
Le PES est un plastique rigide et transparent, biocompatible, stérilisable et chimiquement inerte. Il convient aux équipements en contact avec les aliments tels que les composants de la machine à café. Il est également applicable dans les industries à forte exposition chimique comme l'automobile et l'aérospatiale.
- Téréphtalate de polycyclohexylènediméthylène (PCT)
Ce matériau a une bonne stabilité environnementale et une faible absorption d'humidité. Il est principalement utilisé dans les commutateurs et les connecteurs.
- Polycarbonate-polyéthylène téréphtalate (PC-PET)
Il s'agit d'une combinaison de PC et de PET pour donner un produit solide et résistant aux produits chimiques et qui peut être utilisé comme substitut du PC-ABS. Il résiste aux produits chimiques et aux solvants agressifs, ce qui le rend parfait pour les applications de soins de santé et les équipements sportifs.
- Polycarbonate-polytéréphtalate de butylène (PC-PBT)
Cela a des caractéristiques similaires au PC-PET et est populaire dans les boîtiers électroniques.
- Polyéthylène téréphtalate (PET)
Aussi connu sous le nom de PETE, le PET est une résine PE solide, légère et transparente utilisée dans les bouteilles de soda, les bocaux, les emballages alimentaires, etc. Le PET est sans danger pour les aliments et est recyclable avec un code de résine de 1.
- Polystyrène choc (HIPS)
Il s'agit d'un plastique polyvalent, économique et résistant aux chocs composé de caoutchouc et de styrène cristal. HIPS convient aux composants de qualité alimentaire en raison de ses propriétés non toxiques.
- Polyméthacrylate de méthyle (PMMA)
Le PMMA est un plastique de type hall qui est transparent et présente de bonnes caractéristiques d'usure. C'est le meilleur ajustement pour une utilisation en extérieur.
- Acide polylactique (PLA)
Il s'agit d'un plastique écologique et réutilisable qui a une faible température de transition vitreuse. Il est populaire dans les applications à usage court.
- Polyamide (Nylon)
Le nylon offre d'excellentes propriétés électriques, une résistance à l'usure par la chaleur et aux produits chimiques, ainsi qu'une résistance. Les industries médicales et automobiles utilisent fréquemment le nylon pour les pièces moulées par injection de plastique personnalisées.
2. Matériaux moulés en élastomère et caoutchouc
- Vulcanisats thermoplastiques (TPV)
Le TPV est un matériau thermoplastique dur contenant des parties de caoutchouc souple réticulé réparties sur toute sa matrice polymère. Le TPV offre une sensation de douceur, un jeu de compression élevé et une finition mate. Il est appliqué dans les pare-chocs, les applications sous le capot, les joints, les soufflets et les œillets.
- Polyuréthane thermoplastique (TPU)
Le TPU est connu pour sa bonne clarté, sa dureté moyenne à élevée, sa bonne résistance à l'usure, à la déchirure, à l'abrasion et à la compression modérée. Il est idéal pour les applications extérieures, y compris les roues de skateboard, les pneus souples, les étuis de protection, les joints d'étanchéité et les dispositifs médicaux.
- Polyéther bloc amide (PEBA)
Le PEBA est composé de blocs polyamides durs fluctuant avec des blocs élastomères souples. Il a une bonne résistance aux chocs, au fluage et à la fatigue en flexion. De plus, il a de faibles ensembles de compression et peut bien prospérer à des températures élevées. Les mousses PEBA sont utilisées dans les équipements sportifs, les rembourrages, les semelles de chaussures, l'électronique et les équipements médicaux.
- Élastomère thermoplastique (TPE)
Il s'agit d'un large groupe d'élastomères qui agissent comme un thermodurcissable avec une élasticité et une flexion élevées, mais se comportent comme un thermoplastique lors du moulage.
- Caoutchouc de silicone liquide (LSR)
Les silicones sont des matériaux en caoutchouc flexibles à haute résistance à la chaleur, merveilleusement polyvalents et offrant une alimentation et une biocompatibilité. Le LSR est utilisé dans les produits de consommation, l'automobile, l'aérospatiale et les dispositifs médicaux.
- Caoutchouc monomère éthylène propylène diène (EPDM)
Il s'agit de l'un des élastomères en caoutchouc les plus performants avec une résistance supérieure aux produits chimiques et à la chaleur et des caractéristiques d'étanchéité à l'humidité. Il est couramment utilisé dans les isolateurs électriques, les joints, les joints automobiles et les joints toriques.
Classes de moulage par injection
Nous avons les classes de moules de moulage suivantes :
1. Classification des moules SPI
L'outillage conventionnel des moules à injection est décrit par classes allant de la classe 105 (prototype) à la classe 101 (production à grande échelle). Ces classes de moules aident à gérer à la fois les fournisseurs de moulage par injection et les clients en fonction des exigences générales et de la portée des outils. Voici un aperçu des différentes classes:
- Moule classe 105
Il s'agit d'un moule de moins de 500 cycles et il est généré de la manière la moins coûteuse possible pour créer une quantité minimale de pièces prototypes. Cette classe est également appelée outils de classe V.
- Moule classe 104
Cette classe est inférieure à 100 000 cycles et est un moule à faible production. Il est utilisé uniquement pour une production restreinte, de préférence avec des matériaux non abrasifs.
- Moule classe 103
Ceci est inférieur à 500 000 cycles et est populaire pour les exigences de production faibles à moyennes. C'est aussi la gamme de prix la plus populaire.
- Moule classe 102
Il s'agit d'un moule de premier ordre et à prix élevé utilisé pour l'outillage de production moyenne à élevée. Il est idéal pour les matériaux abrasifs ou les sections nécessitant une tolérance étroite.
- Classe 101
Ceci est supérieur à 1 000 000 de cycles et est conçu pour une production extrêmement élevée. C'est le moule le plus cher et il est créé uniquement avec des matériaux de qualité supérieure.
Finitions de moulage par injection personnalisées
Diverses sélections de finition de surface pour les pièces en plastique moulées sur mesure sont disponibles. Les processus de finition de surface pour le moulage par injection peuvent aider à diminuer ou à augmenter la grossièreté d'une pièce. Par exemple, les finitions plus rugueuses sont idéales pour certaines pièces mécaniques, tandis que la texture brillante convient aux pièces esthétiques comme les jouets.
La société de l'industrie du plastique (SPI) a élaboré des normes industrielles pour les finitions de moulage par injection de plastique, comme indiqué ci-dessous :
1. Finition de surface brillante de moulage par injection
Les pièces en plastique moulées peuvent être rendues plus brillantes en utilisant un processus de finition comme le polissage au diamant. Dans un tel procédé, une entreprise de moulage par injection utilise un matériau abrasif en vrac sur une roue de travail. Ensuite, ils l'utilisent sur des pièces avec un minimum d'agression, produisant des pièces avec les finitions les plus brillantes possibles.
2. Finition de surface de moulage par injection semi-brillante
Cette finition convient aux pièces qui ont besoin d'un peu de brillance. Un papier abrasif abrasif est utilisé. Ce processus fonctionne bien avec un grand nombre de plastiques de moulage par injection. Il est également utilisé pour produire des pièces hautement esthétiques adaptées aux produits de consommation.
3. Finition de surface mate de moulage par injection
Ce processus consiste à éliminer les marques d'usinage des pièces moulées sans générer de finition brillante. Il est idéal pour les pièces qui manquent de valeur esthétique mais qui nécessitent une finition de surface constante. Il offre une texture de surface de moule de haute qualité et ne présente aucune marque visible.
4. Finition de surface de moulage par injection texturée
Dans certains cas, vous pouvez avoir besoin d'une finition très rugueuse pour augmenter la friction, comme dans les utilisations mécaniques. Vous pouvez utiliser un processus de sablage pour appliquer une finition de surface rugueuse dans un tel cas. Le sablage utilise de l'air comprimé pour diriger le matériau abrasif contre la pièce avec force, rendant sa surface rugueuse.
Les autres finitions courantes incluent les suivantes :
- Ponçage
- Anodisation
- Galvanoplastie
- Polissage
- Revêtement de puissance
- Peinture
Avec la bonne finition de moulage en plastique personnalisé, vous êtes sûr d'avoir des pièces en plastique personnalisées durables. Travailler avec nous vous permet d'atteindre cet objectif et d'impressionner vos clients. Notre équipe d'experts connaît bien toutes les finitions et peut suggérer des matériaux et des finitions thermoplastiques appropriés pour des produits particuliers. Par conséquent, associez-vous à nous aujourd'hui et obtenez un avantage concurrentiel avec les meilleurs services.
Contrôles de qualité et options de finition pour les pièces moulées sur mesure
Lorsque vous demandez un devis de moulage par injection, vous pouvez choisir parmi les options suivantes en fonction des besoins de votre application :
1. Inspections de qualité disponibles pour les commandes de fabrication à la demande
Vous disposez des options suivantes :
- Inspection CMM en cours de fabrication et surveillance de la machine
- Rapport scientifique sur le développement du procédé de moulage
- Inspection du premier article (FAI) et rapport de capacité de processus avec GD&T
- Conception pour le retour d'information sur la fabricabilité (DFM)
2. Post-traitement
Sous cette option, vous avez :
- Tampographie
- Assemblage de composants
- Inserts filetés
- Gravure laser
- Texturation du moule
FAQ
1. Pourquoi les moules d'injection plastique coûtent-ils si cher ?
Divers facteurs contribuent aux coûts élevés des moules d'injection plastique. L'un des principaux facteurs est les moules eux-mêmes. Pour produire des pièces en plastique de qualité supérieure, vous devez utiliser un moule à injection construit de haute qualité. Les moules pour l'injection plastique sont constitués d'éléments usinés générés à partir de différents métaux comme les aciers de moule trempés et l'aluminium de qualité aéronautique.
Les moules sont ensuite conçus et créés par des experts, également appelés moulistes. Ces personnes ont passé plusieurs années à apprendre le métier de mouleur. Ainsi, ils connaissent bien ce processus de production de moules de haute qualité. Leur rémunération contribue au coût élevé des moules d'injection plastique.
De plus, les fabricants de moules ont besoin d'outils très coûteux pour effectuer leur travail, comme des machines CNC, des logiciels de pointe, des montages de précision et de l'outillage. D'autres facteurs qui contribuent au coût élevé de l'injection plastique personnalisée sont les suivants :
Conception de moules
La conception personnalisée du moulage par injection a un impact significatif sur son prix. La procédure de moulage par injection de plastique sur mesure nécessite beaucoup de pression lorsque la machine injecte le plastique dans les cavités du moule. Sans la haute pression, les pièces moulées par injection n'auront pas les finitions de surface souhaitées et peuvent être dimensionnellement incorrectes.
Exigences de construction du moule
Un autre facteur important associé au coût élevé des moules à injection est la demande de construction de moules. La construction doit être précise pour qu'un moule à injection fonctionne correctement pendant la procédure de moulage par injection plastique personnalisée. Même si les moules sont décrits comme deux moitiés, un noyau et un côté cavité, plusieurs pièces de précision constituent généralement chaque moitié.
Presque chacun des éléments de moule usinés avec précision qui assembleront et produiront vos pièces moulées sur mesure sont instrumentés avec des tolérances de 0,025 mm ou +/-0,001''. Un papier copie conventionnel a une épaisseur de 0,089 mm ou 0,0035''. Par conséquent, un mouliste doit être très précis pour découper votre papier de copie en trois morceaux ultra-fins et construire avec précision votre moule.
La complexité de la pièce
Plus votre pièce est complexe, plus votre moule d'injection sera cher. De plus, le moule peut être très dur voire impossible à modifier une fois créé par moulage par compression. Il est donc difficile pour vous de modifier la conception.
Matériaux de moule
Pour que votre moule résiste aux pressions auxquelles il est soumis lors de la procédure de moulage par injection sur mesure, il doit être composé d'aluminium et d'acier de qualité supérieure. De plus, il doit être conçu pour résister aux efforts de serrage et d'injection.
2. Comment savoir si le moulage par injection est le bon procédé pour un produit ?
Divers facteurs influencent votre décision quant à savoir si le moulage par injection personnalisé vous convient. Ces facteurs incluent votre budget, le nombre de pièces requises, la géométrie de la pièce et l'application de la pièce.
3. Combien de temps faut-il pour construire un nouveau moule ?
Cela peut prendre en moyenne 8 à 10 semaines, selon la complexité de la conception et les cavités du moule.
4. Les moules de ma pièce seront-ils entretenus entre les cycles de production ?
Les moules sont moins susceptibles d'être maintenus entre les cycles de production. Cependant, cela peut dépendre de facteurs tels que le matériau du moule d'injection, les conditions de fonctionnement, les temps de cycle et le temps entre les cycles de production. Vous pouvez utiliser ces facteurs pour déterminer si vous pouvez entretenir vos moules à tout moment.