Kundenspezifischer Spritzguss
Mit erstklassigen Bearbeitungswerkzeugen fertigen wir fachmännisch Teile, die Ihren erforderlichen Toleranzen und Qualitätsstandards entsprechen. Wir testen alle Produkte, um sicherzustellen, dass sie den Spezifikationen für Ihre Branche und Anwendung entsprechen.
Unsere Fähigkeiten und Kapazitäten ermöglichen es uns, erstklassige kundenspezifische Spritzgussdienstleistungen anzubieten. Wir arbeiten eng mit jedem Kunden zusammen, um sein Projekt zu verstehen und ihn bei der Auswahl der richtigen maßgeschneiderten Formen und Designs zu unterstützen.
Ganz gleich, ob Sie eine kleine Charge von Prototypenteilen oder eine Serienfertigung benötigen, wir bieten individuelle Lösungen, die auf Ihre Bedürfnisse zugeschnitten sind. Dank unserer Fachkompetenz im kundenspezifischen Formenbau können wir stets qualitativ hochwertige Komponenten herstellen, die den Erfolg Ihres Unternehmens unterstützen.
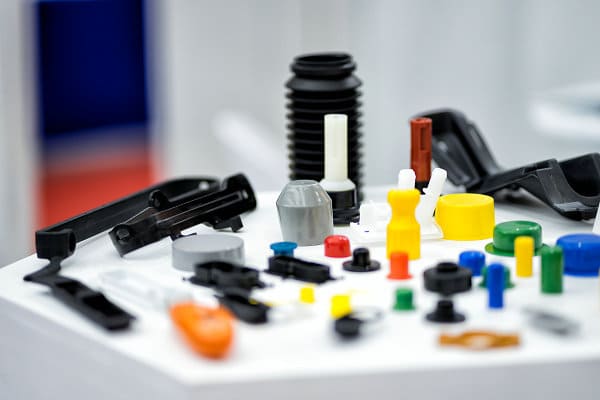
Fordern Sie ein Angebot an
Kundenspezifischer Spritzguss
Spritzgießen ist ein kostengünstiges Herstellungsverfahren für große Mengen kundenspezifischer Kunststoffteile. Beim Spritzgussverfahren wird geschmolzener Kunststoff in ein Formwerkzeug eingebracht und der erstarrte Abschnitt anschließend entfernt. Der Zyklus wiederholt sich mehrmals, wodurch die Formkosten und damit der Preis jeder Einheit gesenkt werden.
Da beim Spritzgussverfahren für jedes Teil ein ähnliches Formwerkzeug verwendet wird, bietet es eine gleichbleibende Qualität bei jedem Produkt. Darüber hinaus weist das Spritzgießen im Vergleich zum 3D-Druck oder der CNC-Bearbeitung eine große Vielfalt an Polituren, Materialien, Kosmetika und Farben auf.
Die kundenspezifischen Kunststoff-Spritzguss-Dienstleistungen von Moldie sind einzigartig. Wir bieten außergewöhnliche Dienstleistungen, die die Erwartungen unserer Kunden übertreffen. Nachdem wir Ihre Bestellung erhalten haben, finden wir den geeigneten Spritzguss-Lieferanten, der die Teile nach Ihren Wünschen zum passenden Preis und ohne Kompromisse beim Design herstellt.
Darüber hinaus bieten wir flexible Dienstleistungen an. Wir verfügen über ausgeklügelte Tools, ein Team von Fachleuten und Ressourcen, die personalisierte Teile für Kunden in verschiedenen Branchen bereitstellen. Außerdem arbeiten wir innerhalb einer kurzen Vorlaufzeit. Alle unsere Prozesse sind optimiert. Dadurch wird sichergestellt, dass Sie Ihre Bestellung innerhalb der gewünschten Zeit erhalten.
Die Vorteile des kundenspezifischen Spritzgießens
Kunststoffspritzguss bietet zahlreiche Vorteile, darunter die folgenden:
1. Es ist kostengünstig
Kunststoffspritzguss ist ein automatisierter Prozess. Daher sind die Arbeitskosten im Vergleich zu anderen Kunststoffherstellungsverfahren relativ gering. Außerdem produziert das Spritzgießen die Teile auf hohem Niveau mit einer hohen Ausbringungsrate, wodurch die Herstellungskosten aufgrund seiner Effektivität gesenkt werden.
2. Kunststoffspritzguss bietet verbesserte Festigkeit
Die aus dem Spritzgussverfahren resultierenden Kunststoff-Spritzgussteile weisen eine erhöhte Festigkeit auf. Das liegt daran, dass Sie Füllstoffe in Spritzgussformen verwenden können. Diese Füllstoffe verringern die Kunststoffdichte während des Formens und verleihen den Formteilen eine größere Festigkeit.
3. Es bietet Flexibilität in Material und Farbe
Heutzutage sind zahlreiche Materialien mit dem Kunststoffspritzgussverfahren kompatibel. Mit allen verfügbaren Optionen können Sie ganz einfach ein Material mit den geeigneten chemischen, physikalischen und mechanischen Eigenschaften auswählen. Außerdem können Sie die Kunststoffe mit mehreren Farbsystemen einfärben.
4. Kunststoffspritzguss unterstützt komplexe Geometrien mit engen Toleranzen
Das kundenspezifische Spritzgießen ermöglicht die Herstellung von hochvolumigen und konsistenten, komplexen Teilen. Um die Effizienz des Massenspritzgusses zu maximieren und die Genauigkeit und Qualität Ihrer Portionen zu optimieren, müssen Sie die Designelemente berücksichtigen. Mit dem entsprechenden Design können Sie Teile in gleichbleibend hoher Qualität produzieren.
Mit Spritzguss können Sie schnell wiederholbare Teile mit engen Toleranzen erhalten, wodurch Sie präzise Produkte für zahlreiche Anwendungen erhalten, die mit CNC-Maschinenteilen vergleichbar sind.
5. Führt zu weniger Abfall
Beim Kunststoff-Spritzgussverfahren entsteht weniger Materialabfall nach der Produktion als bei der konventionellen Fertigung. Außerdem können Sie Kunststoffabfälle für die zukünftige Verwendung nachmahlen und recyceln.
6. Custom Plastic Moulding bietet mehrere Oberflächen
Die meisten Formteile haben eine weiche Oberfläche, die fast dem gewünschten Endergebnis entspricht. Ein glattes Erscheinungsbild ist jedoch nur für einige Anwendungen geeignet. Je nach Materialeigenschaften erzeugt das Spritzgussverfahren Oberflächen, die keine Nachbearbeitung erfordern. Sie können einzigartige Texturen hinzufügen, matte Oberflächen erzielen oder Gravuren anbringen.
7. Es bietet eine hohe Wiederholbarkeit
Ein weiterer wesentlicher Vorteil des kundenspezifischen Spritzgusses ist seine hohe Wiederholbarkeit. Nachdem Sie Ihre Form erstellt haben, können Sie zahlreiche ähnliche Teile herstellen, bevor Sie Ihr Werkzeug warten müssen. Dies führt zu niedrigen Produktionskosten.
8. Es ist hochwirksam bei schneller Produktion
Der kundenspezifische Spritzguss gehört zu den schnellsten Produktionsmethoden. Die Produktionsleistung ist hoch, was sie effektiver und kostengünstiger macht. Meistens hängt die Geschwindigkeit von der Komplexität des Designs und der Größe Ihrer Form ab, aber eine typische Form dauert etwa 5-20 Minuten.
Dies fördert die Produktion von mehr Formen in einer begrenzten Zeit und erhöht so die Gewinnspannen. Darüber hinaus haben einige Formen mehrere Hohlräume, was dazu führt, dass mehr Teile in einem Formzyklus hergestellt werden.
Spritzgussfähigkeiten
In Bezug auf kundenspezifische Kunststoffspritzgussfähigkeiten sind wir stolz darauf, zu den führenden Spritzgussunternehmen zu gehören, die einzigartige und genau definierte Teile liefern, die Maschinen und Verfahren in verschiedenen wichtigen Unternehmen weltweit verbessern können.
Unsere Spritzguss-Fähigkeiten ermöglichen es uns, deutlich geformte Teile herzustellen, die mit anderen Methoden nicht hergestellt werden können. Wir verwenden Mehrkavitäten-, Einzel- und Familienmaschinen, um kostengünstig hochwertige Spritzgussprodukte herzustellen.
Darüber hinaus planen und organisieren wir gemeinsam mit Ihnen innovative Lösungen. Wir sind Experten in der Metall-zu-Kunststoff-Umwandlung, Haltbarkeit und Komponentendesign, um Produktionszeit und -kosten zu senken und gleichzeitig die Effizienz zu steigern. Wir sind bekannt für unser besonderes Verfahren zur Reduzierung von Kosten und Durchlaufzeiten und zur Steigerung der Produktionskapazitäten verschiedener Branchen.
Spritzgussverfahren
Für kundenspezifisches Kunststoffspritzgießen werden drei grundlegende Elemente benötigt – ein Kunststoffrohmaterial, eine Spritzgussmaschine und eine Form. Formen für Kunststoffspritzguss bestehen aus hochfesten Stahl- und Aluminiumelementen, die so programmiert sind, dass sie in zwei Hälften funktionieren. Jede Hälfte wird in der Spritzgussmaschine zusammengesetzt, um ein kundenspezifisches Kunststoffteil zu bilden.
Danach spritzt die Maschine geschmolzenen Kunststoff in die Form, wo er zum Endprodukt erstarrt. Der kundenspezifische Spritzgussprozess folgt strengen Spezifikationen und wird in den folgenden Schritten erreicht:
1. Klemmung
Der erste Schritt des Spritzgussverfahrens ist das Spannen. Im Allgemeinen bestehen Spritzgussformen aus zwei Hälften. In diesem Schritt schließt die Maschine diese Hälften, bevor der Kunststoff in die Form eingesetzt wird, um zu verhindern, dass sich die Form während des Einspritzschritts öffnet.
2. Injektion
In diesem Schritt wird Rohkunststoff, typischerweise in Form kleiner Pellets, in die Spritzgussmaschine am Einzugsbereich einer hin- und hergehenden Schnecke eingeführt. Temperatur und Kompression erhitzen das Kunststoffmaterial, während die Schnecke die Kunststoffpellets durch erhitzte Bereiche des Maschinenzylinders befördert.
Die Menge an geschmolzenem Kunststoff, die zur Vorderseite der Schnecke transportiert wird, wird genau gemessen, da dies die Menge ist, die nach dem Einspritzen das endgültige Teil bildet.
Wenn die entsprechende Menge geschmolzener Kunststoffpellets an der Vorderseite der Schnecke ankommt und die Form gut eingespannt ist, führt die Maschine sie in die Form ein und treibt sie unter hohem Druck bis zum letzten Teil der Kavität.
3. Kühlung
Sobald der geschmolzene Kunststoff die inneren Formoberflächen berührt, kühlt er ab. Das Kühlverfahren verfestigt die Form und Zähigkeit des frisch geformten Kunststoffteils. Die für jedes Kunststoffformteil erforderliche Abkühlzeit hängt von der Wandstärke, den thermodynamischen Eigenschaften des Kunststoffs und den Maßanforderungen der kundenspezifischen Teile ab.
4. Auswurf
Nach dem Abkühlen entspannt und öffnet die Maschine die Kunststoffspritzgussform. Die Vorrichtung ist mit mechanischen Einrichtungen ausgestattet, die mit Komponenten arbeiten, die innerhalb der Kunststoffspritzgussform entwickelt wurden, um das Teil zu entfernen. In dieser Phase wird das individuell geformte Teil herausgedrückt, und die Form ist für den nächsten Schritt bereit, wenn das neue Teil vollständig ausgeworfen wird.
Kundenspezifische Kunststoff-Spritzgussmaterialien
Die kundenspezifischen Kunststoffspritzgussmaterialien werden wie folgt kategorisiert:
1. Starre Kunststoffmaterialien
Nachfolgend finden Sie einige Materialien dieser Kategorie:
- Polyacrylamid (PARA)
Diese wird hauptsächlich mit Füllungen wie Mineralfasern oder Glas gemischt. Es erzeugt starre Abschnitte mit geringem Kriechen und einer langsameren Wasseraufnahme als Nylon. PARA eignet sich perfekt für Strukturelemente in der Medizinelektronik und in Handheld-Geräten.
- Polycarbonat (PC)
PC ist eine leichte, transparente und langlebige Materialalternative zu Glas. Aufgrund seiner hohen Haltbarkeit und extremen Stoßfestigkeit verwenden die meisten Branchen PCs in verschiedenen Anwendungen, einschließlich elektronischer Geräte, Objektive, Sicherheitsausrüstung usw.
- Polyethylen (PE)
Dies ist ein Polymer in Verbraucherqualität, das Sie basierend auf der Dichte auswählen können, was es zu einem der weltweit am häufigsten verwendeten Kunststoffe macht. Sie können Polyethylenterephthalat (PET, PETE) mit niedriger Dichte (LDPE), hoher Dichte (HDPE) oder Polyethylenterephthalat haben.
PE-Kunststoffe haben eine hohe Elastizität, Abriebfestigkeit und Chemikalienbeständigkeit. Sie eignen sich am besten zum Spritzgießen von übergroßen Artikeln, die häufig in Flaschen, Folien, Schläuchen, Verpackungen usw. verwendet werden.
- Acrylnitril-Butadien-Styrol (ABS)
Dies ist ein amorphes thermoplastisches Material mit niedrigem Schmelzpunkt. Es ist mit Farbstoffen kompatibel und enthält unzählige Texturen und Oberflächenoptionen. ABS ist sehr schlagzäh und robust. Es hat jedoch eine schwache Beständigkeit gegen hohe Reibung, UV-Strahlen, Lösungsmittel und Witterungseinflüsse. Außerdem setzt es beim Verbrennen starken Rauch frei.
ABS wird am besten in Konsumgütern, elektronischen Komponenten und Verkleidungen, Sportgeräten und Autoteilen verwendet.
- Polypropylen (PP)
Dies ist auch ein weiterer häufig verwendeter Kunststoff weltweit. Es ähnelt im Wesentlichen PE, ist aber hitzebeständiger und etwas härter. Beim Spritzgießen können Sie dieses Material recyceln und mit anderen Kunststoffmaterialien kombinieren. Aufgrund seiner geringen Dichte wird PP für Aufbewahrungsbehälter, bewegliche Scharniere für Plastikflaschen, Elektrowerkzeuge und Sportartikel verwendet.
- Thermoplastisches Polyurethan (TPU)
TPU ist bekannt für seine Beständigkeit gegen Öle, Abrieb und Chemikalien und seine Fähigkeit, mit hohen Temperaturen umzugehen. Es ist in verschiedenen Qualitäten erhältlich, darunter medizinische, industrielle und kommerzielle. Daher eignet es sich am besten für Räder, Schuhe, medizinische Geräte und elektronische Gehäuse.
- Polyphthalamid (PPA)
PPA ist eine Untergruppe von Nylons, die typischerweise eine geringe Feuchtigkeitsaufnahme und hohe Schmelzpunkte aufweisen. Es wird in Automobil- und Industrieanwendungen eingesetzt, da es aggressiven Chemikalien widerstehen kann. Außerdem eignet es sich gut für Scheinwerfergehäuse und Kraftstoffverteiler.
- Polyvinylidenfluorid (PVDF)
Dies ist ein chemisch inertes Hochtemperaturmaterial. Aufgrund seiner geringen Reibung wird PCDF in Lagern, Rohren, Sanitärteilen, elektrischen Kabelisolierungen und der Handhabung von Chemikalien verwendet.
- Thermoplastisches Polyolefin (TPO)
TPO hat eine gute chemische Beständigkeit und ist flexibel, hat aber eine geringere Temperaturbeständigkeit als PP.
- Styrol-Acrylnitril (SNA)
SNA ist ein transparentes und hitzebeständiges Polystyrol. Es ist beliebt in Küchengeschirr, Türgriffen und Haushaltswaren.
- Polyvinylchlorid (PVC)
Dies ist ein rundum starrer Kunststoff, der zum Beschneiden, für Non-Food-Verpackungen und für Klempnerarbeiten verwendet wird.
- Polyphenylensulfid, Ryton (PPS)
PPS ist ein Hochleistungsthermoplast mit hoher Lösungsmittelbeständigkeit.
- Acetalpolyoxymethylen (POM)
Dieser hat eine hohe Verschleißfestigkeit, geringe Reibung und eine gute Feuchtigkeitsbeständigkeit.
- Polystyrol-Polyphenylether (PS-PPE)
PS-PPE weist eine hohe Hitze- und Flammbeständigkeit auf. Darüber hinaus weist es auch bei hohen Temperaturen Zugfestigkeit und hohe Steifigkeit auf.
- Acrylnitril-Styrol-Acrylat (ASA)
Dieses Material ist fast das gleiche wie ABS, hat aber eine höhere Beständigkeit gegen Ausbleichen und wird daher für den Außenbereich verwendet.
- Polyethylen niedriger Dichte (LDPE)
Ein flexibles und hartes Material, das mit Alkoholen, Säuren und Basen nicht reagiert. Es eignet sich am besten für Schnappdeckel, Mehrzweckbehälter und Tabletts.
- Celluloseacetat (CA)
CA ist ein flexibles Material, das in Filmen, Brillen oder Lebensmittelkontakt verwendet werden kann.
- Flüssigkristallpolymer (LCP)
LCP bietet einzigartige Eigenschaften für dünnwandige Komponenten und Mikrospritzguss. Es ist üblich in medizinischen Geräten und elektrischen Verbindungen und Steckverbindern.
- Polyethylen hoher Dichte (HDPE)
Es hat ein perfektes Verhältnis von Festigkeit zu Gewicht und chemische Beständigkeit. HDPE wird hauptsächlich für Verbindungsisolatoren, Lebensmittelbehälter und Kraftstofftanks verwendet. Es kann auch in Außenanlagen wie Spielplätzen verwendet werden.
- Polyamid 6/6, Nylon 6 (PA 6/6)
Dies sorgt für verbesserte mechanische Festigkeit, hervorragende Wärmestabilität und Steifigkeit sowie chemische Beständigkeit.
- Polybutylenterephthalat (PBT)
Dies ist ein beliebter elektronischer Isolator auf Polyesterbasis. Es wird hauptsächlich in der Automobilindustrie als länger haltbare Alternative zu Nylon verwendet.
- Polyetheretherketon (PEEK)
PEEK bietet eine hervorragende Zugfestigkeit, die die meisten Kunststoffe übertrifft. Aus diesem Grund wird es hauptsächlich als leichte Alternative zu Metallteilen in Anwendungen mit hoher Belastung und hohen Temperaturen verwendet.
- Polycarbonat-Acrylnitril-Butadien-Styrol (PC-ABS)
Wie der Name schon sagt, ist dies eine Kombination aus PC und ABS, die zu einem hochfesten technischen Thermoplast führt, der flexibler als gewöhnliches Polycarbonat ist.
- Polyetherimid (PEI)
Dieses ist bekannt für seine hohe Flamm- und Hitzebeständigkeit. Es wird in den meisten medizinischen Anwendungen eingesetzt und ist kostengünstiger als PEEK.
- Polyethersulfon (PES)
PES ist ein starrer und transparenter Kunststoff, der biokompatibel, sterilisierbar und chemisch inert ist. Es eignet sich für Lebensmittelkontaktgeräte wie Kaffeemaschinenkomponenten. Es ist auch in Branchen mit hoher chemischer Belastung wie der Automobil- und Luft- und Raumfahrtindustrie anwendbar.
- Polycyclohexylendimethylenterephthalat (PCT)
Dieses Material hat eine gute Umweltstabilität und eine geringe Feuchtigkeitsaufnahme. Es wird hauptsächlich in Schaltern und Steckern verwendet.
- Polycarbonat-Polyethylenterephthalat (PC-PET)
Dies ist eine Kombination aus PC und PET, um ein Produkt zu ergeben, das robust und chemisch beständig ist und als Ersatz für PC-ABS verwendet werden kann. Es widersteht aggressiven Chemikalien und Lösungsmitteln und eignet sich daher perfekt für Anwendungen im Gesundheitswesen und Sportausrüstung.
- Polycarbonat-Polybutylenterephthalat (PC-PBT)
Dieses hat ähnliche Eigenschaften wie PC-PET und ist in Elektronikgehäusen beliebt.
- Polyethylenterephthalat (PET)
Auch als PETE bekannt, ist PET ein starkes, leichtes und klares PE-Harz, das in Sodaflaschen, Gläsern, Lebensmittelverpackungen usw. verwendet wird. PET ist lebensmittelecht und mit einem Harzcode von 1 recycelbar.
- Schlagfestes Polystyrol (HIPS)
Dies ist ein vielseitiger, sparsamer und schlagfester Kunststoff, der aus Gummi und kristallinem Styrol besteht. HIPS ist aufgrund seiner ungiftigen Eigenschaften für lebensmitteltaugliche Komponenten geeignet.
- Polymethylmethacrylat (PMMA)
PMMA ist ein hallenähnlicher Kunststoff, der klar ist und gute Verschleißeigenschaften aufweist. Es ist die beste Passform für den Einsatz im Freien.
- Polymilchsäure (PLA)
Dies ist ein umweltfreundlicher und wiederverwendbarer Kunststoff mit einer niedrigen Glasübergangstemperatur. Es ist beliebt bei Kurzzeitanwendungen.
- Polyamid (Nylon)
Nylon bietet hervorragende elektrische Eigenschaften, Beständigkeit gegen Hitzeverschleiß und Chemikalien sowie Festigkeit. Die Medizin- und Automobilindustrie verwendet häufig Nylon für kundenspezifische Spritzgussteile aus Kunststoff.
2. Elastomer- und Gummiformteile
- Thermoplastische Vulkanisate (TPV)
TPV ist ein hartes thermoplastisches Material, das Teile aus weichem, vernetztem Gummi enthält, die über seine gesamte Polymermatrix verteilt sind. TPV bietet ein glattes Gefühl, einen hohen Druckverformungsrest und ein mattes Finish. Es wird in Stoßfängern, Anwendungen unter der Motorhaube, Dichtungen, Manschetten und Ösen verwendet.
- Thermoplastisches Polyurethan (TPU)
TPU ist bekannt für seine gute Klarheit, mittlere bis hohe Härte, guten Verschleiß, Reißfestigkeit, Abriebfestigkeit und moderaten Druckverformungsrest. Es ist ideal für Outdoor-Anwendungen, einschließlich Skateboard-Räder, flexible Reifen, Schutzhüllen, wetterfeste Dichtungen und medizinische Geräte.
- Polyetherblockamid (PEBA)
PEBA besteht aus harten Polyamidblöcken, die mit weichen Elastomerblöcken wechseln. Es hat eine gute Schlagfestigkeit, Kriechfestigkeit und Biegeermüdung. Darüber hinaus hat es niedrige Druckverformungsreste und kann bei hohen Temperaturen gut gedeihen. PEBA-Schaumstoffe werden in Sportgeräten, Polstern, Schuheinlagen, Elektronik und medizinischen Geräten verwendet.
- Thermoplastisches Elastomer (TPE)
Dies ist eine breite Gruppe von Elastomeren, die sich wie ein Duroplast mit Elastizität und hoher Biegung verhalten, sich aber beim Formen wie ein Thermoplast verhalten.
- Flüssiger Silikonkautschuk (LSR)
Silikone sind flexible Gummimaterialien mit hoher Hitzebeständigkeit, wunderbarer Vielseitigkeit und Lebensmittel- und Biokompatibilität. LSR wird in Konsumgütern, in der Automobilindustrie, in der Luft- und Raumfahrt und in medizinischen Geräten verwendet.
- Ethylen-Propylen-Dien-Monomer-Kautschuk (EPDM)
Dies ist eines der am besten funktionierenden Gummielastomere mit überlegener Chemikalien- und Hitzebeständigkeit und Feuchtigkeitsabdichtungseigenschaften. Es wird häufig in elektrischen Isolatoren, Dichtungen, Automobildichtungen und O-Ringen verwendet.
Klassen für Spritzgussformen
Wir haben folgende Formenklassen:
1. SPI-Schimmelklassifizierung
Herkömmliche Spritzgusswerkzeuge werden durch Klassen von Klasse 105 (Prototyp) bis Klasse 101 (Großserienfertigung) beschrieben. Diese Werkzeugklassen helfen bei der Verwaltung sowohl von Spritzgusslieferanten als auch von Kunden in Bezug auf die allgemeinen Werkzeuganforderungen und den Umfang. Nachfolgend finden Sie eine Übersicht über die verschiedenen Klassen:
- Form der Klasse 105
Dies ist eine Form mit weniger als 500 Zyklen und wird auf möglichst kostengünstige Weise hergestellt, um eine minimale Menge an Prototypteilen herzustellen. Diese Klasse wird auch als Klasse-V-Werkzeug bezeichnet.
- Form der Klasse 104
Diese Klasse liegt unter 100.000 Zyklen und ist eine Form mit geringer Produktion. Es wird nur für eingeschränkte Produktion verwendet, vorzugsweise mit nicht abrasiven Materialien.
- Form der Klasse 103
Dies liegt unter 500.000 Zyklen und ist beliebt für niedrige bis mittlere Produktionsanforderungen. Es ist auch die beliebteste Preisklasse.
- Form der Klasse 102
Dies ist eine erstklassige und hochpreisige Form, die für Mittel- bis Hochleistungswerkzeuge verwendet wird. Es ist ideal für abrasive Materialien oder Schnitte, die enge Toleranzen erfordern.
- Klasse 101
Diese liegt bei über 1.000.000 Zyklen und ist für eine überaus hohe Produktion ausgelegt. Es ist die teuerste Form und wird nur aus hochwertigen Materialien hergestellt.
Kundenspezifische Spritzgussoberflächen
Verschiedene Oberflächenausführungen für individuell geformte Kunststoffteile sind verfügbar. Oberflächenveredelungsverfahren für den Spritzguss können dazu beitragen, die Rauheit eines Teils zu verringern oder zu erhöhen. Beispielsweise sind rauere Oberflächen ideal für bestimmte mechanische Teile, während eine glänzende Textur zu ästhetischen Teilen wie Spielzeug passt.
Die Society of Plastic Industry (SPI) hat Industriestandards für Kunststoffspritzgussoberflächen entwickelt, wie unten beschrieben:
1. Glänzende Spritzguss-Oberfläche
Geformte Kunststoffteile können mit einem Veredelungsprozess wie Diamantschwabbelpolieren glänzender gemacht werden. Bei einem solchen Verfahren verwendet ein Spritzgussunternehmen ein loses Schleifmaterial auf einem Arbeitsrad. Anschließend wenden sie dies mit minimaler Aggression an Teilen an und produzieren Teile mit möglichst glänzenden Oberflächen.
2. Halbglänzende Spritzguss-Oberfläche
Dieses Finish eignet sich für Teile, die etwas Glanz benötigen. Es wird ein Schleifpapier mit Körnung verwendet. Dieses Verfahren funktioniert gut mit einer großen Anzahl von Spritzgusskunststoffen. Es wird auch verwendet, um hochästhetische Teile herzustellen, die für Konsumgüter geeignet sind.
3. Mattes Spritzguss-Oberflächenfinish
Bei diesem Verfahren werden Bearbeitungsspuren von Formteilen entfernt, ohne eine glänzende Oberfläche zu erzeugen. Es ist ideal für Teile, die keinen ästhetischen Wert haben, aber eine konsistente Oberflächenbeschaffenheit benötigen. Es bietet eine hochwertige Formoberflächenstruktur und weist keine auffälligen Spuren auf.
4. Strukturierte Spritzguss-Oberfläche
In einigen Fällen benötigen Sie möglicherweise eine sehr raue Oberfläche, um die Reibung zu erhöhen, z. B. bei mechanischen Anwendungen. In einem solchen Fall können Sie mit einem Sandstrahlverfahren eine raue Oberfläche aufbringen. Beim Sandstrahlen wird Druckluft verwendet, um abrasives Material mit Kraft gegen das Teil zu lenken und dessen Oberfläche aufzurauen.
Andere übliche Oberflächen sind die folgenden:
- Schleifen
- Eloxieren
- Galvanik
- Polieren
- Power-Beschichtung
- Malen
Mit der richtigen kundenspezifischen Kunststoffformoberfläche erhalten Sie mit Sicherheit langlebige kundenspezifische Kunststoffteile. Durch die Zusammenarbeit mit uns können Sie dies erreichen und Ihre Kunden beeindrucken. Unser Expertenteam kennt sich mit allen Oberflächen aus und kann geeignete thermoplastische Materialien und Oberflächen für bestimmte Produkte vorschlagen. Arbeiten Sie deshalb noch heute mit uns zusammen und verschaffen Sie sich mit den besten Dienstleistungen einen Wettbewerbsvorteil.
Qualitätsprüfungen und Endbearbeitungsoptionen für kundenspezifische Formteile
Wenn Sie ein Spritzgussangebot anfordern, können Sie je nach Ihren Anwendungsanforderungen aus den folgenden Optionen wählen:
1. Qualitätsprüfungen für On-Demand-Fertigungsaufträge verfügbar
Sie haben folgende Möglichkeiten:
- In-Prozess-KMG-Inspektion und Maschinenüberwachung
- Bericht über die Entwicklung des wissenschaftlichen Formverfahrens
- Erstmusterprüfung (FAI) und Prozessfähigkeitsbericht mit GD&T
- Design für Herstellbarkeits-Feedback (DFM)
2. Nachbearbeitung
Unter dieser Option haben Sie:
- Tampondruck
- Baugruppenmontage
- Gewindeeinsätze
- Laser-Gravur
- Formtexturierung
Häufig gestellte Fragen
1. Warum kosten Kunststoffspritzgussformen so viel?
Verschiedene Faktoren tragen zu den hohen Kosten von Kunststoff-Spritzgussformen bei. Einer der wichtigsten Faktoren sind die Formen selbst. Um hochwertige Kunststoffteile herzustellen, müssen Sie eine hochwertig gebaute Spritzgussform verwenden. Formen für den Kunststoffspritzguss bestehen aus bearbeiteten Elementen, die aus verschiedenen Metallen wie gehärtetem Formstahl und Aluminium in Flugzeugqualität hergestellt werden.
Die Formen werden dann von Experten, auch Formenbauer genannt, entworfen und hergestellt. Diese Menschen haben mehrere Jahre lang das Handwerk des Formenbauers erlernt. Daher sind sie mit diesem Prozess zur Herstellung hochwertiger Formen bestens vertraut. Ihre Vergütung trägt zu den hohen Kosten von Kunststoffspritzgussformen bei.
Darüber hinaus benötigen Formenbauer sehr kostspielige Werkzeuge, um ihre Aufgaben auszuführen, wie CNC-Maschinen, modernste Software, Präzisionsvorrichtungen und Werkzeuge. Andere Faktoren, die zu den hohen Kosten des kundenspezifischen Kunststoffspritzgusses beitragen, sind die folgenden:
Formendesign
Kundenspezifisches Spritzgussdesign hat einen erheblichen Einfluss auf den Preis. Das kundenspezifische Kunststoffspritzgussverfahren erfordert viel Druck, wenn die Maschine den Kunststoff in die Formhohlräume spritzt. Ohne den hohen Druck haben die Spritzgussteile nicht die gewünschte Oberflächengüte und können Maßfehler aufweisen.
Anforderungen an den Formenbau
Ein weiterer wesentlicher Faktor, der mit den hohen Kosten von Spritzgussformen verbunden ist, sind die Anforderungen an den Formenbau. Die Konstruktion muss genau sein, damit eine Spritzgussform während des kundenspezifischen Kunststoff-Spritzgussverfahrens angemessen funktioniert. Obwohl die Formen als zwei Hälften, einen Kern und eine Hohlraumseite, umrissen sind, bilden normalerweise mehrere Präzisionsteile jede Hälfte.
Nahezu jedes der präzise bearbeiteten Formelemente, die Ihre kundenspezifischen Formteile zusammenbauen und produzieren, wird mit Toleranzen von 0,025 mm oder +/- 0,001 Zoll instrumentiert. Ein herkömmliches Kopierpapier ist 0,089 mm oder 0,0035 Zoll dick. Daher muss ein Formenbauer sehr genau sein, um Ihr Kopierpapier in drei ultradünne Stücke zu schneiden und Ihre Form genau zu bauen.
Die Komplexität des Teils
Je komplexer Ihr Teil ist, desto teurer wird Ihre Spritzgussform. Außerdem kann die Form sehr schwer oder sogar unmöglich zu modifizieren sein, wenn sie einmal durch Formpressen hergestellt wurde. Dies macht es schwierig für Sie, das Design zu ändern.
Formmaterialien
Damit Ihre Form den Drücken standhält, denen sie während des kundenspezifischen Spritzgussverfahrens ausgesetzt ist, muss sie aus hochwertigen Aluminium- und Stahlsorten bestehen. Außerdem muss es so hergestellt werden, dass es Klemm- und Einspritzkräften standhält.
2. Woher wissen Sie, ob Spritzgießen das richtige Verfahren für ein Produkt ist?
Verschiedene Faktoren beeinflussen Ihre Entscheidung, ob der kundenspezifische Spritzguss für Sie geeignet ist. Zu diesen Faktoren gehören Ihr Budget, die Anzahl der benötigten Teile, die Geometrie des Teils und die Anwendung des Teils.
3. Wie lange dauert der Bau einer neuen Form?
Es kann durchschnittlich 8-10 Wochen dauern, abhängig von der Designkomplexität und den Kavitäten der Form.
4. Werden die Formen für mein Teil zwischen den Produktionsläufen gewartet?
Es ist weniger wahrscheinlich, dass Formen zwischen Produktionsläufen gewartet werden. Dies kann jedoch von Faktoren wie Spritzgussmaterial, Betriebsbedingungen, Zykluszeiten und Zeit zwischen Produktionsläufen abhängen. Anhand dieser Faktoren können Sie feststellen, ob Sie Ihre Formen jederzeit warten können.