Moldeo por inyección personalizado
Con herramientas de mecanizado de primera línea, fabricamos piezas de manera experta para que coincidan con las tolerancias y estándares de calidad requeridos. Probamos todos los productos para asegurarnos de que se ajusten a las especificaciones de su industria y aplicación.
Nuestras capacidades y capacidad nos permiten ofrecer los mejores servicios de moldeo por inyección personalizados de su clase. Trabajamos estrechamente con cada cliente para comprender su proyecto y guiarlo en la selección de los moldes y diseños personalizados adecuados.
Ya sea que necesite un pequeño lote de piezas prototipo o una producción a gran escala, brindamos soluciones personalizadas adaptadas a sus necesidades. Nuestra experiencia en moldeado personalizado nos permite fabricar constantemente componentes de alta calidad que respaldan el éxito de su negocio.
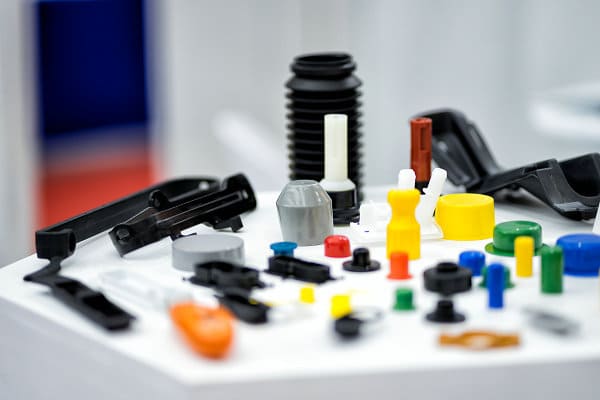
Solicitar presupuesto
Moldeo por inyección personalizado
El moldeo por inyección es un proceso de fabricación rentable para grandes volúmenes de piezas de plástico personalizadas. El proceso de moldeo por inyección implica insertar plástico fundido en una herramienta de moldeo y luego retirar la sección solidificada. El ciclo se repite varias veces, abaratando el costo de moldeado y, por ende, el precio de cada unidad.
Debido a que el proceso de moldeo por inyección utiliza una herramienta de moldeo similar para cada pieza, proporciona una calidad constante en cada producto. Además, el moldeo por inyección tiene una amplia variedad de pulidos, materiales, cosméticos y colores en comparación con la impresión 3D o el mecanizado CNC.
Los servicios de moldeo por inyección de plástico personalizados de Moldie son únicos. Ofrecemos servicios excepcionales que superan las expectativas de nuestros clientes. Una vez que recibimos su pedido, buscamos el proveedor de moldeo por inyección adecuado para moldear las piezas de la forma que desee, al precio adecuado y sin comprometer el diseño.
Además, ofrecemos servicios flexibles. Contamos con herramientas sofisticadas, un equipo de profesionales y recursos que brindan piezas personalizadas para clientes en diversas industrias. Además de eso, trabajamos en un plazo de entrega corto. Todos nuestros procesos están optimizados. Esto garantiza que reciba su pedido en el tiempo deseado.
Las ventajas del moldeo por inyección personalizado
El moldeo por inyección de plástico ofrece numerosas ventajas, incluidas las siguientes:
1. Es rentable
El moldeo por inyección de plástico es un proceso automatizado. Por lo tanto, los costos de mano de obra son relativamente bajos en comparación con otros métodos de fabricación de plástico. Además, el moldeo por inyección produce las piezas a un alto nivel con una alta tasa de producción, lo que reduce los costos de fabricación debido a su eficacia.
2. El moldeo por inyección de plástico ofrece mayor resistencia
Las piezas moldeadas por inyección de plástico resultantes del proceso de inyección tienen una mayor resistencia. Esto se debe a que puede usar rellenos en moldes de inyección. Estos rellenos reducen la densidad plástica durante el moldeo y agregan mayor resistencia a las piezas moldeadas.
3. Ofrece flexibilidad en material y color.
Hoy en día, numerosos materiales son compatibles con el proceso de moldeo por inyección de plástico. Con todas las opciones disponibles, puede elegir fácilmente un material con las propiedades químicas, físicas y mecánicas adecuadas. Aparte de eso, puedes colorear los plásticos usando varios sistemas de coloración.
4. El moldeo por inyección de plástico admite geometrías complejas con tolerancias estrictas
El moldeo por inyección personalizado permite la generación de piezas complejas consistentes y de gran volumen. Para maximizar la eficiencia del moldeo por inyección de gran volumen y optimizar la precisión y calidad de sus porciones, debe considerar los elementos de diseño. Con el diseño adecuado, puede producir piezas de alta calidad de forma constante.
Con el moldeo por inyección, puede obtener rápidamente piezas repetibles con tolerancias estrictas, brindándole productos precisos para numerosas aplicaciones y comparables a las piezas de máquinas CNC.
5. Conduce a Reducción de Residuos
El proceso de moldeo por inyección de plástico genera menos residuos de material de postproducción que la fabricación convencional. Además, puede volver a moler y reciclar cualquier desperdicio de plástico para uso futuro.
6. El moldeado de plástico personalizado ofrece varios acabados
La mayoría de las piezas moldeadas tienen un acabado superficial suave, casi igual al aspecto final deseado. Sin embargo, un aspecto liso solo es adecuado para algunas aplicaciones. Según las propiedades del material, el método de moldeo por inyección produce acabados que no necesitan acciones secundarias. Puede agregar texturas únicas, tener acabados mate o tener grabados.
7. Proporciona alta repetibilidad
Otra ventaja importante del moldeo por inyección personalizado es que es muy repetible. Después de crear el molde, puede generar numerosas piezas similares antes de realizar el mantenimiento de la herramienta. Esto se traduce en un bajo costo de producción.
8. Es muy eficaz y de rápida producción.
El moldeo por inyección personalizado se encuentra entre los métodos de producción más rápidos. La producción es alta, lo que la hace más efectiva y rentable. Principalmente, la velocidad depende de la complejidad del diseño y el tamaño de su molde, pero un molde típico tarda entre 5 y 20 minutos.
Esto promueve la producción de más moldes en un tiempo limitado, aumentando así los márgenes de beneficio. Además, algunos moldes tienen varias cavidades, lo que hace que se produzcan más piezas en un ciclo de moldeo.
Capacidades de moldeo por inyección
En cuanto a las capacidades de inyección de plástico personalizadas, estamos orgullosos de estar entre las principales empresas de moldeo por inyección que proporcionan piezas únicas y definidas con precisión que pueden impulsar las máquinas y los procedimientos en varias empresas esenciales a nivel mundial.
Nuestras capacidades de moldeo por inyección nos permiten producir piezas con formas distintivas que no se pueden crear con otros métodos. Utilizamos máquinas de múltiples cavidades, individuales y familiares para producir productos moldeados por inyección de alta calidad de manera rentable.
Además, trabajamos en estrecha colaboración con usted para planificar y organizar soluciones innovadoras. Somos expertos en conversión de metal a plástico, durabilidad y diseño de componentes, lo que reduce el tiempo y el costo de producción y mejora la eficiencia. Somos conocidos por nuestro procedimiento particular para reducir costos y tiempos de entrega y aumentar las capacidades de producción de diferentes industrias.
Proceso de moldeo por inyección
El moldeo por inyección de plástico personalizado necesita tres elementos fundamentales: una materia prima plástica, una máquina de moldeo por inyección y un molde. Los moldes para inyección de plástico están compuestos por elementos de acero y aluminio de alta resistencia programados para funcionar en dos mitades. Cada mitad se ensambla dentro de la máquina de moldeo para formar una pieza de plástico personalizada.
Después de eso, la máquina inyecta plástico fundido en el molde, donde se solidifica para formar el producto final. El proceso de moldeo por inyección personalizado sigue especificaciones estrictas y se logra en los siguientes pasos:
1. Reprimición
El primer paso del método de moldeo por inyección es la sujeción. Generalmente, los moldes de inyección están hechos de dos mitades. En este paso, la máquina cierra estas mitades antes de insertar el plástico en el molde para evitar que el molde se abra durante el paso de inyección.
2. Inyección
En este paso, el plástico crudo, generalmente en forma de pequeños gránulos, se inserta en la máquina de moldeo por inyección en la sección de la zona de alimentación de un tornillo alternativo. La temperatura y la compresión calientan el material plástico a medida que el tornillo transmite los gránulos de plástico a través de las áreas calentadas del cilindro de la máquina.
La cantidad de plástico derretido que se transmite al frente del tornillo se mide con precisión, ya que esa es la cantidad que formará la pieza final después de la inyección.
Cuando llega la cantidad adecuada de gránulos de plástico fundido al frente del tornillo, y el molde está bien sujeto, la máquina lo introduce en el molde, llevándolo hasta la última parte de la cavidad a alta presión.
3. Enfriamiento
Una vez que el plástico fundido toca las superficies internas del molde, se enfría. El método de enfriamiento solidifica la forma y la dureza de la pieza de plástico recién moldeada. El tiempo de enfriamiento requerido para cada pieza moldeada de plástico depende del grosor de la pared, las propiedades termodinámicas del plástico y la necesidad dimensional de las piezas personalizadas.
4. Expulsión
Después del enfriamiento, la máquina suelta y abre el molde de inyección de plástico. El dispositivo está equipado con dispositivos mecánicos que operan con componentes desarrollados dentro del molde de inyección de plástico para extraer la pieza. En esta etapa, la pieza moldeada a la medida se expulsa y el molde está listo para el siguiente movimiento cuando la nueva pieza se expulsa por completo.
Materiales de moldeo por inyección de plástico personalizados
Los materiales de moldeo por inyección de plástico personalizados se clasifican de las siguientes maneras:
1. Materiales Plásticos Rígidos
A continuación se presentan algunos materiales en esta categoría:
- Poliacrilamida (PARA)
Esto se mezcla principalmente con rellenos como fibras minerales o vidrio. Genera secciones rígidas con baja fluencia y una tasa de absorción de agua más lenta que el nailon. PARA es perfecto para elementos estructurales en electrónica médica y dispositivos portátiles.
- Policarbonato (PC)
El PC es un material ligero, transparente y duradero alternativo al vidrio. Debido a su alta durabilidad y extrema resistencia a los impactos, la mayoría de las industrias utilizan PC en varias aplicaciones, incluidos dispositivos electrónicos, lentes, equipos de seguridad, etc.
- Polietileno (PE)
Este es un polímero de grado de consumo que puede elegir en función de la densidad, lo que lo convierte en uno de los plásticos más utilizados en todo el mundo. Puede tener baja densidad (LDPE), alta densidad (HDPE) o tereftalato de polietileno (PET, PETE).
Los plásticos PE tienen alta elasticidad, resistencia a la abrasión y resistencia química. Se utilizan mejor para moldear por inyección artículos más grandes, a menudo utilizados en botellas, películas, tubos, envases, etc.
- Acrilonitrilo Butadieno Estireno (ABS)
Este es un material termoplástico amorfo con un punto de fusión bajo. Es compatible con colorantes y contiene innumerables opciones de texturas y acabados. El ABS es altamente resistente a los impactos y robusto. Sin embargo, tiene una resistencia débil a la alta fricción, los rayos UV, los solventes y los elementos climáticos. Además, libera humo denso cuando se quema.
El ABS se utiliza mejor en bienes de consumo, componentes y cubiertas electrónicos, equipos deportivos y piezas de automóviles.
- Polipropileno (PP)
Este es también otro plástico de uso común a nivel mundial. Es principalmente similar al PE pero es más resistente al calor y un poco más duro. En el moldeo por inyección, puedes reciclar este material y combinarlo con otros materiales plásticos. Debido a su baja densidad, el PP se utiliza para contenedores de almacenamiento, bisagras vivas para botellas de plástico, herramientas eléctricas y artículos deportivos.
- Poliuretano Termoplástico (TPU)
El TPU es conocido por su resistencia a los aceites, la abrasión y los productos químicos y su capacidad para soportar altas temperaturas. Viene en diferentes grados, incluyendo médicos, industriales y comerciales. Por lo tanto, se adapta mejor a ruedas, zapatos, dispositivos médicos y carcasas electrónicas.
- Poliftalamida (PPA)
PPA es un subgrupo de nailon que normalmente tiene baja absorción de humedad y alto punto de fusión. Se utiliza en aplicaciones automotrices e industriales ya que puede resistir productos químicos agresivos. Además, es bueno en carcasas de faros y colectores de combustible.
- Fluoruro de polivinilideno (PVDF)
Este es un material químicamente inerte de alta temperatura. Debido a su baja fricción, el PCDF se usa en rodamientos, tuberías, piezas de plomería, aislamiento de cables eléctricos y manipulación de productos químicos.
- Poliolefina termoplástica (TPO)
TPO tiene buena resistencia química y es flexible, pero tiene menor resistencia a la temperatura que PP.
- Estireno acrilonitrilo (SNA)
SNA es un poliestireno transparente y resistente al calor. Es popular en utensilios de cocina, manijas de puertas y artículos para el hogar.
- Cloruro de polivinilo (PVC)
Este es un plástico rígido versátil que se utiliza en recortes, empaques no alimentarios y plomería.
- Sulfuro de polifenileno, Ryton (PPS)
El PPS es un termoplástico de alto rendimiento que es altamente resistente a los solventes.
- Acetal polioximetileno (POM)
Este tiene alta resistencia al desgaste, baja fricción y buena resistencia a la humedad.
- Éteres de poliestireno-polifenilo (PS-PPE)
PS-PPE presenta una alta resistencia al calor y a las llamas. Además, tiene resistencia a la tracción y alta rigidez incluso cuando se somete a altas temperaturas.
- Acrilato de acrilonitrilo estireno (ASA)
Este material es casi el mismo que el ABS, pero tiene una mayor resistencia a la decoloración y, por lo tanto, se usa para exteriores.
- Polietileno de baja densidad (LDPE)
Un material flexible y duro que no es reactivo en alcoholes, ácidos y bases. Es más adecuado para tapas a presión, contenedores de uso general y bandejas.
- Acetato de celulosa (CA)
CA es un material flexible que se puede utilizar en la película, anteojos o contacto con alimentos.
- Polímero de cristal líquido (LCP)
LCP ofrece características únicas para componentes de paredes delgadas y micromoldeo. Es común en dispositivos médicos e interconexiones y conectores eléctricos.
- Polietileno de alta densidad (HDPE)
Tiene una perfecta relación resistencia-peso y resistividad química. El HDPE se usa principalmente para aisladores de conectores, contenedores de alimentos y tanques de combustible. También se puede utilizar en equipos exteriores como parques infantiles.
- Poliamida 6/6, nailon 6 (PA 6/6)
Esto proporciona una mayor resistencia mecánica, excelente estabilidad al calor, rigidez y resistencia química.
- Tereftalato de polibutileno (PBT)
Este es un aislador electrónico popular que tiene una base de poliéster. Se aplica principalmente en automoción como una opción de mayor duración al nailon.
- Poliéter éter cetona (PEEK)
PEEK proporciona una resistencia a la tracción excepcional que supera a la mayoría de los plásticos. Por esa razón, se usa principalmente como una alternativa liviana a las piezas metálicas en aplicaciones de alta tensión y altas temperaturas.
- Policarbonato-acrilonitrilo butadieno estireno (PC-ABS)
Como sugiere el nombre, esta es una combinación de PC y ABS que da como resultado un termoplástico de ingeniería de mayor resistencia que es más flexible que el policarbonato común.
- Polieterimida (PEI)
Esto es conocido por su alta resistencia a las llamas y al calor. Se aplica en la mayoría de los usos médicos y es más rentable que PEEK.
- Polietersulfona (PES)
PES es un plástico rígido y transparente, biocompatible, esterilizable y químicamente inerte. Es apto para equipos en contacto con alimentos, como componentes de máquinas de café. También es aplicable en industrias de alta exposición química como la automotriz y aeroespacial.
- Tereftalato de policiclohexilendimetileno (PCT)
Este material tiene buena estabilidad ambiental y baja absorción de humedad. Se utiliza principalmente en interruptores y conectores.
- Policarbonato-tereftalato de polietileno (PC-PET)
Esta es una combinación de PC y PET para producir un producto que es fuerte y químicamente resistente y puede usarse como sustituto de PC-ABS. Soporta solventes y productos químicos agresivos, lo que lo hace perfecto para aplicaciones de atención médica y equipos deportivos.
- Policarbonato-tereftalato de polibutileno (PC-PBT)
Tiene características similares a PC-PET y es popular en gabinetes electrónicos.
- Tereftalato de polietileno (PET)
También conocido como PETE, el PET es una resina de PE fuerte, liviana y transparente que se usa en botellas de refrescos, frascos, envases de alimentos, etc. El PET es apto para alimentos y es reciclable con un código de resina de 1.
- Poliestireno de alto impacto (HIPS)
Este es un plástico versátil, económico y resistente a los impactos que está hecho de caucho y estireno cristal. HIPS es adecuado para componentes de calidad alimentaria debido a sus propiedades no tóxicas.
- Metacrilato de polimetilo (PMMA)
El PMMA es un plástico similar a los pasillos que es transparente y tiene buenas características de uso y desgaste. Es la mejor opción para uso en exteriores.
- Ácido poliláctico (PLA)
Este es un plástico ecológico y reutilizable que tiene una temperatura de transición vítrea baja. Es popular en aplicaciones de uso breve.
- Poliamida (Nylon)
El nailon proporciona excelentes propiedades eléctricas, resistencia al desgaste por calor y productos químicos, y resistencia. Las industrias médica y automotriz utilizan con frecuencia nailon para piezas moldeadas por inyección de plástico personalizadas.
2. Materiales moldeados de caucho y elastómero
- Vulcanizados termoplásticos (TPV)
El TPV es un material termoplástico duro que contiene partes de caucho blando interconectado repartidas por toda su matriz polimérica. TPV proporciona una sensación suave, alta compresión y acabado mate. Se aplica en parachoques, aplicaciones debajo del capó, sellos, fundas y ojales.
- Poliuretano termoplástico (TPU)
El TPU es conocido por su buena claridad, dureza media a alta, buen desgaste, resistencia al desgarro, abrasión y deformación moderada por compresión. Es ideal para aplicaciones al aire libre, incluidas ruedas de monopatín, neumáticos flexibles, fundas protectoras, juntas resistentes a la intemperie y dispositivos médicos.
- Amida de bloque de poliéter (PEBA)
PEBA está hecho de bloques duros de poliamida que fluctúan con bloques elastoméricos blandos. Tiene buena resistencia al impacto, fluencia y fatiga por flexión. Además, tiene juegos de compresión bajos y puede prosperar bien a altas temperaturas. Las espumas PEBA se utilizan en equipos deportivos, almohadillas, plantillas para zapatos, productos electrónicos y equipos médicos.
- Elastómero termoplástico (TPE)
Este es un amplio grupo de elastómeros que actúan como un termoestable con elasticidad y alta flexión pero se comportan como un termoplástico durante el moldeo.
- Goma de silicona líquida (LSR)
Las siliconas son materiales de goma flexibles con alta resistencia al calor, maravillosa versatilidad y que proporcionan alimentos y biocompatibilidad. LSR se utiliza en productos de consumo, automoción, aeroespacial y dispositivos médicos.
- Caucho monómero de etileno propileno dieno (EPDM)
Este es uno de los elastómeros de caucho de más alto funcionamiento con características superiores de resistencia química y al calor y sellado contra la humedad. Se usa comúnmente en aisladores eléctricos, juntas, sellos automotrices y juntas tóricas.
Clases de moldes de moldeo por inyección
Tenemos las siguientes clases de moldes de moldeo:
1. Clasificación de moho SPI
Las herramientas de moldeo por inyección convencionales se describen en clases desde la clase 105 (prototipo) hasta la clase 101 (producción de alto volumen). Esas clases de moldes ayudan a administrar tanto a los proveedores de moldeo por inyección como a los clientes en cuanto a las demandas y el alcance generales de las herramientas. A continuación se muestra un esquema de las distintas clases:
- molde clase 105
Este es un molde de menos de 500 ciclos y se genera de la manera menos costosa posible para crear una cantidad mínima de piezas prototipo. Esta clase también se conoce como herramientas de clase V.
- molde clase 104
Esta clase está por debajo de los 100.000 ciclos y es un molde de baja producción. Se utiliza solo para producción restringida, preferiblemente con materiales no abrasivos.
- molde clase 103
Esto está por debajo de los 500 000 ciclos y es popular para requisitos de producción bajos a medios. También es el rango de precio más popular.
- molde clase 102
Este es un molde de primera clase y alto precio que se utiliza para herramientas de producción media a alta. Es ideal para materiales abrasivos o secciones que necesitan tolerancia estrecha.
- Clase 101
Esto está por encima de 1.000.000 de ciclos y está diseñado para una producción extremadamente alta. Es el molde de mayor precio y se crea solo con materiales de calidad superior.
Acabados de moldes de inyección personalizados
Hay disponibles varias selecciones de acabado de superficie para piezas de plástico moldeadas a medida. Los procesos de acabado de superficies para el moldeo por inyección pueden ayudar a disminuir o aumentar la aspereza de una pieza. Por ejemplo, los acabados más rugosos son ideales para ciertas partes mecánicas, mientras que la textura brillante se adapta a partes estéticas como los juguetes.
La sociedad de la industria del plástico (SPI) ideó estándares de la industria para acabados de moldeo por inyección de plástico, como se describe a continuación:
1. Acabado de superficie de moldeo por inyección brillante
Las piezas de plástico moldeado se pueden hacer más brillantes mediante un proceso de acabado como el pulido con diamante. En dicho método, una empresa de moldeo por inyección utiliza un material abrasivo suelto en una rueda de trabajo. Posteriormente, utilizan esto en piezas con la mínima agresión, produciendo piezas con los acabados más brillantes posibles.
2. Acabado superficial de moldeo por inyección semibrillante
Este acabado es adecuado para piezas que necesitan algo de brillo. Se utiliza una lija de grano. Este proceso funciona bien con una gran cantidad de plásticos moldeados por inyección. También se utiliza para producir piezas de alta estética adecuadas para productos de consumo.
3. Acabado superficial de moldeo por inyección mate
Este proceso consiste en eliminar las marcas de mecanizado de las piezas moldeadas sin generar un acabado brillante. Es ideal para piezas que carecen de valor estético pero que necesitan un acabado de superficie consistente. Ofrece una textura de superficie de molde de alta calidad y no muestra marcas perceptibles.
4. Acabado de superficie de moldeo por inyección texturizado
En algunos casos, puede requerir un acabado muy rugoso para aumentar la fricción, como en usos mecánicos. Puede utilizar un proceso de chorro de arena para aplicar un acabado superficial rugoso en tal caso. El pulido con chorro de arena utiliza aire comprimido para dirigir el material abrasivo contra la pieza con fuerza, volviendo rugosa su superficie.
Otros acabados comunes incluyen los siguientes:
- Lijado
- anodizado
- galvanoplastia
- Pulido
- Recubrimiento de energía
- Cuadro
Con el acabado de moldeado de plástico personalizado adecuado, seguramente tendrá piezas de plástico personalizadas duraderas. Trabajar con nosotros le permite lograr esto e impresionar a sus clientes. Nuestro equipo de expertos está bien versado en todos los acabados y puede sugerir materiales y acabados termoplásticos adecuados para productos particulares. Por lo tanto, asóciese con nosotros hoy y obtenga una ventaja competitiva con los mejores servicios.
Inspecciones de calidad y opciones de acabado para piezas moldeadas personalizadas
Al solicitar una cotización de moldeo por inyección, puede seleccionar entre las siguientes opciones según las necesidades de su aplicación:
1. Inspecciones de calidad disponibles para pedidos de fabricación bajo demanda
Tienes las siguientes opciones:
- Inspección de CMM en proceso y monitoreo de máquinas
- Informe de desarrollo del proceso de moldeo científico
- Inspección de primer artículo (FAI) e informe de capacidad del proceso con GD&T
- Diseño para comentarios de capacidad de fabricación (DFM)
2. Postprocesamiento
Bajo esta opción, usted tiene:
- Tampografía
- Montaje de componentes
- insertos roscados
- Grabado láser
- Texturizado de moldes
preguntas frecuentes
1. ¿Por qué los moldes de inyección de plástico cuestan tanto?
Varios factores contribuyen a los altos costos de los moldes de inyección de plástico. Uno de los factores principales son los propios moldes. Para producir piezas de plástico de calidad superior, debe utilizar un molde de inyección construido de alta calidad. Los moldes para inyección de plástico están hechos de elementos mecanizados generados a partir de diferentes metales, como aceros para moldes endurecidos y aluminio de calidad aeronáutica.
Luego, los moldes son diseñados y creados por expertos, también conocidos como fabricantes de moldes. Estas personas llevan varios años aprendiendo el oficio de hacer moldes. Por lo tanto, están bien versados en este proceso de producción de moldes de alta calidad. Su remuneración contribuye al alto costo de los moldes de inyección de plástico.
Además, los fabricantes de moldes requieren herramientas muy costosas para realizar su trabajo, como máquinas CNC, software de última generación, accesorios de precisión y herramientas. Otros factores que contribuyen al alto costo de la inyección de plástico personalizada incluyen los siguientes:
Diseño de molde
El diseño de moldeo por inyección personalizado tiene un impacto significativo en su precio. El procedimiento de moldeo por inyección de plástico personalizado requiere mucha presión cuando la máquina inyecta el plástico en las cavidades del molde. Sin la alta presión, las piezas moldeadas por inyección no tendrán los acabados superficiales deseados y pueden ser dimensionalmente incorrectas.
Requisitos de construcción de moldes
Otro factor significativo asociado con el alto costo de los moldes de inyección son las demandas de construcción del molde. La construcción debe ser precisa para que un molde de inyección funcione correctamente durante el procedimiento de moldeo por inyección de plástico personalizado. Aunque los moldes se describen como dos mitades, un núcleo y un lado de la cavidad, por lo general varias piezas de precisión constituyen cada mitad.
Casi todos los elementos de molde mecanizados con precisión que ensamblarán y producirán sus piezas moldeadas personalizadas están instrumentados con tolerancias de 0,025 mm o +/-0,001". Un papel de copia convencional tiene un grosor de 0,089 mm o 0,0035''. Por lo tanto, un fabricante de moldes debe ser muy preciso para cortar su papel de copia en tres piezas ultrafinas y construir su molde con precisión.
La complejidad de la Parte
Cuanto más compleja sea su pieza, más caro será su molde de inyección. Además, el molde puede ser muy difícil o incluso imposible de modificar una vez creado mediante moldeo por compresión. Esto hace que sea un desafío para usted cambiar el diseño.
Materiales del molde
Para que su molde resista las presiones a las que está sujeto durante el proceso de moldeo por inyección personalizado, debe estar hecho de aluminio y acero de calidad superior. Además, debe estar hecho para resistir las fuerzas de sujeción e inyección.
2. ¿Cómo saber si el moldeo por inyección es el proceso adecuado para un producto?
Varios factores influyen en su decisión sobre si el moldeo por inyección personalizado es apropiado para usted. Estos factores incluyen su presupuesto, la cantidad de piezas requeridas, la geometría de la pieza y la aplicación de la pieza.
3. ¿Cuánto tiempo se tarda en construir un nuevo molde?
Puede tomar un promedio de 8 a 10 semanas, según la complejidad del diseño y las cavidades del molde.
4. ¿Se mantendrán los moldes de mi pieza entre ciclos de producción?
Es menos probable que los moldes se mantengan entre ciclos de producción. Sin embargo, esto puede depender de factores como el material del molde de inyección, las condiciones de funcionamiento, los tiempos de ciclo y el tiempo entre ciclos de producción. Puede usar estos factores para determinar si puede mantener sus moldes en cualquier momento.