Forma odlewnicza
Nasi doświadczeni inżynierowie wykorzystują najnowszą obróbkę CAD/CAM i CNC, aby produkować wysokiej jakości, trwałe formy zoptymalizowane pod kątem Twojego zastosowania. Oferujemy kompletne usługi projektowania form, w tym analizę wykonalności, symulację i prototypowanie, aby zapewnić doskonałe działanie formy. Dzięki zaawansowanemu sprzętowi i wiedzy specjalistycznej Moldie dostarcza złożone formy odlewnicze o wąskich tolerancjach, dostosowane do Twoich specyfikacji. Nasze formy umożliwiają szybką i wydajną produkcję wysokiej jakości części odlewanych ciśnieniowo w dużych ilościach.
Skontaktuj się z firmą Moldie już dziś, aby rozpocząć prace nad niestandardowym projektem formy do odlewania ciśnieniowego.
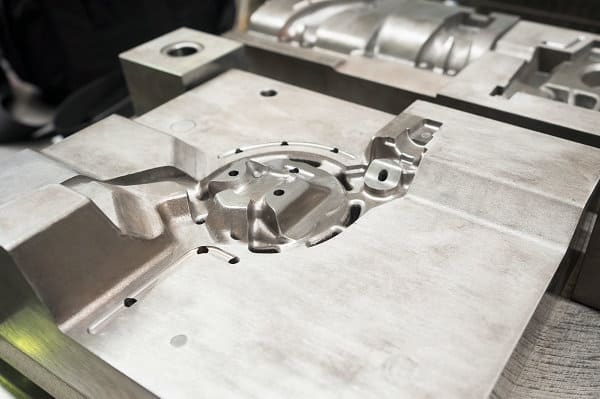
Poprosić o wycenę
Co to jest forma odlewnicza?
Forma odlewnicza to precyzyjne narzędzie służące do produkcji części metalowych poprzez odlewanie ciśnieniowe, wydajny proces produkcyjny, w którym stopiony metal jest wtryskiwany pod wysokim ciśnieniem do wnęki formy. Forma składa się z dwóch połówek – nieruchomej i ruchomej. Po zamknięciu wnęka między nimi tworzy pożądany kształt odlewanej części.
Formy do odlewania ciśnieniowego są wykonane ze stali narzędziowej lub aluminium i mogą wytwarzać złożone geometrie z doskonałą dokładnością, powtarzalnością i wykończeniem powierzchni. Są szeroko stosowane do produkcji części metalowych dla przemysłu motoryzacyjnego, lotniczego i produktów konsumenckich.
Projekt formy odlewniczej
Konstrukcja formy do odlewania ciśnieniowego wymaga zaawansowanej inżynierii, aby osiągnąć wąskie tolerancje wymagane w przypadku wysokiej jakości odlewów. Kluczowe czynniki projektowe obejmują:
- Linie podziału: Linia podziału pomiędzy dwiema połówkami formy musi umożliwiać łatwe wyrzucanie części. Linie podziału są umieszczane tak, aby uniknąć podcięć.
- Kąty pochylenia: Wszystkie powierzchnie pionowe muszą mieć lekkie zwężenie (kąt pochylenia), aby ułatwić wyrzucanie. Typowe kąty pochylenia wynoszą 1-3 stopnie.
- System wyrzutowy: Kołki wypychające i tuleje są wbudowane w formę, aby wypychać zestalony odlew z wnęki.
- System chłodzenia: W formie wiercone są kanały umożliwiające cyrkulację wody lub oleju w celu odprowadzania ciepła i szybkiego zestalenia odlewu.
- System mocowania: Zaciski utrzymują obie połówki w jednej linii pod ogromnym ciśnieniem podczas wtrysku.
- System bram i prowadnic: Kanały dostarczające stopiony metal do wnęki.
Produkcja form odlewniczych
Wysokiej jakości formy odlewnicze wymagają specjalistycznej obróbki i polerowania, aby osiągnąć precyzję na poziomie mikronów. Etapy produkcji obejmują:
- Tworzenie modeli CAD na podstawie rysunków części.
- Obróbka CNC bloków form ze stali lub aluminium.
- Dodatkowe procesy CNC, takie jak frezowanie, wiercenie i szlifowanie w celu uzyskania ostatecznej geometrii formy.
- Ręczne polerowanie i ławkowanie w celu uzyskania wymaganego wykończenia powierzchni.
- Montaż dwóch połówek formy i włączenie wypychaczy, chłodzenie i zaciskanie.
W przypadku skomplikowanych form cały proces wytwarzania form może zająć tygodnie lub miesiące. Właściwy projekt formy i obróbka mają kluczowe znaczenie dla produkcji dokładnych, spójnych części odlewanych ciśnieniowo.
Zalety form odlewniczych
- Produkcja wielkoseryjna z szybszymi cyklami i mniejszym nakładem pracy w porównaniu z innymi procesami.
- Doskonała dokładność wymiarowa i powtarzalność.
- Gładkie wykończenie powierzchni bez obróbki wtórnej.
- Możliwość wytwarzania skomplikowanych kształtów niemożliwych do osiągnięcia innymi metodami.
- Różnorodne opcje stopów, w tym aluminium, cynk i magnez.
- Niższe koszty oprzyrządowania w porównaniu do formowania wtryskowego tworzyw sztucznych.
Dzięki starannemu projektowaniu i obróbce formy do odlewania ciśnieniowego mogą wyprodukować miliony precyzyjnych części metalowych przez wiele lat pracy. Są jednym z najbardziej wydajnych i opłacalnych sposobów wytwarzania elementów metalowych.
Skontaktuj się z firmą Moldie już dziś, aby rozpocząć prace nad niestandardowym projektem formy do odlewania ciśnieniowego.