Plastic Injection Mold Making
Our engineers use the latest 3D modeling and simulation to optimize molds for flawless plastic part production over hundreds of thousands of cycles. Through advanced CNC machining, EDM, and finishing, we fabricate molds capable of dimensional accuracy and flash-free molding. With comprehensive capabilities from design to finished tooling, Moldie provides a one-stop injection mold solution ensuring quality, fast turnaround, and cost-effectiveness.
Contact us to discuss how our complete mold making services can deliver molds to meet your exact injection molding requirements.
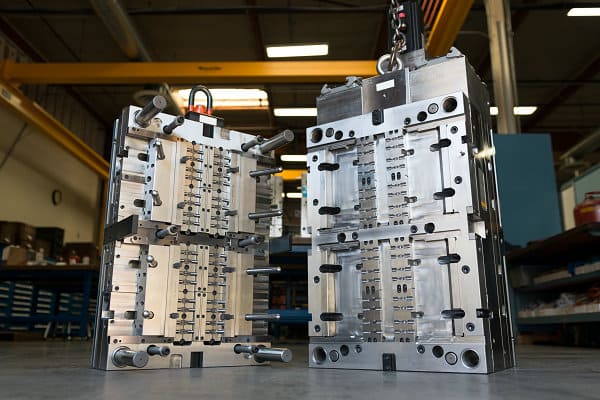
Request a Quote
Moldie – Experts in Precision Plastic Injection Mold Making
Moldie specializes in expertly designing and precisely manufacturing high-quality plastic injection molds to meet your exact specifications. Our experienced mold makers use the latest processes and advanced manufacturing technologies to produce molds capable of flawless, repeatable molding.
Custom Mold Design Optimized for Your Application
Our mold making process begins with our engineers analyzing your product design and specifications. We use precision CAD software to design the optimal mold configuration including the number of cavities, runner and cooling systems, ejector pins, and other critical components.
We optimize our mold designs to meet your specific material requirements, part geometries, shot sizes, and production volumes. The process starts with a consultation to understand your needs and goals. Next, we create a detailed design plan and 3D mold model using CAD software.
We then use precision CNC machining to fabricate the mold components to the required specifications. Once complete, we assemble and test the molds to ensure they meet all necessary quality and performance standards.
Throughout the process, we maintain strict quality control protocols to ensure every mold meets our high accuracy and performance standards. We also offer ongoing support and maintenance services so customers can rely on their molds for years.
Different Types of Plastic Injection Molds
At Moldie, we produce a wide range of injection molds for various industries and applications, including:
- Single Cavity Molds – For small or simple parts with lower production volumes
- Multiple Cavity Molds – For larger, more complex parts requiring high production volumes
- Stack Molds – Produce multiple layers of parts in one cycle by stacking molds
- Hot Runner Molds – Maintain constant molten plastic flow for faster production
- Two-Shot Molds – Produce parts with multiple materials/colors in one cycle
No matter what type of mold you need, Moldie has the expertise and experience to produce high-quality, customized molds that meet your specific requirements.
Overview of the Injection Molding Process
Plastic injection molding is a manufacturing process that produces plastic parts by injecting molten material into a mold. It is a highly efficient and cost-effective method for high-volume production of identical plastic parts.
The process starts with a mold created using CAD software and CNC machining. The steel or aluminum mold is designed to withstand the high pressures and temperatures.
Once complete, the mold is loaded into an injection molding machine. The machine melts the plastic material and injects it into the mold under high pressure. The plastic cools and solidifies, taking the shape of the mold cavity.
After solidifying, the mold opens and the finished part is ejected. The part is inspected and any necessary post-processing is performed.
Injection molding is highly efficient and can produce large volumes of identical parts quickly. It is commonly used across many industries.
Factors that Contribute to Injection Mold Costs
Plastic injection molds can be expensive due to several factors:
- Design complexity – Molds for complex parts require more tooling and machining time.
- Mold size – Larger molds require more material and machining.
- Mold materials – More durable materials are more expensive.
- Production quantity – Molds for higher quantities cost more.
- Lead time – Rush orders may require additional fees.
The combination of these factors determines the overall mold cost. Working with an experienced manufacturer ensures you get the best value.
Contact Us
Please contact us if you have any questions or would like a project quote. We look forward to helping bring your project to life!