Zinc Die Casting
Zinc Die Casting Service
In addition, our zinc die casting process utilizes the latest technology to ascertain that we offer you the best zinc die casting parts. Our services are affordable, and the cost of parts depends on your customization needs.
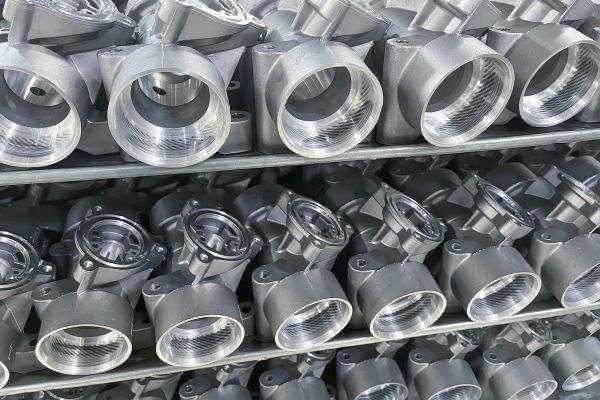
Request a Quote
Zinc die castings are popular in the industrial sector and are used to create several metal parts. Ideally, molten metal is injected into molds that are in the form of die under high pressure to make complex products. Zinc die casting is similar to plastic injection molding, with the primary difference being the material used. In die casting, the materials used to make mold parts are metallic.
Zinc die castings are the most preferred materials because of their mechanical properties. This is because zinc alloys are tough and tough at average temperatures compared to other alloys, such as aluminum die casting, brass, and gray iron.
Zinc alloy die casting produces stronger, tougher, and more stable parts than plastic injection molds despite having complex dimensions. In addition, the zinc die casting process is more cost-effective compared to other casting methods and materials.
Physical And Mechanical Properties
Some of the physical properties and mechanical attributes of zinc die casting are as follows:
- A density of 6.7g per metric cube.
- Tensile strength of about 387MPa.
- Yield strength of 319MPa.
- Elongation at break of about 3.40%.
- Poisson’s ratio of 0.29.
These properties make zinc die casting preferable for parts often subjected to high pressure.
Advantages Of Zinc Die Casting
As mentioned before, zinc die casting is preferable for several reasons. Some of the advantages of zinc die casting include the following:
- Zinc alloy is a strong metal.
- Zinc alloy is durable because of its chemical composition.
- The zinc alloy is cost-effective, therefore, economical.
- High performance because of the toughness and rigidity of the zinc alloy.
- Reduced assembly operations because the die casting process can be done as a single unit.
- Fewer materials can be used because zinc alloy fluidity and stiffness make thinner walls.
- Reduced machining operations because of the net-shaping capabilities of the zinc alloys.
- Allows different forms of aesthetic surface finish.
- The zinc die cast components are environment-friendly, thus reducing pollution.
The benefits of zinc castings are numerous, making them perfect for industrial use.
Zinc Die Casting Applications
The unique factors and chemical and mechanical composition of zinc die make it suitable for many applications. In addition, zinc die casting is cost-effective and, therefore, ideal for making parts used in the following industries:
- Electronic components
- Automotive parts and equipment
- Office equipment
- Door, window, and bath fittings
- Mechanical designs
Zinc alloy die casting can also make other customized parts depending on your needs. You can call us for a consultation on the die casting parts you need to be customized.
Custom Zinc Die Casting Process
Zinc alloy die casting can be done through either a hot or cold chamber process. Both processes can give you the desired results if utilized correctly. Each process is unique and follows a different procedure.
For instance, the hot die casting chamber gives you superior control over the molten metal and its flow. A furnace is attached to the die casting machine during the die casting process through the gooseneck. The injection machine is then immersed into the molten metal in the furnace, from where it’s plunged into the die cavity. The final product from the zinc casting has distinct features and perfect surface finishing.
On the other hand, the cold die casting chamber functions in the opposite way. Here, the molten metal is poured into a cold chamber. Once in the chamber, a hydraulic plunger is used to seal the gate and force the molten into the die cavity using high pressure. Though this method is different, the final products are high-quality with amazing finishes.
The zinc casting process is faster than other metallic materials and is therefore suitable for high die casting production rates.
Zinc Zamak Alloys
Zinc casting alloys have two basic families; Zamak alloys and high-fluidity alloys. In the zamak family, the alloys are categorized depending on their sequential development, such as Alloy 2, Alloy 3, Alloy 4, and so on. Here are some of the main characteristics of these alloys:
- Zamak 2:This zinc alloy has the strongest and hardest qualities because of its copper components of about 3%. The presence of copper in zinc alloys affects its ductility and long-term changes. However, this alloy is perfect for removing bushing and wear inserts when making die cast designs.
- Zamak 3:This is also known as alloy 3, the most commonly used zinc alloy in North America. The alloy’s popularity is based on its physical and mechanical components, which make it stable. In addition, the surface finishing of the alloy is perfect for plating, painting, and chromate treatment. These properties create the standard for rating other alloys.
- Zamak 5: Unlike the Zamak 3, this alloy has created a reputation in Europe because of its castability characteristic and creep performance. Though alloy 5 has high performance, the improvements are at the expense of ductility, which affects secondary operations such as bending, swaging, and riveting. Another contrasting element of this alloy to Alloy 3 is that it contains copper components and is readily finished and plated.
- Zamak 7:This alloy has improved casting fluidity, surface finishes, and ductility because of low magnesium. These attributes make the alloy perfect for making thin-walled parts.
With that said, the choice of alloy used for zinc die castings depends on your needs and its availability in a region.
Conclusion
Zinc die castings are perfect for making industrial parts used under high pressure because of the strength and ductility of the materials. Zinc die cast alloys are suitable for many applications ranging from the automotive industry to electrical appliances. The fabricated components made from die cast zinc are often high-quality, depending on the expertise utilized during casting.