ABS stands for Acrylonitrile Butadiene Styrene. It’s a type of thermoplastic polymer with three major ingredients (monomers): acrylonitrile, butadiene, and styrene. The three monomers have different properties that combine to produce a robust ABS plastic that’s impact-resistant.
Below is more information about the monomers:
Acrylonitrile
Acrylonitrile is made of propylene and ammonia components. It imparts high chemical resistance, hardness, and heat stability to the plastic part.
Butadiene
Butadiene is produced during the formation of ethylene from steam crackers. It provides impact strength and resistance to the polymer.
Styrene
Styrene is made via the alkylation of benzene with ethylene to form ethylbenzene dehydrogenated to styrene. It offers rigidity, additional strength, glossy finish and is responsible for the processability of the ABS polymer.
At Moldie, we offer a wide range of injection molding services, including custom ABS injection molding. We guarantee our customers a seamless manufacturing process.
Properties of plastic ABS
Below are some of the ABS material properties:
ABS chemical structure: (C₈H₈·C₄H₆·C₃H₃N)ₙ
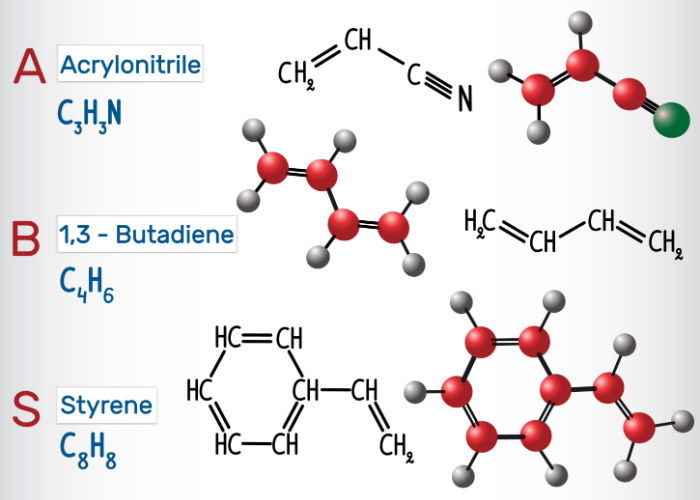
Resistance: ABS plastic has high chemical, strain, heat, and impact resistance.
Shrink rate: Its shrink rate is between o.5 – 0.7 %.
Temperature: Its typical temperature is 200-238 °C/392-460.4 °F.
Liquefying temperature: The thermoplastic liquefies when it reaches 105°C / 221°F.
Specific gravity: 1.06
Tensile strength: 46 MPa (6600 PSI)
Notably, ABS plastic offers a great balance in strength, resistance, electrical features, and other characteristics. These excellent properties have enabled the polymer to be used for various structural applications and product designs.
ABS injection molding process
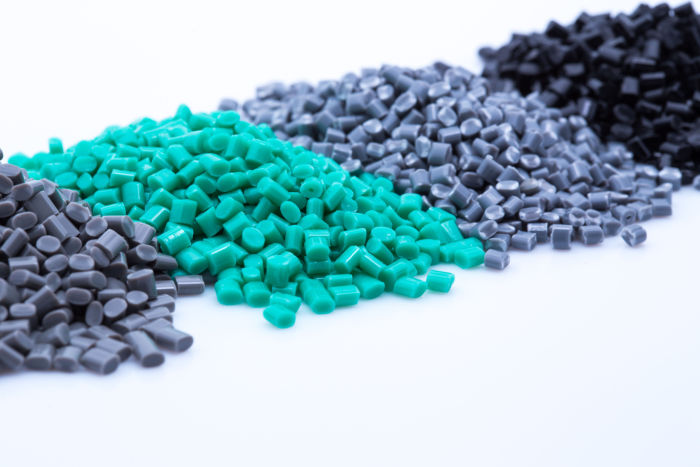
Here is the process cycle for ABS injection molding:
Injection: ABS plastic, in pellet form, is melted into a liquid form and then injected into the mold. The injection time will depend on the injection pressure applied, shot volume (amount of ABS material injected), and injection power.
Cooling: The molten plastic is cooled and solidifies to the mold’s shape. However, note that shrinkage may occur during the cooling process. Therefore, more melt is allowed to flow into the mold to reduce the amount of visible mold shrinkage. The cooling time depends on different thermodynamic plastic properties and the maximum wall thickness.
Ejection: After sufficient cooling, the cooled part can be ejected from the mold through the ejection system.
ABS plastic can be manufactured using most standard types of machinery. It can be blow-molded or injection-molded. Also, because it has a low melting point, about 200°C or 392°F, it can be best processed through 3D printing on an FDM machine.
As a reputable injection molding company, we use the latest manufacturing technologies to produce high-quality molded parts and fully meet your ABS molding needs.
ABS injection molding techniques
Thin-walled parts: Due to ABS’s high viscosity, injection pressure must be increased for thin-walled parts.
Thick-walled parts: Production of thick-walled parts using the standard techniques may result in sink marks. That’s why compression injection molding is recommended. It adds a particular amount of melt into the mold to create the final product.
Large hollow parts: Gas-assisted or water-assisted injection molding techniques are vital for producing large hollow parts.
Multi-material: Over-molding or insert molding may be necessary if you intend to create multi-material parts.
ABS injection molding processing considerations
Here are some aspects to consider during the ABS injection molding process:
Uniform wall thickness
The ABS plastic wall thickness should be uniform to withstand stress or strain. The producer can reinforce strength by implementing extra ribs or radii.
Dry ABS resins pre-treatment
ABS plastic material tends to absorb moisture at a rate of between 0.2% – 0.8%. Moisture absorption may increase operating cycles, energy demand, and costs. Also, moisture presence may result in cloudy molded parts. Therefore, your manufacturer must thoroughly dry ABS resins before the manufacturing stage. That is, at a temperature level between 80 to 90°C for at least 2 hours. It reduces the absorption rate to less than 0.1%.
Radius size
The bigger the radius, the lesser the strain on the plastic material. Even so, a too-big radius may cause mold shrinkage. Therefore, the ratio of the ABS radius to wall thickness should be at least 0.3.
ABS injection molding temperature control
Exposure of ABS plastic to extreme temperatures can cause thermal decomposition. This leads to chemical and physical changes in the injected molded part as it breaks the chemical bonds. Therefore, it’s vital to ensure optimum temperature control between 200 – 238°C / 392°F – 460.4°F.
Injection molding speed
A high injection molding speed can also cause thermal decomposition, reduce glossiness, or discolor the plastic material. In contrast, a low injection molding speed might result in insufficient mold filling. For that reason, your manufacturer should balance the momentum to ensure efficient processing and top-notch molded parts.
Injection pressure
ABS plastic requires a high injection pressure because of its viscosity. However, excessive injection pressure causes the molded parts to stick together strongly and can be more costly to separate. Therefore, your producer must maintain optimal pressure to create end products with superior qualities.
Processing conditions of ABS plastic
Below are some processing conditions to comprehend:
Injection molding pressure: The injection molding pressure should be between 50 – 100 MPa.
Back pressure: While high back pressure enables uniform mixing, it may also cause wear and tear. Therefore, it’s recommended to maintain a back pressure of 5 bar.
Gate and vent design: The gate and vent design must be designed effectively. The parameters to carefully look into include the gate length (less than 1mm), vent width (4-6mm), thickness (0.025-0.05mm), and channel diameter (3mm).
Melting point: The recommended melting point temperature ranges between 200 to 280°C.
Benefits and drawbacks of ABS injection molding
Here are some advantages and disadvantages of ABS plastic:
Advantages
Recyclability: ABS plastic can be recycled and melted several times without losing its physical properties.
Strong and durable: As stated earlier, ABS plastic does not degrade. It remains tough even at low-temperature levels. Also, unlike other thermoset plastic materials, ABS plastic does not burn or degrade during heating, cooling, or reheating. Therefore, they can be subjected to more than one-time heating. They’ll melt into liquid and hence can be readily injection molded.
Energy conserving: The machinery used for ABS injection molding are energy-saving. This lowers energy consumption and also reduces the overall processing times. Generally, ABS plastic molding improves efficiency in the manufacture of thermoplastics.
Reproducibility: ABS injection molding process enables the creation of complex products for complex uses. Regulated injection molding and other complementary techniques allow the reproducibility of results and the production of high-quality parts. Besides, ABS can withstand extreme temperatures and preserve its original physical features.
Flexibility: ABS plastic is a flexible resin with incredible integration capabilities. This versatility enables the processing of a wide range of components for various industries.
High dimensional stability and low shrink rate: Therefore, it’s suitable for manufacturing lightweight and rigid components.
High productivity: ABS plastic molding is a highly effective manufacturing technology that enables high-volume production with little human intervention.
Disadvantages
UV sensitive: Continuous exposure to Ultraviolet (UV) light may cause degradation.
Low fatigue resistance: It may degrade if subjected to consistent high-strain applications.
Applications of ABS injection molding
Generally, you should consider ABS plastic if your desired product requires rigidity and durability and should be lightweight. For instance, it’s highly popular for manufacturing musical instruments, home appliances, computer parts, and other components. Below are other relevant applications for different industries:
Construction industry: It’s mainly used in the construction industry to manufacture pipes and fittings because it’s a high impact resistant plastic.
Automotive industry: Used as an alternative to metal, especially for parts that should be lightweight. That includes seat belt parts, instrument panels, pillar trim, handles, and dashboard components.
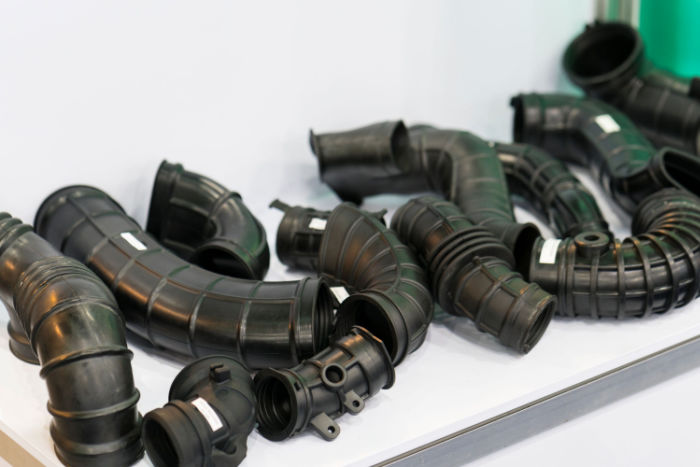
Electrical industry: Used in the electrical industry to make electronic components such as computer keyboards and housings for power tools.
Commercial applications: ABS injection molding is commonly used to create parts used at home. That includes control panels, vacuum cleaners, refrigerator liners, and food processors.
Also, while ABS is a suitable plastic for injection molding, the following common issues may present themselves in the ABS plastic injection molding process:
Sink marks: Occur when the thermoplastic material shrinks unevenly in the cooling stage. Also, they can form when manufacturers apply excessive heat or insufficient injection pressure. Fortunately, producers can prevent this by using high gate pressure and ensuring uniformity when designing the outer walls.
Warping: It happens in case of uneven cooling, causing distortion. Aside from that, warping might occur when the material is ejected early before sufficient cooling. Luckily, this can be prevented with the use of evenly-spaced cooling channels.
Viscosity: The viscosity of ABS plastic increases with an increase in temperature. Therefore, the melt temperature should be kept within an optimal range to ensure perfect injected molded ABS parts.
Additionally, ABS plastic may not be ideal for outdoor applications because it’s not resistant to harsh weather and sunlight. Even so, with filler materials and additives, you can increase its strength and resistance to Ultraviolet (UV) rays. Examples of filler materials are stainless steel fibers, nylon, and acrylic.