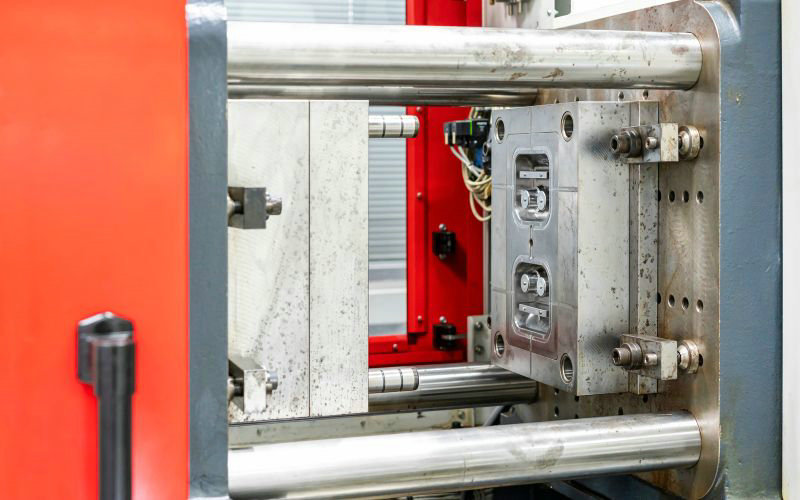
Injection Mold Classification
If you’re assessing injection molds, it’s essential to grasp the classification system that differentiates their capabilities and applications. In this article, we’ll provide you with a straightforward guide to understanding various mold types:
- By Geometry
- By Number of Cavities
- By Mold Plate
- By Ejection Principle
- By Plastic Material
- By Feeding System
Your choice among these types of injection molds often balances the scale of your project, the complexity of the parts, and the operational cost implications. Let’s explore various kinds of plastic injection molds together!
By Geometry
- Simple Geometries:
- Easier to design and manufacture.
- Often have fewer hollow sections.
- Complex Geometries:
- Allow for greater design flexibility.
- Can accommodate hollow sections needed for specific functions.
Complex parts often include features like undercuts, which are indentations or projections that can complicate the mold design. Designing for undercuts requires careful consideration to ensure mold components can separate properly during the ejection phase without damaging the part.
For intricate component designs, using advanced mold technologies, like sliders or lifters, might be necessary to create and release the part from the mold successfully. While this approach offers high design flexibility, it also adds to the complexity and cost of the mold.
Your selection between a simple or complex mold geometry will ultimately depend on the desired part design, functionality, the feasibility of the mold manufacturing process, and the project’s budget. Always balance the need for complex geometries with practical production considerations.
By Number of Cavities
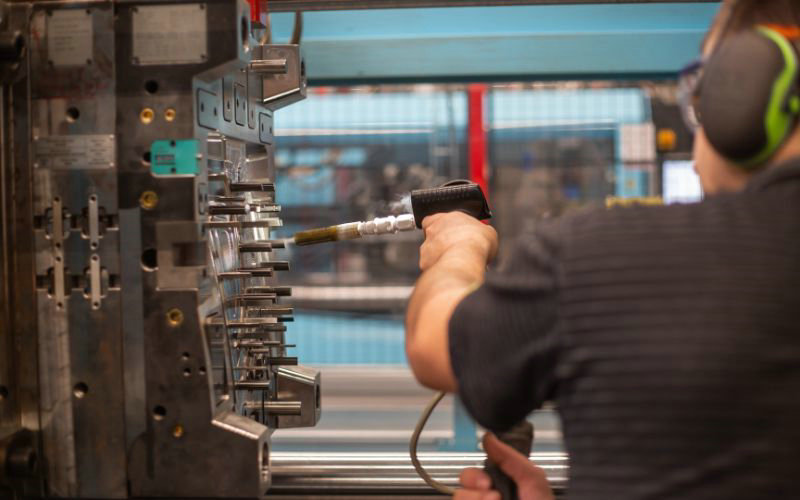
Single-Cavity Molds
- Produce only one product per injection cycle
- Ideal for large, complex, or low-volume parts
- Allow more attention to individual parts to minimize defects
- Lower tooling costs compared to multi-cavity molds for the same part
- Suitable for prototyping and providing out new designs
Multi-Cavity Molds
- Contain multiple identical cavities to produce several parts per cycle
- Enable shorter lead times and increased production efficiency for high volumes
- Reduce per-part costs for large batches
- Require careful design to ensure even filling and consistent quality across cavities
- May have higher initial tooling costs than single-cavity molds
- Typical cavity numbers range from 2 to 64 or more, depending on part size and application
Family Molds
- Incorporate multiple cavities with different shapes to produce various parts in one cycle
- Allow molding of related components or product variants in a single shot
- Useful for prototyping or producing kits with assorted parts
- Limited to parts using the same material and color
- Often have unbalanced filling due to different cavity geometries, increasing defect risk
- Require more post-molding labor to separate and handle different parts
By Mold Plate
Two-Plate Injection Mold
- Simplest and most common injection mold design, consisting of two main parts (A side and B side)
- Has a single parting line where the mold splits into two halves
- Cavity side is fixed, while the core side is movable during the molding process
- Runner and part are located on the same parting plane and ejected together
- Advantages: lower cost, shorter cycle times, easier to set up and operate
- Disadvantages: less flexibility in gate location, requires manual delegating, risk of short shots in multi-cavity molds
Three-Plate Injection Mold
- Also known as stripper plate mold, consists of two parting planes and splits into three sections
- Has an additional floating plate between the cavity and core to accommodate the runner system
- Allows automatic degassing of the runner from the part
- Offers more flexibility in gate location compared to two plate molds
- Advantages: suitable for large parts requiring multiple gates, enables automatic debating
- Disadvantages: more complex and expensive, longer cycle times, less stable due to more moving parts
Stack Injection Mold
- Special mold structure with multiple parting surfaces, each accommodating one or more cavities
- Consists of a moving mold, middle mold, and fixed mold that open simultaneously
- Can double the output of a standard mold without requiring additional machines
- Suitable for high-volume production of flat, thin-walled parts
- Advantages: significantly increased productivity, reduced costs, shorter manufacturing times
- Disadvantages: more complex design, requires careful balancing of cavity filling and cooling
By Ejection Principle
1. Pin Ejection
- Uses ejector pins to push the molded part out of the mold cavity
- Pins are located in the ejector half of the mold and are designed to withstand ejection forces
- Pin diameter, length, material, placement, and shape are critical design considerations
- Suitable for most injection molded parts, but may leave visible ejector pin marks
2. Sleeve Ejection
- Employs a sleeve-shaped ejector that surrounds the core to eject the part
- Provides uniform and stable ejection force without leaving visible marks
- Suitable for cylindrical, thin-walled, or shell-shaped products
- More complex and costly than pin ejection
3. Stripper Plate Ejection
- Uses a stripper plate to push the part off the core
- Ejection force is high, uniform, and stable, minimizing part deformation
- Ideal for cylindrical parts, thin-walled containers, and shell-shaped products
- Avoids visible ejector marks but has a more complex mold structure and a higher cost
4. Blade Ejection
- Utilizes rectangular ejector blades instead of pins
- Suitable for parts with specific geometries or requirements
5. Air Ejection
- Introduces compressed air between the part and mold to eject the part
- Simplifies mold structure and allows ejection at any location
- Often used to support other ejection methods for large, deep-cavity, or thin-walled parts
6. Lifter Ejection
- Employs lifters that move laterally to release undercuts or internal features
- Enables ejection of parts with complex geometries or side actions
By Plastic Material
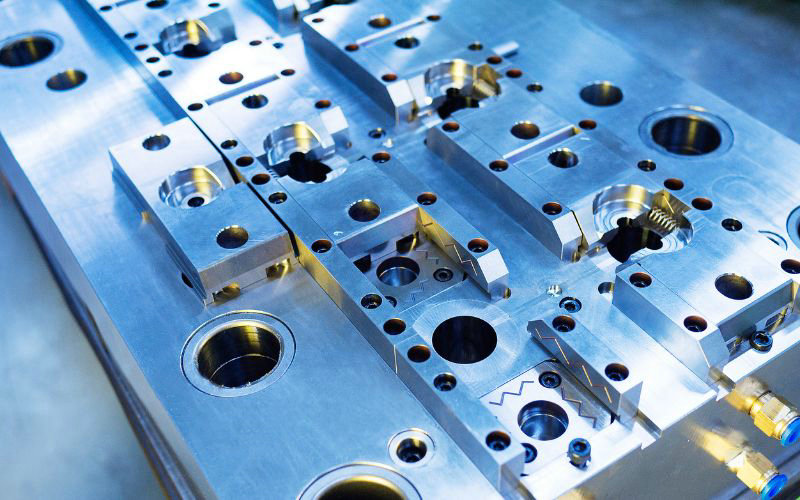
1. Acrylic (PMMA)
- Strong, clear thermoplastic with excellent optical clarity and UV resistance
- Lightweight and shatter-resistant alternative to glass
- Used for lenses, displays, signs, and medical devices
2. Acrylonitrile Butadiene Styrene (ABS)
- Tough, rigid, and impact-resistant thermoplastic
- Good chemical resistance and is easy to paint or glue\
- Used for automotive parts, appliances, toys, and electronics housings
3. Nylon (Polyamide, PA)
- Strong, flexible, and wear-resistant thermoplastic
- High melting point and good chemical resistance
- Used for automotive parts, gears, bearings, and electrical components
4. Polycarbonate (PC)
- Tough, transparent, and heat-resistant thermoplastic
- Good dimensional stability and electrical insulation properties
- Used for automotive components, medical devices, and safety glasses
5. Polyethylene (PE)
- Lightweight, flexible, and chemical-resistant thermoplastic
- High-density (HDPE) and low-density (LDPE) variants available
- Used for packaging, containers, toys, and automotive components
6. Polyoxymethylene (POM)
- Strong, rigid, and dimensionally stable thermoplastic
- Excellent wear and chemical resistance
- Used for gears, bearings, and precision parts
7. Polypropylene (PP)
- Lightweight, tough, and chemical-resistant thermoplastic
- Good fatigue resistance and electrical insulation properties
- Used for packaging, automotive parts, and household goods
8. Polystyrene (PS)
- Rigid, transparent, and easy-to-process thermoplastic\
- Low cost and good dimensional stability
- Used for packaging, disposable cutlery, and toys
9. Thermoplastic Elastomers (TPE) and Polyurethanes (TPU)
- Flexible, rubber-like thermoplastics with good impact and abrasion resistance
- TPUs offer better chemical and temperature resistance than TPEs
- Used for soft-touch grips, gaskets, seals, and footwear
By Feeding System
Cold Runner Injection Mold
- Consists of the sprue, runners, sub-runners, gates, and cold slug wells\
- Sprue delivers the melt from the nozzle to the runner system
- Runners transport the melt from the sprue to the gates
- Gates are small orifices connecting the runner to the cavity
- Cold slug wells store the initial cold material produced during injection intervals
- Can be further divided into side gate and point gate systems
- Suitable for most injection molding applications
Hot Runner Injection Mold
- Has no main runner and sub-runner
- Melt passes through a manifold plate and hot nozzle directly into the cavity via gates
- Utilizes insulated runner or hot runner molds
- Eliminates the need for a traditional cold runner system
- Reduces material waste and cycle times compared to cold runner systems
Runnerless Injection Mold
- Melt flows directly from the nozzle into the cavity without a runner system
- Simplest feeding system design
Recommended Injection Mold at Moldie
Moldie is a leading provider of high-quality, precision plastic injection molds and molding services. With years of experience and state-of-the-art technology, Moldie offers a wide range of injection mold solutions to meet your specific needs:
Precision Plastic Mould Products Injection Mold
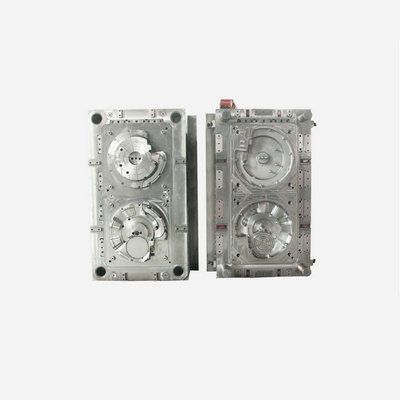
Discover precision plastic moulding products featuring robust material choices, cold/hot runner expertise, and the brilliance of RAL PANTONE colors.
Custom Made High Precision Plastic Parts
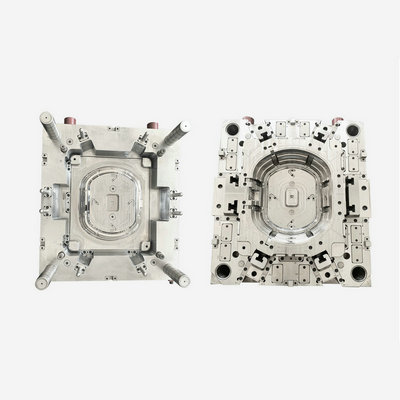
The complexity of the primary and secondary and finishing operations involved is why you should only hire the services of experts like those in our company to handle your production process.
Custom Plastic Molding Manufacturer
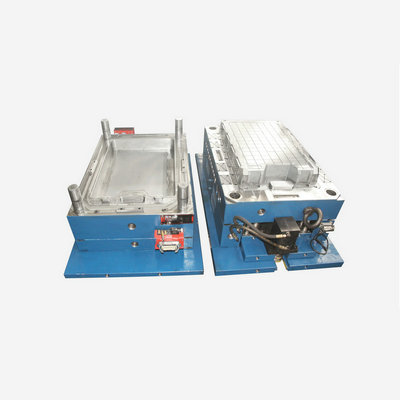
With mold weights ranging from 50kg to 15 tons and compatibility with injection machines up to 1500 tons, adaptability is at the heart of what we do.
Choose Moldie for your injection molding needs and experience the difference that precision, expertise, and customer-centric service can make. Contact us today to discuss your project and learn how we can help bring your vision to life.