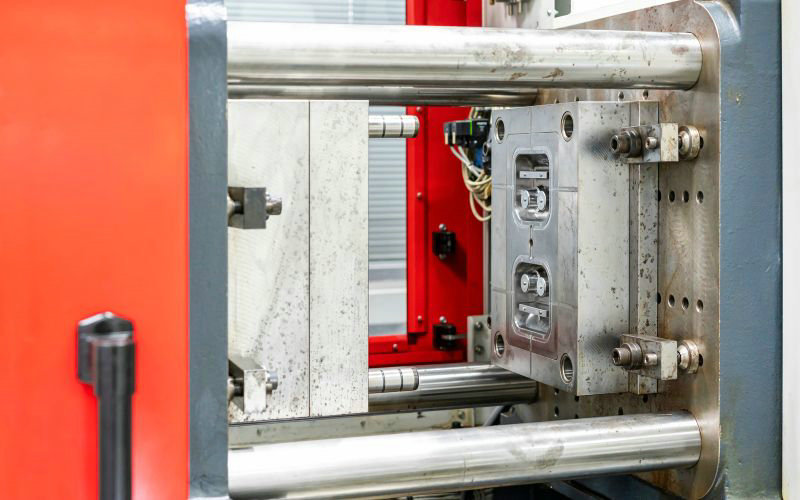
Klasyfikacja form wtryskowych
Jeśli oceniasz formy wtryskowe, ważne jest, aby zrozumieć System klasyfikacji co różnicuje ich możliwości i zastosowania. W tym artykule przedstawimy prosty przewodnik dotyczący zrozumienia różnych typów form:
- Przez Geometria
- Przez Liczba ubytków
- Przez Płyta formy
- Przez Zasada wyrzutu
- Przez Materiał plastikowy
- Przez System zywieniowy
Wybór spośród tego typu form wtryskowych często równoważy skalę projektu, złożoność części i konsekwencje kosztów operacyjnych. Przyjrzyjmy się razem różnym rodzajom form wtryskowych z tworzyw sztucznych!
Według geometrii
- Proste geometrie:
- Łatwiejsze w projektowaniu i produkcji.
- Często mają mniej pustych sekcji.
- Złożone geometrie:
- Pozwól na większą elastyczność projektowania.
- Może pomieścić puste sekcje potrzebne do określonych funkcji.
Złożone części często zawierają elementy takie jak podcięcia, które są wcięciami lub występami, które mogą skomplikować projekt formy. Projektowanie podcięć wymaga starannego rozważenia, aby zapewnić prawidłowe oddzielenie elementów formy w fazie wyrzucania bez uszkodzenia części.
W przypadku skomplikowanych projektów komponentów, aby pomyślnie utworzyć i wypuścić część z formy, może być konieczne zastosowanie zaawansowanych technologii form, takich jak suwaki lub podnośniki. Chociaż takie podejście zapewnia dużą elastyczność projektowania, zwiększa również złożoność i koszt formy.
Twój wybór pomiędzy prostą a złożoną geometrią formy będzie ostatecznie zależał od pożądanego projektu części, funkcjonalności, wykonalności procesu produkcji formy i budżetu projektu. Zawsze równoważ potrzebę stosowania skomplikowanych geometrii z praktycznymi względami produkcyjnymi.
Według liczby ubytków
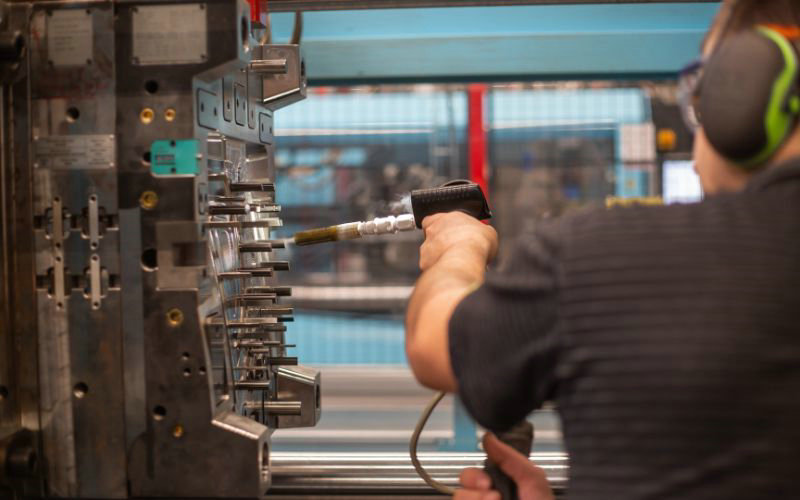
Formy jednogniazdowe
- Wyprodukuj tylko jeden produkt na cykl wtrysku
- Idealny do dużych, złożonych lub małych części
- Poświęć więcej uwagi poszczególnym częściom, aby zminimalizować defekty
- Niższe koszty oprzyrządowania w porównaniu z formami wielogniazdowymi dla tej samej części
- Nadaje się do prototypowania i dostarczania nowych projektów
Formy wielogniazdowe
- Zawiera wiele identycznych wnęk, aby wyprodukować kilka części na cykl
- Umożliwiaj krótsze czasy realizacji i zwiększoną wydajność produkcji w przypadku dużych ilości
- Zmniejsz koszty jednostkowe w przypadku dużych partii
- Wymagają starannego projektowania, aby zapewnić równomierne wypełnienie i stałą jakość we wszystkich ubytkach
- Mogą mieć wyższe początkowe koszty oprzyrządowania niż formy jednogniazdowe
- Typowa liczba gniazd mieści się w zakresie od 2 do 64 lub więcej, w zależności od rozmiaru części i zastosowania
Formy rodzinne
- Łącz wiele wnęk o różnych kształtach, aby wytwarzać różne części w jednym cyklu
- Umożliwia formowanie powiązanych komponentów lub wariantów produktu za jednym razem
- Przydatne do prototypowania lub produkcji zestawów z różnymi częściami
- Ograniczone do części wykonanych z tego samego materiału i koloru
- Często mają niezrównoważone wypełnienie ze względu na różną geometrię wnęki, co zwiększa ryzyko defektu
- Wymagają więcej pracy po formowaniu w celu oddzielenia i obsługi różnych części
Przez płytę formy
Forma wtryskowa dwupłytowa
- Najprostsza i najczęstsza konstrukcja formy wtryskowej, składająca się z dwóch głównych części (strony A i strony B)
- Ma pojedynczą linię podziału, w której forma dzieli się na dwie połowy
- Strona wnęki jest nieruchoma, natomiast strona rdzenia jest ruchoma podczas procesu formowania
- Wrzeciono i część znajdują się na tej samej płaszczyźnie podziału i są razem wyrzucane
- Zalety: niższy koszt, krótsze czasy cykli, łatwiejsza konfiguracja i obsługa
- Wady: mniejsza elastyczność w lokalizacji przewężek, konieczność ręcznego delegowania, ryzyko krótkich wtrysków w formach wielogniazdowych
Forma wtryskowa trójpłytkowa
- Znana również jako forma płyty zgarniającej, składa się z dwóch płaszczyzn podziału i dzieli się na trzy sekcje
- Posiada dodatkową pływającą płytkę pomiędzy wnęką a rdzeniem, aby pomieścić system prowadnic
- Umożliwia automatyczne odgazowanie wlewu z części
- Zapewnia większą elastyczność w lokalizacji przewężki w porównaniu z dwiema formami płytowymi
- Zalety: nadaje się do dużych części wymagających wielu bramek, umożliwia automatyczne debatowanie
- Wady: bardziej złożone i droższe, dłuższe czasy cykli, mniej stabilne ze względu na więcej ruchomych części
Forma wtryskowa stosu
- Specjalna konstrukcja formy z wieloma powierzchniami podziału, z których każda mieści jedną lub więcej wnęk
- Składa się z formy ruchomej, formy środkowej i formy stałej, które otwierają się jednocześnie
- Może podwoić wydajność standardowej formy bez konieczności stosowania dodatkowych maszyn
- Nadaje się do produkcji wielkoseryjnej płaskich, cienkościennych części
- Zalety: znacznie zwiększona produktywność, obniżone koszty, krótszy czas produkcji
- Wady: bardziej złożona konstrukcja, wymaga starannego zrównoważenia napełniania wnęki i chłodzenia
Na zasadzie wyrzutu
1. Wyrzut szpilki
- Wykorzystuje kołki wypychające do wypychania uformowanej części z gniazda formy
- Kołki znajdują się w części wypychającej formy i są zaprojektowane tak, aby wytrzymywały siły wypychające
- Średnica, długość, materiał, rozmieszczenie i kształt sworznia to krytyczne czynniki projektowe
- Nadaje się do większości części formowanych wtryskowo, ale może pozostawiać widoczne ślady sworznia wypychacza
2. Wyrzut rękawa
- Wykorzystuje wypychacz w kształcie tulei, który otacza rdzeń w celu wyrzucenia części
- Zapewnia jednolitą i stabilną siłę wyrzutu bez pozostawiania widocznych śladów
- Nadaje się do produktów cylindrycznych, cienkościennych lub w kształcie muszli
- Bardziej złożone i kosztowne niż wyrzucanie szpilek
3. Wyrzucanie płyty zgarniającej
- Wykorzystuje płytkę zgarniającą do wypchnięcia części z rdzenia
- Siła wyrzutu jest wysoka, jednolita i stabilna, co minimalizuje deformację części
- Idealny do części cylindrycznych, pojemników cienkościennych i produktów w kształcie muszli
- Pozwala uniknąć widocznych śladów wypychacza, ale ma bardziej złożoną strukturę formy i wyższy koszt
4. Wyrzut ostrza
- Wykorzystuje prostokątne ostrza wyrzutnika zamiast kołków
- Nadaje się do części o określonej geometrii lub wymaganiach
5. Wyrzut powietrza
- Wprowadza sprężone powietrze pomiędzy część a formę w celu wyrzucenia części
- Upraszcza konstrukcję formy i umożliwia wyrzucanie w dowolnym miejscu
- Często używany do wspierania innych metod wyrzucania dużych części o głębokich wgłębieniach lub cienkościennych
6. Wyrzut podnośnika
- Wykorzystuje podnośniki, które poruszają się na boki, aby uwolnić podcięcia lub elementy wewnętrzne
- Umożliwia wyrzucanie części o złożonej geometrii lub działaniach bocznych
Przez tworzywo sztuczne
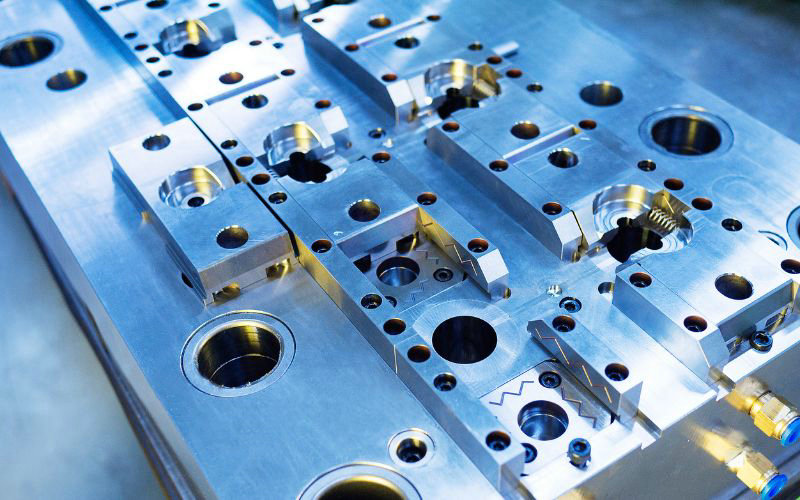
1. Akryl (PMMA)
- Mocny, przezroczysty termoplast o doskonałej przejrzystości optycznej i odporności na promieniowanie UV
- Lekka i odporna na stłuczenie alternatywa dla szkła
- Stosowany do soczewek, wyświetlaczy, znaków i wyrobów medycznych
2. Akrylonitryl-butadien-styren (ABS)
- Wytrzymały, sztywny i odporny na uderzenia termoplast
- Dobra odporność chemiczna i łatwa do malowania lub klejenia
- Stosowany do części samochodowych, urządzeń, zabawek i obudów elektroniki
3. Nylon (poliamid, PA)
- Mocny, elastyczny i odporny na zużycie materiał termoplastyczny
- Wysoka temperatura topnienia i dobra odporność chemiczna
- Stosowany do części samochodowych, przekładni, łożysk i elementów elektrycznych
4. Poliwęglan (PC)
- Wytrzymały, przezroczysty i żaroodporny termoplast
- Dobra stabilność wymiarowa i właściwości izolacji elektrycznej
- Stosowany do części samochodowych, wyrobów medycznych i okularów ochronnych
5. Polietylen (PE)
- Lekki, elastyczny i odporny chemicznie termoplast
- Dostępne warianty o dużej gęstości (HDPE) i niskiej gęstości (LDPE).
- Stosowany do opakowań, pojemników, zabawek i części samochodowych
6. Polioksymetylen (POM)
- Mocny, sztywny i stabilny wymiarowo termoplast
- Doskonała odporność na zużycie i chemikalia
- Stosowany do przekładni, łożysk i części precyzyjnych
7. Polipropylen (PP)
- Lekki, wytrzymały i odporny na chemikalia materiał termoplastyczny
- Dobra odporność na zmęczenie i właściwości izolacji elektrycznej
- Stosowany do opakowań, części samochodowych i artykułów gospodarstwa domowego
8. Polistyren (PS)
- Sztywne, przezroczyste i łatwe w obróbce tworzywo termoplastyczne\
- Niski koszt i dobra stabilność wymiarowa
- Stosowany do opakowań, sztućców jednorazowych i zabawek
9. Elastomery termoplastyczne (TPE) i poliuretany (TPU)
- Elastyczne, gumopodobne tworzywa termoplastyczne o dobrej odporności na uderzenia i ścieranie
- TPU zapewniają lepszą odporność chemiczną i temperaturową niż TPE
- Stosowany do miękkich w dotyku uchwytów, uszczelek, uszczelek i obuwia
Przez system karmienia
Forma wtryskowa zimnego kanału
- Składa się z wlewu, kanałów, kanałów dolnych, zastawek i studni ślimakowych.
- Wlew dostarcza stopiony materiał z dyszy do systemu kanałów
- Biegacze transportują stop z wlewu do bram
- Bramki to małe otwory łączące rynienkę z wnęką
- Zimne studnie na ślimaki przechowują początkowy zimny materiał wytwarzany w przerwach między wtryskami
- Można je dalej podzielić na systemy bramek bocznych i bramek punktowych
- Nadaje się do większości zastosowań związanych z formowaniem wtryskowym
Forma wtryskowa z gorącym kanałem
- Nie ma głównej i pomocniczej prowadnicy
- Stop przechodzi przez płytę rozgałęźną i gorącą dyszę bezpośrednio do wnęki przez zasuwy
- Wykorzystuje izolowane formy kanałowe lub formy gorącokanałowe
- Eliminuje potrzebę stosowania tradycyjnego systemu kanałów zimnych
- Redukuje straty materiału i skraca czas cykli w porównaniu z systemami zimnokanałowymi
Bezstopniowa forma wtryskowa
- Stop przepływa bezpośrednio z dyszy do wnęki bez systemu kanałów
- Najprostsza konstrukcja systemu karmienia
Polecane formy wtryskowe w Moldie
Moldie jest wiodącym dostawcą wysokiej jakości precyzyjnych form wtryskowych do tworzyw sztucznych i usług formowania. Dzięki wieloletniemu doświadczeniu i najnowocześniejszej technologii, Moldie oferuje szeroką gamę rozwiązań w zakresie form wtryskowych, aby spełnić Twoje specyficzne potrzeby:
Precyzyjne formy z tworzyw sztucznych Formy wtryskowe
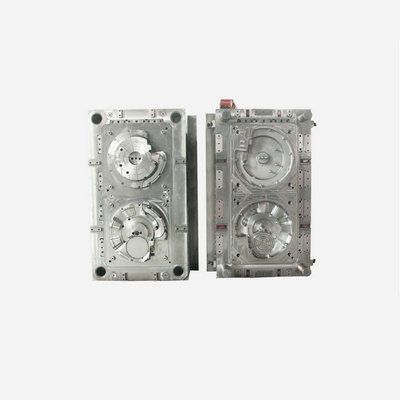
Odkryj precyzyjne produkty do formowania tworzyw sztucznych, charakteryzujące się solidnym wyborem materiałów, specjalistyczną wiedzą na temat kanałów zimnych i gorących oraz blaskiem kolorów RAL PANTONE.
Wykonane na zamówienie części z tworzyw sztucznych o wysokiej precyzji
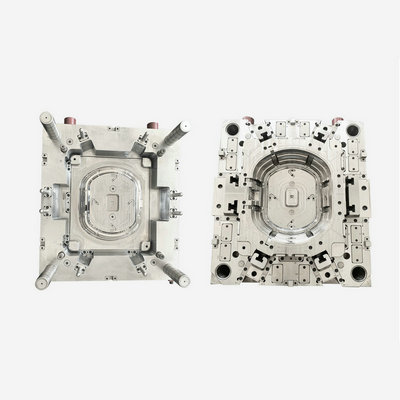
Złożoność operacji pierwotnych, wtórnych i wykończeniowych powoduje, że powinieneś korzystać z usług wyłącznie ekspertów takich jak ci z naszej firmy, którzy zajmą się Twoim procesem produkcyjnym.
Niestandardowy producent formowania tworzyw sztucznych
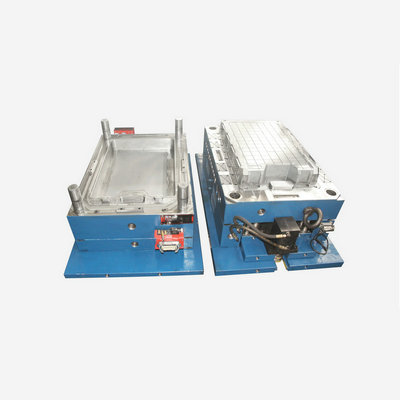
Dzięki masie form od 50 kg do 15 ton i kompatybilności z wtryskarkami do 1500 ton, zdolność adaptacji jest podstawą tego, co robimy.
Wybierać Moldie dla Twoich potrzeb w zakresie formowania wtryskowego i przekonaj się, jaką różnicę może zrobić precyzja, wiedza specjalistyczna i obsługa zorientowana na klienta. Skontaktuj się z nami już dziś, aby omówić swój projekt i dowiedzieć się, jak możemy pomóc w realizacji Twojej wizji.