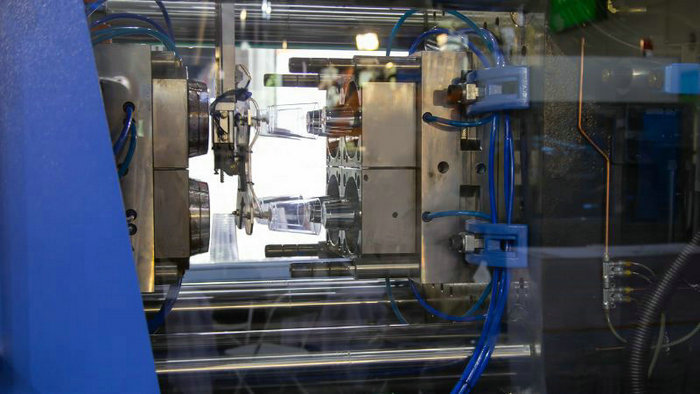
Introduction to Polycarbonate Molding
Polycarbonate molding is a technique you can employ to craft items with a precise combination of excellent toughness, clarity, and impact resistance. This material, polycarbonate, is an amorphous thermoplastic widely celebrated for its remarkable properties.
What Makes Polycarbonate Stands Out
Let’s break down what makes this material so special.
Polycarbonate is a form of thermoplastic polymer that’s noted for being exceptionally rigid and lightweight. Often referred to by its abbreviation “PC,” polycarbonate has several desirable properties that make it useful for various applications.
Chemically, this plastic consists of carbonate groups bonded between aromatic rings along the polymer chain. This chemical structure gives polycarbonate its strength and rigidity. It is amorphous and transparent, allowing light to pass through easily. Yet polycarbonate is highly impact-resistant and can withstand significant force without breaking or cracking.
The production of polycarbonate begins with the reaction of bisphenol A (BPA) and phosgene to form the polymer backbone. Depending on its end use, it can then be formed into solid sheets or molded into various shapes.
During molding, polycarbonate can be shaped into your desired shape while preserving its mechanical properties such as flexural and impact strength. The material is heat resistant, which adds to its durability and makes it suitable for products subjected to high temperatures.
Moreover, the optical clarity of this plastic is akin to transparency, creating parts that are both strong and clear. These characteristics make it an outstanding choice for a variety of applications, including automotive components, consumer electronics, and safety equipment.
Design and Engineering of Molds
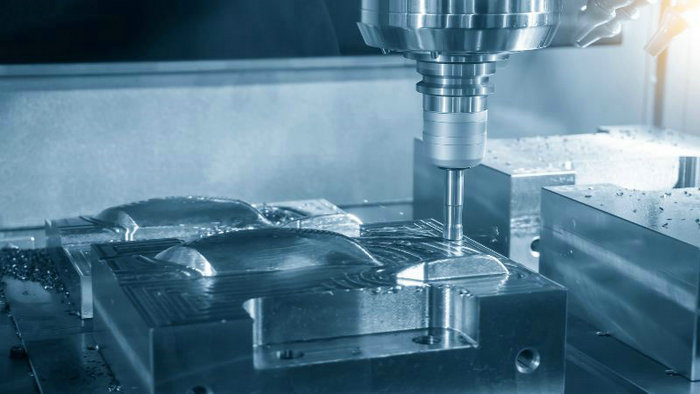
Before venturing into molding polycarbonate, you’ll find the design and engineering of molds to be a critical factor in achieving high-quality, consistent parts. This process encapsulates a range of technical considerations, from selecting the right materials to utilizing advanced software for precision design.
Mold Material Selection
Your choice of mold material directly influences the quality and lifecycle of your polycarbonate products. Tool steels are commonly used due to their durability and resistance to wear. When choosing, consider:
- Thermal conductivity: Affects cooling rate and cycle time.
- Hardness: Determines resistance to surface defects and abrasion.
Precision Engineering for Molds
Achieving tight tolerance is paramount in mold engineering. Precision machining ensures that the molds meet the exact specifications necessary for the desired shape and size of your parts. Understand that:
- Tolerances: Affect the fit and function of your assembled parts.
- Part sizes: Ranging from minute to large are all dependent on the precision of your molds.
Surface Treatments and Finishing
Surface treatment of molds is essential to enhance release properties and reduce surface defects. Finishing options you’ll come across include:
- Polishing: Results in a smooth, glossy surface.
- Texturing: Provides a matte or patterned surface, which may be functional or aesthetic.
Venting and Gate Placement
Proper venting and gate placement are crucial in preventing defects and ensuring optimal flow of the thermoplastic resins. Keep in mind:
- Venting: Allows air to escape from the mold cavity to prevent trapped air defects.
- Gate locations: Influences the resin’s flow and can impact the appearance and integrity of the part.
CAD and Mold Design Software
Utilizing CAD (Computer-Aided Design) and specialized mold design software facilitates the manufacturing process by allowing you to:
- Conduct flow analysis: Predict and enhance resin distribution throughout the mold.
- Visualize gate locations and part shapes: Helps to address potential manufacturing challenges before tooling.
In your journey of molding polycarbonate, these intricacies in the design and engineering of molds shape the journey from raw material to finished product, providing a clear blueprint for success.
Technique of the Polycarbonate Injection Molding Process
Polycarbonate parts produced through injection molding have impressive qualities such as impact and heat resistance. Nevertheless, processing polycarbonate can be complex as some variants exhibit low melt flow rates.
When molding polycarbonate, controlling the parameters of the process is crucial for the quality of your final product. Let’s dive into the specifics to ensure you achieve the best results.
Prepare the Polycarbonate
- Common grades of polycarbonate include general purpose, high heat, UV stabilized, and flame retardant. PC resin must be dried before molding to a moisture content below 0.02% to prevent defects.
- Drying is typically done at 120°C for 2-4 hours.
How to Set the Injection Molding Machine
- Clamping force should be 0.7-0.8 tons per square inch of projected part area.
- Machine size should be 1.5-2 times the part weight.
- Screw should have an L/D ratio of at least 15:1, ideally 20:1, with a check ring and gradual transition.
- Nozzle opening should be slightly smaller than the gate size.
Mold Preparation
- Mold must be cleaned and coated with a release agent to facilitate part ejection.
- Vents must be clear to allow air to escape when the mold is filled.
- Cooling channels should be optimized for even cooling and reduced cycle times.
Process Settings
- Melt temperature: 280-320°C depending on grade.
- Mold temperature: 70-120°C. Higher for better surface finish and lower stress.
- Injection pressure: As high as possible, typically 850-1400 bar. Helps fill mold quickly.
- Injection speed: Slower for small/edge gates, faster otherwise.
- Packing pressure: As low as possible to minimize residual stress.
Post-Molding Procedures
- Plastic parts are ejected when sufficiently cool to handle demolding stresses.
- Gate marks are removed through trimming.
- Annealing at 120-130°C for 30 mins – 1 hour can relieve residual stresses.
- Dimensional checks and visual inspections are performed to ensure part quality.
Ejection Mechanism Details
The ejection process must be carefully controlled to avoid damaging the solidified polycarbonate molded parts.
- Ejector Pins: Ensure pins are positioned to uniformly distribute ejection forces.
- Ejection Speed: Adjust the speed to prevent part sticking or deformation.
By paying attention to these technical specifics, you’ll be better equipped to handle the complex process of polycarbonate injection molding.
Advanced Techniques in Polycarbonate Plastic Injection Molding
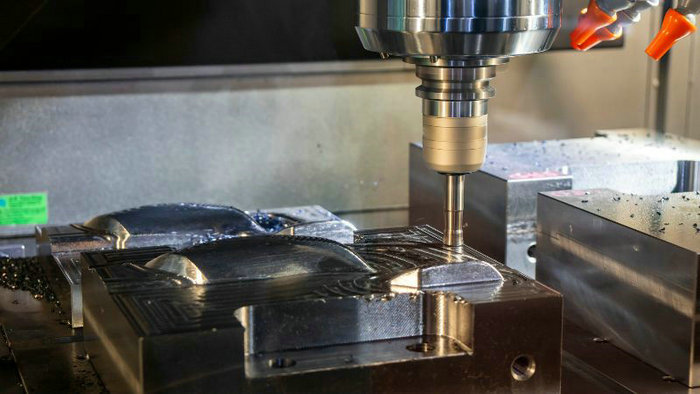
In your journey to master polycarbonate molding, you’ll discover that advanced techniques can be pivotal in enhancing strength, aesthetics, and functionality. Let’s explore how these innovative methods can elevate your products.
Injection-Compression Molding
In injection-compression molding, polycarbonate is first injected into a slightly open mold and then further compressed, improving product uniformity. This method combines the principles of injection molding and compression molding, ensuring reduced stress while achieving thinner and more precise components.
Gas-Assist and Water-Assist Injection Molding
Gas-assist injection molding introduces nitrogen gas into the mold cavity post-injection, creating internal channels and reducing material usage without compromising structural integrity. On the flip side, water-assist injection molding achieves similar results with water, enhancing the cooling process and cycle time.
- Advantages:
- Weight reduction
- Increased strength
- Faster cycle times
Multi-Material and Co-Injection Molding
Moving onto multi-material (two-component) molding, you can mold polycarbonate with different materials in a single cycle for composite structures. Co-injection molding, a subset of this technique, involves injecting two distinct polymers into one mold, one after another, to create a part with layered properties.
- Composite Part Composition:
- Core material: Usually the cheaper or less robust material.
- Skin material: Typically the more durable material that surfaces the part.
Each method plays a critical role in tailoring your polycarbonate components to meet specific requirements – from structural aspects to aesthetic features. Using these advanced techniques, your polycarbonate products will not only meet but exceed the expectations of even the most challenging applications.
Sustainability and Environmental Impact
As you explore the world of polycarbonate, it’s essential to understand not only its practical applications but also the impact its production and life cycle have on the environment. In this section, we’ll take a closer look at how recycling and the efficiency of its production processes contribute to sustainability.
Recycling and Reusing Polycarbonate
Polycarbonate’s robust nature allows for its use in various products, from eyewear lenses to bulletproof glass. However, when these items reach the end of their lifecycle, recycling and reusing polycarbonate becomes paramount to reduce environmental waste. Fortunately, polycarbonate can be mechanically recycled to decrease its ecological footprint. The process involves:
- Grinding: Polycarbonate products are ground into smaller pieces.
- Cleaning: Contaminants are removed to prepare for reintegration.
- Melting: The clean polycarbonate scraps are rapidly heated and remolded into new products or polycarbonate sheets.
By converting polycarbonate waste into granules through extrusion, it can be added to other plastic products, effectively extending its usefulness and preventing pollution.
Energy Efficiency in Production
To enhance sustainability, it’s crucial to focus on the energy efficiency of producing polycarbonate. The manufacturing process typically involves rapid heating and precise control to produce high-quality polycarbonate sheets or products. To save energy, advancements have been implemented that:
- Optimize processes: Fine-tuning production parameters to minimize energy waste.
- Incorporate green technology: Utilizing energy-saving equipment and renewable energy sources when possible.
This continuous improvement effort aims to cut down on the overall energy consumption and carbon footprint associated with the production of polycarbonate. By prioritizing these practices, you can partake in more eco-friendly initiatives within the industry.
Frequently Asked Questions
What temperatures are needed for polycarbonate injection molding?
For successful injection molding, temperature control is very important. Polycarbonate typically requires temperatures ranging from -40°C/-40°F to 120°C/248°F. These parameters ensure that polycarbonate maintains its strength and stability during the process.
What are common issues in polycarbonate injection molding and how can they be addressed?
Common issues include warping, bubbling, and poor filling. Address these by optimizing venting requirements, controlling process parameters, and maintaining uniform wall thickness.
What is the process for drape forming polycarbonate sheets?
Drape forming involves heating the polycarbonate sheet to a pliable temperature, then draping it over a mold to achieve the desired shape. Cooling it down preserves the form.
What are the steps involved in processing polycarbonate materials?
Processing polycarbonate consists of heating the material to the recommended temperature, injecting it into molds, cooling it to solidify, and then ejecting of the final injection molded parts.
What is the methodology for thermoforming polycarbonate?
Thermoforming polycarbonate includes heating the sheet to its softening point, stretching it over a mold, and then cooling it to form a rigid, shaped finished product.
What are the disadvantages of polycarbonate injection molding?
The higher viscosity of polycarbonate leads to slower molding cycles, higher molding pressures, and a need for more robust molds which can impact the cost of injection molding. Defect management is also more critical.