Plastic injection molding or injection molding is the production of plastic parts in large quantities using injection molding machines.
To understand how it works, you must have basic knowledge of the injection molds tools, what they are, how they work, where to find them, and which injection molding tools are best for specific tasks.
Luckily, this article provides you with all the details you need to know before operating an injection molding tool:
What is an Injection Mold?
An injection mold or A plate is a machined tool used in the plastic injection molding process. It molds the molten plastics into finished plastic goods.
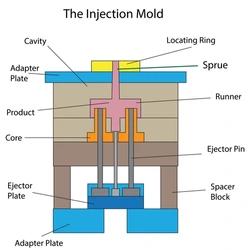
It’s the entry point that allows the melted plastic to pass through from the injection unit. The entrance of the injection mold is called the sprue bushing. They connect to runners, tunnels connecting the sprue to the cavity image.
The cavity image is an empty space in the injection mold that transforms the molten plastics to their desired shape and size.
Generally, this injection molding tool can have single or multiple cavities, depending on your production volume. Single-cavity molds are called single-impression cavity molds, while those with multiple cavities are called multiple-impression cavity molds.
What is an Ejector Mold?
The ejector mold or the B plate is the part of the injection molding tool that acts as the exit point through which plastic parts eject from the injection mold.
When the molten plastic molds, the clamping unit slides the B plate from the injection mold creating an exit point and pushing the plastic products out of the injection molds using ejector pins.
What is overmolding?
Overmolding is the process through which the injection mold forms multiple layers around a single product. It does this by re-introducing the injection molded parts into the mold.
However, you need specialized injection molding tools with multiple injection units for this process to be successful.
The overmolding process is simple. You start by molding the plastic products with a base-color material, ensuring you leave enough room to fit more plastic products with different colors.
Injection mold tooling gate types
The small opening created when a mold opens is called a gate. Plastic enters the mold cavities through these openings. There are two main gate types found in injection molds. They include:
- Automatically-trimmed gates: These gates open automatically without the interference of an operator. This way, there’s less damage and scars. These gates include the hot runner gate, valve gate, and ejector pin gate.
- Manually-trimmed gates: These gate types require an operator to separate the components from the runners once a cycle is complete. They include the sprue, spider, overlap gate, and others.
Types of Injection Molds
The injection molds differ in shape and size depending on the plastic product you want to produce.
There are many types of injection mold you could use for your plastic injection molding process, but two-plate molding is the most used.
The various plastic injection molding molds are classified based on the following:
The number of mold cavities
One of the primary ways to differentiate injection molding is by the number of mold cavities. There are three different types of injection molds under this category. They include the following:
- Family molds: Family molds have multiple distinct cavities. Manufacturing companies use it to produce plastic components of varying shapes and sizes.
- Single-cavity molds: It’s used to create a single molded part per cycle as it only has a single cavity. They’re typically not ideal for large-volume plastic productions but are cheaper than others.
- Multi-cavity molds: This injection molding tool has multiple identical cavities to produce large volumes of similar containers.
The feeding system
Another way to differentiate the plastic injection molding tools is through their feeding system, a collection of channels, including the runners, gates, and sprues, which direct the molten plastic into the mold cavity.
Here are the different types of molds under this category:
- Insulated runner injection mold: This injection molding uses unheated runners to direct the molten plastic into the cavity image and cartridge heaters to create layers surrounding the molten plastic to form insulated culls.
- Hot runner injection mold: These are injection molds used in injection molding that use externally or internally-heated rods. The molds are enclosed in a manifold plate permanently to prevent them from ejecting with the plastic parts.
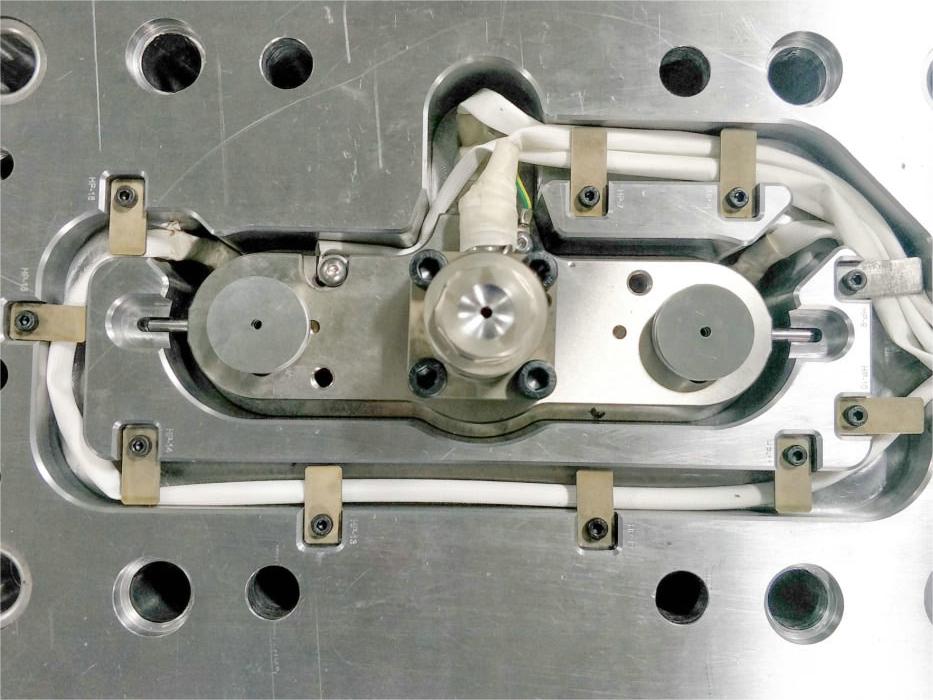
- Cold runner injection mold: Like the insulated runner injection mold, cold runners use unheated runners to guide the melted plastic into the cavities, making them the best option when producing heat-sensitive plastic components.
The mold plate
As mentioned, mold plates are one of the molding tools used to produce plastic containers. You can use the number of mold plates to differentiate various plastic injection tools. They include the following:
- Two-plate injection molding: This injection mold has affordable tooling costs and can be used with just about any runner system, making it the most used injection mold by hundreds of thousands of plastic manufacturing companies. However, they’re more familiar with single-cavity molds.
- Three-plate injection molding: It has an additional stripper plate with two parting lines, unlike the two-plate mold with a single parting line. These lines separate the running system from the injection molded parts.
- Stack injection mold: It’s the most expensive injection mold to purchase in this category, but it’s more efficient and reduces the overall operational costs. It also uses a few clamp tonnages with each cycle.
Plastic Injection Tooling Material Selection
Tooling material selection is one of the most overlooked yet critical injection molding tooling designs. Your choice of material will significantly influence the lifespan of your injection mold tooling.
You can build your molding tools using aluminum or steel. However, aluminum isn’t the best option when producing high-tolerance plastic parts. You should, therefore, use it when making low-tolerant components only.
You should also note that:
- Proper steel hardness and grade are crucial in balancing the injection mold tooling’s toughness and durability.
- You’ll need harder steel to mold glass-filled materials capable of wearing down toolings, such as runners and gates.
- You can also use steel hardness to introduce steel brittleness. And it’s therefore not the best to use for tooling components vulnerable to side loading.
The Relationship Between Tight Tooling Complexity and Tight Tolerance
Tools mold design, cavitation, and materials impact the plastic injection tooling tolerance. A simpler process is likely to get and maintain a tighter tolerance than complex parts because they can put tight tolerance at risk as there are other variables, such as the number of cavities, to consider.
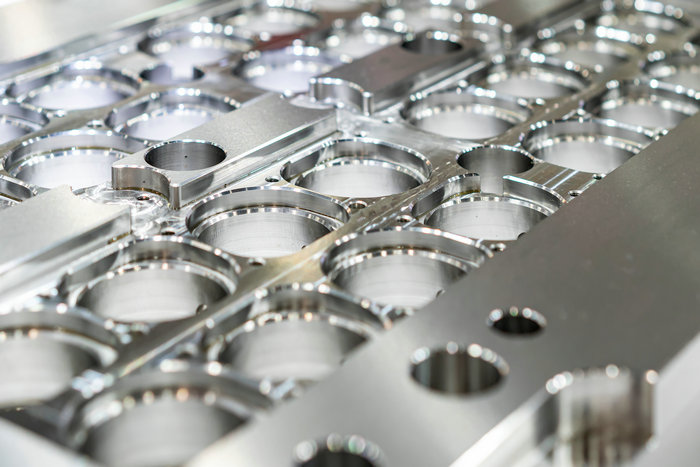
Generally, you’ll need sophisticated plastic injection molding tools to produce complex parts with added features like threads and undercuts. You may also require additional rotating mechanical gears in case of complex geometries.
The Process for Injection Molding Tooling
The process for injection molding tooling isn’t that complicated. However, the process may vary depending on the products, materials, and specifications you want to meet.
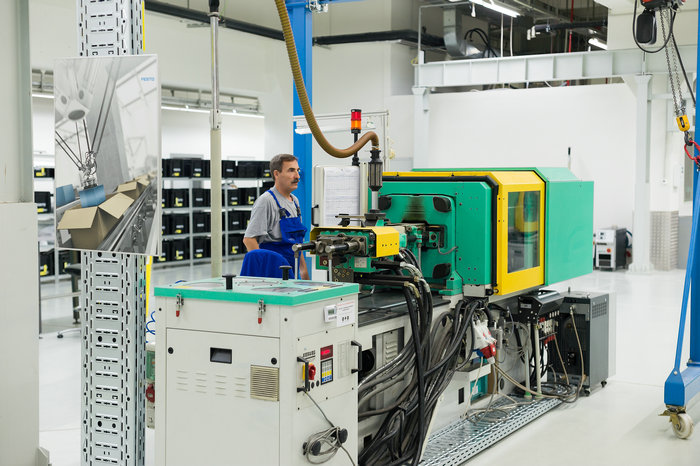
That said, here are the basic stages of the injection molding process:
Design and Engineering
The first stage in the injection molding process is the design creation and engineering. It involves creating a 3D CAD model of the injection mold and testing its performance, to see if it produces plastic parts with the desired shapes, sizes, and tolerance, using a simulation software.
Prototype
The next step is to create a prototype mold to test the design. This helps you decide whether or not your model will give you the desired outcome. You can also use this stage to improve your mold design before it reaches the final stages.
Toolmaking
Here’s where you produce the actual mold. You can use various materials, like aluminum and steel, and techniques, such as electrical discharge machining (EDM), CNC machining, or 3D printing to produce the molds.
Mold qualification
The next process in the injection molding tooling involves producing several test parts and measuring the properties and dimensions of the molded plastics to see if they meet the required specifications and standards.
Mass production
Now that you know your mold qualifies, you can use it for mass production. This involves filling the various mold cavities with the molten plastics and giving it enough time to cool and solidify, taking the mold shape.
Maintenance
The process doesn’t end with a single production. You must maintain the injection molding to ensure it continues producing the high quality products. This means repairing worn parts, making needed adjustments, and cleaning it from time to time.
Things to Consider When Looking for a Plastic Mold Manufacturing Company
Finding the best manufacturing company for your custom injection molding process may be a little challenging. You must know the questions to ask and the response you need.
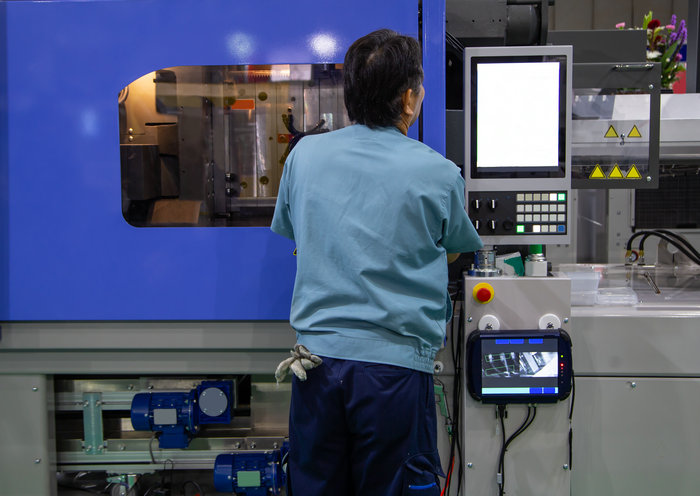
To get the best manufacturer for your molding process, consider the following:
- Years of experience: Experience matters. Manufactures with more experience are likely to produce fewer defects, reducing the total operational costs.
- Domestic manufacturing: You would want to hire a local manufacturer to take advantage of the in-house tooling.
- Clear communications: You would want to hire a reliable manufacturer who will let you in on how the process is proceeding. Request them to take you through the process beforehand, not forgetting to inquire about the materials needed. See how they present their objectives and decide whether they’re the kind you can communicate with
Conclusion
Now that you know how plastic injection molding tools work, you can start your project. It’s a pretty straightforward process to create plastic containers in large quantities within a reasonable time frame. It’s also affordable and will help you produce quality pieces within the shortest time possible.