The injection molding technique is used in manufacturing injection molds for identical parts, known as molded components. This process requires high pressure, and the molten plastic or other material is injected into a mold cavity for plastic injection molding.
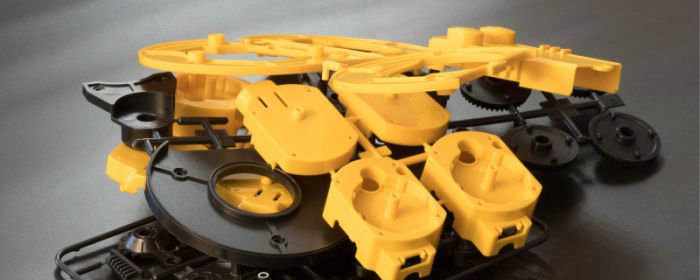
The second step takes place inside the mold, where the substance cools and solidifies, conforming to the contours of the hollow. The molded portion is then removed after opening the mold. The procedure is repeated several times to create many identical pieces.
Additionally, immensely strong steel is commonly used for injection molds, built to withstand the high pressure and heat generated during the injection molding process. To make accurate and consistent parts, the molds must be precise.
The quality of the finished product is significantly influenced by the design of the mold, which can be complicated due to considerations such as the type of material being molded, the intended shape of the finished item, and the production procedures involved.
Molded parts are used in various products, from straightforward home goods to intricate mechanical parts used in sectors including the automobile, electronics, and medical device industries. Injection molding is a well-liked production method for various products due to its adaptability and affordability.
Injection Molding Products: Equipment And Process
Utilizing specialized machinery, the industrial process of injection molding creates molded components from thermoplastic or thermosetting materials. The following components are essential in the manufacture of injection molding products:
Equipment
The following equipment is used during the injection molding process:
- Injection molding machine: This machine contains components such as a hopper, a heating barrel, a reciprocating screw, and a mold clamp that make up the primary part of the injection molding procedure. The plastic pellets are melted by the machine and injected under solid pressure into the mold to make a molded part..
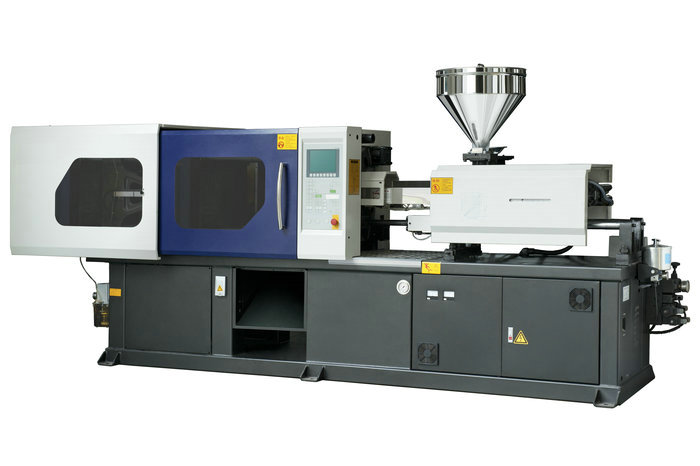
- Mold cavity: This instrument, often composed of steel or aluminum, gives the plastic its shape. Two pieces of the mold are fastened together during the injection molding procedure.
- Material hopper: Before being fed into the heating barrel of the injection molding machine, the plastic pellets are kept here.
- Heating barrel: The plastic pellets are melted in this part of the injection molding process so they are ready to be injected into the mold.
- Reciprocating screw: This part of the injection molding machine heats the plastic before directing it toward the mold.
- Mold clamp: This system applies the pressure required to inject the molten plastic into the mold while keeping the mold closed during the injection molding process.
- Cooling system: This is used to cool the injection-molded components once they have been created. This can be accomplished by chilling the system with air, water, or a combination of the two.
These are the essential elements of a setup for injection molding. Depending on the particular needs of the injection molding process, additional auxiliary equipment may also be employed, such as granulators, material dryers, and temperature control units.
Plastic Injection Unit
Melting and injecting the plastic material into the mold cavity is done by the plastic injection unit in injection molding. The plastic material is melted and injected into the mold using a heated barrel, a screw, and a nozzle.
The plastic substance is then put into the barrel, where the moving screw heats and mixes it. In the next step, the nozzle injects the plastic material into the mold cavity once it has reached the proper temperature and consistency, where it cools and hardens to create the desired result.
To maintain constant and high-quality output, the plastic injection unit, which is a crucial part of the injection molding process, must be appropriately managed.
Mold Clamping Unit
The two mold halves must be tightly closed and held together during the injection and cooling processes by the mold clamping device in injection molding. The clamping force required to keep the mold halves firmly together and stop any plastic material from seeping out of the mold cavity is applied and maintained by the unit.
A stationary platen and a moving platen coupled to a hydraulic or mechanical system make up the mold clamping unit. The two platens are pulled together when the mold is placed into the machine, and a clamping force is then applied to keep the mold closed.
The amount of clamping force needed varies depending on the size, intricacy, and kind of plastic used and the mold. To ensure safe and effective manufacturing, the mold clamping unit, a crucial part of the injection molding process, must be closely monitored.
Processes: Injection Molding Thermoplastic Polymers
The process for injection molding thermoplastic polymers typically involves the following:
The Mold
The injection molding of thermoplastic polymers depends heavily on the injection mold. It is a device used to mold molten plastic into the desired finished item. The cavity and the core, the two main components of the mold, are typically constructed to fit together to create a three-dimensional shape.
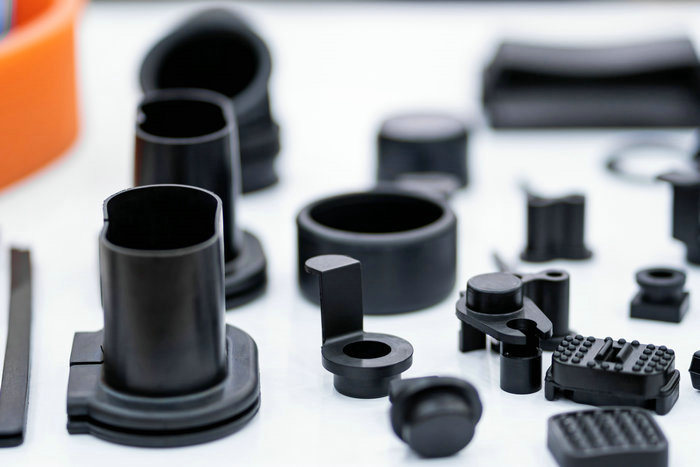
After being injected into the mold cavity, the plastic material cools and hardens to assume the mold’s shape. The ultimate shape and size of the product are determined by the mold’s design, making it a critical component of the injection molding process.
The mold must be carefully developed to guarantee that the plastic material flows effortlessly into every cavity and that the cooling process is quick and even. Additionally, the mold must be constructed from materials that endure the high temperatures and pressures used in the injection molding process.
Since the mold is reusable during injection, it can be used to create numerous identical parts. To keep it in good shape and able to continue producing high-quality parts, the mold may need to be cleaned and maintained regularly.
Two-Plate Mold
In injecting thermoplastic polymers, the two-plate mold is a typical style of mold. It comprises two parts fixed on the molding machine’s two plates, the cavity half and the core half. The two-plate mold is so called because it has a two-part design with a dividing line separating the two portions of the mold.
The two-plate mold’s job is to mold the molten plastic into the required final shape. The plastic material is injected into the cavity half of the mold through a gate at the separating line. The cavity is filled with plastic material, which is then allowed to cool and solidify. The finished item is released once the mold’s two halves are split open.
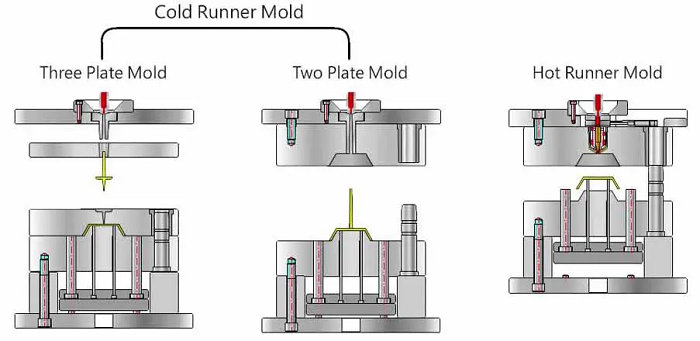
Since it only needs two plates and a few simple components, the two-plate mold is a reasonably easy and affordable type of mold. It works well for components with straightforward geometry, including flat or rounded curves.
However, it might not be appropriate for parts with more intricate geometries because filling the cavity with plastic might be challenging in these circumstances. In injection molding, the two-plate mold is versatile and often used, especially for straightforward pieces and modest production runs.
Three-Plate Mold
The three-plate mold is one of the molds used in the injection molding of thermoplastic polymers. Compared to the two-plate mold, it has more features and versatility because it has three plates; two moving and one stable.
The three-plate mold’s purpose is to mold the plastic injection molded parts into the required final shape. The plastic material is injected into the mold’s cavity half through a gate on the separating line.
Once the molten plastic is in the mold cavity, the two moving plates detach from the stationary plate, allowing the plastic object to be expelled from the mold. The third plate in the three-plate mold, sandwiched between the cavity and core half, is referred to as the runner plate or sub-plate.
With the use of this plate, a unique runner system can be created that can be utilized to direct the flow of plastic material to various cavities or locations inside of a single cavity. As a result, the injection molding process can be more flexible and effective.
When producing larger items, where using a two-plate mold would result in a higher mold size or necessitate the installation of extra features like lifters, the three-plate mold is frequently employed. By including several cavities in the mold design, the three-plate mold can make various parts in a single cycle.
The three-plate mold is a versatile and effective mold type frequently used in the injection molding process, especially for bigger parts and production runs.
Reusing The Sprue And Runner In Two And Three-Plate Molds
The material being used, the part geometry, and the desired qualities of the finished product all affect how much sprue and runner can be reused in injection molding. Sprue and runner reuse is frequently done in the injection molding industry because it can lower costs and waste.
Additionally, the sprue and runner are normally fastened to the molded object in a two-plate mold, and the assembly as a whole is ejected from the mold. The item can then be manually detached from the sprue and runner, which can be utilized in other molding cycles.
Sprue and runner reuse could necessitate further processing procedures, including grinding or remelting, to ensure the material is in an appropriate form for reuse. In a three-plate mold, the ejection procedure separates the sprue and runner from the molded object, and the sprue is often reused in consecutive molding cycles.
The runner plate is typically detachable, making it easier to access the runner system and reuse the sprue and runner. It is crucial to remember that the reuse of sprue and runner can significantly impact the final product’s consistency and quality.
However, reused materials could have impurities or consistency issues that influence the strength or durability of the plastic material. To achieve consistent and high-quality products, continuous monitoring of the molding process and the quality of the recycled material is required.
In general, the injection molding industry reuses sprue and runner in two- and three-plate molds, which can help cut costs and waste. Ensuring the final product’s quality and qualities aren’t compromised requires rigorous thought and management.
Injection Molding Machines
The machines used for the infection molding process include the following:
Injection Units
The injection unit, which melts and injects plastic material into the mold, is a crucial part of an injection molding machine. The typical components are the barrel, heater, screw or plunger, hopper, and injection unit.
Before being put into the barrel, the plastic material is first fed into the hopper and kept there. The moving screw or plunger and the heat from the heater melt and homogenize the plastic inside the barrel. As it advances, the molten plastic material is injected into the mold through a gate by the screw or plunger.
The injection unit’s purpose is to precisely regulate the plastic material’s temperature, pressure, and flow rate throughout the injection molding process. This guarantees that the plastic material is uniformly homogenized, correctly melted, and injected into the mold.
It’s also possible to change the injection unit’s speed, pressure, and volume, which is crucial when molding objects with intricate geometries or exacting tolerances. Depending on the exact application, the kind and size of the injection unit may change, with some machines made for high-volume production and others for precise or small-scale molding.
The injection unit is crucial for generating high-quality plastic goods and is often one of the most significant components in defining the performance and capabilities of an injection molding machine.
Reciprocating Screw Machine
An injection molding device, a reciprocating screw machine, melts and injects plastic material into the mold using a reciprocating screw. Due to its adaptability, effectiveness, and capacity to create high-quality plastic goods, this equipment is frequently utilized in the injection molding sector.
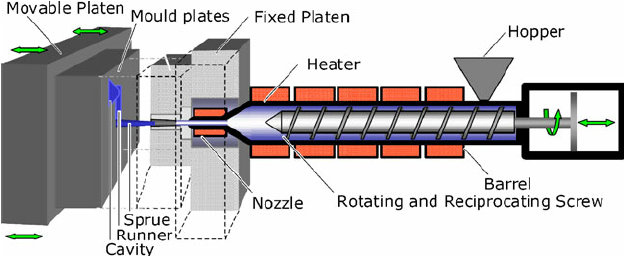
Ideally, injection molding involves melting and injecting thermoplastic materials into a mold using a reciprocating screw machine. The plastic pellets are fed into the barrel of the machine by the reciprocating screw and melted, thereby pressure and heat.
After being melted, the plastic is injected into the mold using a screw under high pressure to give the finished product the desired shape.
Screw-Pre Plasticizer Machine or Two-Stage Machine
The two-stage machine is an injection molding machine that uses two independent injection units; one for melting the plastic material and another for injecting it into the mold.
The melting and preparation for injection of the plastic material are referred to as the first stage, or “plasticizing.” At this stage, a reciprocating screw produces heat and pressure that melt the plastic as it is supplied into the machine’s primary injection unit.
The melted plastic material is pumped into the mold during the second stage, also called the “metering” stage. This step involves moving the melted plastic from the primary injection unit to the secondary injection unit, where it is injected under solid pressure into the mold.
Large and complex pieces are frequently produced using two-stage machines because they provide superior molding process control and enable more accurate injection of the plastic material into the mold.
Clamping Units
The following clamping units are used to make injection molded parts:
Toggle Clamps
To hold the two parts of the mold together while the injection process is taking place, toggle clamps are employed in injection molding. The clamps are made to generate a strong clamping force to make sure that the mold stays closed and correctly oriented throughout the injection of the molten plastic material.
Toggle clamps increase the clamping force delivered to the mold through a linkage system. The linkage system produces a mechanical advantage when the clamp is engaged, increasing the force applied to the mold. As a result, the clamps may apply much force with only a small input force.
Additionally, toggle clamps are favored in injection molding because they provide a robust and dependable gripping force that can be altered to fit the unique needs of the molding process. Additionally, they are quick to engage and disengage and are simple to use, all of which contribute to a shorter overall cycle time for the molding process.
Hydraulic Clamps
Hydraulic clamps are frequently employed in injection molding to hold the two halves of the mold together during the injection process. To deliver a strong clamping force to the mold and keep it securely closed and aligned during the injection of the molten plastic material, hydraulic clamps use hydraulic pressure.
A hydraulic pump, control valves, and cylinders make up the conventional hydraulic system utilized in the clamping mechanism. The cylinders move the clamping platen or the mold mounting plate when the hydraulic system is activated, applying pressure to the mold in the process.
Hydromechanical Clamps
To keep the two parts of the mold together during the injection molding project, injection molding uses hydromechanical clamps, also referred to as toggle-assist clamps.
By combining a hydraulic system to start the clamping process and a mechanical toggle mechanism to increase and sustain the clamping force, hydromechanical clamps combine the benefits of hydraulic and mechanical clamping methods.
A hydraulic cylinder that moves the clamping platen toward the fixed platen generates the clamping force. Once a particular amount of clamping force has been reached, the hydraulic cylinder locks, and the mechanical toggle mechanism takes over to continue to apply clamping force.