Метод литья под давлением используется для изготовления форм для литья под давлением для идентичных деталей, известных как формованные компоненты. Этот процесс требует высокого давления, и расплавленный пластик или другой материал впрыскивается в полость пресс-формы для литья пластмасс под давлением.
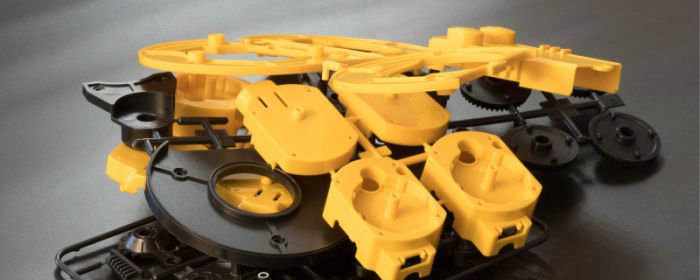
Второй этап происходит внутри формы, где вещество охлаждается и затвердевает, приспосабливаясь к контурам полости. Отформованная часть затем удаляется после открытия формы. Процедура повторяется несколько раз, чтобы создать много одинаковых частей.
Кроме того, чрезвычайно прочная сталь обычно используется для форм для литья под давлением, которые выдерживают высокое давление и тепло, возникающие в процессе литья под давлением. Для изготовления точных и однородных деталей формы должны быть точными.
На качество готового продукта существенное влияние оказывает конструкция пресс-формы, которая может быть сложной из-за таких соображений, как тип формуемого материала, предполагаемая форма готового изделия и задействованные производственные процедуры.
Формованные детали используются в различных продуктах, от простых товаров для дома до сложных механических деталей, используемых в таких секторах, как автомобилестроение, электроника и медицинское оборудование. Литье под давлением является популярным методом производства различных продуктов из-за его адаптируемости и доступности.
Изделия для литья под давлением: оборудование и процесс
Используя специализированное оборудование, промышленный процесс литья под давлением создает формованные компоненты из термопластичных или термореактивных материалов. В производстве изделий для литья под давлением необходимы следующие компоненты:
Оборудование
В процессе литья под давлением используется следующее оборудование:
- Машина для литья под давлением: Эта машина содержит такие компоненты, как бункер, нагревательный цилиндр, возвратно-поступательный шнек и зажим формы, которые составляют основную часть процедуры литья под давлением. Пластиковые гранулы расплавляются машиной и впрыскиваются под сильным давлением в форму для изготовления формованной детали.
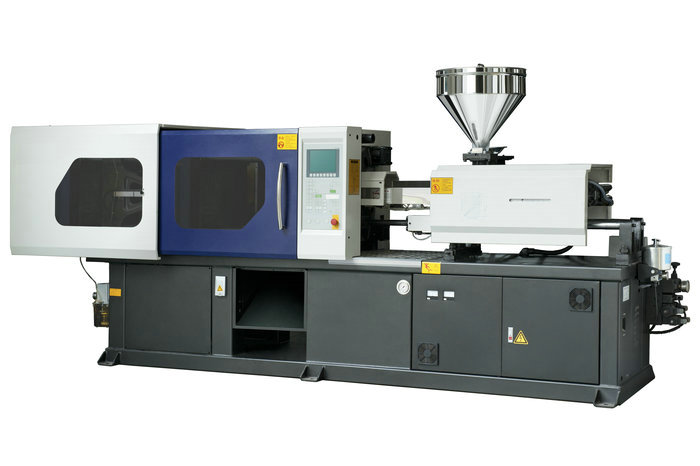
- Полость формы: Этот инструмент, часто состоящий из стали или алюминия, придает пластику форму. Две части формы скрепляются во время процедуры литья под давлением.
- Бункер для материала: Перед подачей в нагревательный цилиндр машины для литья под давлением пластиковые гранулы хранятся здесь.
- Отопительный ствол: Пластиковые гранулы расплавляются на этом этапе процесса литья под давлением, поэтому они готовы к впрыскиванию в форму.
- Поршневой винт: Эта часть машины для литья под давлением нагревает пластик, прежде чем направить его в форму.
- Зажим пресс-формы: Эта система применяет давление, необходимое для впрыска расплавленного пластика в форму, удерживая форму закрытой во время процесса литья под давлением.
- Система охлаждения: Это используется для охлаждения отлитых под давлением компонентов после их создания. Этого можно добиться путем охлаждения системы воздухом, водой или их комбинацией.
Это основные элементы установки для литья под давлением. В зависимости от конкретных потребностей процесса литья под давлением может также использоваться дополнительное вспомогательное оборудование, такое как грануляторы, сушилки материалов и устройства контроля температуры.
Блок впрыска пластика
Плавление и впрыск пластика в полость пресс-формы осуществляется с помощью блока впрыска пластика при литье под давлением. Пластмассовый материал расплавляется и впрыскивается в форму с помощью нагретого цилиндра, шнека и сопла.
Затем пластиковое вещество помещается в цилиндр, где движущийся винт нагревает и перемешивает его. На следующем этапе сопло впрыскивает пластиковый материал в полость формы после того, как он достигнет нужной температуры и консистенции, где он охлаждается и затвердевает для получения желаемого результата.
Для поддержания постоянного и высокого качества выпуска продукции необходимо надлежащим образом управлять устройством для впрыска пластика, которое является важной частью процесса литья под давлением.
Блок зажима пресс-формы
Две половины пресс-формы должны быть плотно закрыты и удерживаться вместе во время процессов впрыска и охлаждения с помощью зажимного устройства пресс-формы при литье под давлением. Усилие зажима, необходимое для прочного соединения половинок пресс-формы и предотвращения просачивания пластикового материала из полости пресс-формы, прикладывается и поддерживается устройством.
Стационарная плита и подвижная плита, соединенные с гидравлической или механической системой, составляют узел зажима пресс-формы. Две пластины стягиваются, когда форма помещается в машину, а затем прикладывается усилие зажима, чтобы удерживать форму закрытой.
Величина необходимой силы зажима варьируется в зависимости от размера, сложности и типа используемого пластика и формы. Чтобы обеспечить безопасное и эффективное производство, узел зажима пресс-формы, являющийся важной частью процесса литья под давлением, должен тщательно контролироваться.
Процессы: литье под давлением термопластичных полимеров
Процесс литья под давлением термопластичных полимеров обычно включает в себя следующее:
Плесень
Литье под давлением термопластичных полимеров в значительной степени зависит от формы для литья под давлением. Это устройство, используемое для формования расплавленного пластика в желаемое готовое изделие. Полость и сердцевина, два основных компонента пресс-формы, обычно сконструированы таким образом, чтобы соответствовать друг другу для создания трехмерной формы.
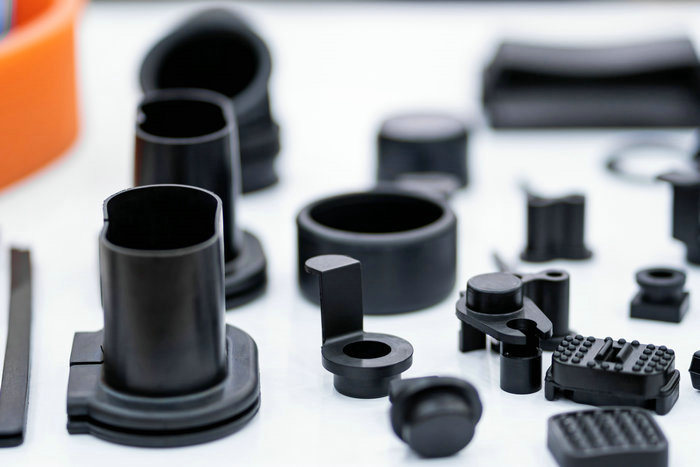
После впрыскивания в полость формы пластик охлаждается и затвердевает, принимая форму формы. Конечная форма и размер продукта определяются конструкцией пресс-формы, что делает ее важным компонентом процесса литья под давлением.
Форма должна быть тщательно разработана, чтобы гарантировать, что пластиковый материал без усилий заполнит каждую полость, а процесс охлаждения будет быстрым и равномерным. Кроме того, пресс-форма должна быть изготовлена из материалов, выдерживающих высокие температуры и давления, используемые в процессе литья под давлением.
Поскольку форму можно использовать повторно во время впрыска, ее можно использовать для создания множества одинаковых деталей. Чтобы пресс-форма оставалась в хорошем состоянии и могла продолжать производить высококачественные детали, может потребоваться регулярная очистка пресс-формы и ее техническое обслуживание.
Двухпластинчатая форма
При литье под давлением термопластичных полимеров двухпластинчатая пресс-форма является типичным типом пресс-формы. Он состоит из двух частей, закрепленных на двух плитах формовочной машины, половины полости и половины стержня. Форма с двумя плитами называется так потому, что она состоит из двух частей с разделительной линией, разделяющей две части формы.
Задача двухпластинчатой пресс-формы состоит в том, чтобы придать расплавленному пластику требуемую окончательную форму. Пластичный материал впрыскивается в полость половины пресс-формы через заслонку на разделительной линии. Полость заполняется пластиковым материалом, которому затем дают остыть и затвердеть. Готовое изделие выпускается после того, как две половины формы разделены.
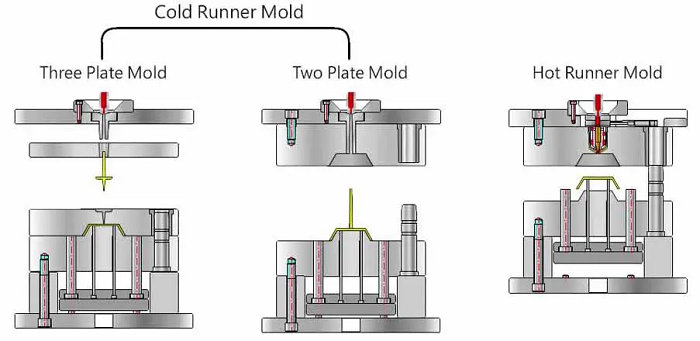
Поскольку для этого нужны только две пластины и несколько простых компонентов, форма с двумя пластинами является достаточно простым и доступным типом формы. Он хорошо работает для компонентов с простой геометрией, включая плоские или закругленные кривые.
Однако это может не подходить для деталей с более сложной геометрией, потому что в этих обстоятельствах заполнение полости пластиком может быть затруднено. В литье под давлением форма с двумя пластинами универсальна и часто используется, особенно для простых деталей и небольших производственных циклов.
Трехпластинчатая форма
Трехпластинчатая форма является одной из форм, используемых при литье под давлением термопластичных полимеров. По сравнению с пресс-формой с двумя пластинами, она имеет больше возможностей и универсальности, поскольку имеет три пластины; два подвижных и один устойчивый.
Трехпластинчатая пресс-форма предназначена для придания пластиковым литым деталям требуемой окончательной формы. Пластичный материал впрыскивается в полость пресс-формы наполовину через заслонку на разделительной линии.
Как только расплавленный пластик попадает в полость формы, две подвижные пластины отсоединяются от неподвижной пластины, позволяя вытолкнуть пластиковый объект из формы. Третья пластина в трехпластинчатой форме, расположенная между полостью и половиной сердечника, называется направляющей плитой или вспомогательной плитой.
С помощью этой пластины можно создать уникальную систему направляющих, которую можно использовать для направления потока пластикового материала в различные полости или места внутри одной полости. В результате процесс литья под давлением может быть более гибким и эффективным.
При производстве более крупных изделий, где использование формы с двумя плитами приведет к увеличению размера формы или потребует установки дополнительных функций, таких как подъемники, часто используется форма с тремя плитами. Включая несколько полостей в конструкцию пресс-формы, пресс-форма с тремя пластинами может изготавливать различные детали за один цикл.
Трехпластинчатая пресс-форма представляет собой универсальный и эффективный тип пресс-формы, часто используемый в процессе литья под давлением, особенно для крупных деталей и производственных циклов.
Повторное использование литника и рабочего колеса в двух- и трехпластинчатых пресс-формах
Используемый материал, геометрия детали и желаемое качество конечного продукта — все это влияет на то, сколько литников и литейных каналов можно повторно использовать при литье под давлением. Повторное использование литников и направляющих часто используется в литьевой промышленности, поскольку это может снизить затраты и количество отходов.
Кроме того, литник и литник обычно крепятся к формованному изделию в двухпластинчатой форме, а сборка в целом выталкивается из формы. Затем изделие можно вручную отсоединить от литника и направляющей, которые можно использовать в других циклах формования.
Повторное использование литников и литников может потребовать дополнительных процедур обработки, включая шлифовку или переплавку, чтобы убедиться, что материал находится в подходящей форме для повторного использования. В пресс-форме с тремя плитами процедура выталкивания отделяет литник и бегунок от формованного объекта, и литник часто повторно используется в последовательных циклах формования.
Пластина литника обычно является съемной, что облегчает доступ к системе литника и повторное использование литника и литника. Крайне важно помнить, что повторное использование литника и литника может значительно повлиять на консистенцию и качество конечного продукта.
Однако повторно используемые материалы могут иметь примеси или проблемы с консистенцией, которые влияют на прочность или долговечность пластика. Для получения однородной и высококачественной продукции требуется постоянный контроль процесса формования и качества перерабатываемого материала.
Как правило, в индустрии литья под давлением повторно используются литники и направляющие в двух- и трехпластинчатых пресс-формах, что может помочь сократить расходы и сократить количество отходов. Обеспечение того, чтобы качество и качество конечного продукта не ухудшались, требует тщательного обдумывания и управления.
Машины для литья под давлением
Машины, используемые для процесса инфекционного формования, включают следующее:
Установки для инъекций
Узел впрыска, который плавит и впрыскивает пластиковый материал в форму, является важной частью машины для литья под давлением. Типичными компонентами являются цилиндр, нагреватель, шнек или плунжер, воронка и узел впрыска.
Перед помещением в бочку пластиковый материал сначала подается в бункер и хранится там. Движущийся винт или поршень и тепло нагревателя плавят и гомогенизируют пластик внутри цилиндра. По мере продвижения расплавленный пластиковый материал впрыскивается в форму через затвор с помощью винта или плунжера.
Целью блока впрыска является точное регулирование температуры, давления и скорости потока пластмассы на протяжении всего процесса литья под давлением. Это гарантирует, что пластик будет однородно гомогенизирован, правильно расплавлен и впрыснут в форму.
Также возможно изменить скорость, давление и объем узла впрыска, что имеет решающее значение при формовании объектов со сложной геометрией или строгими допусками. В зависимости от конкретного применения тип и размер узла впрыска могут меняться: некоторые машины предназначены для крупносерийного производства, а другие — для точного или мелкосерийного формования.
Блок впрыска имеет решающее значение для производства высококачественных пластиковых изделий и часто является одним из наиболее важных компонентов, определяющих производительность и возможности машины для литья под давлением.
Винтовая машина с возвратно-поступательным движением
Устройство для литья под давлением, машина с возвратно-поступательным движением шнека, плавит и впрыскивает пластиковый материал в форму с помощью возвратно-поступательного шнека. Благодаря своей адаптируемости, эффективности и способности создавать высококачественные пластиковые изделия это оборудование часто используется в секторе литья под давлением.
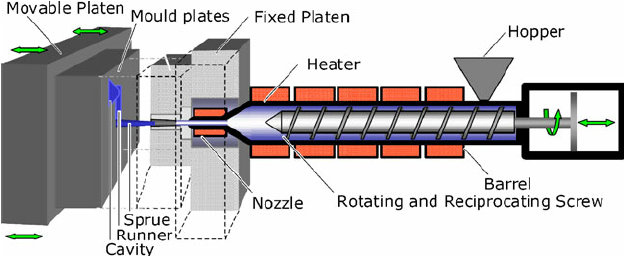
В идеале литье под давлением включает плавление и впрыскивание термопластичных материалов в форму с помощью шнековой машины с возвратно-поступательным движением. Пластиковые гранулы подаются в ствол машины возвратно-поступательным движением шнека и расплавляются под действием давления и тепла.
После расплавления пластик впрыскивается в форму с помощью шнека под высоким давлением, чтобы придать готовому изделию желаемую форму.
Винтовой препластификатор или двухступенчатая машина
Двухступенчатая машина представляет собой машину для литья под давлением, в которой используются два независимых узла впрыска; один для плавления пластикового материала, а другой для впрыскивания его в форму.
Плавление и подготовка пластика к впрыскиванию называются первой стадией или «пластификацией». На этом этапе возвратно-поступательный шнек создает тепло и давление, которые плавят пластик, когда он поступает в первичный блок впрыска машины.
Расплавленный пластиковый материал закачивается в форму на втором этапе, также называемом этапом «дозирования». Этот этап включает в себя перемещение расплавленного пластика из узла первичного впрыска во вторичный узел впрыска, где он впрыскивается под твердым давлением в форму.
Большие и сложные детали часто изготавливаются с использованием двухступенчатых машин, поскольку они обеспечивают превосходный контроль процесса формования и позволяют более точно вводить пластиковый материал в форму.
Зажимные устройства
Для изготовления литьевых деталей используются следующие зажимные устройства:
Перекидные зажимы
Чтобы удерживать две части формы вместе во время процесса литья под давлением, при литье под давлением используются шарнирно-рычажные зажимы. Зажимы предназначены для создания сильного зажимного усилия, чтобы убедиться, что форма остается закрытой и правильно ориентированной во время впрыска расплавленного пластикового материала.
Шарнирно-рычажные зажимы увеличивают усилие зажима, прикладываемое к пресс-форме за счет системы рычагов. Система сцепления обеспечивает механическое преимущество при включении зажима, увеличивая усилие, прикладываемое к пресс-форме. В результате зажимы могут прилагать большое усилие при небольшом усилии.
Кроме того, при литье под давлением предпочтение отдается шарнирно-рычажным зажимам, поскольку они обеспечивают надежное и надежное усилие зажима, которое можно изменять в соответствии с уникальными потребностями процесса литья. Кроме того, они быстро включаются и расцепляются и просты в использовании, что способствует сокращению общего времени цикла процесса формования.
Гидравлические зажимы
Гидравлические зажимы часто используются в литье под давлением, чтобы скрепить две половины формы во время процесса литья под давлением. Чтобы передать сильное зажимное усилие пресс-форме и удерживать ее надежно закрытой и выровненной во время впрыска расплавленного пластикового материала, гидравлические зажимы используют гидравлическое давление.
Гидравлический насос, регулирующие клапаны и цилиндры составляют обычную гидравлическую систему, используемую в зажимном механизме. Цилиндры перемещают зажимную пластину или монтажную плиту пресс-формы, когда гидравлическая система активирована, оказывая давление на пресс-форму в процессе.
Гидромеханические зажимы
Чтобы удерживать две части формы вместе во время проекта литья под давлением, в литье под давлением используются гидромеханические зажимы, также называемые зажимами с рычажным механизмом.
Комбинируя гидравлическую систему для запуска процесса зажима и механический рычажный механизм для увеличения и поддержания силы зажима, гидромеханические зажимы сочетают в себе преимущества гидравлического и механического методов зажима.
Гидравлический цилиндр, который перемещает прижимную плиту к неподвижной плите, создает зажимное усилие. Как только достигается определенное усилие зажима, гидравлический цилиндр блокируется, и механический рычажный механизм продолжает прикладывать усилие зажима.