Compression molding and injection molding are two of the most common manufacturing processes used for producing plastic parts on a large scale. While both involve shaping plastic in a mold under heat and pressure, there are some key differences in how each method works.
Understanding the distinctions between compression molding vs injection molding is important for manufacturers to determine which approach is best suited for a given application. However, the specifics of the processes can be confusing even for those familiar with plastics production.
This article aims to provide a clear overview of the similarities and differences between compression molding and injection molding. We’ll break down the basic steps involved in each technique and how they vary. Factors like part design suitability, cycle times, material waste and cost-effectiveness will also be examined.
An Overview of Injection and Compression Molding
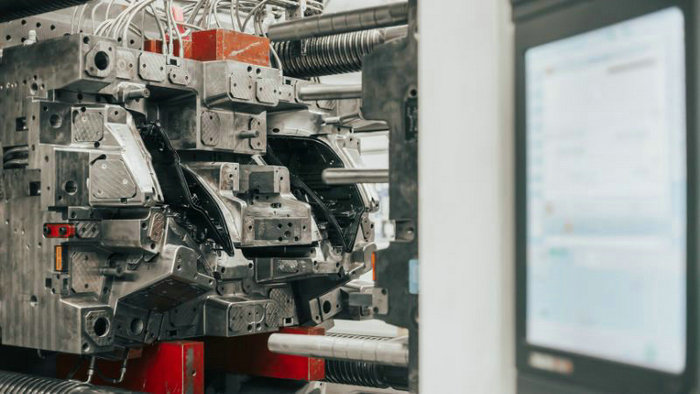
Understanding Injection Molding
Injection molding is a manufacturing method that involves heating a material, usually a thermoplastic, and injecting it into a closed mold through a hopper and a screw. The material cools and solidifies, taking the desired shape. Injection molding offers various advantages, such as:
- Suitability for complex parts: It’s well-suited for parts with intricate details and complex shapes.
- High automation: This process typically doesn’t need constant human supervision.
- Fast production times: Injection molding has shorter cycle times than compression molding.
However, injection molding has its disadvantages, including high initial tooling costs and difficulty in producing very large parts.
Defining Compression Molding
Compression molding is a manufacturing process where a preheated material, typically a thermosetting plastic, is placed into a mold cavity. The mold is then closed, and pressure is applied to force the material to conform to the shape of the mold. This process is well-suited for simple geometries and large panels. However, it has some limitations, including:
- Limited to simpler designs: Compression molding isn’t the best choice for intricate details or complex geometries.
- Slower production rates: Cycle times are longer compared to injection molding.
- Labor-intensive: Material placement often requires more manual labor.
The main differences between compression and injection molding:
- Compression molding is typically used for larger, simpler parts like gaskets. Injection is better for small, complex, high-precision parts.
- Compression molding has lower tooling costs but slower cycle times. Injection molding has faster cycle times and is better for high-quality parts, making it a popular choice for many industries.
- Injection molding offers higher dimensional precision and consistency.
In summary, compression molding is an excellent choice for simpler parts with larger panels, while injection molding is better for more complex and detailed components. While both processes are useful and versatile, understanding the specific requirements of your project will help you choose the best technique for your needs.
Material Considerations
Material Selection for Compression Molding
Compression molding uses thermoset materials, which offer excellent strength, dimensional stability, and resistance to high temperatures. Some commonly used materials for compression molding include:
- Bulk Molding Compound (BMC): A mixture of polyester resin, glass fibers, and mineral fillers that provides mechanical strength and dimensional stability. It is commonly used for automotive, electrical, and consumer product applications.
- Sheet Molding Compound (SMC): Similar to BMC, SMC consists of a thermosetting resin combined with glass fibers. SMC features higher strength-to-weight ratios and is suitable for larger components, such as automotive body parts and aerospace components.
- Diallyl Phthalate (DAP): A thermosetting plastic offering excellent electrical insulation properties, DAP is often used in electrical components and switchgear applications.
- Phenolics & Vinyl Esters: These materials boast strong resistance to chemicals and heat. Phenolics are often used for electrical components, while vinyl esters find their way into corrosion-resistant applications.
Material Use in Injection Molding
On the other hand, injection molding is frequently uses thermoplastic materials that can be melted and reused. The following are some popular thermoplastics used in injection molding:
- Polyethylene (PE): A versatile plastic used in a wide range of applications such as packaging, toys, and consumer goods. It can be found in various forms, including high-density polyethylene (HDPE) and low-density polyethylene (LDPE).
- Polypropylene (PP): Known for its chemical resistance, impact strength, and durability, PP is used in automotive parts, food packaging, and medical devices.
- Polyvinyl Chloride (PVC): Commonly used for pipes and fittings, PVC offers excellent resistance to chemicals and weathering.
- Polystyrene (PS): From disposable food service items to home appliances, PS is a frequently used material due to its low cost and ease of processing.
- Nylon: Distinguished by its strength and heat-resistance, nylon is employed in applications such as automotive parts, textiles, and electrical components.
The Molding Machine
Compression Molding Machines
The main components of a compression molding machine include:
- Mold – Usually made of steel, aluminum or epoxy. Consists of two halves that contain the mold cavity.
- Heating Platens – Heat the mold to melt the plastic resin. Often oil-heated or electrically heated.
- Hydraulic Ram – Applies high pressure to close the mold and compress the material.
- Ejector System – Pins, sleeves, strippers that help remove the molded part.
The raw material starts in granule form and is preheated and placed into the mold cavity. The platens close and pressure is applied, forcing the raw plastic material to take the shape of the mold. After cooling and curing, the mold opens and the part is ejected.
Injection Molding Machines
The main components of an injection molding machine include:
- Hopper – Holds the plastic pellets or granules before molding
- Barrel – Contains the reciprocating screw that rotates to melt the material
- Screw – Rotates and mixes the melting plastic, then injects it into the mold
- Clamping Unit – Opens and closes the mold halves
- Heaters – Band heaters surround the barrel to melt the plastic
- Hydraulic Systems – Apply pressure for injection and clamping
- Ejection System – Pins, sleeves and strippers help remove the part
The granules are fed into the barrel from the hopper. As the screw rotates, friction and heat melt the material. The screw then injects the molten plastic at high pressure into the mold cavity. The material cools and hardens into the final part shape before being ejected.
Injection vs Compression: The Molding Process in Detail
The Process of Compression Molding
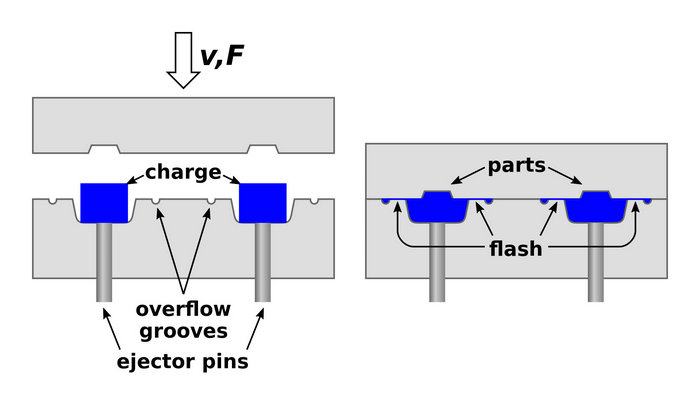
In the compression molding process, your raw material, typically a preheated rubber or thermosetting plastic, is placed directly into the mold cavity. This cavity is shaped like the desired final product and has been heated beforehand, which helps with material flow and curing. The mold is then closed, and pressure is applied, ensuring that the material completely fills the mold cavity.
The Process of Injection Molding
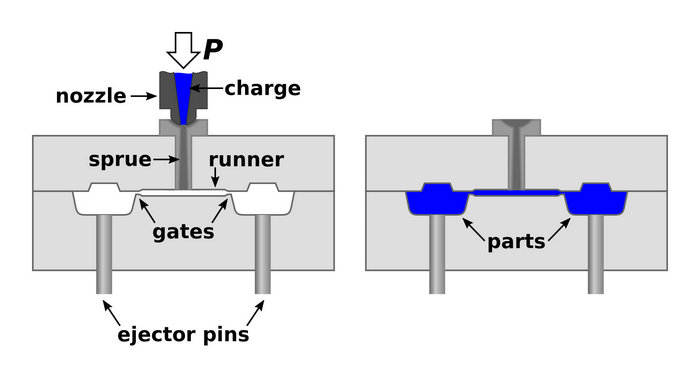
Injection molding, on the other hand, is a bit more complex. First, you’ll need to feed the raw material, usually in the form of plastic pellets, into a hopper. The material will then be pushed through a screw which heats and melts the plastic, turning it into a liquid state.
Next, the liquefied plastic is injected into the heated mold cavity under high pressure, filling it completely. The material cools down and solidifies inside the mold, taking on the desired shape. Finally, the mold is opened, and the finished product is ejected.
This process is ideal for high-volume production, given its potential for producing highly detailed and complex parts. Injection molding can also achieve faster production rates compared to compression molding.
In short, here’s a brief comparison of the two processes:
Compression Molding | Injection Molding | |
Raw Material Placement | Manual, in heated mold cavity | Via hopper and screw, into the heated mold cavity |
Pressure | Applied when mold is closed | High pressure during injection |
Heat | Preheated mold cavity and material | Screw heats the material; heated mold cavity |
Detail Complexity | Suited for simpler designs | Capable of producing intricate details and complex geometries |
Production Volume | Medium-volume | High-volume |
Labor Intensity | More manual labor for material placement | Less labor-intensive, as material is fed through hopper and screw |
Tooling and Manufacturing Costs
When considering compression molding and injection molding for your project, it’s essential to understand the differences in tooling and manufacturing costs. The following information will help you get a better grasp of these processes from a cost perspective.
Tooling Costs
Compression Molding: Tooling costs for compression molding are generally lower than injection molding. The molds are easier to maintain and have a longer lifespan. This makes compression molding a viable option for a cost-effective manufacturing process, particularly for smaller production runs and simpler part designs.
Injection Molding: Tooling costs for injection molding can be higher due to the complexity of the molds, which often require multiple parts and cooling systems. However, in the long run, the initial investment in quality tooling for injection molding may pay off, especially if you plan on large production runs or need more intricate parts.
Manufacturing Process and Costs
Compression Molding: In the compression molding process, preheated materials are placed in the mold cavity, which is then closed and subjected to heat and pressure. Due to its labor-intensive nature, this method can result in higher per-part costs, especially for smaller production volumes.
Injection Molding: The injection molding process involves injecting molten material into the mold cavity under high pressure. This process has the advantage of faster production rates compared to compression molding, which can reduce part costs when dealing with large production runs. The automated nature of injection molding can also lead to better consistency and quality of the finished parts.
To summarize:
Compression Molding | Injection Molding | |
Tooling Costs | Lower, easier to maintain | Higher, more complex |
Manufacturing | Labor-intensive, slower | Automated, faster |
Cost-Effective | Smaller production runs | Large production runs |
Intricate Parts | Not ideal for complex parts | Suitable for complex parts |
Applications and Suitability Factors
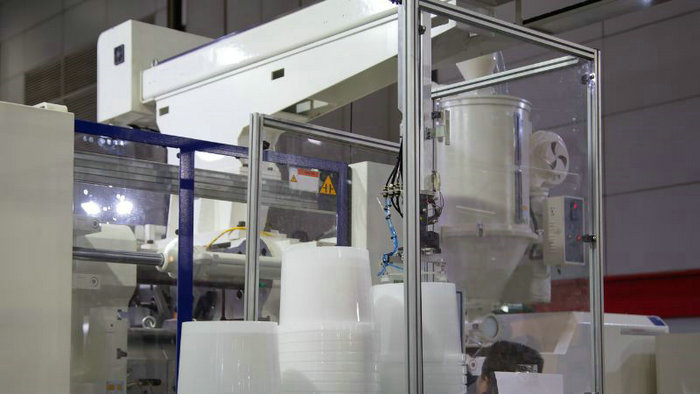
Applications of compression molding include automotive, industrial, and consumer products. It’s a popular choice for manufacturing gaskets, seals, and other rubber components.
Injection molding also produces automotive products. It creates intricate, high-precision parts in industries like medicine.
Here is a summary:
Molding Process | Use Cases |
Compression Molding | – Automotive: Gaskets, seals, rubber components – Medical: Silicone components due to biocompatibility – Industrial: Large, durable parts for heavy-duty equipment |
Injection Molding | – Automotive: Plastic components for interior, exterior, engine parts, connectors – Medical: High precision medical devices, consumables, diagnostic equipment – Consumer Products: Toys, food containers – high production speed and efficiency |
Strength and Durability of Compression Molding and Injection Molding
When comparing compression molding and injection molding, it’s essential to consider the strength and durability of the produced parts. Both processes can produce high-strength materials, but certain factors affect the overall strength.
Here’s a quick comparison of both processes regarding strength and durability:
Compression Molding | Injection Molding | |
Material choices | Urethane, composites | Plastics, metals |
Strength & Durability | Dense, strong parts | Material-dependent |
Complex shapes | Limited options | More flexibility |
Frequently Asked Questions
What are the key differences between compression molding and injection molding?
In compression molding, a premeasured amount of material is placed in a mold cavity, which is then closed and compressed under heat and pressure to form the desired shape. Injection molding, on the other hand, involves injecting heated, liquified material (typically plastic) into a mold cavity to create components and parts. While injection molding is generally more automated and better suited for complex parts, compression molding is often used for simpler geometries and may require more human intervention.
How do costs compare between compression molding and injection molding?
The costs of compression and injection molding can vary depending on the specific project requirements. Compression molding is typically more affordable for building simple components, particularly when upfront tooling and equipment costs are considered. However, the greater automation and efficiency of injection molding can offer cost advantages in large-scale production or when creating intricate components.
What materials are suitable for compression molding vs injection molding?
Both processes can handle various materials, including thermoplastics, thermosetting plastics, and elastomers. Injection molding is predominantly used for thermoplastics, while compression molding is commonly used with thermosetting plastics and rubber materials. It is essential to choose the right molding process based on the specific material properties and application requirements.
In which industries are compression molding and injection molding most commonly used?
Compression and injection molding are employed across a wide range of industries, such as automotive, aerospace, medical, electronics, and consumer goods. Injection molding is often chosen for producing intricate parts for electronics and medical devices. Compression molding is commonly used in creating rubber components, such as gaskets or seals, and large panel production in the automotive and aerospace industries.
What are the main advantages of injection molding over compression molding?
Injection molding offers several advantages over compression molding. These include greater automation, which reduces labor costs and the need for constant supervision, increased precision and repeatability in creating complex components, and faster production rates due to reduced cycle times. This makes injection molding the preferred choice for large-scale production and intricate part designs.
How do cycle times and production rates differ between compression molding and injection molding?
Injection molding typically has shorter cycle times and higher production rates compared to compression molding. This is because injection molding is a more automated process, allowing for quicker material injection, cooling, and solidification. Compression molding, on the other hand, requires time for material to be placed in the mold, compressed, heated, and then cooled before being removed. Consequently, the slower cycle times of compression molding can result in lower overall production rates for this process.