Die casting uses high temperatures and pressure in manufacturing molten metals and alloys to generate the desired shape. It involves melting low melting-point metals and inserting them into die-casting molds.
Usually, die casting is classified according to the temperature and pressure needed to insert the molten metal into the die-cast mold. Nevertheless, it can also be classified according to the type of material used in the process, and zinc is among the most common versatile die-cast metals. With that in mind, here’s all you need to know about zinc alloy casting:
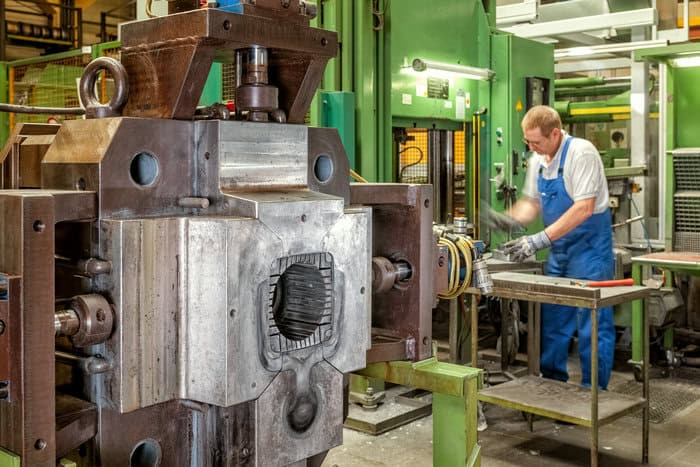
What Is Zinc Die Casting?
Zinc die casting is a process involving the injection of liquid zinc metal under pressure into a mold and left to solidify. The mold cavity is made from two hardened tool steel molds designed to your desired shape.
Zinc alloys have low melting points, hence the casting proceeds under lower heat. Additionally, their impact strength and ductility make them suitable for part manufacturing.
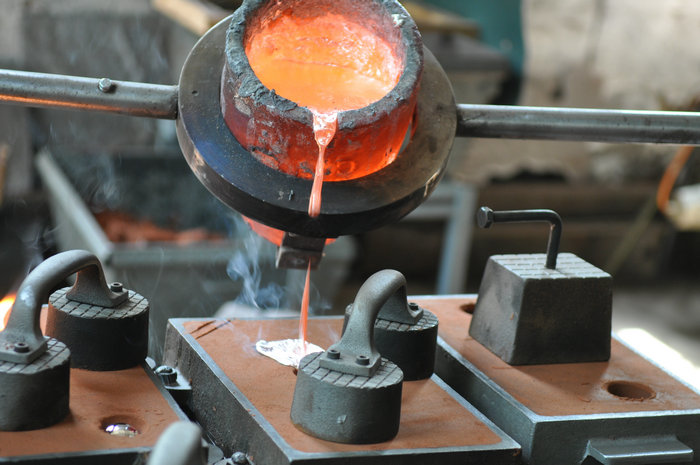
Steps Of The Zinc Die Casting Process
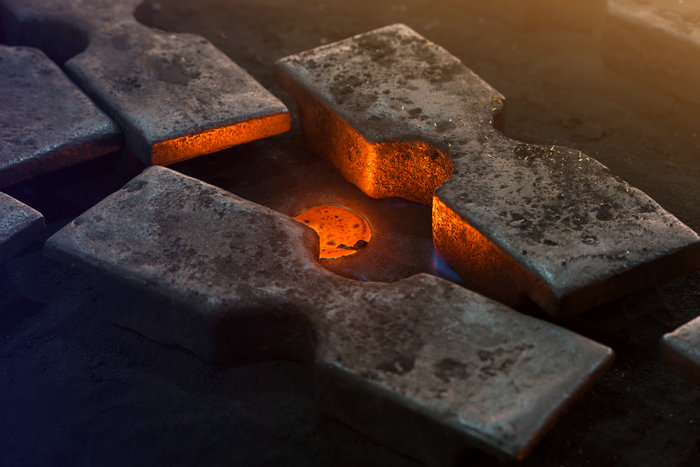
The zinc alloy die-casting process may differ depending on the size and types of machines you use. However, there’s a general procedure you can follow as outlined below:
- Step 1: Preparing the Die
Before starting your casting process, the first thing is to prepare the die itself. Here, you need to purify the die-cast mold by cleaning it. Then, lubricate the die to enhance the casted portion’s insertion after cooling. You can also lubricate the inner walls of the molds to control the mold’s temperature and facilitate easy removal of the cast.
Finally, clamp the die under high pressure.
- Step 2: Injection
The next step is to insert the zinc alloy into the machine’s shot chamber. Here, you need to melt your zinc alloy before the injection. Since zinc alloy die casting is a hot chamber die cast process, the shot chamber will be hot. Next, insert the molten zinc metal into the mold under high pressure.
- Step 3: Cooling and Ejection
After injecting the molten zinc into the chamber, you can leave it to cool and solidify. Ensure to give your metal adequate time to gel and take the shape of the mold. Also, ensure it’s completely set before unclamping the die. Remember that ejecting the cast prematurely can lead to permanent damage.
Once your die cools and solidifies, you can unclamp the die halves, open them, and carefully remove the cast parts.
- Step 4: Trimming
The last step in the zinc die-casting process is trimming. While the metal is cooling, you can keenly remove any scrap metal, such as flash, sprues, and runners, from the zinc casting. You may use tools like a saw, trim die, etc., to achieve your desired component shape. Ensure to clean every part before dispatching it to your clients.
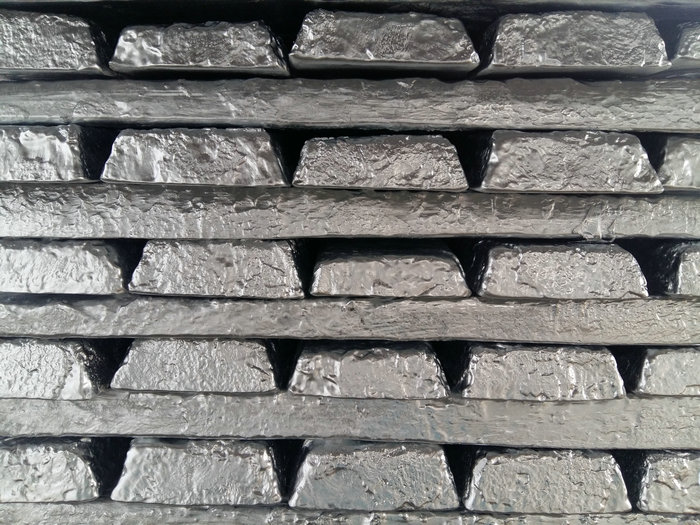
Zinc Alloys for Die Casting
Below are the most common zinc alloys suitable for die casting:
- Zamak 2
Also known as zinc alloy 2 or kirksite, zamak 2 has the highest strength and hardness of all the zamak alloys. For this reason, it’s used in casting sections that need high structural integrity, like the automotive and mechanical sectors.
Besides that, Zamak 2 has outstanding casting features like high creep performance, superb damping capacity, and vibration resistance than other metal alloys.
- Zamak 3
Zamak 3 zinc alloy is one of the most popular alloys for die casting due to various reasons, including the following:
- Excellent castability and durable dimensional stability
- Perfect balance between the physical and mechanical properties
- Excellent compatibility with different finishing options like plating, chromate treatments, and painting
- Good combination of strength and flexibility
- Zamak 7
Zamak 7, also called zinc alloy 7, is a modified Zamak 3 with high purity and low magnesium content than other zamak alloys. It also has firm impurities specification, enhancing casting flexibility, fluidity, and surface finish.
This zinc alloy is applied in unique hardware uses or when casting needs additional formability during succeeding assembly operations like staking and crimping.
- ZA 8
ZA-8, or zinc-aluminum alloy, contains high aluminum content than other members of the zamak family. Compared to other ZA alloys, ZA-8 is the only ZA alloy that can be hot chamber die cast.
On top of that, ZA-8 provides significantly enhanced hardness, strength, and creep properties. It’s primarily used for decorative purposes.
- ACuZinc5
General Motors researched and developed this zinc alloy. It’s also known as zinc, copper, and aluminum alloy and has improved strength and hardness due to its low aluminum and high copper contents. Moreover, it has outstanding bearing performance, like lubricity.
ACuZinc5 is used in parts that require high structural integrity and applied in hot conditions.
- EZAC
EZAC alloy offers maximum creep resistance, higher yield strength, and hardness than other zinc alloys. It performs better than Zamak 2 and lasts longer than ACuZinc 5.
- ZA 27- Zinc Aluminium
ZA-27 contains the highest aluminum content, melting point, strength, and density compared to other ZA alloys. Ideally, this ZA alloy has 27% aluminum and displays perfect bearing properties, enabling bearings to be created in castings of specific applications.
Advantages of Zinc Die Casting
Zinc die casting offers a plethora of advantages. Some of the top benefits include the following:
Easy Assembly
One of the significant advantages of zinc die casting is that assembly operations are minimized. Generally, the zinc alloy die-casting process is done as a single unit, removing the need for costly manual assembly activities.
High Precision WIth Thin Wall
Zinc die casting generates multi-cavity, complex shapes in close tolerance than other casting processes. Moreover, it produces high-volume runs of nearly identical and wear-resistant parts with high dimensional stability.
Better Mechanical properties
Zinc alloys have numerous advantages over other materials like aluminum and zinc according to mechanical properties like firmness, strength, resistance, toughness, and durability. For this reason, zinc die castings are used in parts that need superior strength.
Cast Complex Geometries
Zinc’s excellent bearing and wear properties allow it to serve as bushings for structures in motion. Additionally, it makes it possible to manufacture die-cast parts with complex geometries because it can form joints with other materials.
Longer Tool Life
Another significant advantage of zinc Zinc die casting molds is that they can last several times longer than aluminum. This is because zinc alloys have lower melting points and are less abrasive. For this reason, there’s a decrease in mold damage and an increase in the tool’s longevity, reducing the cost of tooling more than other materials.
Faster Production
As outlined above, faster production zinc alloys require low melting temperatures and a chamber die-casting process under high pressures. As a result, it augments the zinc die casting cycle rate, which, in turn, increases the die-casting production rates.
Zinc die-casting injection is straightforward, unlike aluminum die-casting injection, which demands melting the aluminum in a different container before insertion. Furthermore, the casting has a high solidification rate, improving the number of parts produced and reducing the casting costs.
Various Finishing Options
There are numerous finishing options ideal for die-casting materials. Below are some popular ones suitable for zinc die casting:
- Powder coatings: This finishing option is suitable for aesthetic purposes because of its broad range of available colors. Besides that, it generates a long-lasting and even surface finish on the casted portions.
- Painting: Painting is responsible for functional and aesthetic properties. Like powder coating, it has various colors and is used for practical color. Painting needs a short time and low production costs.
- Plating: This boosts the functional properties, including increased durability and corrosion resistance of the zinc die-cast.
Removes bearings and bushings
Zinc’s excellent bearing and wear properties enable higher design flexibility and reduce fabrication costs by removing small bushings and wear insertions.
Good electrical and thermal conductivity
Zinc is a better conductor of heat and electricity than aluminum. As a result, zinc casting is ideal for applications such as heat sinks and other electrical components.
Less machining needed
One major advantage of zinc die casting is the less machining it requires. Zinc die casting has tighter tolerances, eliminating the need for extra machining.
Disadvantages of Zinc Die Casting
Everything that has a good side also has some disadvantages. Zinc die casting comes with the following drawbacks:
Is Prone to Defects
The zinc die-casting process is rapid, and the cooling is fast. For that reason, the gas discharge can delay, resulting in defects like:
- Blisters: These are thin films forming on the surface of zinc die-cast components.
- Cracks: These occur when the zinc metal doesn’t have enough strength to withstand tensile force during solidification.
- Swells: These are extensions in the zinc casting resulting in a smooth bulge on the vertical side of the cast.
- Mismatch or shift: This is a horizontal shift of a metal due to distortion of the upper and lower sections of the mold.
- Fusion: It occurs when sand particles combine with molten metal.
- Blow holes: Blow holes arise when improper venting leads to the metal not holding sufficient gas as the fluid form.
- Warping: This alters the dimensions of the final item and can occur during or after solidification.
- Drops: This happens when pieces of sand fall into the casting when the metal is still in liquid form.
Heavy Parts
Zinc die castings produce much heavier parts than other metals like aluminum and magnesium. For this reason, they’re unfit for lightweight uses, like in the aerospace industry.
Not Suitable for Small-Batch Production
Zinc die casting has high initial investment costs. Therefore, it’s primarily suitable for the mass manufacture of parts and is inapplicable in small-batch production.
Applications of Zinc Die Cast Parts
Zinc die casts parts are used in various industries, including:
Automotive Industry
Due to their incredible strength and hardness, complex geometric features, good surface quality, high dimensional tolerance, and corrosion resistance, zinc die-cast components are applied in the automotive industry for the manufacture of:
- Rearview mirrors
- Enclosures
- Chassis parts
- User and car safety components like pulleys and gears
- Transmission components
- Sunroof, windshield wipers
- Brackets
- Bearings
- Steering
- Brake parts
Above are just some of the automotive components manufactured from die casting.
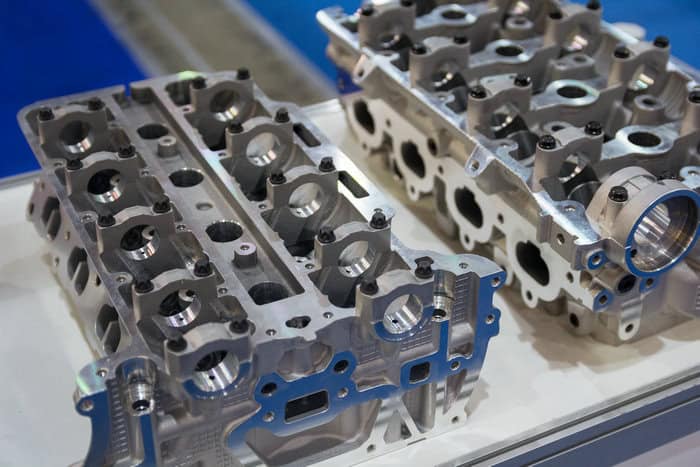
Electronics
Zinc die casting has numerous benefits in electronic applications. One of its significant properties is its ability to be cast into thinner walls and complicated shapes. As explained above, zinc alloys are hardier than other die-casting metals.
Aside from that, zinc alloy has excellent electromagnetic shielding and vibrational dampening suitable for safeguarding internal electrical components.
Home Appliances
Zinc die-casting is among the best die-casting metals for home appliances. Due to its good surface finishing, dimensional stability, and strength, zinc casting is used to manufacture home appliances like door locks, blenders, belts, hand mixers, shoe buckles, handles, key chains, etc.
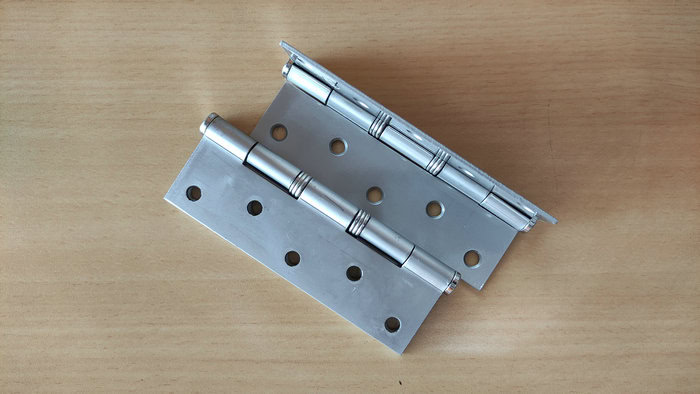
Mechanical Sector
Another significant application of zinc die casting is in the mechanical sector. Casted zinc parts are used in manufacturing engine parts in this sector.
Conclusion
Zinc alloy casting is among the most popular casting methods. It offers several advantages over other metal castings, including easy and direct injection. However, before starting your casting process, it’s vital to understand the various procedures, alloys, applications, and benefits and drawbacks.
For better outcomes, consider enlisting the help of reliable experts like Moldie. We offer high-quality custom zinc die-casting services at affordable prices.
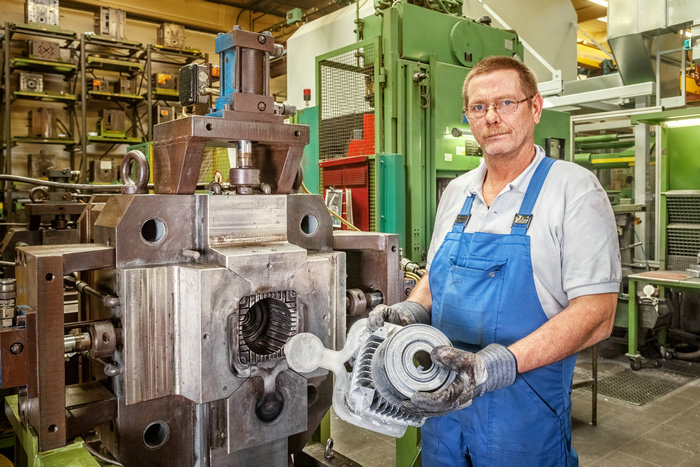
FAQs
How Strong Are Zinc Die Casts?
Zinc die casts are very strong. They provide higher tensile strength than the most popular non-ferrous alloys used in die casting. For instance, zinc die-casting alloys have about 2.5 times more strength than aluminum.
Will Zinc Die Cast Rust?
No. Zinc die castings have high corrosion resistance. When exposed to air and moisture, zinc will react with oxygen to form a thin layer of oxide, which then reacts with moisture to form zinc hydroxide. For this reason, zinc die-cast parts won’t rust even if used in corrosive environments.
However, when the zinc surface hasn’t fully developed a protective layer, it displays a corrosion called white rust. This occurs when there’s insufficient oxygen over the zinc surface; thus, the white rust is powdery.
Can Zinc Die Cast Be Welded?
No. It can be challenging to weld zinc die cast because of its low melting point. But, if you use materials like Super Alloy 1, you can solder the die-cast part.