Injection molding, also known as plastic injection molding, refers to large production volumes of plastic parts. Typically, it’s used in mass production processes of identical items. The molding process occurs when molten materials are injected into a mold.
Mold customization, which gives the parts various shapes, occurs during tooling. Customization allows you to create as many parts as you want in equal dimensions and shapes. This includes complex molds and designs that only allow for low dimensional tolerance.
If you want to start plastic molding, you must learn the injection mold cost and how to reduce it before starting the molding process. Luckily, this article has you covered. It discusses the plastic injection molding costs and the various factors influencing them, helping you evaluate the average production molding costs.
How does injection molding work?
The molding process is quite simple. You start by creating the mold tool. You can build it from metals like steel and aluminum. However, you should only use an aluminum mold when producing plastics of narrow tolerance.
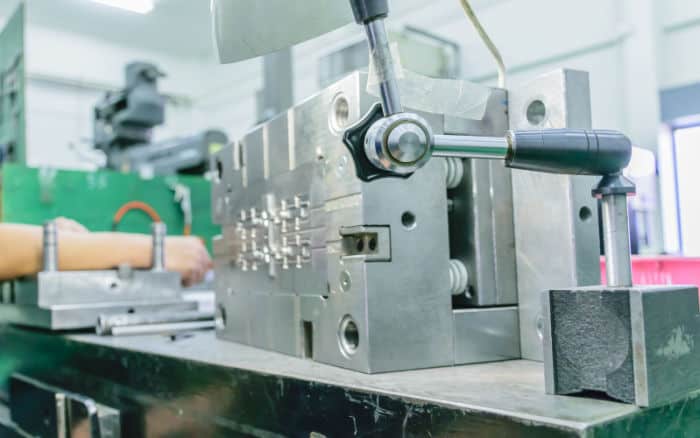
Also, it’s not the best option for producing parts in high volume because they wear out quickly and have substandard mechanical properties. Steel molds are the best option for high-production volume because they’re durable with better mechanical properties.
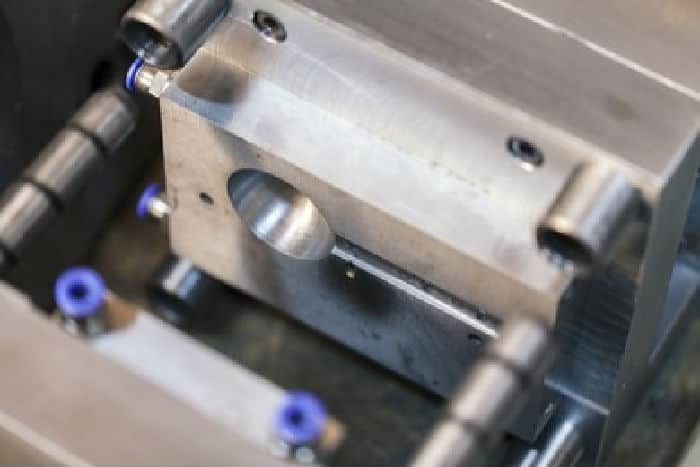
The next thing is to feed the materials you’re going to use into a heated battle and mix. Once the materials melt, inject them into an enclosed metal mold tool. When the molten plastic cools, it takes the shape of the molding tool. You can use an external temperature controller that circulates oil or water to reduce the cooling time of the molten parts.
Mount the mold tools onto the platens (plate mold) once the plastic molds solidify, allowing ejector pins to eject the plastic parts. The next step is to separate the materials and combine them in a two-shot mold (a type of plastic injection molding) to soften the touch of the plastic injection mold, produce them with varying performance characteristics, and even add colors.
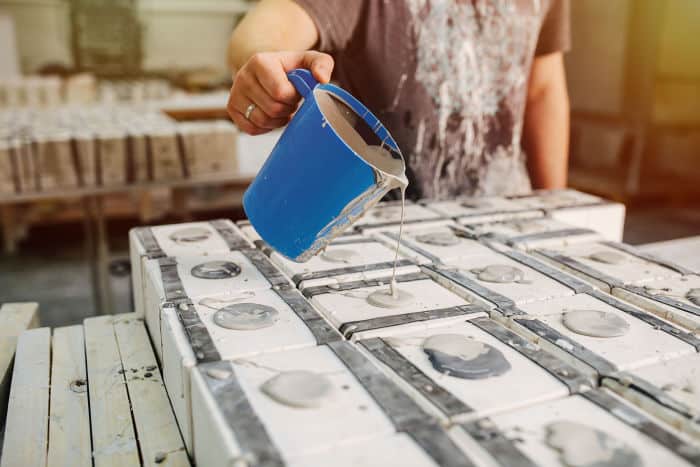
You can either make a one-cavity mold or multiple cavities. When using multi-cavity molds, you can choose to create identical or unique parts in all the cavities. However, single and multi-cavity molds require careful design and quality materials.
That said, here are a few considerations for your injection molding project:
- Finances: If you’re planning to start manufacturing injection molding, you should be well-prepared in terms of finances. The entry cost of the injection molding process can be ridiculously high because you’ll have to purchase the molds and machinery.
- Production volume: Another important factor you should consider before starting mold production is the number of parts you want to manufacture. This will help you determine whether or not injection molding will be cost-effective.
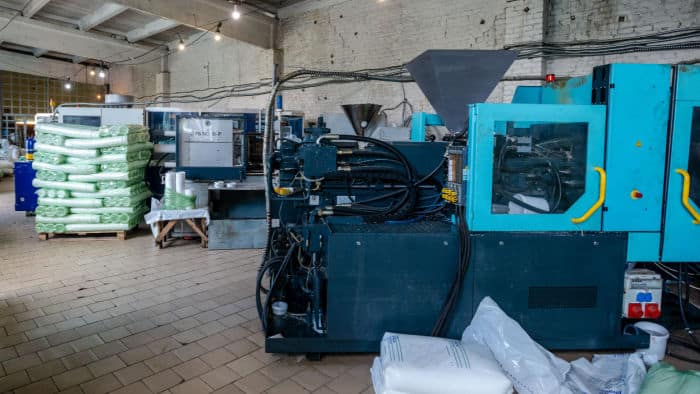
- Design factors: The designs of the parts you intend to manufacture will make your injection molding process easier or more challenging. Simple geometry simplifies the injection molding process. A good design will minimize damages and defects during production.
- Production considerations: You must also consider the overall time it’ll take to produce the parts. Minimizing time aids production. You should therefore consider using well-thought-out tooling and hot-running machine molds to reduce the machine cycle.
Factors that influence the injection molding costs
Injection molding cost vary from one plastic injection molding to another, depending on type, shape, and mold size. The various factors that influence molding cost include the following:
Equipment costs
The equipment you need for your project will greatly affect the cost of injection molding. There are small-scale injection machines you could purchase for your start-up. They’re less expensive and will fit right into your setup costs.
Larger equipment is better for large-scale manufacturing of injection molding. If you’re shipping the equipment from abroad, the injection mold costs will increase due to shipping charges.
If you’re in no position to bear the injection mold costs, you can outsource it to third-party experts with high-end injection molding capabilities.
Tooling costs
Another factor that’ll greatly influence is the tooling costs. Unlike the equipment, producing molds is not a one-time investment. You have to keep building new mold base from time to time which increases the tooling and the mold cost.
The tooling costs vary from process to process. Examples of these processes include:
3D printing: It’s among the fastest and cost-effective methods you could use to create injection molded parts for injection molding.
It’s considered a cheaper means of creating molds because all you need to create your mold is a 3D printer. Also, you don’t need to hire especial expertise, reducing the total cost of injection molding.
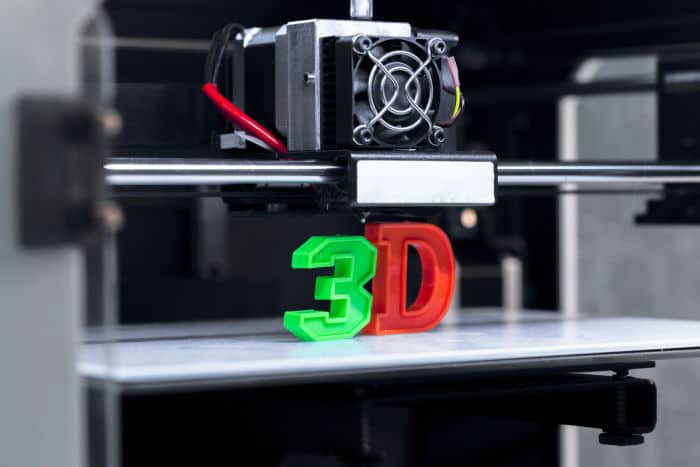
CNC machining: CNC machining is used when constructing metal molds. The method is effective and produces quality molds However, CNC machines have shorter lifespan, meaning you’ll have to purchase new ones from time to time thus increasing the injection mold cost.
Electrical discharge machining: You can use EDM to create complex molds. It bends metal to the wanted shape through heating. EDM is very accurate but can only be used on metals.
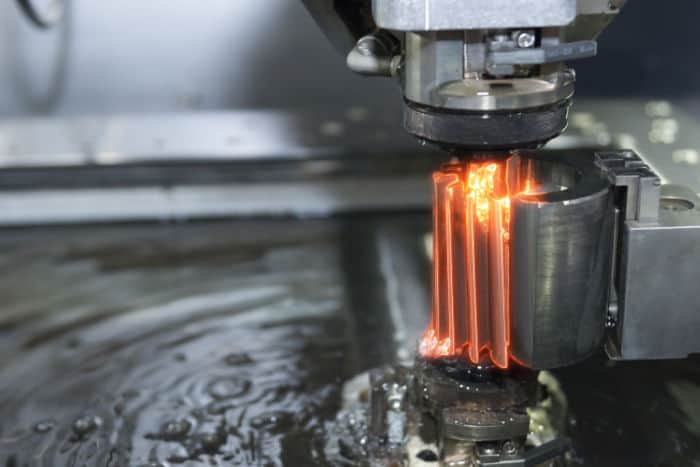
Complexity
Another factor that determines the injection molding cost is the design aesthetics and complexity. Designs that are more complex will results to higher plastic injection molds cost.
Plastic resin
The plastic resin you use for injection molding will also determine whether or not you’ll have low-cost injection molding. The more you need, the higher the total cost of injection molding process. Less resins lower the cost of the mold.
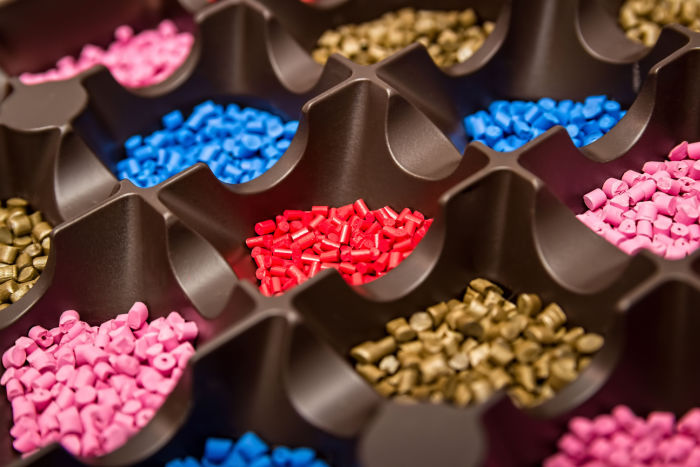
Labor costs
Although most processes are automated, you’ll still incur setup costs, operation, and repair which increases the total injection mold cost.
Injected material cost
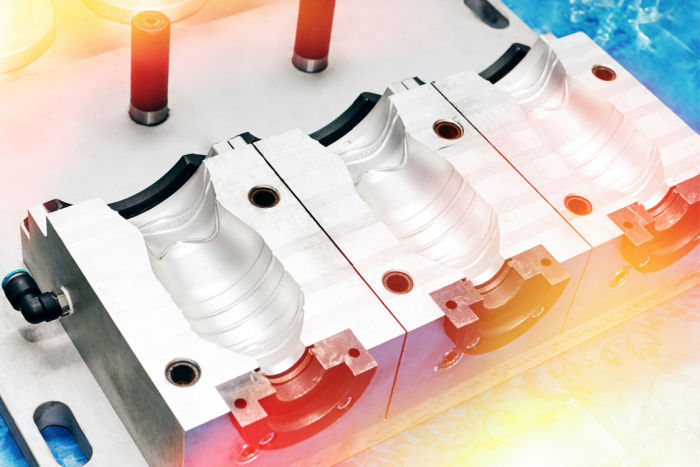
Other factors
Other factors that’ll affect the total cost of the injection molding cycle include the following:
- Secondary services
- Product features
- Production volume
How to reduce injection molding costs
Injection molding can be very expensive. To manage the costs, you need to understand how you can reduce molding costs. Some of the ways to reduce these costs include the following:
- Reusing molds
- Using insert molding technology
- Avoiding unnecessary features
- Simplifying the designs of the parts
- Making use of multi-cavity and family molds
Classification of plastic injection molds
Selecting the best plastic injection mold is crucial because it’ll affect the overall production costs of the injection molding, speed, and quality of the outputs. The injection molds are categorized based on various attributes. They include the following:
Based on the mold plate
Plates are used in the mold cavities to ensure satisfactory outputs. You can identify the different types of molds based on the number of mold plates. Injection molds identifiable with the number of plates include the following:
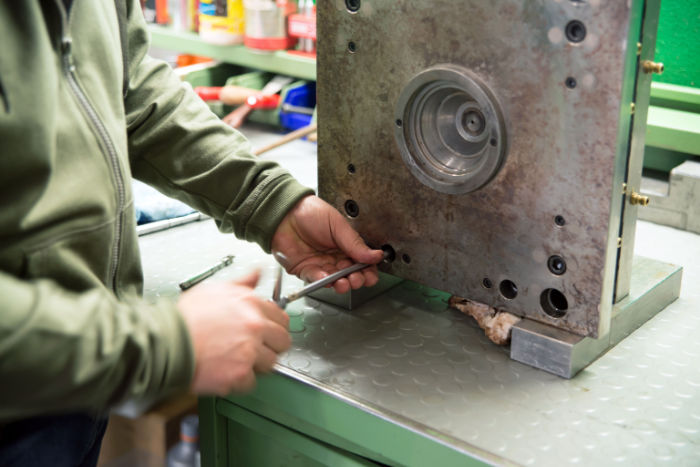
Stack injection mold
The stack injection mold cost is higher than the two-plate and three-plate injection molds. However, the overall operational cost is less because it has several parallel plates to make the process more efficient with fewer defects. The best part about it is that it only needs a few clamp tonnages per cycle.
Three-plate injection mold
It has a third plate called the stripper plate. Unlike the two-plate, it has two parting lines between the core and cavity plates. The parting lines separate the molded part and the running system. It’s not as common as a two-plate injection mold but is faster and more efficient as the runner system doesn’t require recycling or manual separation.
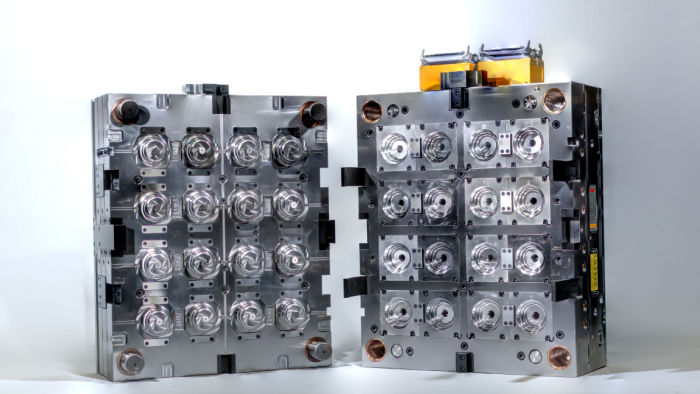
Two-plate injection mold
It’s the most common type of injection mold in this classification because of its affordable tooling cost. It has one parting line that connects the cavity plate and core plate. You can use this mold with all runner systems, but it’s more compatible with single-cavity molds.
Based on the number of mold cavities
Another factor that identifies the different types of plastic injection molds is the number of parts they produce per cycle. They include the following:
Single cavity mold
This type of cavity mold produces a single part because they only have one cavity inside. They are the cheapest compared to multi-cavity and family molds but have lower production rates which result in higher plastic injection molding cost.
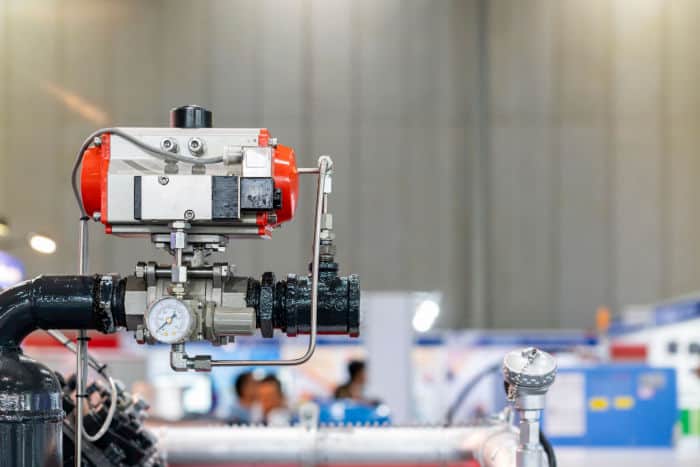
Multi-cavity molds
It has multiple cavities, which allows them to produce several parts simultaneously. The production rate of these molds is higher than the single-cavity mold making it more cost-effective. If you’re producing larger plastic components, you should consider purchasing an injection mold with multiple cavities.
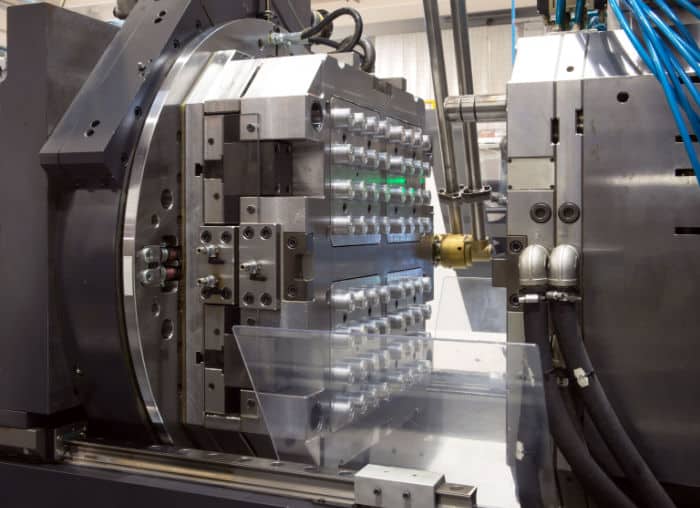
Family molds
Like multi-cavity injection molds, family molds have several cavities. However, the cavities aren’t identical, meaning you can only use them to produce parts that vary in shape and size.
For instance, you can use it to manufacture plastic containers and their lids in a single molding cycle. Using this type of mold activation will be more expensive because of the mold cost, but it’ll improve production quantity and reduce the overall operating costs.
Based on the feeding system
There are three types of injection molds under this category. It differentiates the molds with their feeding and runner systems. The feeding system is a series of channels, such as sprues, gates, and runners, directing molten plats to the cavities. The molds under this category include the following:
Hot runner injection molds
These are molds that are heated with rods or coils internally or externally. The molds are permanently encased in a stationary manifold plate, which prevents them from ejecting with the plastic components.
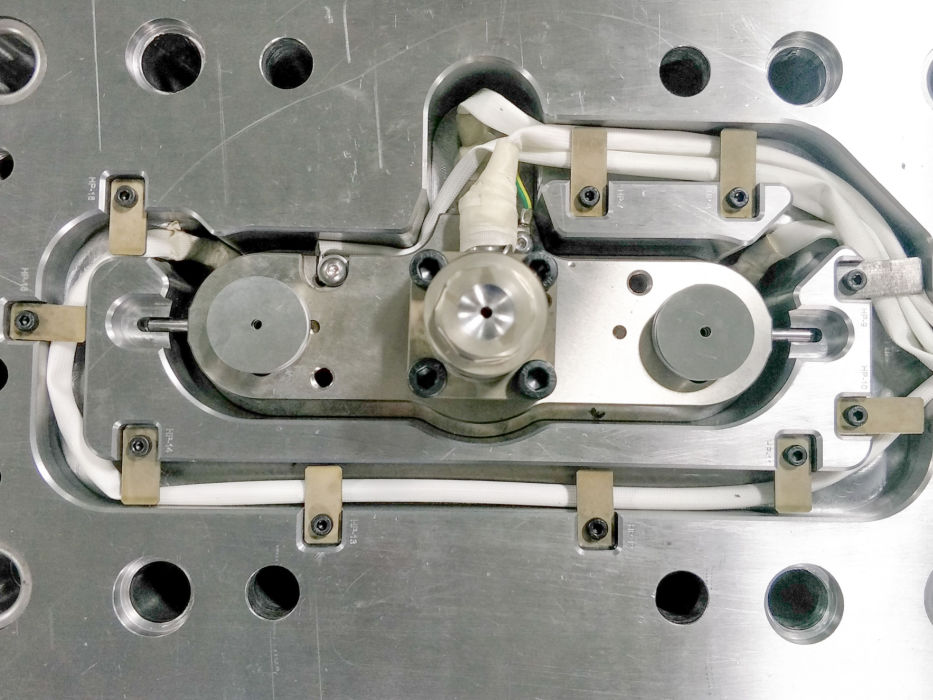
The hot runner injection molding process creates efficiency and reduces waste. Also, no regrinding is required or any additional processes to remove runners. If you intend to produce large volumes quickly, hot runner molds combined with multi-cavity are the best injection mold tooling.
However, hot runner injections mold also have their disadvantages. For one, it’s the cost of the mold is relatively high. It also requires high maintenance and upkeep, and you’ll have to hire a trained professional to monitor the plastic injection molding process.
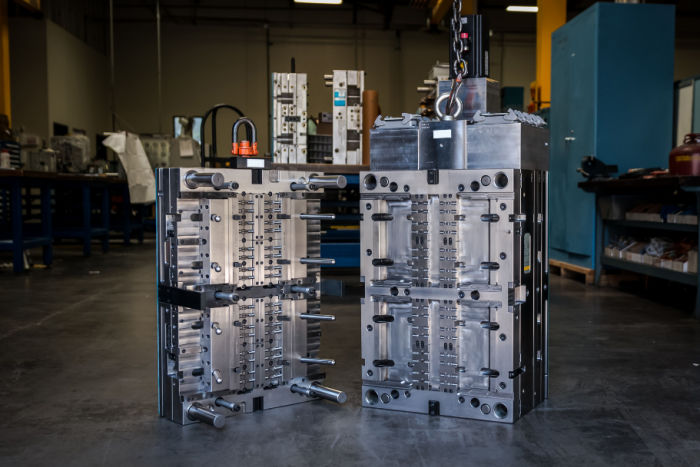
As mentioned, the molds are hidden in manifold plates. This makes it challenging to clean, meaning you won’t be able to get rid of any plastic residue or leftovers from the previous processes. You may want to consider using a different feeding system if you want to manufacture colored containers.
Another disadvantage of using a hot runner system is that the containers might stick to the cavities. Therefore, you may want to consider using this system when dealing with materials that aren’t sensitive to heat.
Cold runner injection molds
This system uses unheated runners to direct molten parts into the cavity. This means you can use them even when working with heat-sensitive materials. The injection molding in this system is naked, meaning you know whenever it needs cleaning.
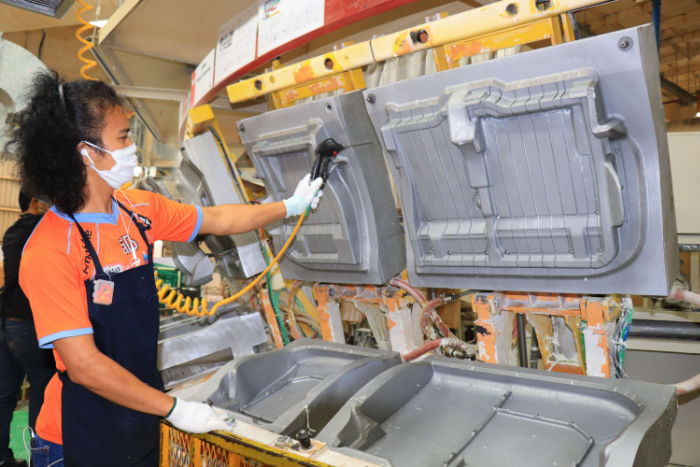
They’re also easy to maintain and are less costly. The better about it is that you can easily change colors and the materials you’re using in production. Also, it’s pretty simple to add design alterations because of its runner positions and fast-changing gates.
The disadvantage of using a cold runner injection molding system is that you’ll have to prepare a new runner system whenever you start a new cycle because you’ll cut into the mold when ejecting components. Also, you may have to separate the runner system and the molded part.
Another disadvantage is that they produce wastes in large quantities, meaning you’ll need additional; processes to regrind and remove runners, which may affect the final outcome.
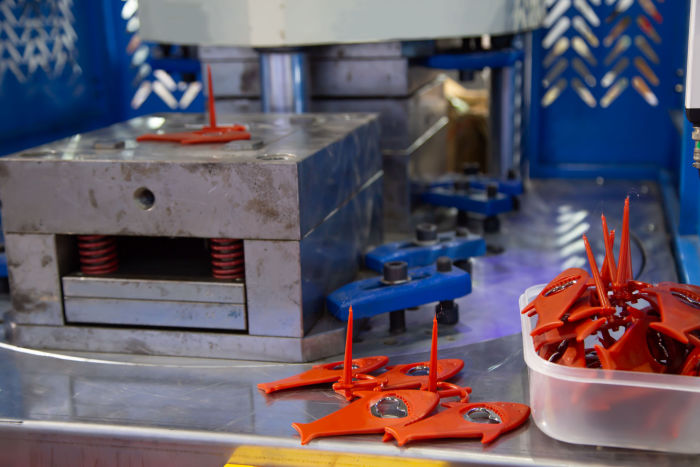
Insulated runner injection molds
Insulated runner injection molding uses the same ideas as cold runner injection molding. However, the end effects are similar to hot runner injection molding. These injection molds use the same idea as cold runner mold but use cartridge heaters to create layers. The layers formed surrounds the molten plastic, forming insulated culls.
They are the best alternatives for hot runners because they’re less costly, and you don’t need to monitor their temperatures. It also allows for fast-material change and colors. However, you can only use it for engineering-grade plastics.
Conclusion
The injection molding process is among the most used processes in the manufacturing industry. It’s cost-effective when manufacturing high volumes of parts and you should consider it if you plan on starting a plastic manufacturing company.