Plastic injection molding continues to advance with the emergence of new technology. With the rapid advancement of the industry, there are new opportunities for the parts being manufactured in the automotive industry.
Worldwide, industries continue to work with a greater percentage of plastic injection molding parts in every round of vehicle designs. Luckily plastic injection molding can accommodate the demand.
Injection molding offers a viable solution for producing high-quality and high-volume automotive parts from various polymers. The automotive industry prides itself on the safety, consistency, and quality of its parts, and plastic injection molding is important in achieving these qualities.
This article will give you insight into the various aspects of automotive plastic injection molding discussed below.
Why injection molding is used for automotive applications
Plastic injection molding is among the common methods used to produce plastic components. Although automobiles are traditionally related to steel and other metals, plastic has become part of the integral products used in creating trucks, cars, and other vehicles worldwide.
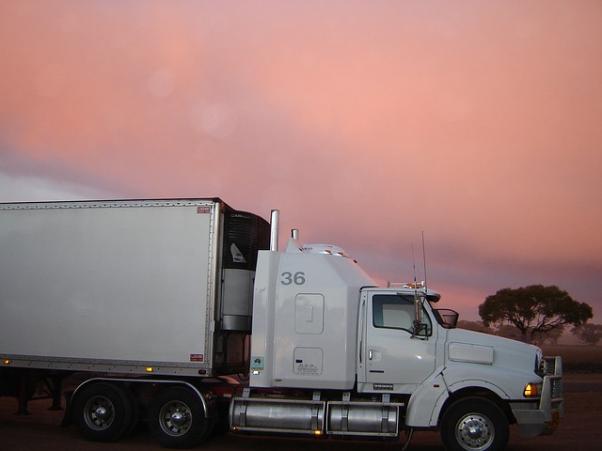
There are various reasons why plastic injection molding has become popular in the automotive industry. Plastic is more durable than some metals in some cases, and it’s sturdier.
Also, today users have different expectations of the comfort and fuel efficiency of their cars. These expectations are met more effectively by injection molded parts than metal parts.
The history of automotive plastic injection molding
The art of plastic injection molding dates back to 1872, when the first machine was invented and patented. This marked the start of plastics in the manufacturing industry.
Traditionally the automotive industry cars were almost fully made from metal, which made them extremely heavy and clunky. However, the eruptions of plastics in the 1940s redefined the industry. Automotive began experimenting with the production of plastic car parts.
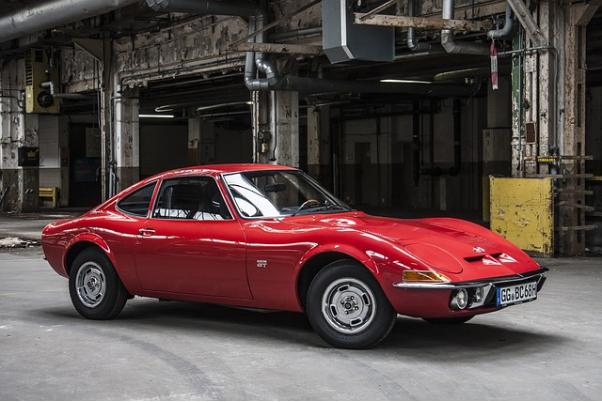
The first car with plastic used for decorative elements was rolled out in 1970s. Later, in the 80s, more functional parts such as bumpers, fenders, and headlights were introduced to the automotive industry.
In 2000s, the automotive industry unveiled the first plastic structural components for cars. Their main advantage was that they were more lightweight than metal ones, cheaper to produce, and had improved fuel efficiency.
Today, plastic injection molding is a dominant production method in the automotive industry for plastic car parts. Plastic has great design flexibility, and it’s used on various items you can find in your car, like mirror housing, door panels, bumpers, dashboards, and cup holders.
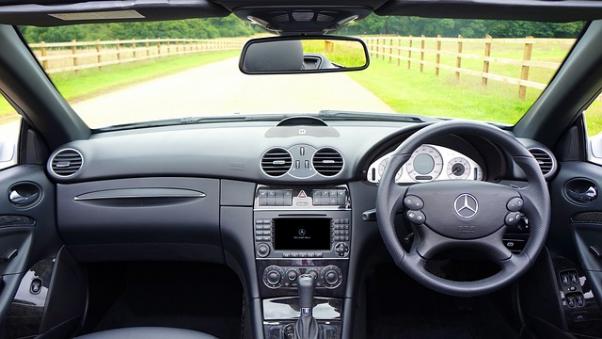
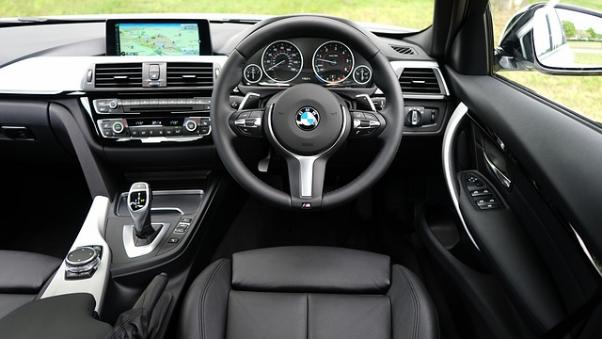
Benefits of injection molding in automotive applications
Today plastic injection molding has set root in industries and has become an established production process. The car industry uses injection molding, where molten plastic is injected into a mold cavity to make parts.
Once the melted plastic is injected into the mold, it cools and hardens to make the finished automotive parts. Automotive plastic injection molding is challenging and critical, but when done well, it’s a reliable method for producing high-quality plastic parts that are solid.
The following are the reasons why the process is of benefit to automotive parts production:
- Sale and cost
Due to the price of the mold, the price of injection molding can be very high. However, it’s a highly scalable process that has its overall cost decrease as the manufacturer makes more automotive parts.
When used for mass production, injection molding becomes highly beneficial to the manufacturer. The cost of injection molding tooling can curb the cost efficiency of injection molding in any production that isn’t mass production.
- Color options
The auto industry makes vehicles based on user needs, including color preferences. In automotive plastic injection molding, it’s easy to modify the colors molded to fit the color schemes of the vehicles.
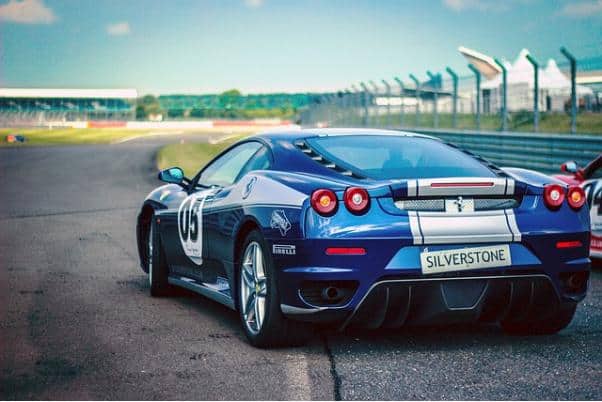
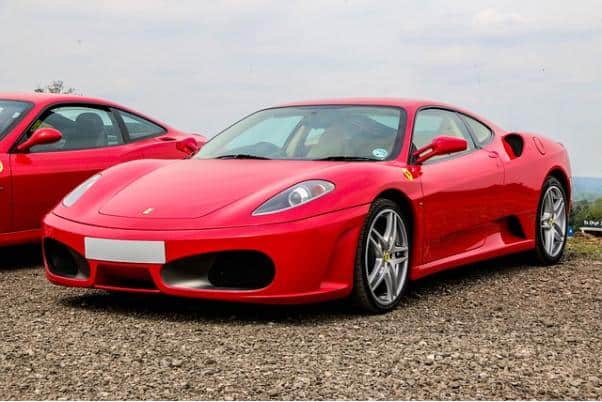
Injection molding allows you to mix dyes with raw material pellets before manufacturing begins. This process produces a solid, consistent coloration, and there’s no need for painting or tinting once the molding is completed.
- Repeatability
The ability to produce consistent parts in the automotive industry is essential. When cars are modeled, they should be similar and repeatable procedures are highly welcome.
Automotive plastic injection molding relies on huge metal molds, and the final molded plastic part is identical each time.
Although some factors come into play with the injection molding process, it’s highly repeatable if the mold has great finishing and design.
- Material availability
Injection molding benefits the auto industry because the process is compatible with a vast range of flexible, rigid, or rubber plastics.
Automotive manufacturers use different polymers for different applications in the auto industry. These polymers include acrylic, polycarbonate, nylon, and more.
- Quik prototypes with rapid tooling
Injection molding in the automotive industry is not only used for the mass production of automotive parts but also as a prototyping tool. Automotive mold manufacturers can manufacture prototyped molded car parts faster than traditional steel tools by creating low-cost, fast aluminum molds using rapid tooling.
- High precision and great surface finish
Automobiles need a high-quality surface finish to sell well in the market. Injection molding is an ideal choice for producing plastic parts that have simple geometry and need a high-quality surface finish.
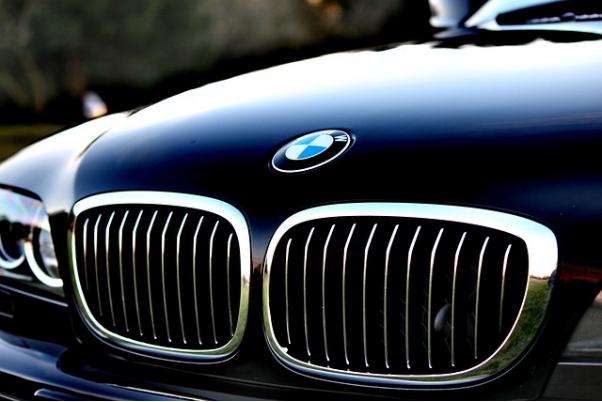
Various options can be used on the surface finishing of a product, like matte, glossy and rough. This finishing can be applied directly to the mold and not the molded part for a more uniform and quality look. Remember, various plastic materials have a different final surface finish.
Application of injection molding in automobile production
Injection molding is a predominant method in the automobile sector to manufacture plastic automotive parts. The parts range from the small pins to the large body panels of the car. Some of the main car parts produced by injection molding include the following:
Exterior components
Injection molding isis used in the manufacture of various exterior automotive parts. The exterior parts include:
- Splash guards
- Grilles
- Floor rails
- Fenders
- Bumpers
- Doors
- Tail lights
- A/C condensers
- Hoods
- Nose panels
- Header
- Mirrors
- Radiator supports
- Light housings
- Door handles
- Headlight covers
From the list, splash guards are a clear depiction of the durability of molded auto parts.
Components under the hood
Most of the under-the-hood components were made from metal parts. However, today, most automotive manufacturers have moved to plastic. The polymers used for these auto parts are nylon, PET, and ABS.
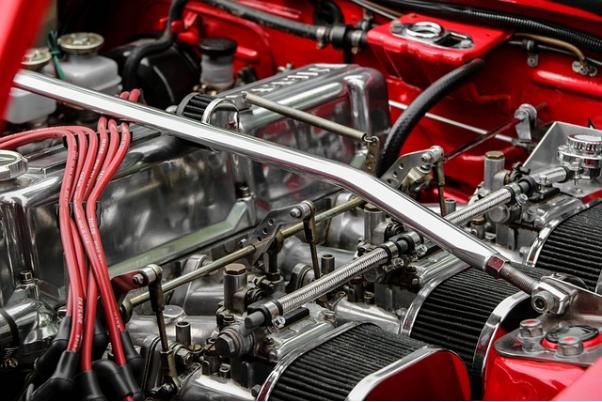
However, parts like the oil pans and cylinder head covers are made from injection molding. The method offers lower costs and weight compared to the traditional components. Some of the plastic components under the hood include:
- Engine tubes and hoses
- Air intake manifolds
- Engine cooling shutters
- Crankshaft
Interior parts
Automotive manufacturers also produce interior parts using the injection molding processes. These components include:
- Interior surfaces
- Glove compartments
- Internal door handles
- Interior surfaces
- Air vents
- Dashboard faceplates
Also, plastic is used in producing decorative plastic elements.
Injection molding alternatives for low-cost automotive prototypes
Molded plastics serve as an alternative to metals. Today, injection molding is the most preferred in producing auto parts like seat belt modules, brackets, and airbags.
Also, manufacturers can replace molded plastic parts with 3D-printed parts. Hence, injection molding is not only used for the mass production of parts but also as a prototyping tool.
Materials used in injection molding for automotive parts
For automobiles to be considered roadworthy, manufacturers have to build the cars based on various rigorous safety standards and meet various certifications.
Therefore, it’s important that the right plastics are chosen for thermoplastic injection molding. The following are a few of the commonly used ones:
Nylon
Nylon has good chemical and abrasion resistance, but it’s not resistant to liquids. It’s molded to make components like bearings and bushes.
- Reinforced composites
These are the carbon fibers and glass that are used in the reinforcement of plastics to make them stronger than the ordinary resins used in bumpers and car bodywork.
- Acrylonitrile butadiene styrene (ABS)
This is widely used in 3D printing and injection molding. It’s highly durable and fairly resistant to weather changes. It’s used in making auto parts like covers and dashboards
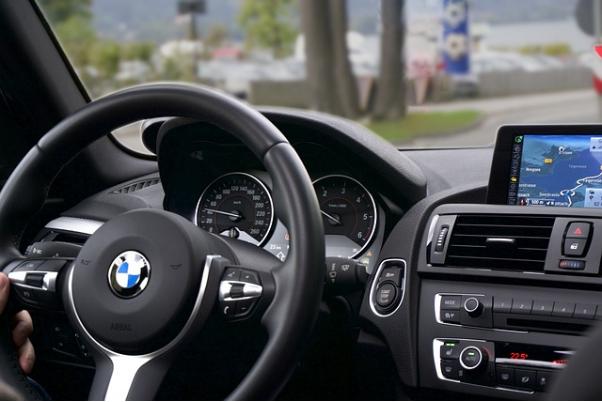
- Polyurethane
It’s often found in spongy and flexible items like foam seating. Its auto applications include gaskets, suspension bushings, insulation panels, and seals.
- Polyvinyl chloride
This is the third most popular plastic polymer in the auto industry and the world. It’s used for auto parts that need high chemical resistance. These include the dashboards, interior panels, and cable insulation.
- Polypropylene
Auto manufacturers use this in producing high-intensity parts and various exterior components. The material has great chemical, water, and UV light resistance. Some of the parts it makes include the battery cover and bumpers.
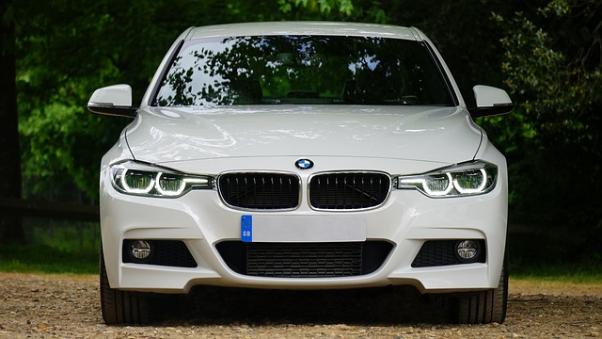
- Polymethyl methacrylate (PMMA)
Acrylic is transparent, making it an excellent choice to substitute glass. It’s perfect for the production of internal screens and headlight covers.
Moldie automotive plastic injection services
Moldie offers you professional injection molding services to produce plastic car parts. Our clients include various industries, including the automobile company.
We work with a wide range of plastic injection materials. This includes heat-resistant, strong, and rigid thermoplastics. Our plastic injection molding services will enable you to get high-quality auto parts that meet all the application requirements.