Concept Of High Pressure Die Casting
High pressure die casting (HPDC) is a metal casting process used for mass production of complex, high-integrity, and near-net-shape metal parts. The process involves injecting molten metal into a pre-designed mold at high pressure, typically between 1000 to 25000 PSI (pounds per square inch). The high pressure is maintained until the molten metal solidifies and is removed from the mold.
This process is carried out using either a hot chamber or cold chamber die casting machine. The hot chamber machine is used for low melting point materials like zinc, while the cold chamber machine is used for high melting point materials like aluminum and magnesium. HPDC is widely used in industries like automotive, aerospace, and medical due to its ability to produce high-quality parts with tight tolerances and complex shapes.
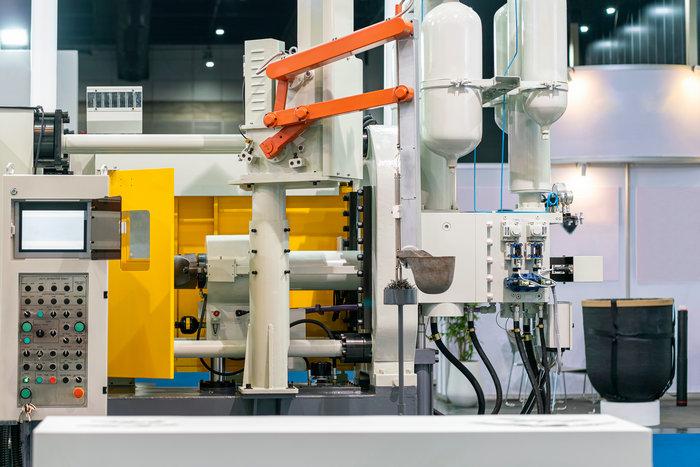
Importance Of High Pressure Die Casting Concept In Various Industries
High pressure die casting (HPDC) is an important concept in various industries due to its numerous benefits. Here are some industries that benefit from the HPDC concept:
Consumer Electronics: Consumer electronics such as smartphones, laptops, and tablets require small, lightweight parts that can be easily manufactured using the HPDC process. This process allows for the production of intricate designs and precise components with high accuracy.
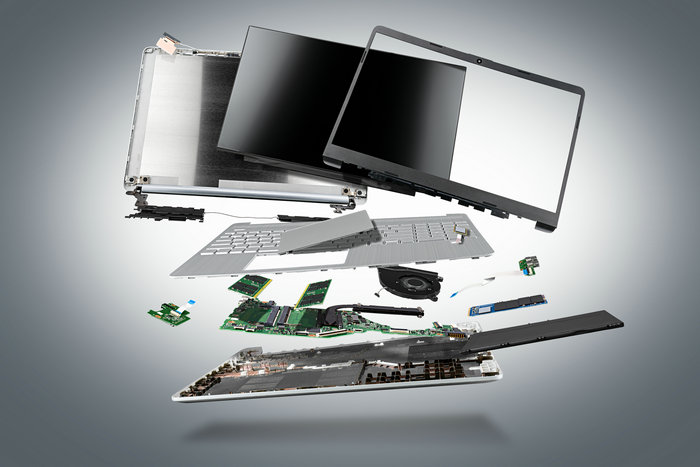
Medical Equipment: The medical industry also benefits from the HPDC concept, which allows for the production of lightweight, precise components for use in medical devices and equipment. The process provides high-quality components with excellent surface finishes, making it ideal for the industry’s stringent requirements.
Defense Industry: HPDC is advantageous in the defense industry by enabling the production of complex, high-strength components with excellent dimensional accuracy, which are crucial for military vehicles, aircraft, and weapons systems. This allows for continued innovation and development to meet the advancing technology requirements of military equipment.Materials Compatible With High Pressure Die Casting
The following brief overview of compatible materials will help you determine whether HPDC is the appropriate manufacturing process or if an alternative method should be used.
Aluminum: This is a widely used material in high pressure die casting due to its inherent properties such as lightweight, dimensional stability, electrical conductivity, corrosion resistance, and thermal resistance.
The material has good flow when melted at high pressure but requires a cold chamber system to produce high-quality castings. Common aluminum alloys used in the process include 380, 390, 412, 443, and 518. This material is commonly used in industries like automotive and aerospace.
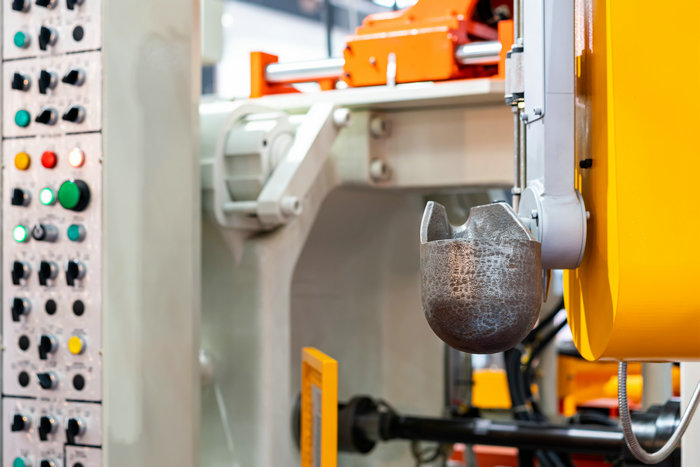
Magnesium: This is another lightweight material commonly used in hpdc process. It has high machinability and is suitable for hot chamber die casting due to its lower melting point. Common magnesium alloys used in the process include AZ91D, AM60, AS41B, and AE42.
Zinc: This is the most manufacturer-friendly material of the three common HPDC materials. It’s suitable for both hot and cold chamber systems. Common high pressure zinc die casting alloys include Zamak, 2, 3, and 5. Zinc die-casted materials are strong, durable, and machinable.
What is Aluminium High Pressure Die Casting
Aluminum high pressure die casting (HPDC) is a metal casting process that involves injecting molten aluminum at high pressure into a pre-designed mold to create high-quality metal parts. The aluminum is pressurized at levels ranging from 1,000 to 25,000 PSI to fill the mold cavity and replicate the shape of the desired part. It’s carried out using either a hot or cold chamber die casting machine, depending on the aluminum alloy’s melting point.
When Should I Choose the HPDC Process?
There are two types of equipment used for high pressure die casting: cold chamber and hot chamber die casting equipment. For high pressure aluminum casting, it is necessary to use the cold chamber machines.
High Pressure Die Casting (HPDC) is a fast and cost-effective manufacturing technique suitable for casting non-ferrous metals. It is ideal for high production demands and can produce thin-walled parts with a better surface finish quality. However, there is a risk of porosity inside the casting, which can compromise the structural integrity and make it unsuitable for heat treatment.
Components Of A High Pressure Die Casting Machine
If a manufacturer intends to acquire an HPDC machine, here are some components of the machine and their respective functions.
Die Cast Mold
It’s the main component of the machine, usually made of steel. It has a design that represents the intended product, and it’s responsible for shaping the molten metal into the desired form. The die cast mold has two halves, a movable and a fixed half, that clamp under force when the operator injects molten metal.
Ejector Pins
These are components that help in the ejection of the die-cast after solidification. They are mostly located on the movable die half and aid in removing the cast parts from the mold.
Piston
It produces the pressure that injects the molten metal from the blow chamber into the mold. Depending on the type of machine, it can be automated.
Heating Components
These consist of the heating element, thermocouple, and blow chamber (location of the molten metal). They function to heat the metal while storing and maintaining the temperature of the molten metal. The heating components are absent in the cold chamber system.
Riser Tube: This serves as a passageway for the molten metal into the die-cast mold.
High Pressure Die Casting Process Steps
The following information provides a comprehensive understanding of how the high pressure die casting processes works:
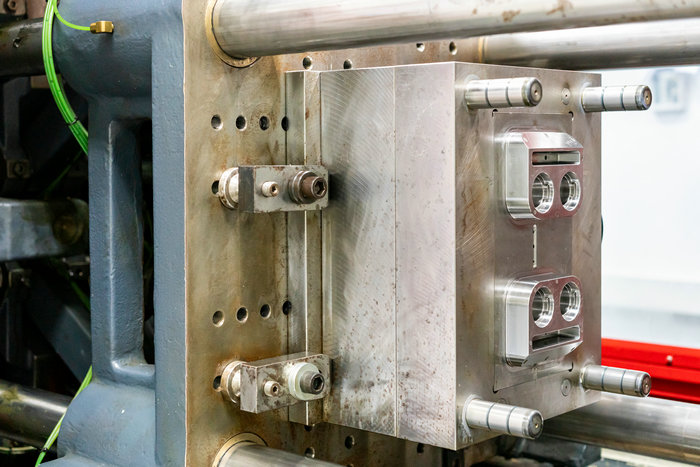
The first step is mold preparation: It involves cleaning the mold and lubricating its interior walls for easier ejection and temperature regulation.
The second step is injection: It can be done using either the hot chamber or cold chamber injection system, depending on the type of material used. The hot chamber system is suitable for low melting point metals like zinc and magnesium, while the cold chamber is used for high melting point metals like aluminum and brass.
The third step is part removal: It involves using an ejector pin to release the mold’s cavity and push out the solidified casts.
The final step is trimming: It involves removing the extra materials found on the casting and the mold using various methods, such as a trim die or saw.
Advantages And Limitations Of High Pressure Die Castings
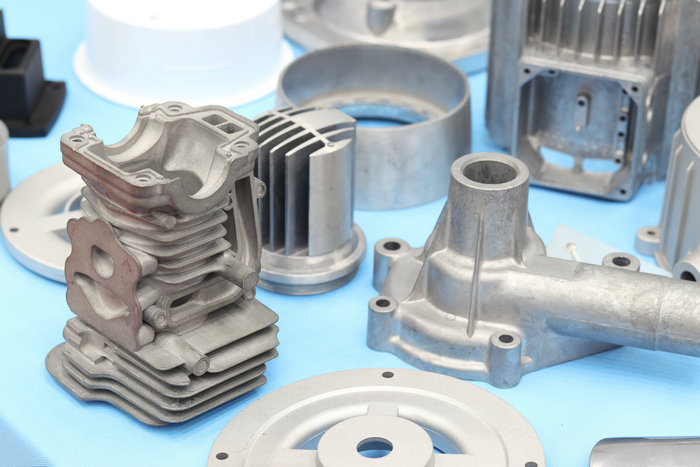
Advantages
Higher Production Rates
The injection stage in HPDC is a vital step and is completed quickly, resulting in high production rates. This makes the process beneficial for rapid prototyping, particularly for high-volume manufacturing, and faster compared to other casting methods such as LPDC.
Quality High Pressure Die Castings
Die cast parts produced using HPDC have high dimensional accuracy, excellent uniformity, and good surface finish. They also retain the mechanical properties of the parent material and usually require minimal machining.
Thin Wall Products
HPDC can achieve a thin wall thickness of less than 0.40mm, and the process allows for the addition of inserts or co-cast parts. This feature reduces the number of components required during assembly.
Complex Design Achievements
HPDC is suitable for creating products with intricate die shapes due to the flexibility in die mold design. This flexibility makes it easier to assemble the produced parts.
Durable Dies
The die cast molds utilized in HPDC are highly durable, enabling their use in multiple production cycles. This durability reduces the die casting per unit cost.
Limitations
Presence of air
This is a common issue in HPDC, resulting in air pockets in the final product. This makes HPDC unsuitable for products that require airtightness, as air entrapment can cause porosity and surface blisters when heat-treated. In such cases, low-pressure die casting may be a better alternative.
The initial startup costs
The startup costs of a personal HPDC machine can be significant, which is why many individuals and businesses opt to outsource their die casting needs to a service provider.
Minimizing Die Defects in HPDC
Below are some of the most prevalent types of defects and how to minimize them:
Porosity
This is a common issue encountered during the HPDC process. Although it is challenging to eliminate porosity entirely, you can minimize it by incorporating vacuum technology into the equipment.
Flash
Flash is another common occurrence in high-pressure aluminum casting, which is the excess material that leaks along the parting lines. This is usually caused when the injection pressure surpasses the clamping force. One way to prevent flash defects is to use die casting equipment with enough tonnage.
Hot tearing
This can result from non-uniform cooling and may cause tearing in hot spots of your parts. Non-uniform cooling often arises due to variation of wall thickness in a casting, but it can be addressed by improving the design.
Unfilled sections
Unfilled sections in the die cavity can occur due to various factors. This issue can be prevented by monitoring the shot volume, speed, and pouring temperature.
Application Of The High Pressure Die Casting Process
Medical Industry: In the medical industry, HPDC is commonly used to manufacture high-production imaging equipment, infusion pumps, and other medical parts. The process’s high productivity, compatibility with various materials, and ability to produce intricate designs make it a popular choice in this industry.
Automotive Industry: The automotive industry relies on HPDC to manufacture crucial vehicular components such as engine blocks, engine mounts, gearbox casings, and other structural parts. The method’s compatibility with materials like aluminum and magnesium, its ability to achieve high accuracy, and its capability of producing complex designs make it a preferred choice in this sector.
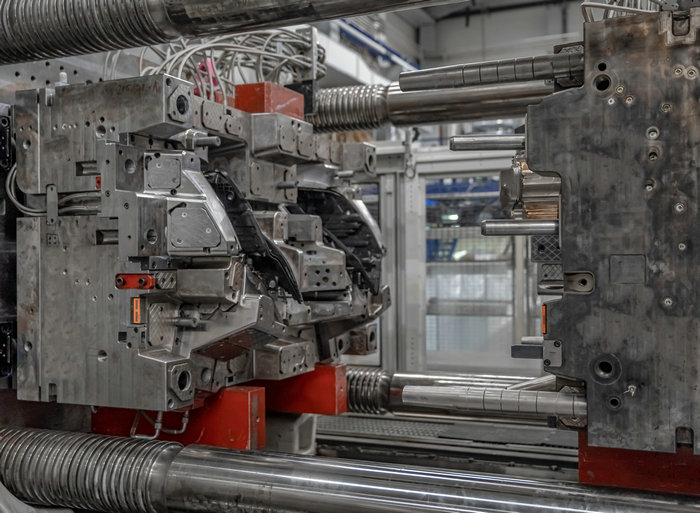
Aerospace Industry: The aerospace sector also employs HPDC to manufacture engine parts using materials like zinc, magnesium, and aluminum. These metals possess unique properties that make them suitable for high pressure die casting, and the method’s ability to produce complex designs makes it an ideal option for the aerospace industry.
Comparison Between HPDC and LPDC
A. High pressure aluminum die casting
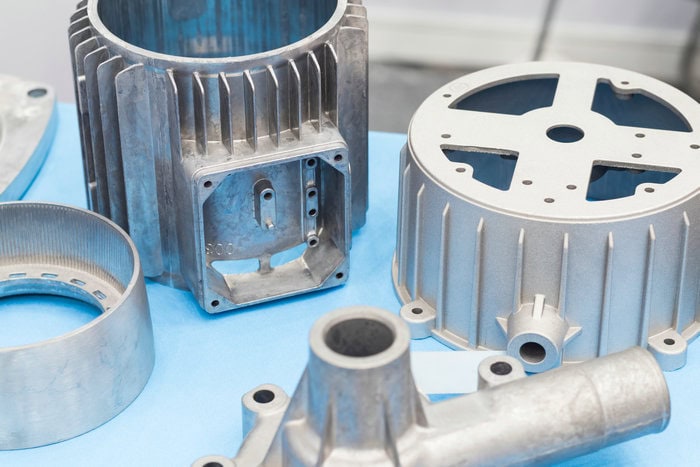
High pressure aluminum die casting (HPDC) is a widely utilized manufacturing process worldwide, with approximately 70% of die casting manufacturers utilizing this process. The steps involved in the aluminium die casting process are as follows:
Firstly, aluminum alloys are melted in a separate furnace. Next, the molten aluminum is transferred into the shot sleeve of the die casting equipment, either manually or by a robot arm. Then, the molten metal is pushed into the mold by a piston at high pressure. The casting is left to cool and solidify inside the dies for a specific period before the die halves are separated, and the finished casting is retrieved.
B. Low pressure die casting
Low pressure aluminum casting machines have a different structure compared to high pressure aluminum casting equipment, and the process of low pressure die casting is described below:
First, the aluminum alloy is melted in a furnace that is sealed off. The die halves are positioned on top of the furnace and connected using a riser tube. Then, low air pressure is applied from within the furnace, causing the molten aluminum to rise through the tube and fill the die cavity. The air pressure is maintained until the casting has solidified. Finally, the dies are opened, and the casting is retrieved.
C. When to choose HPDC or LPDC process
Choosing between high pressure die casting (HPDC) and low pressure die casting (LPDC) depends on various factors such as the complexity of the part design, the desired production volume, the material properties required, and the cost considerations.
HPDC is preferred for complex parts with thin walls and intricate details, as it allows for intricate die mold design flexibility. It’s also ideal for high-volume production runs since it is a fast process with high production rates. HPDC produces parts with high dimensional accuracy, good surface finish, and excellent uniformity. However, HPDC may not be suitable for parts that cannot have air pockets or defects.
LPDC, on the other hand, is suitable for producing parts with thicker walls and less complexity. It is ideal for parts with high mechanical properties and those that require heat treatment, such as engine components. LPDC can also produce parts with fewer defects and less porosity. However, LPDC may not be as fast as HPDC and may not be suitable for high-volume production runs.
Frequently Asked Questions (FAQ)
Why use CNC machining for die casting mold?
CNC machining is a widely preferred manufacturing process for die casting molds due to its precision, accuracy, and ability to achieve high tolerances. Since die casting molds require high levels of detail, CNC machining is the preferred process for manufacturing them.
High pressure die casting: Is it for plastics?
It’s important to note that high pressure die casting is not used for plastics. Injection molding is the preferred process for plastic polymers, while die casting is used for metals.
How do you differentiate between high pressure casting and gravity casting?
The main difference between high pressure casting and gravity casting lies in the method used to fill the mold with molten metal. High pressure casting involves injecting the metal under high pressure, while gravity casting relies on the force of gravity to fill the mold with molten metal.