Aluminum die casting is a mainstay manufacturing process that’s existed since the 19th century. This technique has stayed relevant into the modern-day world, and thanks to advancements in technology, it’s become incredibly sophisticated.
An advantage of this process is that it produces precise metal parts with incredible accuracy and quicker metal parts production. This article looks into the aluminum die-casting process and all essential details you should know about it.
What is the aluminum die casting
Aluminum die casting is a manufacturing technique that involves using a furnace, metal, die casting machine and a die to produce geometrically complex metal parts. Manufacturers use this method to create parts for a wide range of industries, including electronics, automotive, and other consumer products.
Ideally, the process begins by creating a sturdy steel die having precise specifications that define the aluminum metal part being produced.
Manufacturers then heat the die to a high temperature before injecting molten aluminum into its cavity under pressure. After the die cools, the finished aluminum metal can be ready for removal and use.
History of die-casting manufacturing
While die-casting gained popularity through the 19th century, history can trace its inception through the mid-1800s throughout the United States and Europe.
This metal-forming technique became more advanced in the 1920s as manufacturers began producing more symmetrical and complex metal parts. It was in this period that idea of using aluminum alloys became more prevalent in the die casting process.
The key driver to this unperceived adaptation was that alloys had better corrosion resistance, were more flexible, and had high dimensional stability. Besides, they were a low cost option and more durable.
Today, this metal-forming process has become increasingly sophisticated with the use of computer-aided designing (CAD).
Unlike before, prototyping, designing, manufacturing, and testing have become more automated.
Advantages of Aluminum die casting
Aluminum die casting has cemented its place as one of the most preferred metal-forming processes and an ideal alternative to metal stamping. This process offers numerous advantages nearly any industry can find practical, including the following:
- Low-cost raw materials: Aluminum is abundantly available, making it a more accessible raw material. Moreover, it’s highly recyclable, further reducing procurement and production costs.
- Finished products have excellent surface finishing: Unlike other metal forming processes, including progressive die stamping, the aluminum die casting process produces parts having excellent surface finish.
- Die casting machines use precise measurements to produce more precise complex parts. This has become possible due to the use of CAD to create die cast dies has led to the creation of more detailed designs that meet all industry standards.
- High dimensional tolerance in parts: Mostly, metal parts resulting from aluminum die castings have incredibly high dimensional accuracies
- Metal parts have less impurity and porosity: Aluminum die casting involves injecting molten aluminum into an enclosed die under pressure. That eliminates the chances of producing porous and impure parts.
- Ideal for producing parts with complex designs: A significant advantage of using this metal forming process is that aluminum castings can be highly precise. Precision is a valuable feature that only a few metal-forming processes produce, making aluminum die casting more preferred.
- High thickness accuracy: Industries that require strong and durable metal parts can go for metal parts from aluminum die casting. This process allows for precise control of the thickness of parts that need production.
Aluminum die casting has become sought-after for the benefits it offers numerous industries, including automotive, medical, and fabrication. However, limited material options, high initial tools and sometimes, porosity issues still slightly hold it back.
Common Aluminum Die Cast Alloys
As a commonly used raw material, aluminum has numerous alloys fit for various applications. Working with various alloys provides different options that meet various production needs.
This variation in alloy types is due to the unique combination of properties, including ductility, corrosion resistance, strength, and thermal conductivity.
Below are the various typically used aluminum die cast alloys available:
- ADC12: This alloy comprises aluminum as the primary composition, making up 87%. Other element compositions include magnesium and silicon, which comprise 0.5% and 13% of the alloy.
- A380: The most significant variation between A380 and ADC12 is their aluminum amount, amounting to 89.1%. Other dominant elements in the alloy include silicon and magnesium, which comprise about 10% of the alloy. This alloy, like ADC12, has other elements, including iron, copper, and zinc.
- A383: Aluminum makes up 84% of this alloy, and other elements, including copper, magnesium, and silicon, contribute the rest. Other elements in incredibly minute amounts include iron, manganese, and zinc.
- AISi10Mg: Aluminum also dominates the elemental composition in this alloy, making up 92%. Other less dominant elements include silicon and magnesium, contributing to the rest of the alloy volume.
- A413: This alloy, like the rest, has a dominant aluminum volume of between 86% and 89%. It also has silicon, copper, and magnesium as other significant elements and more minute amounts of iron, magnesium, and zinc.
These alloys have different properties that make them suitable for various industrial applications.
Characteristics of Aluminum Die Casting Alloys
Aluminum is a metal sought-after in manufacturing processes due to its remarkable properties. Especially as an alloy, aluminum can be more robust and support numerous industrial applications.
Below are the aluminum die casting alloy characteristics you should know more about:
- Excellent casting properties: Aluminum alloys have incredible dimensional stability, low porosity, and perfect finishing.
- These properties all measure up to the metal requirements to be used in die-casting processes.
- High fluidity: Manufacturers can quickly and efficiently inject molten aluminum alloys easily into die cavities. The metal’s fluidity, therefore, gives it the edge over other types.
- Excellent strength and ductility: A more ductile metal can easily mold into various complex shapes, making aluminum alloys easier to work with. They’re difficult to break or crack as they’re mostly malleable in their solid forms.
- Lightweight: Aluminum alloys are lighter for easy lifting and transfer during the metal forming processes. Industries, including aerospace and automotive, find using aluminum alloys for their components and parts much more applicable than other metals.
- Corrosion resistance: Aluminum can resist corrosion when exposed to harsh environments. That makes them ideal for creating metal components used in aerospace and automotive, where exposure to degrading elements is highly likely.
Other properties, including a low melting point and high thermal conductivity, make aluminum die casting alloys more applicable to the industry.
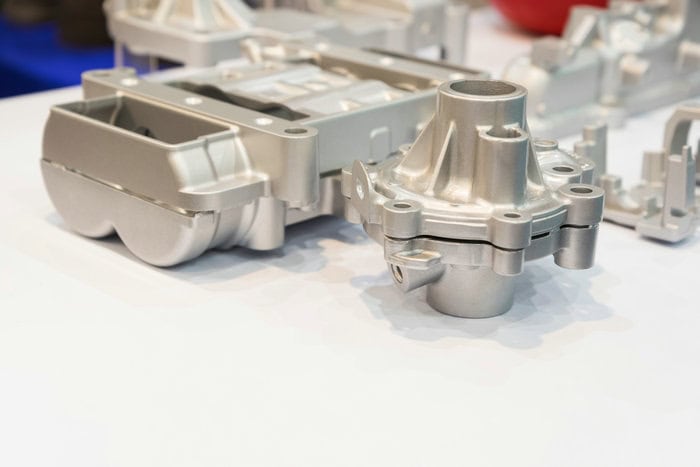
Surface Finishing Options for Aluminum die cast
The good thing with aluminum die casting is that it may not require more intensive finishing touches, including polishing. That’s because the process ensures that finished metal parts are perfect for use immediately.
However, you can still take it as an option to create a better finishing touch. That can be due to your individual preferences or doing it to improve their appeal and durability.
Below are some popular finishing options you can use for your aluminum die cast:
- Anodizing: Anodizing involves creating a protective layer on the surface of every part through an electrochemical process. This technique oxidizes the aluminum, creating a protective layer that makes it durable.
- The process offers a variety of anodizing options, including glossy or matte, depending on how you prefer your metal parts to look.
- Powder Coat: This finishing option uses powder to create a durable and hard finish. Manufacturers apply dry powder before heating to provide various finishes and colors.
- This option can be best for creating corrosion and impact-resistant parts.
- Chemical Film: Also known as chromate conversion coating, this process involves applying a chemical solution on the surface of the metal part to form a protective layer.
This option is mostly decorative and marginally protective, but can get your aluminum metal parts to last longer.
Your choice of aluminum finishing can depend on how you prefer your parts to look. Moreover, the desire to make these metals more aesthetic can motivate you to consider these finishing options.
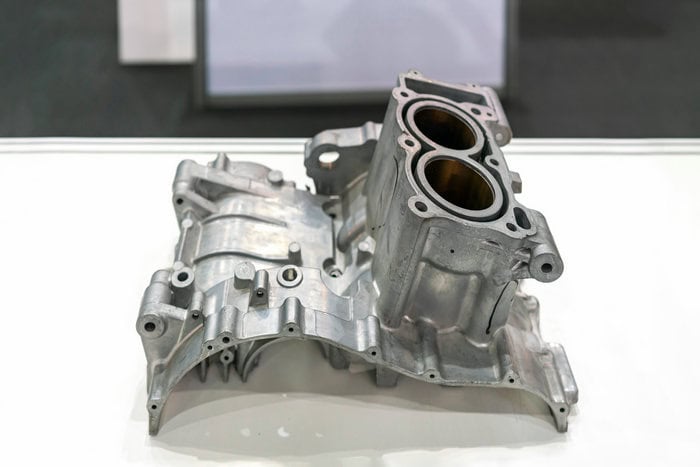
Applications of Aluminum Casting Parts
Aluminum casting parts are among the most used across numerous manufacturing industry, particularly the automotive and aerospace industries.
Below are the various areas of application of aluminum casting parts:
Construction
The construction industry utilizes aluminum casting parts for various applications, including window frames, door frames, roofing systems, and decorative elements.
Aluminum provides a high strength-to-weight ratio, corrosion resistance, and excellent thermal conductivity. That makes it an excellent perfect material for construction applications.
Automotive
Engine blocks, transmission cases, wheels, suspension components, and other structural parts are examples of the application of aluminum casting parts.
Aluminum offers high strength and stiffness, excellent corrosion resistance, and near-perfect machinability, making it an ideal material for automotive applications.
Electronics industry
Aluminum casting parts are practical in the electronics industry, including heat sinks, housings, and structural components.
Aluminum provides high thermal, electrical, and dimensional stability, making it an ideal material for electronic components.
Furniture
Aluminum casting parts are usable in the furniture industry, including chair frames, table legs, and decorative elements.
Aluminum offers high strength and stiffness, good corrosion resistance, and excellent surface finishing properties, making it an ideal material for furniture applications.
Aerospace industry
The application of aluminum casting parts structural components in the aerospace industry includes engine and landing gear components.
Aluminum provides a high strength-to-weight ratio, good corrosion resistance, and excellent fatigue properties, making it an ideal material for aerospace applications.
These applications all define the versatility this metal provides. The metal’s properties make it a much more preferred alternative to other metals, and its low costs make it much favored.
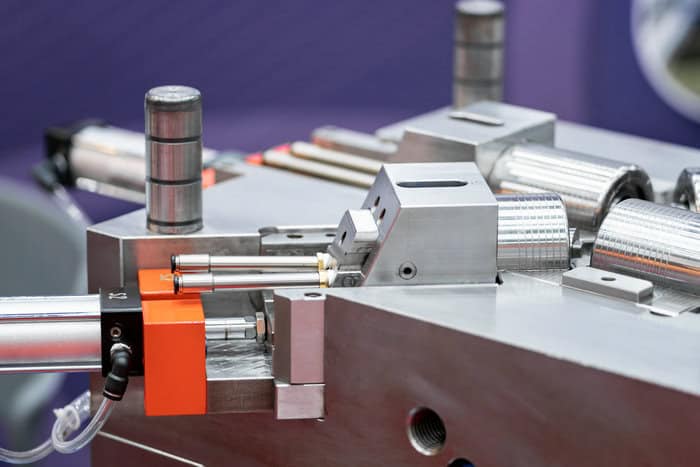
Aluminum Die Casting Parts Design – 3 Factors to Consider
Mold design, the location of the injection point, and wall thickness are all essential factors to always consider when designing aluminum parts. However, please note that how your metal part looks will depend on your die design.
When designing your die, it’s best to fine-tune your CAD machine settings to match your preferences.
Below are the three factors to consider in aluminum die casting parts design.
Mold Design
It’s best to note that your mold design can define your final part’s consistency and quality. It should have the geometry you require, and the surface finish you desire.
Unlike before, mold designing has become incredibly sophisticated due to automation. CAD designing, which typically uses computer algorithms to shape your casting molds.
An advantage of CAD is that it’s incredibly accurate and less prone to errors, and you can rely on it. It can also create mold designs that consider shrinkage and distortion that may occur during solidification.
Whichever your preferred mold design technique is, it should result in a high-quality mold that considers your preferences and expectations in the final part.
The Location of Injection Point
The injection point’s location dictates the molten flow in the mold cavity. The injection point should be strategic enough to allow an even flow and avoid air pockets that might compromise your final part’s quality.
It’s best you understand the position of the injection point can also affect your part’s appearance, sometimes leaving a mark that can make it appear unaesthetic.
Wall Thickness
You may need your metal part to be sturdy enough to withstand the pressures and stresses of their applications. A great way to guarantee that can be ensuring that the thickness of the part measures up to your expectations.
That means you should thoughtfully design your mold to accommodate the dimensions and measurements. That can provide you with a more workable part thickness. Please note that your metal part’s thickness can determine the overall production time, and the thicker they are, the longer you may have to wait.
Understanding how your mold design requirements can be handy in helping you create a more workable aluminum die cast part.
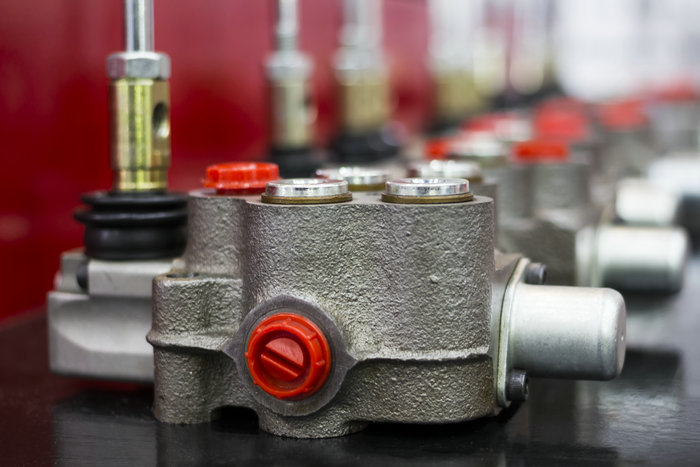
Aluminum Die Casting Quotes: Custom Aluminum Die Casting Prototypes and Parts
You may request a quote that specifies the number of parts you need and the types you prefer, depending on your industry. In this case, it’s best to specify your requirements and how you want your metal parts to appear on the surface.
Below is a checklist of some of the factors you should consider when requesting a quote:
- Part design: Provide detailed drawings or CAD files of the part you want to produce. Include information about wall thickness, dimensions, surface finish, and other critical features.
- Quantity: Indicate the number of parts you want to produce. That’ll impact the cost of tooling and the overall cost per part.
- Alloy selection: Specify the type of aluminum alloy you want for the part. That’ll affect the part’s mechanical properties and overall performance.
- Surface finishing: Indicate the type of surface finishing you require for the part, such as anodizing, powder coating, or chem film.
- Tolerances: Provide information about the tolerances required for the part, including dimensional tolerances and surface finish requirements.
- Lead time: Specify the lead time required for the production and delivery of the parts.
Knowing what you need in a metal part can inform your aluminum die-cast manufacturer to tailor the production. Please ensure you’re clear about what you want for high-quality metal parts.
Aluminum Casting Cost
Aluminum casting can cost quite a fortune, but that can depend on the volumes you need and the complexity of metal parts. On average, however, you can get a single part for prices between USD$ 0.189-5.16.
This price can range depending on several factors, including the following:
- Part design: The complexity of the part design can impact the cost of tooling and the overall production cost. More intricate designs may require more expensive tooling and longer production times.
- Alloy selection: Different aluminum alloys have different properties and costs, and the choice of alloy can impact the overall cost of the part.
- Part size and quantity: The size and quantity of parts being produced can impact the cost of production. Larger parts may require more material and energy, while higher quantities can lead to lower per-part costs due to economies of scale.
- Production process: Different aluminum casting processes have different costs. For example, high-pressure die casting is typically more expensive than gravity casting.
- Surface finishing: The type of surface finishing required for the part can also impact the overall cost. More complex surface finishing techniques like anodizing can add to the overall cost.
The cost of aluminum casting parts isn’t one-fits-all. Therefore, it’d be best to consider the factors above to get a crude estimate of how much you’ll need to pay
It’s best to always liaise with your manufacturer to determine the overall cost it’d take.
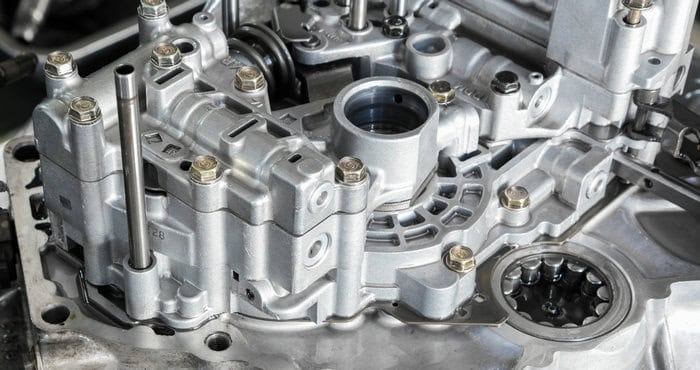
Moldie – Your Cost-Effective Aluminum Die-casting Service Provider
Moldie is an industry-leading plastic mold manufacturer and also specialize in aluminum die casting services.
MOLDIE dedicated to providing high-quality aluminum die casting solutions for clients worldwide. The company’s comprehensive range of services includes everything from part design and prototype making to mold design, production, mass production, and assembly.
From simple designs to complex technical parts, the company has the expertise and experience to deliver on even the most challenging projects.
MOLDIE are committed to quality and use only the highest-quality aluminum alloys to produce metal parts.
Partner with MOLDIE for all your aluminum die-casting needs and experience the difference in working with a trusted and reliable partner.
Conclusion
Aluminum die casting is a commonly used process for manufacturing precision parts. The method has quite a history, from simple sand casting dies to become one of the most automated metal forming processes.
The key to getting more precise aluminum parts is working with a trusted and reliable manufacturer. Moreover, it helps to get a proper acquaintance of what it takes to create more efficient types.
Hopefully, this article will help you understand the process better.
FAQ
What are the Differences Between Aluminum Die Casting vs. Sand Casting?
Aluminum die casting and sand casting are two methods used for casting aluminum parts. Die casting is faster, produces smoother parts with tighter tolerances, and is more expensive for small production runs. Sand casting is slower but cheaper, and can produce parts with a rougher surface finish.
How Expensive is Aluminum Casting?
Estimating the cost of aluminum casting can depend on the various factors involved, including the volume of parts produced and the type of casting used. Generally, though, aluminum casting can be incredibly costly, especially if the alloy used is of high quality.
How fast is the die casting process?
The die-casting process is relatively quick and can produce a significant volume of parts in a short span. The entire process, from filling the mold with molten aluminum to ejecting the finished part, typically takes only between a few seconds and a few minutes. However, that may depend on the size and complexity of the part.