Injection molding and 3D printing are two manufacturing processes widely used today. While both technologies can produce high-quality parts, they differ in many aspects, including the cost, speed, and scale of production, manufacturing method and the types of materials and part geometries that can be produced.
Explore the critical differences between injection molding and 3D printing, and find information on when to use each technology based on specific application requirements.
What is Injection Molding?
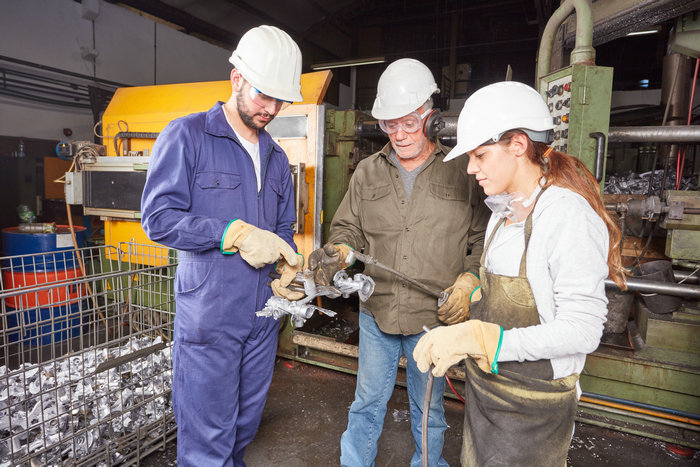
Injection molding is a manufacturing technique that involves injecting molten material, typically plastic, into a mold to produce a part. The manufacturing process begins with creating a mold designed to produce the desired shape of the final part.
Once the mold is made, the material is heated to a liquid state and injected into the mold cavity under high pressure. The material then cools and solidifies, taking on the shape of the mold.
Injection molding is widely used in manufacturing a wide range of products, from toys to medical devices and automotive components. The process is highly automated and can produce plastic parts relatively cheaply. Injection molding can produce exact and complex parts with excellent surface finish and consistency.
The materials used in injection molding include a wide range of thermoplastics, such as polyethylene, polystyrene, and polypropylene. Also, thermosetting plastics, such as epoxy and phenolic, can be used in the injection molding process.
What is 3D Printing?
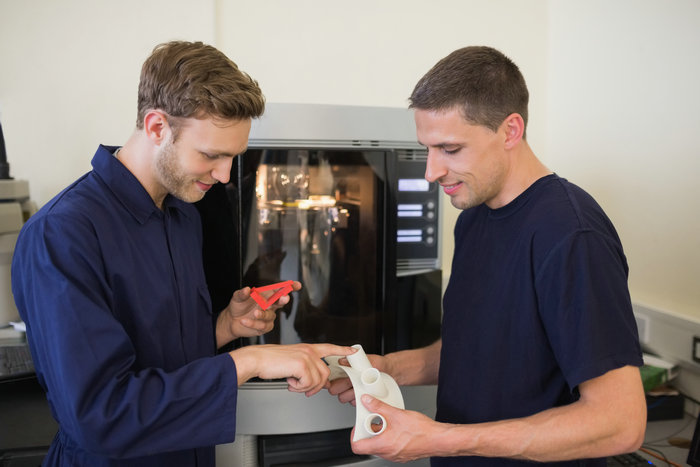
3D printing, also known as additive manufacturing, creates three-dimensional objects by adding successive layers of material, typically plastic or metal, based on a digital model. The process begins with creating a digital design or model of the object to be printed using computer-aided design (CAD) software. The design is then converted into a format the 3D printer can read, such as a stereolithography (STL) file.
Once the design is ready, the 3D printer deposits thin layers of material, one on top of the other, until the object is fully formed. The material used in 3D printing can be in the form of filament, powder, or liquid. The most common materials used in 3D printing are plastics, such as Polylactic Acid (PLA) and Acrylonitrile Butadiene Styrene (ABS), but metals, ceramics, and even food materials can also be used.
What is the Difference Between Injection Moulding and 3D Printing?
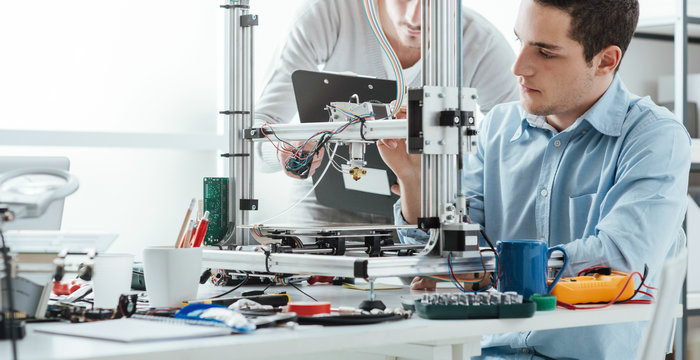
Understanding the differences between injection molding and 3D printing is essential for anyone interested in manufacturing products. Both processes have their strengths and weaknesses, and deciding which one to use primarily depends on the type of product and production volume. Here are the significant differences:
1. Part Design
Regarding part design, injection molding and 3D printing have some significant differences. Injection molding requires creating a mould designed to produce the desired shape of the final part. This means the part’s design must be finalized before the injection molds can be made.
Any changes in the design phase would require the creation of new injection molds, which can be time-consuming and expensive. On the other hand, 3D printing allows for more flexibility in part design. With 3D printing, designers can change the digital model and print a new version of the part quickly and easily.
This makes additive manufacturing an ideal choice for prototyping and iterative design processes. Aside from that, injection molding can produce parts with a high degree of precision and consistency. Still, the design must be relatively simple due to the limitations of the molding process.
With 3D printing, however, designers can create highly complex and detailed parts that would be difficult or impossible to produce with injection molding. Overall, the differences in part design between injection molding and 3D printing mean that each process best suits different applications.
Injection molding is better for large batch production of simple parts, while 3D printing is ideal for the small batch production of complex designs and customizable parts. Understanding the differences in part design can help manufacturers choose the best process for their specific needs, ensuring the best possible outcome for their project.
2. Process
The two manufacturing methods differ significantly in their fundamental approach to manufacturing, the machinery and manufacturing environment required, and whether to own or outsource the production process.
Fundamental Differences
Although additive manufacturing and traditional manufacturing, may use similar raw materials, the processes are fundamentally different. The two methods have some fundamentally different characteristics that set them apart.
For example, 3D printing is a tool-free process that doesn’t require specialized tooling to create a final product. Instead, the printer builds parts slowly, one layer at a time, following a computer-generated design. This allows for greater flexibility in design, with almost total geometric freedom to create complex shapes and features.
However, overhanging sections may require support structures to prevent sagging during printing. In contrast, traditional manufacturing requires injection molding tooling to form the final product. The mold is created beforehand and then used to inject molten plastic into the desired shape.
This process is swift and efficient, with the ability to produce high volumes of parts in a short amount of time. However, this also means injection molding is more limited regarding design flexibility. Also, 3D printing involves a printhead that moves along three axes, guided by computer instructions, to deposit the material at specific coordinates precisely. In contrast, the nozzle of the 3d injection molding machine remains stationary while the mold moves to create the part.
This means that additive manufacturing is more error-prone than injection molding. 3D printing is like building a house brick by brick, potentially creating multiple rooms and features. In contrast, plastic injection is like filling an ice cube tray with limited flexibility but lightning-fast production times.
Machinery and Manufacturing Environment
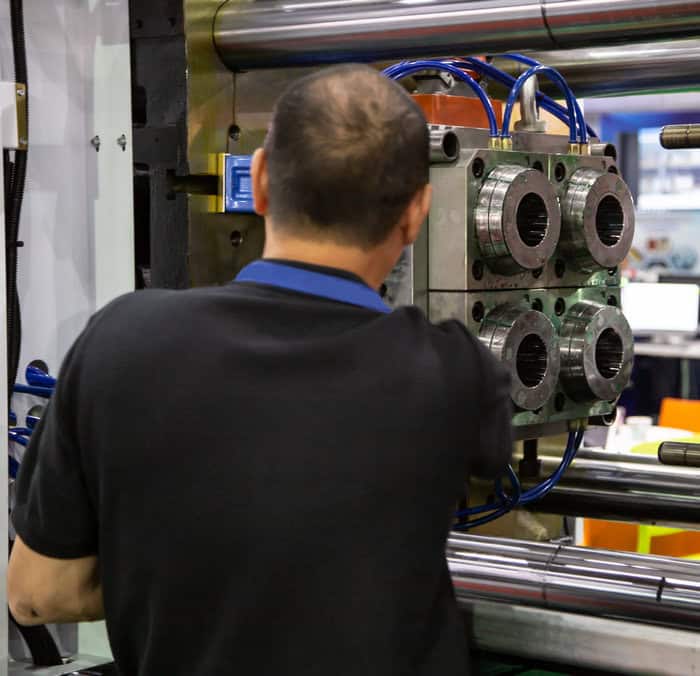
Traditional manufacturing uses heavy machinery that can only be operated by trained professionals in a factory or industrial setting. They require a significant amount of space, with some machines having a footprint of several square meters. Also, space is needed to store the molds and the finished mold parts.
On the other hand, the machinery used in 3D printing varies greatly depending on the printer type. Some industrial 3D printers, such as those using Direct Metal Laser Sintering (DMLS), can be as large and complex as injection molding machines. These printers often require significant space and power usage and have emissions that can be harmful, so they are also typically restricted to industrial settings.
However, many FDM (Fused Deposition Modeling) 3D printers have a more compact footprint and can be used in non-industrial environments, such as offices or residential buildings. These printers are often classified as industrial, professional, or desktop, depending on their size, quality, and where they can be used.
Desktop 3D printers are the smallest and can be used in casual settings like classrooms or homes. In contrast, industrial printers are larger, more powerful, and used for mass production in factories and industrial settings. The differences in manufacturing and machinery requirements between these two manufacturing methods significantly affect production processes.
Injection molding requires a significant upfront investment in machinery, injection molding tooling, and factory space, making it best suited for high-volume production. 3D printing, on the other hand, can be done with smaller, more affordable equipment and can produce parts on-demand with much more flexibility in design and production volume.
Ownership vs. Outsourcing
Injection molding requires a significant investment in machinery, mold-making equipment, and the necessary infrastructure to support these processes. As a result, outsourcing the injection molding process to a specialized manufacturer is often more cost-effective.
In contrast, 3D printing machines are often more affordable and accessible, making it easier for small businesses and individuals to own equipment and produce parts in-house. This can be especially beneficial for small-scale production runs or custom-designed parts.
3. Material
Both 3D printing and injection molding rely heavily on plastic polymers, although there are some critical differences between the manufacturing technique. Regarding form, 3D printing uses a filament, essentially long strands of plastic wound onto a spool. On the other hand, injection molding uses plastic pellets, which are small, solid chunks of raw material. Interestingly, filament used in 3D printing is often created by melting and extruding pellets, which are then wound onto spools.
Aside from that, most injection molding machines can produce melted plastic with high melting points. However, the hot end of a typical 3D printer may not have enough power to handle high-temperature materials. 3D printers typically achieve better results with low-temperature materials like Polylactic Acid (PLA), although these parts have inferior mechanical properties. High-end 3D printers have high-temperature hot ends and enclosed print chambers and can more easily print high-temperature materials.
Some of the most common 3D printing filaments are Acrylonitrile Butadiene Styrene (ABS), PLA, Polyethylene Terephthalate Glycol (PETG), and Thermoplastic Polyurethane (TPU). At the same time, performance materials (printable on production-grade printers only) include Polyether Ether Ketone (PEEK) and Polyetherketoneketone (PEKK).
ABS, Polycarbonate (PC), Polyethylene (PE), Polypropylene (PP), and nylon are the most common injection molding materials. It’s also possible to create hybrid materials, as different pellet types can be easily mixed, including non-plastic materials.
4. Post Processing
Regarding post-processing, there are distinct differences between 3D printing and injection molding. One of the biggest challenges with FDM 3D printing is the poor surface finish that often results. The process leaves behind visible layer lines on the surface of the printed parts, which can detract from their appearance and feel.
To overcome this, 3D-printed parts often require extensive post-processing to achieve a smoother surface finish. Surface finishing techniques like sanding, polishing, or abrasive blasting can create a more polished look. However, these techniques add time and cost to the production process. Additionally, support structures may need to be removed manually or chemically.
In contrast, traditional manufacturing generally produces higher-quality surface finishes without requiring post-processing. The metal mold used in the injection molding process is typically textured, which transfers to each molding, saving time and reducing the need for additional finishing steps. However, some moldings may require flash, or excess plastic, to be removed manually after the molding process is complete.
5. Cost, Speed and Scale
3D printing is perfect for producing small batches and one-off parts, with low upfront costs and short lead times. The process doesn’t require tooling, so the first part can be fabricated within a few hours. This makes it an ideal choice for prototypes and low-volume production runs. However, 3D printing has no economy of scale. As quantities increase, the cost per part remains unchanged, making it less cost-effective.
On the other hand, injection molding requires metal tooling, which takes several weeks and can cost several thousand dollars to manufacture. All precise parts can be fabricated once the mold is ready, but once the tooling is set up, parts can be produced at a low additional cost in seconds. Injection molding is best suited to larger production runs where economies of scale come into play.
For batches over 10,000 units, injection molding is of better value and significantly better value beyond 100,000 units. Determining whether a part is best suited for 3D printing or injection molding involves finding the break-even point for the mold. A general rule of thumb is that 3D printing is cheaper for batches under 10,000, while injection molding is more cost-effective above that number.
However, the two processes have their own advantages, and there are ways to lower costs and turnaround times of the manufacturing process. For example, CNC machining the tooling from low-cost aluminum instead of steel can reduce the tooling costs.
Likewise, it is becoming more affordable to 3D print parts in large volumes using production-ready 3D printers with large build volumes. Moreover, some printers with large build volumes can print several parts simultaneously, increasing productivity and reducing production time.
6. Applications
3D printing excels in creating custom parts for individual users, spare parts for obsolete systems, prosthetics, toys, and electronic device housings. Also, it’s great for creating prototypes and display models in fields like healthcare and architecture.
On the other hand, traditional manufacturing is perfect for mass production of products in areas like food, consumer goods, and automotive. It’s ideal for creating containers and boxes, food packaging, automotive dashboard components, and custom jigs and fixtures. Moreover, injection molding is the go-to process for prototypes of molded parts. Each technology has its own niche in the manufacturing world, and the choice between them depends on the application and the production volume.
When Should You Use Each Process?
Injection molding is best suited for producing large parts, typically over 10,000 units. The upfront cost can be high due to the need for tooling, but once the mold is created, it can produce parts at a meagre cost per unit. This makes injection molding an excellent choice for mass production in the food, consumer goods, and automotive industries. If you need to produce many identical parts, injection molding is likely the way.
On the other hand, 3D printing is ideal for low-volume production and rapid prototyping. The process is excellent for quickly creating small batches of custom or one-of-a-kind parts with little upfront cost. Also, it’s perfect for creating complex geometries that would be difficult or impossible to produce with injection molding. It’s an excellent choice for industries like healthcare and architecture, where display models and custom medical devices are often required.
Which One Should You Choose?
When deciding between 3D printing and injection molding, there are several factors to consider. Both technologies have their unique advantages and disadvantages, and choosing the right one for your specific application requires careful consideration.
Benefits of Injection Molding
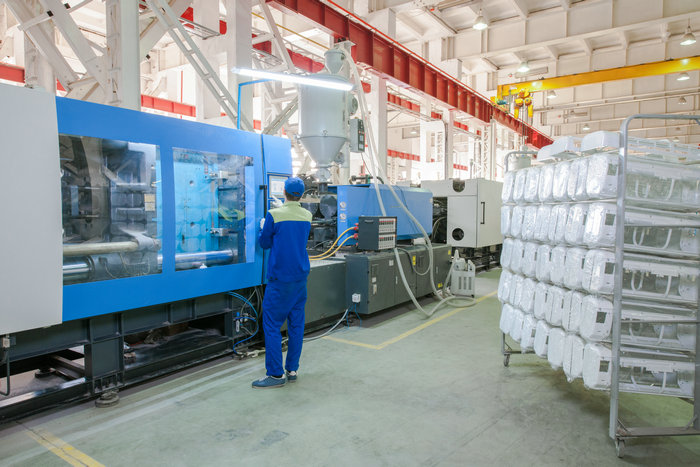
Injection molding is a manufacturing process that offers several benefits over 3D printing. Here are some of the critical benefits of injection molding:
- High-volume production: Injection molding is ideal for producing large quantities of parts quickly and efficiently. Once the mold is created, parts can be produced rapidly and cheaply per unit.
- Consistency and repeatability: Injection molding offers high accuracy and consistency, making it ideal for producing complex parts with tight tolerances. The process allows for creating identical parts with high precision and accuracy, reducing the likelihood of defects or inconsistencies.
- Wide range of materials: Injection molding can be used with various materials, including plastics, metals, and ceramics. This versatility makes it suitable for a wide range of applications and industries.
- High-quality parts: Injection molding produces excellent surface finishes and dimensional accuracy. The process allows for producing parts with intricate details and complex geometries, producing high-quality parts that meet the most demanding specifications.
- Low cost per unit: While injection molding requires an initial investment in tooling, the cost per unit decreases as the volume of parts produced increases. This makes injection molding a cheaper choice for high-volume production runs.
Injection molding is an excellent choice for high-volume production runs, applications that require a wide range of materials and parts with complex geometries and tight tolerances.
Disadvantages of Injection Moulding
- High upfront cost: Injection molding requires the creation of a mold which can be costly and time-consuming to produce. This means that it may not be cost-effective for smaller production runs.
- Limited design flexibility: The design of the mold can limit the shapes and geometries that can be produced. Changes to the mold can be costly and time-consuming.
- Material waste: Injection molding can produce a significant amount of waste material, particularly during the set-up and testing of the mold.
- Production time: The process of mold creation can take several weeks, which can delay the production of parts.
- Environmental impact: The production of injection molding often involves the use of large amounts of energy and resources, which can have a negative effect on the environment.
Benefits of 3d Printing
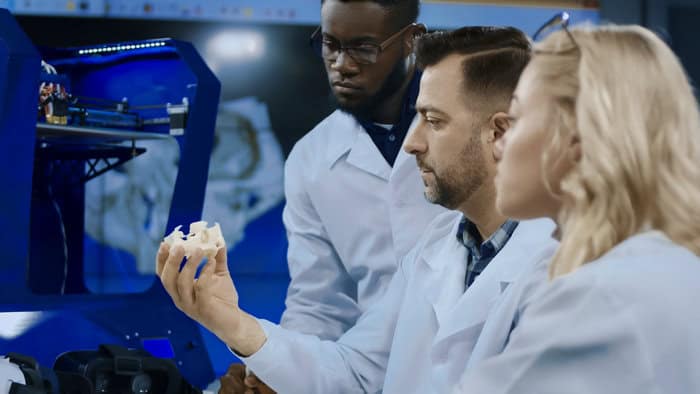
When deciding between injection molding and 3D printing, there are many factors to consider. Here are some of the benefits of 3D printing that you may want to keep in mind:
- Rapid Prototyping: One of the most significant advantages of 3D printing is its ability to prototype parts rapidly. With 3D printing, you can quickly produce a physical part from a digital model, allowing you to test and refine your designs much faster than traditional manufacturing methods. This can be especially helpful in product development when time is of the essence.
- Customization: 3D printing also allows you to customize parts and create unique designs that may not be possible with injection molding. This can be especially useful in the medical and dental fields, where custom-fitted prosthetics and implants are often required.
- Low-Cost Tooling: Unlike injection molding, 3D printing doesn’t require expensive tooling to create parts. This means you can produce small quantities of parts at a lower cost and without the upfront investment required for tooling.
- Design Freedom: With 3D printing, you have greater design freedom than injection molding. You can create parts with complex geometries, internal structures, and organic shapes that may be difficult or impossible to produce.
- Reduced Waste: With injection molding, excess plastic material must be removed and discarded, whereas 3D printing only uses the material necessary to produce the part.
3D printing is a versatile and flexible manufacturing process that offers unique benefits not available with injection molding. However, injection molding may still be the better choice for specific applications, such as high-volume production runs or parts that require a very high precision or surface finish. It’s essential to carefully consider your project’s requirements and weigh each manufacturing method’s pros and cons before deciding.
Disadvantages of 3D Printing
- Limited materials: 3D printing is limited in the range of materials it can use compared to injection molding. While injection molding can use various materials, 3D printing is limited to specific types of plastics, resins, and metals.
- Slow production speed: 3D printing is slower than injection molding, making it less suitable for high-volume production runs.
- Poor surface finish: The surface finish of 3D printed parts could be better, with visible layer lines that require post-processing to improve.
- Limited scalability: While 3D printing is ideal for small-scale production and prototyping, it becomes less cost-effective as production volumes increase, making it less scalable than injection molding.
Conclusion
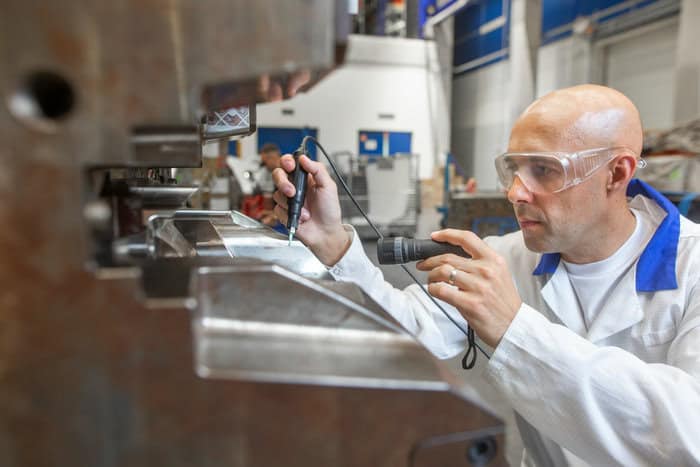
Both injection molding and 3D printing have their unique strengths and weaknesses. When choosing which technology to use, it is crucial to consider factors such as production scale, lead time, cost, and part complexity.
Injection molding is an excellent choice for high-volume production runs, and it offers a wide range of materials, perfect part consistency, and precise tolerances. On the other hand, 3D printing excels at producing complex geometries and low-volume production runs and offers rapid prototyping and design flexibility.
Ultimately, the decision on which technology to use will depend on the specific needs of your project. By considering the benefits and limitations of each method, you can choose the one that best suits your needs and budget.