Aluminum Die Casting
Aluminum Die Casting Service
We have an expert in-house team that closely monitors every step of the die-casting process from design to finished product. This enables us to maintain tight tolerances, excellent mechanical properties, and efficient production volumes across small and large orders for clients.
Our aluminum die-casting capabilities cater to diverse sectors like medical, military, automotive, agriculture, and other industries. We can produce intricate or basic aluminum die-cast parts as per your exact specifications using direct injection methods and automation.
At Moldie, we are committed to safety, efficiency, sustainability, and providing clients with high-quality custom aluminum die-cast components suitable for specialized applications or mass production needs. Get in touch with us to learn more or request a quote.
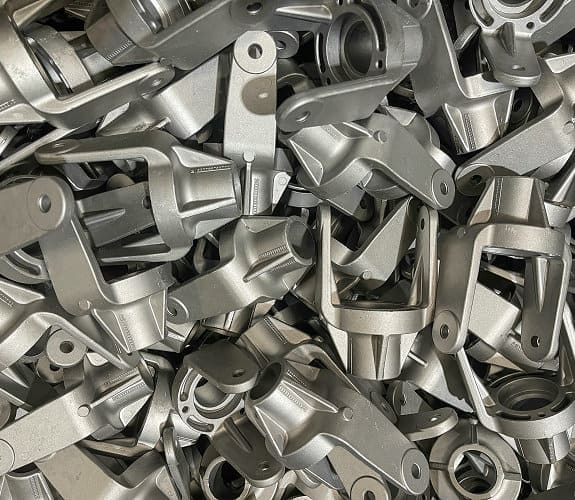
Request a Quote
Basics of Aluminum Die Casting
You’re diving into a process that has reshaped the manufacturing world, especially when it comes to aluminum.
Die casting allows for the production of complex aluminum parts with great precision and efficiency.
Understanding Die Casting and Aluminum
Die casting is a metal fabrication process where molten aluminum is injected under high pressure into a mold cavity.
This technique is favored for its ability to produce large quantities of parts with detailed, complex shapes that would be difficult or impossible to achieve with other manufacturing methods. The process utilizes dies – or molds – which can be reused for producing identical castings.
- Aluminum: A versatile and lightweight metal ideal for die casting.
- Die Casting Process: Involves injecting molten aluminum into a die at high pressure.
One of the aluminum alloys often used in die casting is alloy 383. It’s a favorite for being easy to cast while offering a good balance between performance and cost.
Properties of Aluminum for Casting
Aluminum has several properties that make it an excellent choice for casting:
- Lightweight: One of the key benefits you’ll hear about aluminum is its low density, making it exceptionally lightweight, which is important for the automotive and aerospace industries.
- Strength: Despite its lightness, aluminum alloys like 383 are strong and durable.
- Corrosion Resistance: Your aluminum die cast parts will resist rusting and corrosion naturally, perfect for outdoor or harsh environment applications.
- Conductivity: Aluminum’s impressive electrical and thermal conductivity is essential for electronics and cooling systems.
Property | Benefit |
---|---|
Lightweight | Ideal for portability |
Strength | Ensures durability |
Corrosion Resistance | Withstands harsh conditions |
Conductivity | Conducts heat and electricity |
Aluminum’s combination of lightweight, strength, and corrosion resistance, coupled with its excellent conductivity, makes it a top material for your die casting needs.
Die Casting Process
Die casting is all about precision and technique, where you take molten metal and inject it into a mold to create complex parts. It’s a bit like high-stakes baking with metal. Let’s break down the steps.
Preparation and Injection of Molten Metal
First things first, you’ve got to heat up your chosen metal to its melting point; think of it as getting your ingredients ready.
Once it’s molten, that’s when the action happens.
You don’t just pour the metal into the mold—that would be too easy. Instead, you inject it under high pressure, making sure it fills every nook and cranny of the mold for the detail you need. This step’s key players are:
- Molten metal: It’s got to be just the right temperature. Not too hot, not too cool.
- Injection: Think of it like filling a water balloon without any of the splash.
Mold Design and Creation
Before you even think about metal, you’ve got to get your mold sorted. This isn’t just any mold—you design this for the long haul, built to withstand high pressure and temperatures repeatedly. The design includes:
- Parting line: This is where your mold pieces come together and split apart. Getting this right is crucial for a clean finish.
And remember, shrinkage happens. When metal cools, it shrinks, so account for that in your mold design.
Cooling and Solidification
Once the molten metal’s in, you’ve got to cool it down so it solidifies. But don’t rush this part; metal needs to chill out at its own pace to avoid defects.
As it solidifies, the details of your design emerge, crisp and precise. Here’s the cool-down checklist:
- Give it time: Let the metal cool slowly to avoid issues like shrinkage messing up your masterpiece.
- Eject the part: When everything’s solid, open the mold and take out your creation. It’s like opening the oven to find a perfectly baked cake, only way tougher and much less tasty.
Aluminum Alloys and Selection
When you’re getting into aluminum die casting, knowing which alloy to pick can make or break your project. Every alloy has a unique set of properties that affect how it behaves during and after casting.
Popular Aluminum Alloys in Die Casting
Aluminum alloys are a go-to for die casting because they’re lightweight, strong, and can withstand high temperatures. Here’s a quick look at some of the stars of the show:
- A360: Great for pressure tightness and fluidity, making it a solid choice for complex parts.
- A380: Your all-rounder – it’s the most common with a good mix of performance, cost, and metalworking properties.
- A413: Think high pressure situations. It’s the one for when you need maximum strength.
- B390: Go for this when you’re dealing with abrasive wear and needing high hardness; it’s a champ for automotive parts, especially.
Alloy Properties and Suitability
Each alloy has a superpower – whether it’s corrosion resistance, strength, or being easy to work with. Here’s why that matters:
Corrosion Resistance:
- Alloys like A380 are your buddies for parts that need to resist the elements.
Strength:
- Got something heavy-duty? B390 may be your hero for its strength and wear-resistance — think transmission components.
Machinability:
- A360 isn’t just strong, it’s also easy to machine, which means less hassle during manufacturing.
Remember, the alloy you choose will impact not just how your cast turns out, but also its durability, appearance, and cost.
It’s like picking a character in a video game — each has different abilities, so you choose based on the mission ahead.
Keep an eye on elements like magnesium, copper, and silicon which can influence an alloy’s properties. For instance, silicon can improve fluidity and reduce shrinkage in alloys like A380, making it easier to fill in complex molds.
Design Considerations for Aluminum Parts
Designing aluminum die-cast parts demands a fine balance between their structural integrity and functional performance. You’ve got to consider how each aspect of your design will shape up during the die-casting process.
Optimizing Structure and Functionality
When tweaking your design for manufacturability (DFM), you’re aiming to simplify complex shapes without compromising on durability. Let’s break it down:
- Wall Thickness: Keep it consistent. Thick walls can lead to areas of prolonged cooling and shrinkage issues, whereas thin walls might not fill correctly. Aim for uniformity to prevent these issues.
- Fillet vs. Sharp Corners: Round ’em up! Fillets (curved transitions between surfaces) are your friends in die-casting. They reduce stress concentrations and facilitate smoother material flow.
- Draft Angles: Ever tried pulling a tight lid off a container? That’s a no-draft nightmare. Include slight angles on vertical walls to allow easy part removal from the die.
Reducing Defects and Enhancing Performance
Your goal is to produce high-performing parts with minimal defects. Pay attention to these details:
- Bosses and Ribs: Use bosses for mounting and stand-offs, and ribs for structural support, but keep them proportionate. Thicker features can cause uneven cooling, leading to defects.
- Holes and Windows: Ensure you’ve got enough draft and that hole diameters don’t undercut the wall thickness to maintain integrity.
- Tolerances: Tight tolerances can be costly and are harder to maintain in die-casting. Be realistic; only specify tight tolerances where critical to the part’s function.
Post-Casting Operations
After your aluminum parts come out of the die casting mold, they’re not finished yet. You’ve still got to clean them up and give them that functional and aesthetic edge. That’s where post-casting operations come in. They’re like the afterparty for die casting—a necessary phase to get your parts looking and functioning just right.
Trimming and Machining
Trimming is your first step. You’ll be cutting off the excess material, known as flash, that’s just hanging around after casting. This tidies up your parts and preps them for their next big event.
When we talk about machining, we’re getting into the nitty-gritty of precision. It’s where you drill, mill, or turn the parts to get the tight tolerances and perfect fit that your project demands.
- Key Machining Processes:
- Drilling: Making holes where you need them.
- Milling: Removing material to shape the part to your specs.
- Turning: Spinning your parts on a lathe to get the right diameter.
Surface Finishing and Treatment
Getting the right surface finish plays a huge part in how your product looks and performs. You’ve got a few choices depending on what you need:
- Anodizing: For the tough-as-nails surface that also lets you add some color.
- Powder Coat: This gives your parts a strong, even, and colorful coat that’s eco-friendlier than traditional painting.
- Plating: If you’re looking for corrosion resistance or electrical conductivity, plating’s your go-to.
Each coating process brings its own perks, from scratch resistance to special textures. Just remember, the better the surface preparation, the better the finish will stick.
- Popular Coatings:
- Chrome Plating: Shiny and durable.
- Nickel Plating: Corrosion-resistant and magnetic.
Applications and Industries
When you’re looking into aluminum die casting, you’ll find its applications spanning across various industries thanks to the material’s strength, lightweight nature, and versatility. Aluminum parts like engine blocks and housings are just the tip of the iceberg.
Automotive and Aerospace
In the automotive sector, aluminum die casting is crucial for producing engine blocks, transmission housings, and structural components. These parts benefit from aluminum’s thermal efficiency and durability, which is essential for vehicles.
Similarly, in the aerospace industry, aluminum parts made through die casting are valued for their strength-to-weight ratio, playing a pivotal role in constructing components that can withstand high pressures while keeping the heft to a minimum.
- Automotive Applications:
- Engine blocks
- Gearboxes
- Structural components
- Aerospace Applications:
- Landing gear parts
- Seat frames
- Instrument panels
Electrical Components and Telecom
You’ll see aluminum die casting making a mark in the electrical and telecom fields as well. The superior electrical performance and heat dissipation properties of aluminum are ideal for housings of electronic devices and connectors.
The telecom industry benefits from die-cast aluminum components due to their durability and the protection they offer to sensitive communication equipment.
- Electrical Applications:
- Connectors
- Enclosures for electronics
- Telecom Applications:
- Antenna mounts
- Communication boxes
Construction and Industrial Applications
Move over to construction and industrial applications, and you’ll find aluminum die-cast parts are everywhere. They’re in the tools you use, the machines that are part of your daily operations, and even in the buildings you frequent.
Aluminum’s corrosion resistance means your construction materials stand up better against the elements.
- Construction Applications:
- Window and door frames
- Building façades
- Industrial Applications:
- Machine parts
- Conveyance equipment
Advantages of Aluminum Die Casting
Aluminum die casting brings to the table a blend of perks that can be pivotal in your production line. You’ve got economic benefits that’ll keep your wallet in check, as well as physical and mechanical advantages ensuring your components rock at their jobs.
Economic Benefits
- Cost-effective: You save money because aluminum die casting is less expensive compared to other processes, especially when you’re eyeballing production of large quantities.
- Efficiency: Your operations speed up with aluminum die casting’s fast cycles – more parts per hour means a happier bottom line.
Physical and Mechanical Advantages
- Strength-to-weight ratio: Products turn out tough yet lightweight, which means you get the best of both worlds – strength where it counts and ease of handling.
- Precision: Get intricate details spot on, with high precision that’s consistent across batches.
- Versatile: Whether it’s for aerospace gadgets or kitchen widgets, aluminum die casting fits into a wide variety of industry needs.
- Dimensional stability: Parts keep their cool and shape, even when temperatures soar, thanks to aluminum’s excellent stability under heat.
- Durability: Your components will be ready to take on wear and tear like champs, making them a durable choice for the long haul.
- Corrosion resistance: Aluminum parts resist rust and corrosion, so they stay looking good and working right, even in tough environments.
Quality Control and Standards
When you’re dealing with aluminum die casting, maintaining high quality and adhering to stringent standards are non-negotiable. It’s all about striking the balance between performance and accuracy, ensuring your casts are up to scratch in design and durability.
Implementing ISO 9001 and Industry Standards
To keep your aluminum die casting game strong, it’s key to implement ISO 9001 standards. This international benchmark spells out what’s expected in terms of a quality management system.
By following these guidelines, you ensure that your processes are as sharp as they can be, minimizing errors and boosting performance. Let’s break this down:
- Compliance: Adhering to ISO 9001 helps you stay aligned with international quality practices.
- Consistency: Regular audits and continuous improvement mean your die casts are always dependable.
Achieving Accuracy and Consistency
Hitting the mark on accuracy and consistency is super important in aluminum die casting. Your die design has to nail the complex shapes without a hitch and make sure each cast looks great and functions without fail.
- Die Design: Crafting dies that can reliably reproduce complex shapes is crucial for your product’s appearance and its longevity.
- Structural Integrity: A well-designed die also ensures the structural integrity of your casts, so they hold up under stress and do the job they’re designed for.
Sustainability and Recycling
Die casting with aluminum isn’t just about shaping metal; it’s your way to contribute to greener manufacturing by choosing a process that supports full recyclability and sustainable manufacturing practices.
Recycling Aluminum Castings
When you recycle aluminum castings, you’re engaging in a cycle that’s both sustainable and economically savvy. Aluminum is 100% recyclable, which means you can recycle your castings without losing quality.
- Economic Benefit: Recycling aluminum saves around 95% of the energy required to produce it from raw materials.
- Environmental Impact: By recycling, you reduce CO2 emissions and the need for new raw material extraction, aligning with green manufacturing principles.
Remember, recycling isn’t just tossing leftovers into a bin; it’s a planned process. You might come across systems designed to measure the environmental impact of die casting, like those computing CO2 emissions, solid waste, and energy consumption per process plan.
In your die casting endeavors, keep an eye out for technologies that enhance sustainability, such as solid-state electrolysis processes. These aim to lower energy consumption even further, which is a big win for both the planet and your power bills.
By preferring aluminum castings and recycling them, you’re not only upholding sustainable manufacturing values, you’re also ensuring a greener future with every production cycle.