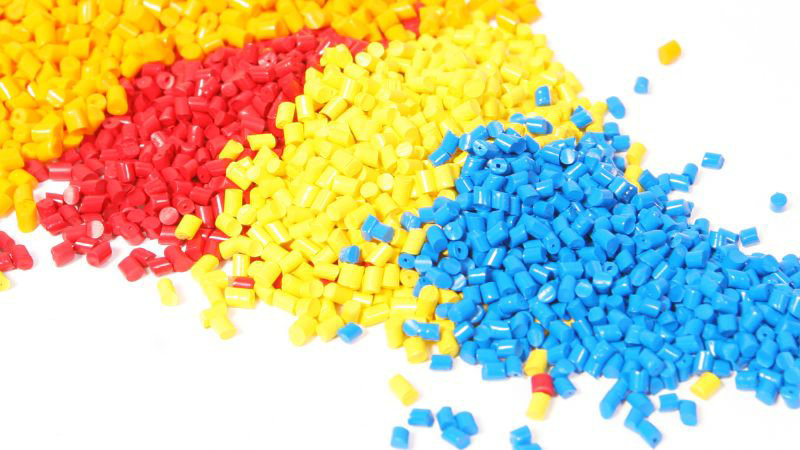
Thermoplastics and thermosets are two main types of plastics that are commonly used in various industries. While they share some similarities as organic polymers, thermoplastics and thermosets have key differences in their molecular structure and properties that determine how they can be used.
This article will help you understand the differences between thermoplastics and thermosets to help provide an understanding of their different characteristics and applications.
Overview of Thermoplastic and Thermosets
The two main categories of polymeric materials used in manufacturing are thermosets and thermoplastics.
Here is a brief definition of both materials:
- Thermoplastics are polymers that become pliable or moldable above a specific temperature and solidify upon cooling. You can reheat and reshape them again and again without altering their chemical structure.
- Thermosets are polymer materials that irreversibly cure or harden through the formation of cross-linked networks.
Differences between thermoset and thermoplastic:
Parameter | Thermoplastics | Thermosets |
---|---|---|
Structure | Linear, branched polymers | Cross-linked polymers |
Bonding | Weak van der Waals forces | Strong covalent bonds |
Melting point | Sharp, can be remelted | Gradual degradation |
Recyclability | Recyclable | Not recyclable |
Examples | Polyethylene, nylon, PET | Epoxies, phenolics |
Some key properties that differ:
- Thermoplastics can be repeatedly hardened and softened when heated, while thermosets undergo permanent hardening after initial forming
- Thermoplastics have lower melting temperatures compared to the degradation temperatures of thermosets
- Thermosets generally have higher mechanical strength, hardness and thermal stability
Here are some examples of thermoplastic
- Acrylic
- Nylon
- Acetal Copolymer Polyoxymethylene
- Acetal Homopolymer Polyoxymethylene
- Polycarbonate (PC)
- Polyethylene (PE)
- Polystyrene (PS)
- Polypropylene (PP)
- Polyvinylchloride (PVC)
- Polyethylene terephthalate (PET)
- Teflon
Thermoset plastics are used in industries because thermosets provide structural integrity and are more economical. Here are some examples of thermoset plastic:
- Phenolics
- Silicone
- Melamine
- Epoxy
- Polyvinylidene fluoride (PVDF)
- Polytetrafluoroethylene (PTFE)
- Polyurethane
- Polyimide
In manufacturing, thermoplastics are amenable to processes like injection molding, while thermosets require impregnation of reinforcements and controlled curing. Composites can be made using both thermoplastic and thermoset polymer matrices. Examples are carbon fiber reinforced plastics (CFRP) and ceramic matrix composites (CMC) like C/C-SiC.
Chemical Properties and Structure
Polymer Chains and Crosslinking
Thermoplastics are linear chains of molecules, usually carbon-based, like polyethylene and nylon. Easy to remold, they’re flexible because they lack strong bonds between chains. However, the molecules in thermosets are crosslinked, creating a complex web. Materials like epoxy, silicone, and phenolic have this mesh-like structure, which makes them a tough one to reshape once they’ve cured.
- Thermoplastics: Linear, no crosslinking (e.g., Polycarbonate, Acrylic)
- Thermosets: Crosslinked, intersecting networks (e.g., Epoxy, Polyurethane)
Chemical Resistance
If you’re up against chemicals, you want to know what’ll hold up. Polymer choice is key. Thermoplastics like polypropylene can resist many a chemical villain without a hitch, but they might weaken with certain solvents. Thermosets, bless their sturdy structure, come out a bit stronger – materials like epoxy and phenolic stand firm against a broader spectrum of chemical substances due to that pesky crosslinking.
- Chemical Resistance:
- Thermoplastics: Good to excellent (varies by material, e.g., Nylon, Acrylic)
- Thermosets: Typically excellent (e.g., Silicone, Polyurethane)
Manufacturing and Molding Process
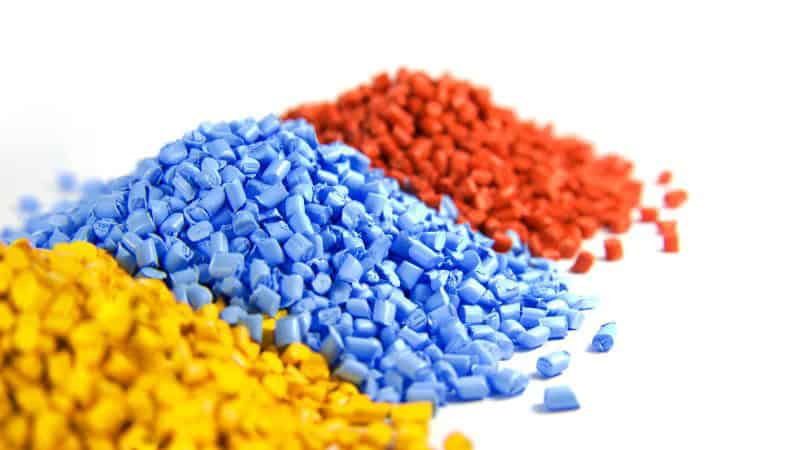
When you need to produce thermoplastic and thermoset products, there are different techniques for processing into:
- Thermoplastics: Heated to make them pliable for processes like injection molding and extrusion.
- Thermosets: Impregnated into reinforcements and undergo controlled curing reactions.
Injection Molding and Extrusion
When you’re dealing with thermoplastics, techniques like injection molding and extrusion are the go-to methods. In injection molding, the thermoset plastic is melted and injected into a mold under high pressure. It’s a fast process, ideal for making large quantities of identical items. For extrusion, the plastic is pushed through a die to create long, continuous shapes.
Key process characteristics:
- Thermoplastic pellets are fed into a heated barrel and forced into a mold cavity under pressure.
- Issues can occur due to flow direction and the formation of weld lines.
- Crystalline thermoplastics like polyethylene (PE) are more prone compared to amorphous ones like polystyrene (PS).
Parameter | Effects |
---|---|
Mold temperature | Cooling rate, crystallinity |
Injection speed | Flow direction, weld line strength |
Holding pressure | Reduces voids and sinks |
Curing Processes
Curing is critical when you’re working with thermosetting plastics. You apply heat or a chemical reaction, and the material changes permanently — it can’t be reshaped after it’s cured. This process allows thermosets like polyimide to solidify into strong, durable items like insulation or adhesives. Curing makes them resistant to high temperatures and chemicals, so they’re often used in harsh environments.
Liquid Silicon Infiltration
Based on the search results, Liquid Silicon Infiltration (LSI) is a process used to manufacture ceramic matrix composites, specifically C/C-SiC (carbon-carbon silicon carbide) composites. The key points about Liquid Silicon Infiltration (LSI) from the sources are:
- It involves infiltrating a porous carbon preform with molten silicon above the melting point of silicon (1414°C)
- The molten silicon reacts with carbon to form silicon carbide (SiC), hence creating a SiC matrix composite
- It is an efficient and cost-effective way of fabricating SiC matrix composites compared to other processes like Chemical Vapor Infiltration
- Process parameters like temperature, vacuum level, and inert gas pressure can be controlled to optimize infiltration
- The porous carbon preform microstructure affects the completeness of infiltration and reaction
- Composites made by LSI have high thermal stability, thermal conductivity and other enhanced properties
In summary, Liquid Silicon Infiltration (LSI) is a specialized manufacturing process to create C/C-SiC ceramic matrix composites using molten silicon infiltration and reaction with carbon.
Resin Transfer and Reaction Injection Molding
If you’re using thermoset plastics, you might use resin transfer molding (RTM) — it’s like a more sophisticated version of injection molding, using preforms. Reaction injection molding (RIM) is another technique for thermosets, mixing two liquid components to react and set inside the mold. Both methods give you strong parts with complex shapes, often found in automotive and aerospace applications.
Material Properties and Performance
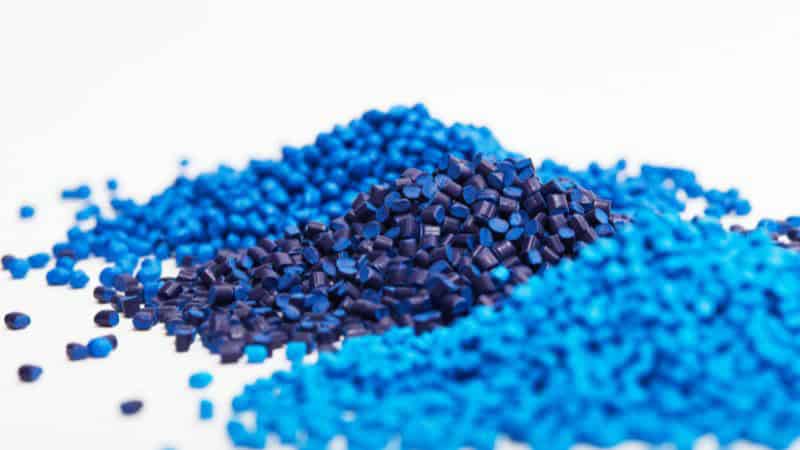
Thermoplastics and thermosets differ significantly in their properties and performance characteristics:
Mechanical Properties
- Strength -Thermosets generally offer superior strength and durability compared to thermoplastics. They’re often used in demanding applications where materials must withstand high stress without deforming. Meanwhile, thermoplastics like polypropylene boast a high strength-to-weight ratio, which makes them strong enough for many uses while being lightweight.
Property | Thermoplastics | Thermosets |
---|---|---|
Hardness | Lower | Higher |
Stiffness | Lower | Higher |
Toughness | Higher | More brittle |
Elasticity and Flexibility
Thermoplastics are typically more flexible and elastic than thermosets. For example, thermoplastics such as polystyrene can bend and stretch, making them ideal for products that require some give. This elasticity is due to their lower melting points, which allow them to be reheated and reshaped as needed.
Dimensional Stability and Tolerance
Thermosets excel in dimensional stability—you won’t see them changing shape or dimensions easily under heat or during curing. Their structure once set is rock solid. For precision parts where tolerances are tight, this is a huge advantage. Thermoplastics also have good dimensional stability, but they can warp if not processed correctly.
Shrinkage and Creep Behavior
You’ll observe that thermoplastics tend to shrink somewhat as they cool down from molding processes. On the other hand, thermosets have minimal shrinkage thanks to their cross-linked structure. Over the long term, thermoplastics can creep or deform under constant stress, whereas thermosets maintain their form steadfastly, giving them better impact resistance over time.
Effects of Microstructure
- Crystallinity impacts properties of semi-crystalline thermoplastics
- Cross-link density affects the thermal stability of thermosets
- Porosity and defects degrade mechanical performance
High-Temperature Behavior
- Most thermoplastics soften near 150-200°C
- Thermosets retain properties up to 300-400°C
- Oxidation and corrosion resistance important
Recycling and Sustainability
- Thermoplastics are recyclable
- Thermosets form cross-linked networks and cannot be reprocessed
Applications and Industry Use
Thermoplastics and thermosets are used across various industries owing to differences in their properties and cost economics:
Industry-wise Applications
Some major application areas:
- Automotive: Interior parts, under-the-hood components
- Aerospace: Airframe structures, engine components
- Construction: Pipes, coatings, adhesives
- Electronics: Printed circuit boards, connectors
Industry | Thermoplastics Use | Thermosets Use |
---|---|---|
Consumer goods | Toys, housewares | Adhesives, coatings |
Medical devices | Flexible tubing, implants | Epoxy encapsulants |
Oil and gas | Valves, seals | Pipe coatings |
Composites and Precursors
- C/C-SiC composites made using phenolic resin and other thermosets as precursors
- Carbon fiber and glass fiber reinforced plastics using epoxy matrices
Cost Economics
While thermoplastics have higher raw material costs, thermoset processing can be more complex and expensive. Lifecycle cost analysis is important to determine the optimal material choice.
Current Research Trends of Thermoset Plastics And Thermoplastics
Ongoing research is focused on further improving thermoplastics and thermoset plastic, as well as comparing their potential for different applications:
Thermoset Precursor Development
- Evaluating new phenolic resins and other polymers as carbon fiber and carbon-carbon (C/C) precursors
- Tailoring precursor properties for optimized composite performance
Processing Method Improvements
- Optimizing injection molding parameters to minimize weld line defects
- Developing high speed and precision additive manufacturing techniques
Microstructure-Property Relations
- Elucidating links between crystallinity, cross-link density and ultimate mechanical properties
- Strategies to reduce porosity and improve interfacial strength
Comparative Assessment
- Techno-economic analyses to determine the optimal material choice
- Lifecycle assessment models considering sustainability metrics
- Decision matrices ranking materials based on key criteria
Criteria | Weight | Thermosets | Thermoplastics |
---|---|---|---|
Cost | High | 2 | 4 |
Performance | High | 4 | 3 |
Manufacturability | Medium | 3 | 4 |
Future Outlook of Thermoplastics and Thermosetting Plastics?
Ongoing advances in materials and manufacturing will shape the future landscape for thermoplastics and thermosets:
Thermoplastic Precursors
- New engineered thermoplastic precursors for composites manufacturing
- Leverage recyclability while retaining high mechanical performance
Hybrid Systems
- Blends and composites to optimize properties
- Examples include thermoplastic toughened epoxies
Additive Manufacturing
- High speed 3D printing of end-use thermoplastic parts
- Overcomes limitations in geometrical complexity
Sustainable Processing
- Shift towards bio-based and CO2-reduced production
- Adoption of Industry 4.0 principles
Trend | Implications |
---|---|
Lightweighting | Increased use of high performance composites |
Mass customization | Leveraging additive manufacturing |
Sustainability | Recyclable and eco-friendly materials |
Overall, synergistic utilization of thermoplastics and thermosets will enable developing high-performance and sustainable engineered systems.
In summary, thermoplastics and thermosets differ significantly in how they are formed and how they respond to heat. Thermoplastics can be repeatedly softened with heat and hardened with cooling, allowing them to be reshaped and recycled more easily. Thermosets on the other hand undergo an irreversible chemical reaction when cured, meaning they hold their shape permanently but cannot be remelted or remolded. Knowing the properties of thermoplastics versus thermosets is important for engineers and manufacturers to select the right plastic material for different product requirements and end-of-life considerations.