Magnesium Die Casting
Magnesium Die Casting Service
Magnesium is an exceptional material for die casting due to its lightweight properties, corrosion resistance, and strength. Our capabilities make it possible to produce thin-wall castings to tight tolerances and smooth finishes, ideal for applications where weight reduction or corrosion resistance is critical.
At Moldie, we cast a variety of magnesium alloys including AZ91D, AM60B, and ZE41A. Our qualified metallurgists closely monitor each melt to ensure chemical composition is within specifications for optimum mechanical performance. We can accommodate small to high volume production runs while maintaining quick turnarounds.
Every step of the process from tooling design to final inspection is done in-house at our ISO-certified facility. We utilize state-of-the-art die casting machines and perform first article inspections as well as dimensional reports per your requirements. Please contact us to learn more about our magnesium die casting expertise and how we can deliver high-quality components to meet your exact needs.
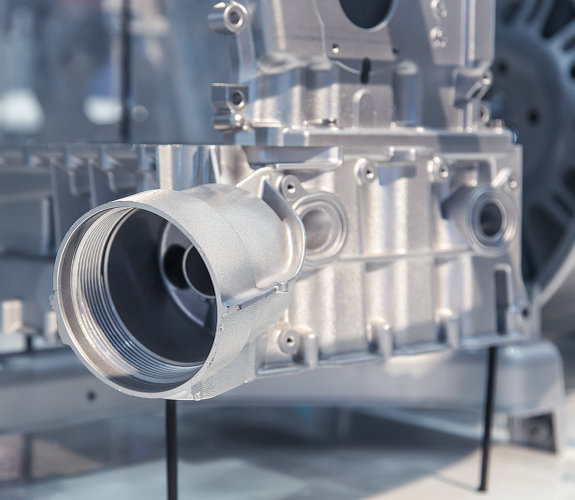
Request a Quote
Magnesium Die Casting Overview
When you’re looking into die casting processes, you’ll find magnesium die casting stands out for its ability to create strong, stable, yet lightweight components. This method involves melting down magnesium alloys and then injecting the molten metal into a die, similar to a mold, under high pressure.
Why go for magnesium? Well, apart from being the lightest of all the structural metals, it brings a stellar strength-to-weight ratio to the table. That’s a fancy way of saying that your parts will be tough without weighing down your final product.
Plus, check out the stability of magnesium alloys—these are rigid and robust enough to take on significant stress without breaking a sweat. They’re perfect when you need parts that are going to be part of something that moves or shakes a lot, like in cars or airplanes.
Here’s a quick breakdown:
- Lightweight: Magnesium is your go-to for parts that need to be as light as possible.
- High Pressure: That’s how the molten magnesium gets into every nook of the die.
- Solidification: Once in the die, the metal cools down, takes shape, and becomes a solid part.
So, if you’re aiming to produce something on the lighter side but don’t want to compromise on strength or stability, magnesium alloys in die casting could very well be your match made in manufacturing heaven.
Die Casting Process
The die casting process in manufacturing with magnesium involves handling molten metal, applying high pressure, and ensuring proper cooling. You’re going to see how each step is critical to the precision and quality of the final product.
Molten Magnesium Handling
Handling molten magnesium is delicate work. You need to heat the magnesium alloy until it’s completely molten. Since it’s a reactive metal, you’ve got to manage the temperature carefully to prevent any mishaps. The ideal temperature is dependent on the alloy composition but usually falls within a range that ensures the metal is fluid enough for casting without causing damage to the equipment or degrading the metal’s properties.
High Pressure Techniques
Once your magnesium is molten, you’ll inject it into the die using high pressure. This ensures the molten magnesium fills every nook and cranny of your mold. Typically, the pressure applied during the injection can be as high as thousands of pounds per square inch. This pressure is sustained until the magnesium starts to solidify, allowing for the creation of a detailed and accurate casting.
Solidification and Cooling
After you’ve shot the magnesium into the mold, solidification begins. The high pressure is maintained to combat any shrinkage and to ensure the integrity of the casting. The solidification process is where the metal goes from liquid to solid as it cools and takes shape. After solidification, the cooling continues until the magnesium casting is strong enough to be ejected from the die. Proper cooling is essential; it affects the mechanical properties and the overall quality of the final product.
Magnesium Alloys Used in Die Casting
When you’re looking into magnesium die casting, a few specific alloys like AZ91, AM60, and AM50 are going to come up a lot. They’ve got unique properties that make ’em stand out for different applications.
AZ91 Alloy
AZ91D is sorta the superstar of magnesium die casting alloys. It’s got a solid rep for its excellent mechanical properties and corrosion resistance. Here’s the deal with its chemical composition: it’s a mix of magnesium with 9% aluminum and 1% zinc, which is why it’s got that ‘D’ at the end – stands for die casting.
AM60 and AM50 Alloys
Now, if you need something with better ductility, then you might wanna check out AM60. It’s the go-to for parts that need a bit more flex, like automotive seat frames. On the other hand, AM50 leans towards even higher ductility and slightly less strength – great for when you need that extra give without compromising too much on toughness.
Unique Alloy Properties
What makes magnesium alloys a sweet pick for die casting is their unique properties. They’re lightweight, strong, and they’ve got superb die castability which means complex parts come out smooth and precise. This has heaps to do with their chemical composition – a thoughtful balance of magnesium with elements like aluminum and zinc.
Benefits of Magnesium Die Casting
When you’re considering materials for manufacturing components, you’ve got to give magnesium die casting a serious look. This method brings quite a few perks to the table, especially when you need parts that are both strong and light. Here’s the lowdown:
Weight Reduction Firstly, your products can shed some serious weight while maintaining strength. Magnesium is the lightest structural metal, and this can lead to major savings in both material costs and, later on, transportation.
Castability and Strength-to-Weight Ratio Your designers will thank you—magnesium’s castability is top-notch. It fills intricate molds with ease, giving you complex shapes and near net-shapes right out of the gate. Plus, the strength-to-weight ratio is fantastic, ensuring your parts can take the strain without piling on pounds.
Stability and Rigidity Don’t worry about the twists and warps; magnesium die castings offer a commendable level of dimensional stability. They hold their shape under stress and heat, which is a big deal if you want rigidity and consistent performance.
Corrosion Resistance Let’s talk durability. Magnesium holds up well against the elements, making it a choice ally for products that face tough environments.
- Cost-Effective: The efficiency of magnesium die casting can translate into lower manufacturing costs.
- Stiffness: Although light, magnesium doesn’t skimp on stiffness.
Lastly, if you’re all about that green life, you’ll be happy to know that magnesium can be recycled easily. So, your environmental footprint stays in check, too.
Design and Engineering
When you dive into the world of magnesium die casting, design and engineering form the bedrock of a successful project. It’s crucial that you have these two aspects sharply defined to transform your concept into a tangible product. Getting them right from the get-go saves you time and cost overruns.
Prototyping and Design Assistance
Your journey from idea to product kicks off with prototyping and design assistance. This crucial phase is where you test the waters with your designs. A well-equipped partner can provide practical design assistance, ensuring that your prototype is not only viable but also optimized for die casting. Prototyping should address key factors like material characteristics, dimensional tolerances, and draft angles. It’s the golden opportunity to iron out kinks in your product design before heading to mass production.
Die Construction
Moving on, the die construction phase plays a pivotal role in shaping your final product. The die is essentially your blueprint come to life in 3D. You’ll want precise engineering here—every dimension and tolerance must be spot-on, as any discrepancies in the die will be reflected in every single piece produced. It’s part science, part meticulous artistry. Here’s what you need to zone in on:
- Material Choice: Opt for materials that will stand the test of time and use.
- Dimensional Tolerance: Keep tolerances tight to ensure uniformity across products.
- Draft Angles: Just right to facilitate the ejection of the casting from the die without damaging the piece.
_Remember, the journey from design to a finished die is peppered with checks and balances that hinge on precise engineering and savvy design principles.
Automotive Applications
When you think about innovation in the automotive industry, magnesium die casting leaps out as a game-changer. Your cars are shedding weight and beefing up performance, all thanks to this nifty process.
Lightweight Components
You’re driving a revolution – not just a car. Component groups in your vehicle, like door frames and panels, undergo a transformation to magnesium die castings for their extraordinary weight-saving potential. Lighter parts mean your car doesn’t have to work as hard, giving you the twin benefits of fuel efficiency and reduced emissions – a win for both your wallet and the environment.
Structural Applications
From the floorboards beneath your feet to the framework cradling the engine, magnesium die castings are like the unsung heroes holding your car together. Because of the toughness and ductility magnesium offers, structural parts made of it can handle stress and strain without breaking a sweat. You probably wouldn’t notice this silent strength, but it’s there, keeping you safer on every trip.
Engine and Powertrain Parts
Under the hood, powertrain components cast from magnesium alloys, such as AZ91D, are doing their thing to boost your car’s power without the bulk. Your engine benefits from reduced weight, leading to better performance and can make a notable difference in how your car handles acceleration and fuel economy. Cool, right?
Mechanical and Physical Properties
You’re about to dive into what makes magnesium die casting a stand-out choice for parts where strength and durability matter a ton, even when the heat is on.
Strength and Rigidity
Magnesium die cast alloys come with an impressive combo of strength and rigidity. When you need a material that holds up without heft, this is your go-to. Its high strength-to-weight ratio means you get the brawn without the bulk—a key perk for automotive and aerospace parts looking to shed some pounds.
High-Temperature Resistance
Amidst rising temperatures, magnesium die casting alloys keep their cool, maintaining integrity under heat stress. This makes magnesium a solid pick not just for your everyday components, but also for those that’ll face the occasional heat wave, which could be anything from engine parts to high-performance gear.
Mechanical Properties
- Strength: These alloys aren’t just strong; they’re also resilient, able to resist nicks and dings that would damage lesser materials.
- Ductility: While magnesium alloys might not break stretching records, they offer a solid amount of give, so they can bend a bit when you need them to.
- Corrosion Resistance: You can also wave off worries about rust, thanks to a naturally protective oxide film that plays defense against corrosion.
Your parts crafted with magnesium die casting won’t just be tough and tolerant to high temps; they’ll keep pushing through without weighing you down or wearing out quick.
Surface Finishing and Treatment
When dealing with magnesium die casting, the final touch that counts is the surface finish. It gives your parts the desired look and protective characteristics they need to perform in the real world.
Finishing Characteristics
To get the scoop on what makes a good finish, you should know that it’s about more than just good looks. The finish on your die cast parts affects everything from how it feels in your hand to how well it machines. Typically, the choices include painting, powder coating, or plating. Each one gives your parts a unique edge—you just need to pick what’s right for your project.
Corrosion Resistance Techniques
For keeping corrosion at bay, your magnesium parts need a solid defense. There are two main heavy-hitters in this ring:
- Chemical Treatments: They prep your part’s surface, creating a stage for better adhesion of subsequent layers.
- Anodic Treatments: After chemical prepping, anodic treatments step in to beef up that anti-corrosion barrier.
Sealing and organic coatings might follow these procedures, locking down the part’s resistance to corrosive forces.
Wear Resistance
When it comes to wear resistance, it’s like giving your parts a suit of armor. The right finish can reduce the wear and tear your parts face over time. Think of:
- Physical Vapor Deposition (PVD): It’s like a shield that keeps the surface tough against abrasion.
- Thermal Spraying: Your part gets a coat that’s like chain-mail against high-temperature clashes.
Remember, the endgame of finishing isn’t just a pretty part—it’s about making your parts last longer and fight off the everyday wear they’re going to face.
Manufacturing Considerations
When it comes to magnesium die casting, your success hinges on paying close attention to a couple of critical manufacturing aspects. Nailing down your tolerances and understanding the nuances of post-processing stages, like machining and welding, can make or break the quality and efficiency of your final product.
Tolerance and Precision
Tight tolerances are key in magnesium die casting because they ensure the parts you produce fit together seamlessly and function as intended. The term dimensional accuracy refers to how closely the cast part matches its design specifications. Typically, you’re looking at tolerances that can be as precise as:
- Dimensional tolerance: 0.001 inch per inch
- Draft angle: 0.5 to 1.5 degrees
To hit these precise measurements, you’ve got to keep a sharp eye on the casting process and make sure you’re using high-purity alloys like AZ91D, which provides both excellent corrosion resistance and strength.
Machining, Welding, and Assembly
After your part comes out of the die, there’s a good chance you’ll need some additional work to get it just right.
- Machining: Sometimes, you can’t get the precision you need straight from the die. Machining lets you fine-tune your parts to the right size and shape. But remember, extra machining adds to your welding and assembly costs.
- Welding and Assembly: If you’ve got multiple components coming together, how you join them is as crucial as the cast itself. Good welding and assembly practices reduce material waste and increase structural integrity.
- Trimming: Since you’re dealing with magnesium, any excess material (often called scrap material) can typically be recycled, which helps keep your costs down.
Remember, every additional step must be carefully planned to avoid unnecessary costs and material waste.
Performance in Electrical and Thermal Environments
When you’re dealing with magnesium alloys in your projects, especially in high-pressure die castings, it’s key to understand their performance under various conditions. Let’s look at how they hold up in electrical and thermal environments.
Thermal Properties
Your magnesium alloy parts are quite the performers when it comes to heat dissipation. Due to their superior thermal conductivity, these materials are chosen for applications where keeping cool is crucial. Magnesium alloys typically have a thermal conductivity in the range of 51 to 96 W/mK, which makes them better at transferring heat compared to many other metals.
Electrical Conductivity
For your electrical applications, magnesium alloys offer reasonable electrical conductivity. They are not as conductive as copper, of course, but with a conductivity around 22.7 MS/m, they’re still useful for certain electrical applications. What’s more, you get good electromagnetic shielding. The inherent properties of magnesium alloys allow them to block out unwanted electromagnetic interference, keeping your sensitive electronic devices safe and sound.
Comparing Magnesium to Other Metals
When you’re picking out materials for your project, knowing the perks and quirks of magnesium compared to other metals can save you time and cash. Let’s break down how it stacks up.
Magnesium vs. Aluminum
Magnesium is the featherweight champ in the metal world, so it’s lighter than aluminum. If you’re looking to shave off weight from your product, magnesium could be your go-to. On the flip side, aluminum is often less pricey and still packs a punch with durability, so it can give you some cost savings if your budget’s tight. Check out this quick comparison:
Property | Magnesium | Aluminum |
---|---|---|
Weight | Lighter | Heavier |
Cost | Generally Higher | Generally Lower |
Durability | High | Higher |
Casting Technique | Hot chamber machine | Cold chamber machine |
Magnesium vs. Steel
Steel’s a heavy-duty player with knockout strength, but magnesium is no slouch either. It’s about 75% lighter than steel, which can be a game-changer if you’re aiming to cut weight. But don’t count on the same kind of cost savings here—steel often comes in cheaper, making it a solid choice for your wallet when weight’s not a worry.
Magnesium vs. Zinc
Zinc’s a tough cookie with a rep for high precision and extending the life of casting tools—which can mean cost savings in the long run. But if your parts need to be lighter, magnesium’s your ally; it has a lower density than zinc. Remember though, magnesium can cost a bit more, but it’s worth considering for its blend of strength and lightweight charm. Here are the highlights:
Property | Magnesium | Zinc |
---|---|---|
Weight | Lighter | Heavier |
Cost | More Expensive | Less Expensive |
Precision | High | Higher |
Tool Life | Shorter | Longer |
Each metal has its own set of pros and cons, so your choice really boils down to what’s crucial for you—be it sticking to a budget, cutting weight, or going for gold in durability and precision.
Applications Beyond Automotive
While you might be well-versed with magnesium die casting in car parts, it’s not all about engines and chassis. Dive into other industries, and you’ll find surprising uses for this lightweight metal.
Electronic Housing
In the realm of electronics, magnesium die casting is a game-changer for housing components. It’s not just about the sleek finish; its superior thermal conductivity makes it ideal to protect your gadgets from overheating. Lightweight yet sturdy, it’s perfect for your laptops, smartphones, and even camera bodies. With die-cast magnesium, manufacturers give you portability without compromising on durability.
Medical Equipment
Now, let’s talk medical gears. Magnesium die casting is a big win for medical components — think surgical tools, device housings, and instrument panels. You want your medical devices to be both strong and light, especially if you’re wheeling equipment around or holding devices for long surgeries. Plus, the biocompatibility of magnesium die casting means it’s safe for those countless life-saving applications it forms a part of.
Eco-Friendly Aspects of Magnesium Castings
Magnesium castings offer a sustainable option in materials technology, pairing lightweight characteristics with impressive eco-friendly credentials, particularly when it comes to recycling and environmental impact.
Recyclability and Environmental Impact
Recyclability: You’ll find magnesium to be highly recyclable. The recycling process for magnesium castings doesn’t degrade its properties, which means it maintains its quality through multiple cycles of use and reuse. This ensures that the material can serve many lifespans, reducing the need for raw extraction and processing.
- Process: The steps in recycling magnesium are straightforward. Whether from post-consumer scrap or manufacturing remnants, magnesium castings can be melted down, purified, and remade into new products without significant material loss.
- Energy efficiency: Compared to primary production, recycling magnesium requires significantly less energy, approximately only 5% of the energy needed to produce new magnesium from ore. This contributes to a reduction in carbon emissions, making it a friendlier choice for the environment.
Environmental Impact: Your choice of magnesium for castings has a lesser environmental footprint. Magnesium is the lightest structural metal, which means it’s a great candidate for reducing weight in transportation and, consequently, improving fuel efficiency. Additionally, magnesium is abundant and its extraction impact is less intensive compared to other metals, like titanium. This positions magnesium as a forward-thinking, eco-conscious material for diverse applications.
Magnesium Die Casting for Complex Parts
When you’re looking to produce parts with complex shapes and intricate details, magnesium die casting is a game-changer for you. This process is like a superhero for metals, swooping in to save the day with its ability to create net shape parts—meaning they need little to no post-casting machining. Isn’t that a time and cost saver for you?
Here’s a quick look at why magnesium die casting is the go-to for complex parts:
- Precision: You can achieve exceptional detail and precision, matching your design specs to the T.
- Strength-to-Weight Ratio: Magnesium parts are strong yet lightweight, so your parts won’t weigh you down.
- Efficiency: Producing net shape parts directly from the mold reduces waste and speeds up production.
By injecting molten magnesium into a die at high pressure, you get parts that not only meet design criteria but may also boast improved properties. Think of it as the process turning the heat up to get your parts just right, with better properties like impact and wear resistance.
The casting process includes a few steps:
- The die is prepped and closed.
- Molten magnesium is shot into the die.
- The metal solidifies quickly, thanks to magnesium’s high thermal conductivity.
- The part is ejected, and voilà—you’ve got your complex shape!
But remember, while magnesium is fantastic for complex parts, it’s always smart to chat with a casting expert to ensure it’s the right fit for your specific part needs.
Cost Considerations in Magnesium Die Casting
When you’re looking into magnesium die casting, the price tag can vary widely. Your expenses generally fall into two main categories: Capital Costs, which include the initial setup and equipment, and Production and Material Costs, which cover the ongoing expenses. Let’s break those down.
Capital Costs
Your initial investment for magnesium die casting primarily encompasses buying or creating molds. These molds are like the blueprint, dictating the final product’s shape and size. Here’s what you should know about the capital costs:
- Mold Design and Complexity: The more intricate your product, the more costly the mold. Simple designs save you money.
- Mold Material: High-grade steel molds are pricey, but they last longer, which could save you cash in long runs.
Production and Material Costs
Once you’ve got your molds, you’ll encounter ongoing costs for each batch of parts:
- Material Costs: Magnesium is cost-effective due to its abundant supply, and its price fluctuates based on market conditions. Keep an eye on material prices as they can significantly impact your production costs.
- Production Volume: Higher volumes typically mean lower costs per piece. So, if you can, go big with your order.
- Assembly Costs: After casting, it’s time to put everything together. Complex assemblies that require additional hardware or labor can add to your bill.
- Energy Use: Remember, die casting involves melting metal, and that takes a lot of heat – and in turn, energy. The more energy-efficient your process is, the lower your bills will be.
Your goal is to find a sweet spot where your capital costs are justified by your production volumes and your material costs don’t skyrocket. Keep these considerations in mind, and magnesium die casting can be a very financially savvy choice for your manufacturing needs.