The die casting industry primarily encompasses aluminum and zinc alloys die casting, which has seen significant utilization in recent years. Understanding the differences between zinc and aluminum is crucial for selecting the appropriate material for specific purposes and optimizing their utilization.
This article will delve into the key characteristics that differentiate zinc and aluminum, shedding light on their distinctive properties, uses, and considerations for practical applications.
What are Zinc and Aluminum?
Zinc and aluminum are different metals with unique characteristics. Zinc is a soft, silvery-white metal that finds application in various fields, including galvanizing steel for corrosion protection, die-casting, and brass production.
Aluminum is a lightweight and sturdy metal used in diverse applications such as aircraft construction, beverage cans, and window frames.
Zinc and aluminum can be combined to form various alloys with distinct properties.
What is Zinc Alloy?
Zinc alloy refers to a metal alloy composed primarily of zinc, along with other metallic elements. The common elements used in zinc alloy include aluminum, magnesium, copper, cadmium, lead, titanium, and other low-temperature zinc alloys. Zinc alloys are prepared by melting the constituents and processing them through die-casting or other pressure-shaping methods to obtain the desired material form.
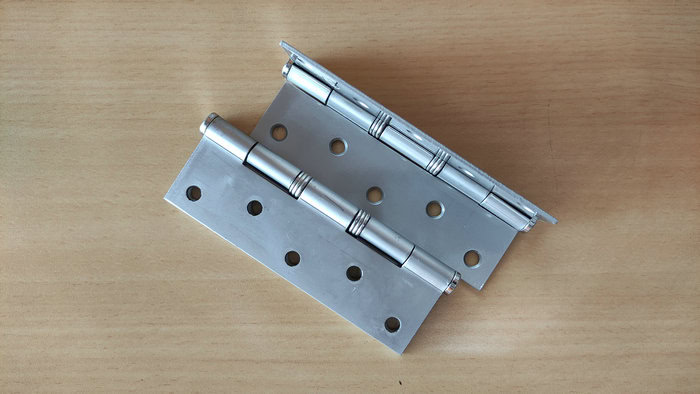
Zinc alloys can be classified into cast and deformed, depending on the manufacturing process employed. They find application in various industries, such as die-casting for instruments and automotive parts as well as hot-dip galvanizing treatment for boiler water wall pipes to enhance high-temperature corrosion resistance.
Features of zinc alloy
- It has excellent casting performance, enabling the production of intricate and thin-walled precision parts with a smooth surface finish.
- Enables surface treatment options such as electroplating, spraying, painting, polishing, and grinding.
- During the melting and die-casting processes, it doesn’t absorb iron, resists pressure corrosion, and does not adhere to molds.
- Possesses favorable mechanical properties and offers wear resistance at ambient temperatures.
- Boasts a low melting point of 385℃, facilitating easy die casting.
What is Aluminum Alloy?
Aluminum alloy refers to a category of alloys based on aluminum. It incorporates various primary alloying elements such as copper, silicon, magnesium, zinc, and manganese and secondary alloying elements like nickel, iron, titanium, chromium, and lithium.
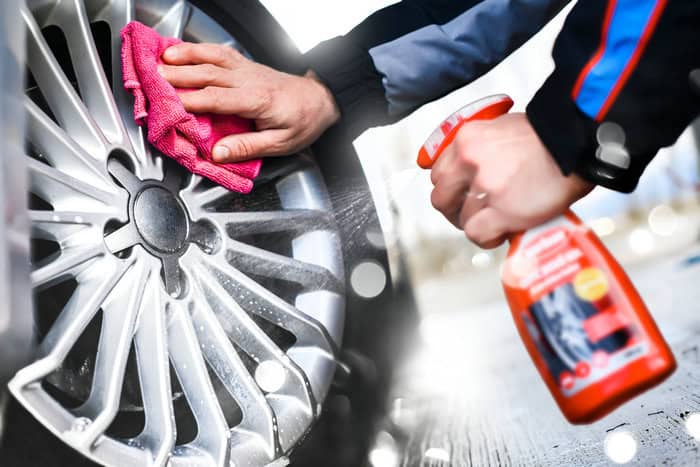
In terms of density, aluminum alloy possesses lower density than steel. And regarding strength, in general, steel is stronger than aluminum. However, once the lighter weight of aluminum is factored into the equation, aluminum comes out on top with a superior strength-to-weight ratio. Some aluminum alloys are stronger than steel. It offers excellent plasticity and can be processed into diverse profiles, making it a widely used non-ferrous metal structural material across various industries. Its applications span aviation, aerospace, automobile manufacturing, machinery production, shipbuilding, and the chemical industry.
Features of aluminum alloy
- Lightweight making it ideal for industries where weight reduction is critical.
- Excellent thermal conductivity.
- Environmentally friendly composition.
- Resistant to low temperatures.
- Ability to achieve favorable mechanical properties, physical characteristics, and corrosion resistance through heat treatment.
- High strength properties.
Differences Between Zinc And Aluminum Alloy
Material
Zinc alloy material has a significant specific gravity and exhibits excellent casting performance. It boasts high density and strength, comparable to or even surpassing that of high-quality steel. As a result, zinc alloy die casting parts typically weigh more than aluminum alloy die casting parts.
Property
The zinc alloy material exhibits a low melting point, favorable mechanical properties, and wear resistance. It is also suitable for surface treatment applications. On the other hand, aluminum alloy demonstrates excellent electrical conductivity, thermal conductivity, and corrosion resistance.
Die casting process
The melting points of zinc and aluminum alloys vary. Zinc alloys have a lower melting point compared to aluminum alloys. This discrepancy in melting points necessitates using special processing equipment and parameters when die casting.
Zinc alloy die casting commonly employs a hot chamber die casting machine. The zinc alloy is melted within this machine, enabling faster cycle times.
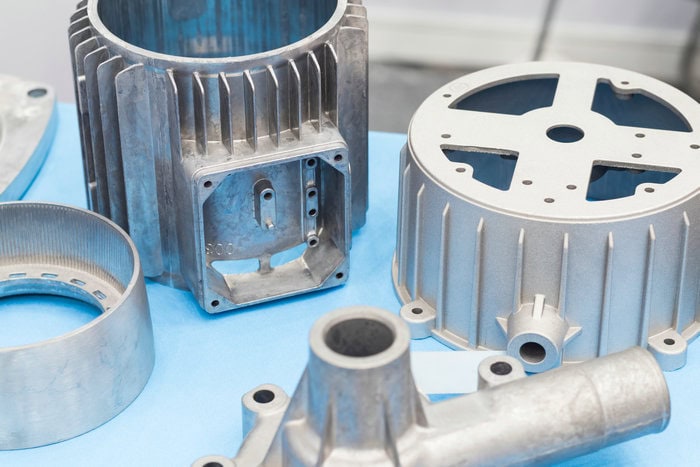
In contrast, aluminum alloy die casting utilizes a cold chamber die casting machine. The aluminum alloy is melted outside the machine and then poured into the injection machine. This process takes longer compared to hot chamber die casting.
The utilization of different processing equipment and parameters for zinc alloy die casting and aluminum alloy die casting leads to divergent properties in the finished products. Zinc alloy die castings tend to be more durable and corrosion-resistant than their aluminum counterparts. Conversely, aluminum alloy die castings are typically lighter and possess better thermal conductivity.
Weight
In terms of weight, zinc alloy is generally denser and heavier than aluminum.Pure zinc has a specific density of 5g/cm3, while aluminum has a lower density of 2.7g/cm3. This higher density contributes to zinc alloys’ superior impact resistance compared to aluminum parts, making them a preferred material for manufacturing castings intended for structural applications.
Properties
Here are the common properties of both die-cast materials and how they distinguish from each other:
- Melting Point
Zinc has a lower melting point (around 420°C) than aluminum. The melting point is a crucial factor in die casting, influencing the choice of the casting process. Zinc’s lower melting point makes it compatible with the hot chamber process.
This characteristic offers advantages such as reduced production costs, improved production efficiency, and a lower risk of mold degradation. Conversely, aluminum has a higher melting point (around 660°C), making it suitable for the cold chamber process.
- Thermal Conductivity
Zinc alloy exhibits superior thermal conductivity compared to aluminum die casting. It effectively absorbs and dissipates heat, making it suitable for applications involving high heat generation or heat dissipation requirements. Zinc castings are particularly beneficial in producing components like heat sinks or electronics.
- Corrosion Resistance
Zinc castings possess excellent corrosion resistance, surpassing aluminum die-casted parts.This property makes zinc more suitable for projects in harsh environmental conditions where corrosion protection is essential.
Surface Finishing
Die castings typically require secondary surface finishing treatments, unlike CNC machined parts. The need for surface finishing is influenced by the casting process and the type of material used.
Zinc castings exhibit a smoother and more patterned surface after casting, as they don’t have pores. In contrast, aluminum castings can develop pores, pits, and blisters during casting, necessitating compensatory surface finishing.
Both zinc and aluminum castings can benefit from surface finishing processes. However, zinc is more compatible with a broader range of surface finishing options, including plating, powder coating, painting, electroplating, and anodizing.
Tooling Life
The molds employed in zinc die casting don’t require high tensile strength due to the material’s less abrasive nature and low melting point. These properties result in reduced mold damage and lower tooling costs. Consequently, molds used in zinc casting can withstand over 1,000,000 shots before requiring replacement, whereas molds used in aluminum casting typically last around 100,000 shots.
Applications
Both zinc and aluminum castings find applications in various industries. Zinc casting is known for its strength, making it a popular choice for home appliances and automotive die casting.
On the other hand, aluminum casting excels in its strength-to-weight ratio, making it ideal for lightweight yet robust components. This characteristic makes aluminum castings particularly valuable in the aerospace industry, where the need for lightweight materials is crucial.
Cycle Time
The cycle time is significant when comparing aluminum die casting to zinc die casting. Zinc die casting occurs at a high pressure and low melting point, distinguishing it from aluminum die casting. Consequently, zinc die casting exhibits a shorter cycle time, typically 150-200% faster than aluminum casting.
Additionally, the heating process for zinc die casting occurs internally, unlike aluminum die casting, which employs the cold chamber process. Furthermore, zinc casting’s efficient heat dissipation enables faster solidification of the molten metal, contributing to a further reduction in cycle time.
Costs
The cost of die casting production is affected by various factors, including material choice, production process, operator skill, cycle time, and surface finishing. Zinc die castings made from zinc alloys are less expensive but have lower strength and corrosion resistance compared to aluminum alloys. Aluminum die castings are stronger and more corrosion-resistant but come at a higher cost.
The production process involves melting the metal, injecting it into a mold, and cooling it to form the final part. Skilled operators and shorter cycle times can reduce costs. Also, surface finishing, such as painting or plating, adds to the overall cost. Generally, zinc die castings are more cost-effective than aluminum die castings.
When and Why You Should Choose Zinc Die Casting
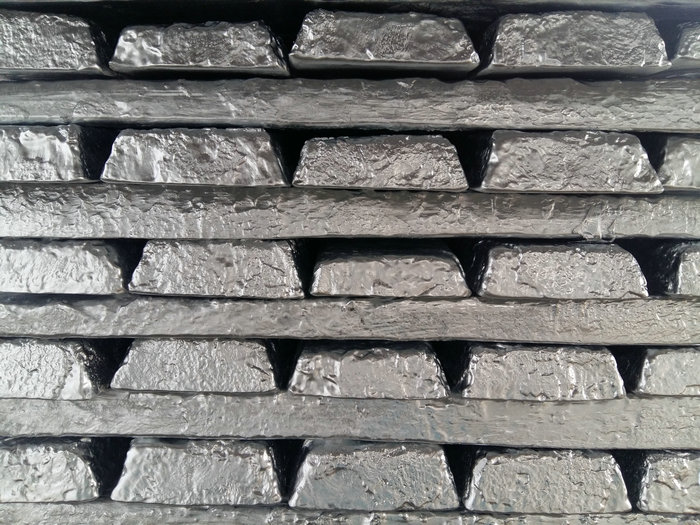
When faced with the dilemma of choosing between zinc die casting and aluminum die casting, consider the following factors that make zinc die casting the preferred option
Parts with Thin Walls
Zinc die casting is well-suited for producing parts with thin walls due to its strength compared to other materials. The dense nature of zinc ensures structural integrity and stability, reducing material usage and die-casting costs.
Harsh Environmental Conditions
Zinc die casting excels in harsh environmental conditions, particularly those prone to corrosion. Its exceptional corrosion resistance forms a protective layer on the parts when exposed to such conditions.
Lesser Residual Stress
Die casting involves applying pressure to inject molten metal into the die. High-pressure die casting can lead to residual stress on parts, but zinc die casting, which utilizes low-pressure die casting, minimizes residual stress.
Die cast mold
Choosing zinc die casting is advantageous if you are working with delicate die casting molds. Zinc die casting molds can last approximately ten times longer than aluminum die-casting molds.
Faster Production
Zinc alloys have a low melting point, enabling a hot chamber die-casting process with high-pressure injection. This results in a higher cycle rate compared to other materials.Unlike in aluminum die casting where the operator melts the aluminum outside the machine before pouring it into the injection machine, in zinc die casting, the zinc is melted within the machine
By considering these factors, zinc die casting can be a preferred choice in various scenarios.
Why and When Choose Aluminum Die Casting
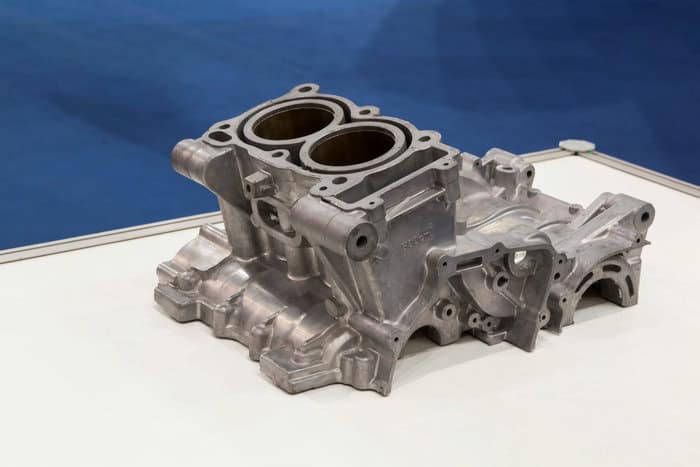
When faced with the decision between aluminum vs zinc die casting parts, there are certain conditions where aluminum die casting should be given preference. Consider the following factors:
Strength-to-weight ratio
If you’re seeking lightweight and high tensile strength properties, it’s advisable to consider aluminum die casted parts. These parts are well-known for their ability to offer both characteristics. Notably, the aerospace industry widely utilizes die cast parts made from aluminum due to their lightweight nature.
High operating temperatures
Due to their high melting point and ability to withstand high temperatures, aluminum die castings are the favored option for applications that involve elevated operating temperatures, such as in metallurgical processes. This characteristic ensures that the structural and physical properties of the castings remain intact even when exposed to extreme heat.
Electrical conductivity
Due to their excellent electrical conductivity, aluminum die castings are the preferred choice for various electronic components in die casting. This is particularly important in applications such as EMI shielding, where parts must be protected from electromagnetic signals.
Get Your Zinc or Aluminum Die Casting Parts
Are you in need of high-quality zinc or aluminum die casting parts? Look no further! Moldie is here to fulfill all your die casting requirements with precision, efficiency, and top-notch quality. It’s your one-stop solution for Zinc and Aluminum Die Casting Parts!
We specialize in providing exceptional die casting services for both zinc and aluminum alloys, catering to a wide range of industries and applications.
Whether you need lightweight and strong aluminum parts or corrosion-resistant zinc components, we have got you covered. Our ethical die-casting procedures involve using the best raw materials and house capabilities to deliver outstanding results when you order from us in bulk. Visit our website for more information.
Conclusion
Zinc and aluminum have distinct characteristics that make them suitable for different applications. Zinc offers advantages such as high density, corrosion resistance, and low melting point, while aluminum provides lightweight, high strength, and superior thermal conductivity. Understanding these differences allows for informed material selection in various industries and projects.
FAQs
Are zinc die casts stronger than aluminum die castings?
Zinc die casting parts exhibit greater strength compared to aluminum die casting. Experts assert that zinc die casting surpasses several common non-ferrous alloys in strength. Zinc alloys are reported to be 2.5 times stronger than aluminum die casting.
What are the parameters that differentiate aluminum and zinc castings?
The weight, corrosion resistance, melting point, and thermal conductivity distinguish the two castings. Zinc casting is characterized by its higher weight, lower melting point, superior corrosion resistance, and better thermal conductivity compared to the others.
Which is more corrosion-resistant: zinc or aluminum?
Aluminum die casting parts exhibit lower corrosion resistance than zinc casting, although this may vary depending on the pH level. For instance, in alkaline solutions with a pH of 11, the corrosion resistance of aluminum casting is equivalent to that of zinc.