L'industrie du moulage sous pression englobe principalement le moulage sous pression d'alliages d'aluminium et de zinc, qui a connu une utilisation importante ces dernières années. Comprendre les différences entre le zinc et l'aluminium est crucial pour sélectionner le matériau approprié à des fins spécifiques et optimiser leur utilisation.
Cet article examinera les principales caractéristiques qui différencient le zinc et l'aluminium, mettant en lumière leurs propriétés distinctives, leurs utilisations et leurs considérations pour les applications pratiques.
Que sont le zinc et l’aluminium ?
Le zinc et l’aluminium sont des métaux différents aux caractéristiques uniques. Le zinc est un métal tendre, blanc argenté, qui trouve des applications dans divers domaines, notamment la galvanisation de l'acier pour la protection contre la corrosion, le moulage sous pression et la production de laiton.
L'aluminium est un métal léger et robuste utilisé dans diverses applications telles que la construction aéronautique, les canettes de boissons et les cadres de fenêtres.
Le zinc et l’aluminium peuvent être combinés pour former divers alliages aux propriétés distinctes.
Qu'est-ce que l'alliage de zinc ?
L'alliage de zinc fait référence à un alliage métallique composé principalement de zinc et d'autres éléments métalliques. Les éléments courants utilisés dans les alliages de zinc comprennent l'aluminium, le magnésium, le cuivre, le cadmium, le plomb, le titane et d'autres alliages de zinc à basse température. Les alliages de zinc sont préparés en faisant fondre les constituants et en les traitant par moulage sous pression ou par d'autres méthodes de mise en forme sous pression pour obtenir la forme de matériau souhaitée.
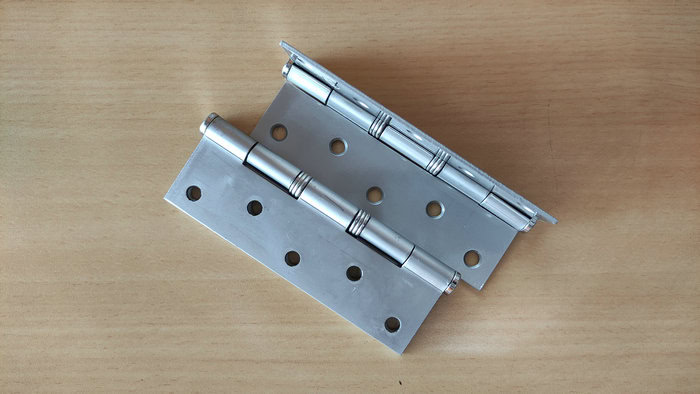
Les alliages de zinc peuvent être classés en alliages coulés et déformés, en fonction du procédé de fabrication utilisé. Ils trouvent des applications dans diverses industries, telles que le moulage sous pression d'instruments et de pièces automobiles, ainsi que le traitement de galvanisation à chaud pour les tuyaux des parois d'eau des chaudières afin d'améliorer la résistance à la corrosion à haute température.
Caractéristiques de l'alliage de zinc
- Il présente d'excellentes performances de moulage, permettant la production de pièces de précision complexes et à parois minces avec une finition de surface lisse.
- Permet des options de traitement de surface telles que la galvanoplastie, la pulvérisation, la peinture, le polissage et le meulage.
- Pendant les processus de fusion et de moulage sous pression, il n'absorbe pas le fer, résiste à la corrosion sous pression et n'adhère pas aux moules.
- Possède des propriétés mécaniques favorables et offre une résistance à l'usure à température ambiante.
- Possède un faible point de fusion de 385 ℃, facilitant le moulage sous pression.
Qu’est-ce que l’alliage d’aluminium ?
L'alliage d'aluminium fait référence à une catégorie d'alliages à base d'aluminium. Il incorpore divers éléments d'alliage primaires tels que le cuivre, le silicium, le magnésium, le zinc et le manganèse et des éléments d'alliage secondaires comme le nickel, le fer, le titane, le chrome et le lithium.
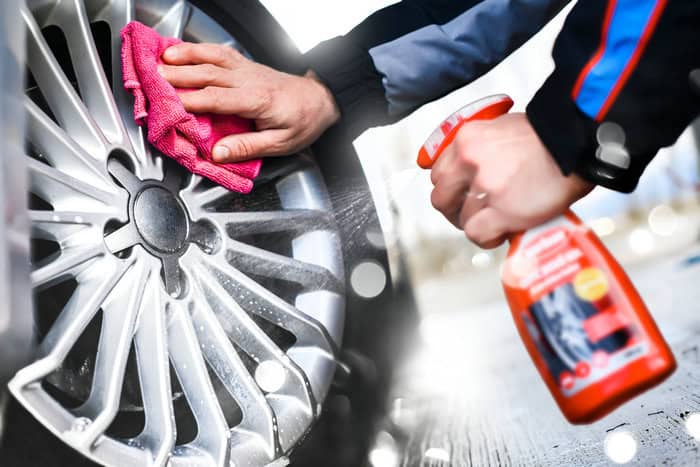
En termes de densité, l'alliage d'aluminium possède une densité inférieure à celle de l'acier. Et concernant la résistance, en général, l’acier est plus résistant que l’aluminium. Cependant, une fois que le poids plus léger de l’aluminium est pris en compte dans l’équation, l’aluminium arrive en tête avec un rapport résistance/poids supérieur. Certains alliages d'aluminium sont plus résistants que l'acier. Il offre une excellente plasticité et peut être transformé en divers profils, ce qui en fait un matériau de structure en métal non ferreux largement utilisé dans diverses industries. Ses applications couvrent l'aviation, l'aérospatiale, la construction automobile, la production de machines, la construction navale et l'industrie chimique.
Caractéristiques de l'alliage d'aluminium
- Léger, ce qui le rend idéal pour les industries où la réduction de poids est essentielle.
- Excellente conductivité thermique.
- Composition respectueuse de l'environnement.
- Résistant aux basses températures.
- Capacité à obtenir des propriétés mécaniques, des caractéristiques physiques et une résistance à la corrosion favorables grâce à un traitement thermique.
- Propriétés de haute résistance.
Différences entre le zinc et l’alliage d’aluminium
Matériel
Le matériau en alliage de zinc a une densité spécifique significative et présente d'excellentes performances de coulée. Il présente une densité et une résistance élevées, comparables, voire supérieures, à celles de l'acier de haute qualité. En conséquence, les pièces moulées sous pression en alliage de zinc pèsent généralement plus que les pièces moulées sous pression en alliage d’aluminium.
Propriété
Le matériau en alliage de zinc présente un faible point de fusion, des propriétés mécaniques favorables et une résistance à l'usure. Il convient également aux applications de traitement de surface. D'autre part, l'alliage d'aluminium présente une excellente conductivité électrique, conductivité thermique et résistance à la corrosion.
Processus de moulage sous pression
Les points de fusion des alliages de zinc et d’aluminium varient. Les alliages de zinc ont un point de fusion plus bas que les alliages d'aluminium. Cet écart dans les points de fusion nécessite l’utilisation d’équipements et de paramètres de traitement spéciaux lors du moulage sous pression.
Le moulage sous pression en alliage de zinc utilise généralement une machine de moulage sous pression à chambre chaude. L'alliage de zinc est fondu dans cette machine, permettant des temps de cycle plus rapides.
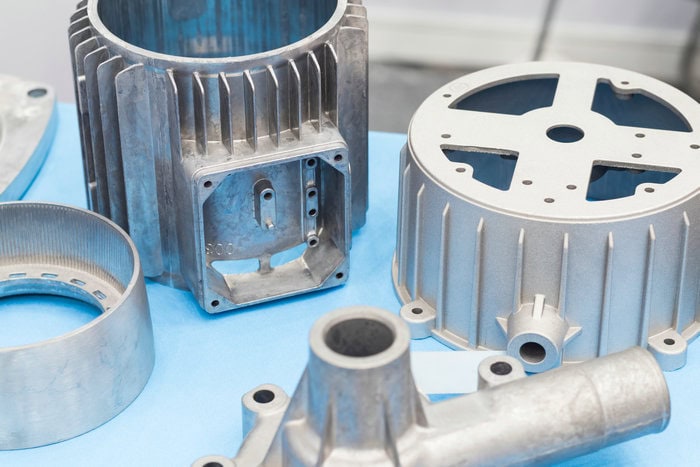
En revanche, le moulage sous pression d’alliages d’aluminium utilise une machine de moulage sous pression à chambre froide. L'alliage d'aluminium est fondu à l'extérieur de la machine puis coulé dans la machine à injecter. Ce processus prend plus de temps que le moulage sous pression en chambre chaude.
L'utilisation de différents équipements et paramètres de traitement pour le moulage sous pression en alliage de zinc et le moulage sous pression en alliage d'aluminium conduit à des propriétés divergentes dans les produits finis. Les pièces moulées sous pression en alliage de zinc ont tendance à être plus durables et résistantes à la corrosion que leurs homologues en aluminium. À l’inverse, les pièces moulées sous pression en alliage d’aluminium sont généralement plus légères et possèdent une meilleure conductivité thermique.
Poids
En termes de poids, l'alliage de zinc est généralement plus dense et plus lourd que l'aluminium. Le zinc pur a une densité spécifique de 5 g/cm3, tandis que l'aluminium a une densité inférieure de 2,7 g/cm3. Cette densité plus élevée contribue à la résistance aux chocs supérieure des alliages de zinc par rapport aux pièces en aluminium, ce qui en fait un matériau privilégié pour la fabrication de pièces moulées destinées à des applications structurelles.
Propriétés
Voici les propriétés communes des deux matériaux moulés sous pression et comment ils se distinguent les uns des autres :
- Point de fusion
Le zinc a un point de fusion plus bas (environ 420°C) que l'aluminium. Le point de fusion est un facteur crucial dans le moulage sous pression, influençant le choix du procédé de coulée. Le point de fusion plus bas du zinc le rend compatible avec le procédé en chambre chaude.
Cette caractéristique offre des avantages tels que des coûts de production réduits, une efficacité de production améliorée et un risque moindre de dégradation des moisissures. À l’inverse, l’aluminium a un point de fusion plus élevé (environ 660°C), ce qui le rend adapté au procédé en chambre froide.
- Conductivité thermique
L'alliage de zinc présente une conductivité thermique supérieure à celle de l'aluminium moulé sous pression. Il absorbe et dissipe efficacement la chaleur, ce qui le rend adapté aux applications impliquant des exigences élevées de génération ou de dissipation thermique. Les pièces moulées en zinc sont particulièrement utiles dans la production de composants tels que des dissipateurs thermiques ou des composants électroniques.
- Résistance à la corrosion
Les pièces moulées en zinc possèdent une excellente résistance à la corrosion, surpassant les pièces moulées sous pression en aluminium. Cette propriété rend le zinc plus adapté aux projets dans des conditions environnementales difficiles où la protection contre la corrosion est essentielle.
Finition des surfaces
Les moulages sous pression nécessitent généralement des traitements de finition de surface secondaires, contrairement aux pièces usinées CNC. Le besoin de finition de surface est influencé par le processus de coulée et le type de matériau utilisé.
Les pièces moulées en zinc présentent une surface plus lisse et plus structurée après la coulée, car elles n'ont pas de pores. En revanche, les pièces moulées en aluminium peuvent développer des pores, des piqûres et des cloques pendant la coulée, nécessitant une finition de surface compensatoire.
Les pièces moulées en zinc et en aluminium peuvent bénéficier de processus de finition de surface. Cependant, le zinc est plus compatible avec une gamme plus large d’options de finition de surface, notamment le placage, le revêtement en poudre, la peinture, la galvanoplastie et l’anodisation.
Durée de vie de l'outillage
Les moules utilisés dans le moulage sous pression du zinc ne nécessitent pas une résistance à la traction élevée en raison de la nature moins abrasive du matériau et de son faible point de fusion. Ces propriétés entraînent une réduction des dommages causés par le moule et des coûts d'outillage inférieurs. Par conséquent, les moules utilisés dans la coulée de zinc peuvent résister à plus de 1 000 000 de tirs avant de devoir être remplacés, alors que les moules utilisés dans le moulage de l'aluminium durent généralement environ 100 000 tirs.
Applications
Les pièces moulées en zinc et en aluminium trouvent des applications dans diverses industries. Le moulage du zinc est connu pour sa résistance, ce qui en fait un choix populaire pour les appareils électroménagers et le moulage sous pression automobile.
D'autre part, la fonte d'aluminium excelle dans son rapport résistance/poids, ce qui la rend idéale pour les composants légers mais robustes. Cette caractéristique rend les pièces moulées en aluminium particulièrement utiles dans l’industrie aérospatiale, où le besoin de matériaux légers est crucial.
Temps d'un cycle
Le temps de cycle est important lorsque l’on compare le moulage sous pression d’aluminium au moulage sous pression de zinc. Le moulage sous pression du zinc s'effectue à une pression élevée et à un point de fusion bas, ce qui le distingue du moulage sous pression de l'aluminium. Par conséquent, le moulage sous pression du zinc présente un temps de cycle plus court, généralement 150-200% plus rapide que le moulage de l'aluminium.
De plus, le processus de chauffage pour le moulage sous pression du zinc se produit en interne, contrairement au moulage sous pression de l'aluminium, qui utilise le processus en chambre froide. De plus, la dissipation thermique efficace du moulage de zinc permet une solidification plus rapide du métal en fusion, contribuant ainsi à une réduction supplémentaire du temps de cycle.
Frais
Le coût de production du moulage sous pression dépend de divers facteurs, notamment le choix des matériaux, le processus de production, les compétences de l'opérateur, la durée du cycle et la finition de surface. Les pièces moulées sous pression en zinc fabriquées à partir d'alliages de zinc sont moins chères mais ont une résistance et une résistance à la corrosion inférieures à celles des alliages d'aluminium. Les pièces moulées sous pression en aluminium sont plus solides et plus résistantes à la corrosion, mais leur coût est plus élevé.
Le processus de production consiste à faire fondre le métal, à l’injecter dans un moule et à le refroidir pour former la pièce finale. Des opérateurs qualifiés et des temps de cycle plus courts peuvent réduire les coûts. De plus, la finition des surfaces, comme la peinture ou le placage, augmente le coût global. Généralement, les pièces moulées sous pression en zinc sont plus rentables que les pièces moulées sous pression en aluminium.
Quand et pourquoi choisir le moulage sous pression en zinc
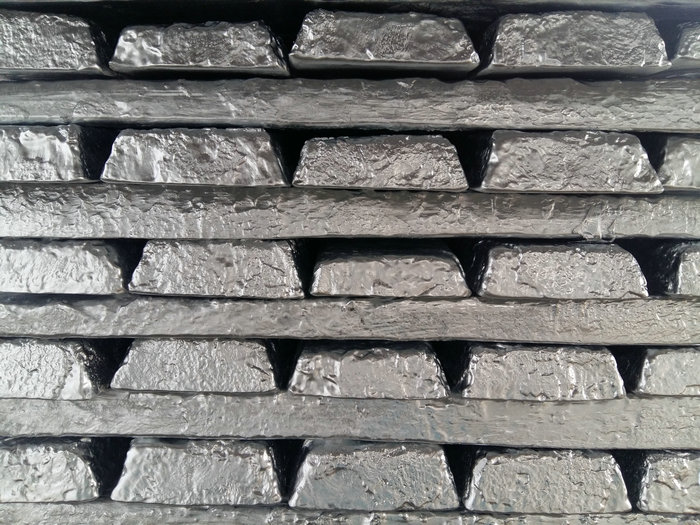
Face au dilemme de choisir entre le moulage sous pression en zinc et le moulage sous pression en aluminium, tenez compte des facteurs suivants qui font du moulage sous pression en zinc l'option privilégiée.
Pièces à parois fines
Le moulage sous pression du zinc est bien adapté à la production de pièces à parois minces en raison de sa résistance par rapport à d'autres matériaux. La nature dense du zinc garantit l’intégrité et la stabilité structurelles, réduisant ainsi l’utilisation de matériaux et les coûts de moulage sous pression.
Conditions environnementales difficiles
Le moulage sous pression du zinc excelle dans les conditions environnementales difficiles, en particulier celles sujettes à la corrosion. Sa résistance exceptionnelle à la corrosion forme une couche protectrice sur les pièces exposées à de telles conditions.
Moins de stress résiduel
Le moulage sous pression consiste à appliquer une pression pour injecter du métal en fusion dans la matrice. Le moulage sous pression à haute pression peut entraîner des contraintes résiduelles sur les pièces, mais le moulage sous pression du zinc, qui utilise le moulage sous pression à basse pression, minimise les contraintes résiduelles.
Moule moulé sous pression
Le choix du moulage sous pression en zinc est avantageux si vous travaillez avec des moules de moulage sous pression délicats. Les moules de moulage sous pression en zinc peuvent durer environ dix fois plus longtemps que les moules de moulage sous pression en aluminium.
Production plus rapide
Les alliages de zinc ont un point de fusion bas, ce qui permet un processus de moulage sous pression en chambre chaude avec injection à haute pression. Cela se traduit par un taux de cycle plus élevé par rapport aux autres matériaux. Contrairement au moulage sous pression d'aluminium où l'opérateur fait fondre l'aluminium à l'extérieur de la machine avant de le verser dans la machine d'injection, dans le moulage sous pression de zinc, le zinc est fondu dans la machine.
En tenant compte de ces facteurs, le moulage sous pression du zinc peut être un choix privilégié dans divers scénarios.
Pourquoi et quand choisir le moulage sous pression en aluminium
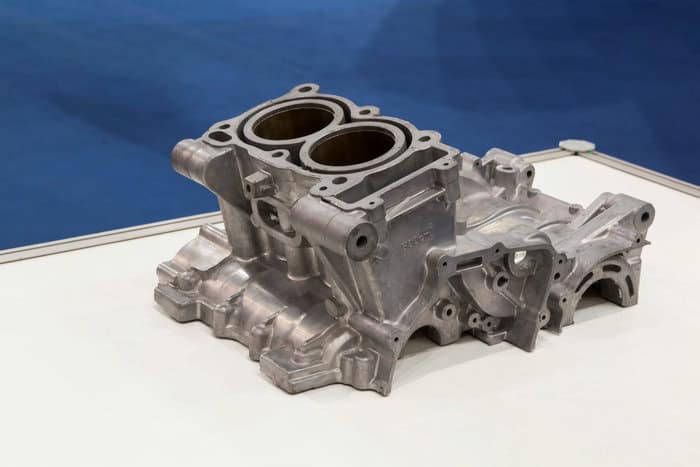
Face au choix entre des pièces moulées sous pression en aluminium ou en zinc, il existe certaines conditions dans lesquelles le moulage sous pression en aluminium doit être privilégié. Tenez compte des facteurs suivants :
Rapport résistance/poids
Si vous recherchez des propriétés de légèreté et de résistance élevée à la traction, il est conseillé d'envisager des pièces moulées sous pression en aluminium. Ces pièces sont réputées pour leur capacité à offrir les deux caractéristiques. Notamment, l’industrie aérospatiale utilise largement des pièces moulées sous pression en aluminium en raison de leur légèreté.
Températures de fonctionnement élevées
En raison de leur point de fusion élevé et de leur capacité à résister à des températures élevées, les pièces moulées sous pression en aluminium sont l'option privilégiée pour les applications impliquant des températures de fonctionnement élevées, comme dans les processus métallurgiques. Cette caractéristique garantit que les propriétés structurelles et physiques des pièces moulées restent intactes même lorsqu'elles sont exposées à une chaleur extrême.
Conductivité électrique
En raison de leur excellente conductivité électrique, les pièces moulées sous pression en aluminium sont le choix privilégié pour divers composants électroniques lors du moulage sous pression. Ceci est particulièrement important dans les applications telles que le blindage EMI, où les pièces doivent être protégées des signaux électromagnétiques.
Obtenez vos pièces moulées sous pression en zinc ou en aluminium
Avez-vous besoin de pièces moulées sous pression en zinc ou en aluminium de haute qualité ? Cherchez pas plus loin! Moldie est là pour répondre à toutes vos exigences en matière de moulage sous pression avec précision, efficacité et qualité supérieure. C'est votre solution unique pour les pièces moulées sous pression en zinc et en aluminium !
Nous sommes spécialisés dans la fourniture de services de moulage sous pression exceptionnels pour les alliages de zinc et d'aluminium, destinés à un large éventail d'industries et d'applications.
Que vous ayez besoin de pièces en aluminium légères et solides ou de composants en zinc résistant à la corrosion, nous avons ce qu'il vous faut. Notre éthique moulage sous pression les procédures impliquent l’utilisation des meilleures matières premières et des meilleures capacités de la maison pour fournir des résultats exceptionnels lorsque vous commandez chez nous en gros. Visitez notre site web pour plus d'informations.
Conclusion
Le zinc et l'aluminium ont des caractéristiques distinctes qui les rendent adaptés à différentes applications. Le zinc offre des avantages tels qu'une densité élevée, une résistance à la corrosion et un faible point de fusion, tandis que l'aluminium offre une légèreté, une résistance élevée et une conductivité thermique supérieure. Comprendre ces différences permet une sélection éclairée des matériaux dans diverses industries et projets.
FAQ
Les pièces moulées sous pression en zinc sont-elles plus résistantes que les pièces moulées sous pression en aluminium ?
Les pièces moulées sous pression en zinc présentent une plus grande résistance que celles en aluminium moulé sous pression. Les experts affirment que le zinc moulé sous pression surpasse plusieurs alliages non ferreux courants en termes de résistance. Les alliages de zinc seraient 2,5 fois plus résistants que l’aluminium moulé sous pression.
Quels sont les paramètres qui différencient les pièces moulées en aluminium et en zinc ?
Le poids, la résistance à la corrosion, le point de fusion et la conductivité thermique distinguent les deux pièces moulées. Le moulage du zinc se caractérise par son poids plus élevé, son point de fusion plus bas, sa résistance supérieure à la corrosion et sa meilleure conductivité thermique par rapport aux autres.
Qu'est-ce qui est le plus résistant à la corrosion : le zinc ou l'aluminium ?
Les pièces moulées sous pression en aluminium présentent une résistance à la corrosion inférieure à celle du moulage en zinc, bien que cela puisse varier en fonction du niveau de pH. Par exemple, dans des solutions alcalines d’un pH de 11, la résistance à la corrosion de l’aluminium moulé est équivalente à celle du zinc.