L’industria della pressofusione comprende principalmente la pressofusione di leghe di alluminio e zinco, che ha visto un utilizzo significativo negli ultimi anni. Comprendere le differenze tra zinco e alluminio è fondamentale per selezionare il materiale appropriato per scopi specifici e ottimizzarne l'utilizzo.
Questo articolo approfondirà le caratteristiche chiave che differenziano lo zinco e l'alluminio, facendo luce sulle loro proprietà distintive, usi e considerazioni per le applicazioni pratiche.
Cosa sono lo zinco e l'alluminio?
Lo zinco e l'alluminio sono metalli diversi con caratteristiche uniche. Lo zinco è un metallo tenero, bianco-argenteo che trova applicazione in vari campi, tra cui la zincatura dell'acciaio per la protezione dalla corrosione, la pressofusione e la produzione di ottone.
L'alluminio è un metallo leggero e robusto utilizzato in diverse applicazioni come la costruzione di aeromobili, lattine per bevande e infissi.
Lo zinco e l'alluminio possono essere combinati per formare varie leghe con proprietà distinte.
Cos'è la lega di zinco?
La lega di zinco si riferisce a una lega metallica composta principalmente da zinco, insieme ad altri elementi metallici. Gli elementi comuni utilizzati nella lega di zinco includono alluminio, magnesio, rame, cadmio, piombo, titanio e altre leghe di zinco a bassa temperatura. Le leghe di zinco vengono preparate fondendo i costituenti e lavorandoli tramite pressofusione o altri metodi di formatura a pressione per ottenere la forma materiale desiderata.
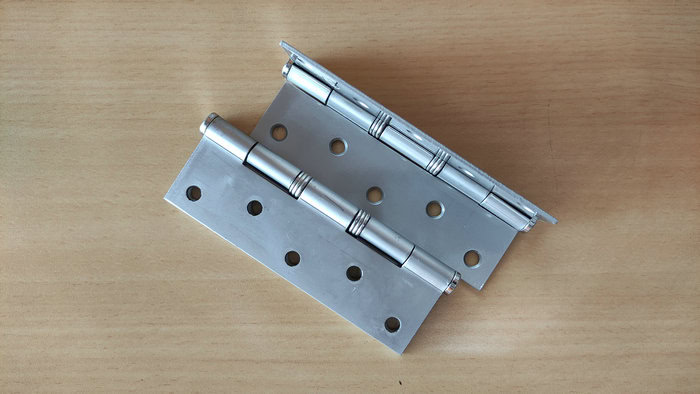
Le leghe di zinco possono essere classificate in colate e deformate, a seconda del processo di fabbricazione impiegato. Trovano applicazione in vari settori, come la pressofusione di strumenti e parti automobilistiche, nonché il trattamento di zincatura a caldo per i tubi delle pareti dell'acqua delle caldaie per migliorare la resistenza alla corrosione alle alte temperature.
Caratteristiche della lega di zinco
- Ha eccellenti prestazioni di fusione, consentendo la produzione di parti di precisione complesse e a pareti sottili con una finitura superficiale liscia.
- Abilita opzioni di trattamento superficiale come galvanica, spruzzatura, verniciatura, lucidatura e molatura.
- Durante i processi di fusione e pressofusione non assorbe ferro, resiste alla corrosione da pressione e non aderisce agli stampi.
- Possiede proprietà meccaniche favorevoli e offre resistenza all'usura a temperatura ambiente.
- Vanta un basso punto di fusione di 385 ℃, facilitando la pressofusione.
Cos'è la lega di alluminio?
La lega di alluminio si riferisce a una categoria di leghe a base di alluminio. Incorpora vari elementi di lega primari come rame, silicio, magnesio, zinco e manganese ed elementi di lega secondari come nichel, ferro, titanio, cromo e litio.
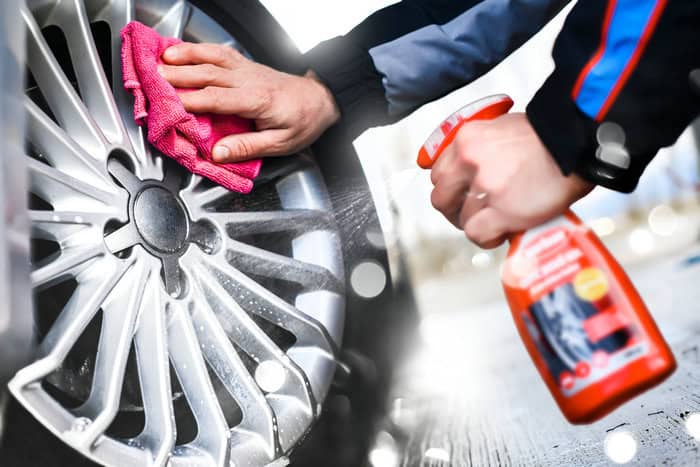
In termini di densità, la lega di alluminio possiede una densità inferiore rispetto all'acciaio. E per quanto riguarda la resistenza, in generale, l'acciaio è più resistente dell'alluminio. Tuttavia, una volta che nell’equazione si tiene conto del peso più leggero dell’alluminio, l’alluminio risulta essere il migliore con un rapporto resistenza/peso superiore. Alcune leghe di alluminio sono più resistenti dell'acciaio. Offre un'eccellente plasticità e può essere lavorato in diversi profili, rendendolo un materiale strutturale metallico non ferroso ampiamente utilizzato in vari settori. Le sue applicazioni spaziano dall'aviazione, all'aerospaziale, alla produzione automobilistica, alla produzione di macchinari, alla costruzione navale e all'industria chimica.
Caratteristiche della lega di alluminio
- Leggero che lo rende ideale per le industrie in cui la riduzione del peso è fondamentale.
- Eccellente conduttività termica.
- Composizione ecologica.
- Resistente alle basse temperature.
- Capacità di ottenere proprietà meccaniche, caratteristiche fisiche e resistenza alla corrosione favorevoli attraverso il trattamento termico.
- Proprietà ad alta resistenza.
Differenze tra lega di zinco e alluminio
Materiale
Il materiale in lega di zinco ha un peso specifico significativo e presenta eccellenti prestazioni di fusione. Vanta un'elevata densità e resistenza, paragonabili o addirittura superiori a quelle dell'acciaio di alta qualità. Di conseguenza, le parti pressofuse in lega di zinco in genere pesano più delle parti pressofuse in lega di alluminio.
Proprietà
Il materiale in lega di zinco presenta un basso punto di fusione, proprietà meccaniche favorevoli e resistenza all'usura. È adatto anche per applicazioni di trattamento superficiale. D'altra parte, la lega di alluminio dimostra un'eccellente conduttività elettrica, conduttività termica e resistenza alla corrosione.
Processo di pressofusione
I punti di fusione delle leghe di zinco e alluminio variano. Le leghe di zinco hanno un punto di fusione inferiore rispetto alle leghe di alluminio. Questa discrepanza nei punti di fusione richiede l'uso di apparecchiature e parametri di lavorazione speciali durante la pressofusione.
La pressofusione della lega di zinco utilizza comunemente una macchina per pressofusione a camera calda. La lega di zinco viene fusa all'interno di questa macchina, consentendo tempi di ciclo più rapidi.
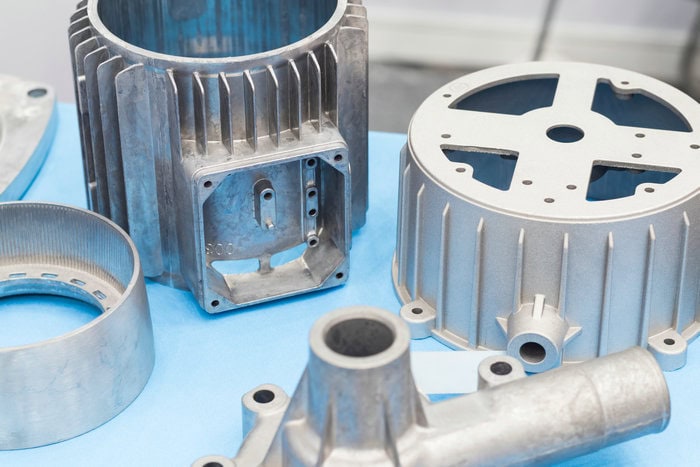
Al contrario, la pressofusione della lega di alluminio utilizza una macchina per pressofusione a camera fredda. La lega di alluminio viene fusa all'esterno della macchina e poi versata nella macchina ad iniezione. Questo processo richiede più tempo rispetto alla pressofusione a camera calda.
L'utilizzo di diverse apparecchiature di lavorazione e parametri per la pressofusione della lega di zinco e della pressofusione della lega di alluminio porta a proprietà divergenti nei prodotti finiti. Le pressofusioni in lega di zinco tendono ad essere più durevoli e resistenti alla corrosione rispetto alle loro controparti in alluminio. Al contrario, i getti pressofusi in lega di alluminio sono generalmente più leggeri e possiedono una migliore conduttività termica.
Peso
In termini di peso, la lega di zinco è generalmente più densa e più pesante dell'alluminio. Lo zinco puro ha una densità specifica di 5 g/cm3, mentre l'alluminio ha una densità inferiore di 2,7 g/cm3. Questa maggiore densità contribuisce alla superiore resistenza agli urti delle leghe di zinco rispetto alle parti in alluminio, rendendole un materiale preferito per la produzione di getti destinati ad applicazioni strutturali.
Proprietà
Ecco le proprietà comuni di entrambi i materiali pressofusi e come si distinguono l'uno dall'altro:
- Punto di fusione
Lo zinco ha un punto di fusione inferiore (circa 420°C) rispetto all'alluminio. Il punto di fusione è un fattore cruciale nella pressofusione, influenzando la scelta del processo di fusione. Il punto di fusione più basso dello zinco lo rende compatibile con il processo a camera calda.
Questa caratteristica offre vantaggi quali costi di produzione ridotti, migliore efficienza produttiva e un minor rischio di degrado dello stampo. Al contrario, l’alluminio ha un punto di fusione più elevato (intorno a 660°C), che lo rende adatto al processo in camera fredda.
- Conduttività termica
La lega di zinco presenta una conduttività termica superiore rispetto alla pressofusione di alluminio. Assorbe e dissipa efficacemente il calore, rendendolo adatto per applicazioni che comportano elevati requisiti di generazione o dissipazione del calore. Le fusioni di zinco sono particolarmente utili nella produzione di componenti come dissipatori di calore o componenti elettronici.
- Resistenza alla corrosione
I getti di zinco possiedono un'eccellente resistenza alla corrosione, superando le parti pressofuse in alluminio. Questa proprietà rende lo zinco più adatto per progetti in condizioni ambientali difficili dove la protezione dalla corrosione è essenziale.
Finitura superficiale
Le pressofusioni richiedono in genere trattamenti di finitura superficiale secondari, a differenza delle parti lavorate a CNC. La necessità di finitura superficiale è influenzata dal processo di fusione e dal tipo di materiale utilizzato.
I getti di zinco presentano una superficie più liscia e con più motivi dopo la fusione, poiché non presentano pori. Al contrario, i getti di alluminio possono sviluppare pori, cavità e bolle durante la fusione, rendendo necessaria una finitura superficiale compensativa.
Sia le fusioni di zinco che quelle di alluminio possono trarre vantaggio dai processi di finitura superficiale. Tuttavia, lo zinco è più compatibile con una gamma più ampia di opzioni di finitura superficiale, tra cui placcatura, verniciatura a polvere, verniciatura, galvanica e anodizzazione.
Vita degli utensili
Gli stampi utilizzati nella pressofusione di zinco non richiedono un'elevata resistenza alla trazione a causa della natura meno abrasiva del materiale e del basso punto di fusione. Queste proprietà si traducono in minori danni allo stampo e minori costi di lavorazione. Di conseguenza, gli stampi utilizzati nella fusione di zinco possono resistere a oltre 1.000.000 di colpi prima di richiedere la sostituzione, mentre gli stampi utilizzati nella fusione di alluminio durano tipicamente circa 100.000 colpi.
Applicazioni
Sia le fusioni di zinco che quelle di alluminio trovano applicazioni in vari settori. La fusione di zinco è nota per la sua resistenza, il che la rende una scelta popolare per gli elettrodomestici e la pressofusione automobilistica.
D'altra parte, la fusione di alluminio eccelle nel suo rapporto resistenza/peso, rendendola ideale per componenti leggeri ma robusti. Questa caratteristica rende i getti di alluminio particolarmente preziosi nel settore aerospaziale, dove la necessità di materiali leggeri è cruciale.
Tempo di ciclo
Il tempo ciclo è significativo quando si confronta la pressofusione di alluminio con la pressofusione di zinco. La pressofusione dello zinco avviene ad alta pressione e basso punto di fusione, distinguendola dalla pressofusione dell'alluminio. Di conseguenza, la pressofusione di zinco presenta un tempo di ciclo più breve, in genere 150-200% più veloce della fusione di alluminio.
Inoltre, il processo di riscaldamento per la pressofusione di zinco avviene internamente, a differenza della pressofusione di alluminio, che utilizza il processo a camera fredda. Inoltre, l'efficiente dissipazione del calore della fusione di zinco consente una solidificazione più rapida del metallo fuso, contribuendo a un'ulteriore riduzione del tempo di ciclo.
Costi
Il costo della produzione della pressofusione è influenzato da vari fattori, tra cui la scelta del materiale, il processo di produzione, l'abilità dell'operatore, il tempo di ciclo e la finitura superficiale. I getti pressofusi realizzati con leghe di zinco sono meno costosi ma hanno una robustezza e una resistenza alla corrosione inferiori rispetto alle leghe di alluminio. Le pressofusioni di alluminio sono più robuste e resistenti alla corrosione, ma hanno un costo più elevato.
Il processo di produzione prevede la fusione del metallo, l'iniezione in uno stampo e il raffreddamento per formare la parte finale. Operatori qualificati e tempi di ciclo più brevi possono ridurre i costi. Inoltre, la finitura superficiale, come la verniciatura o la placcatura, aumenta il costo complessivo. In generale, i pressofusi di zinco sono più convenienti rispetto a quelli di alluminio.
Quando e perché scegliere la pressofusione di zinco
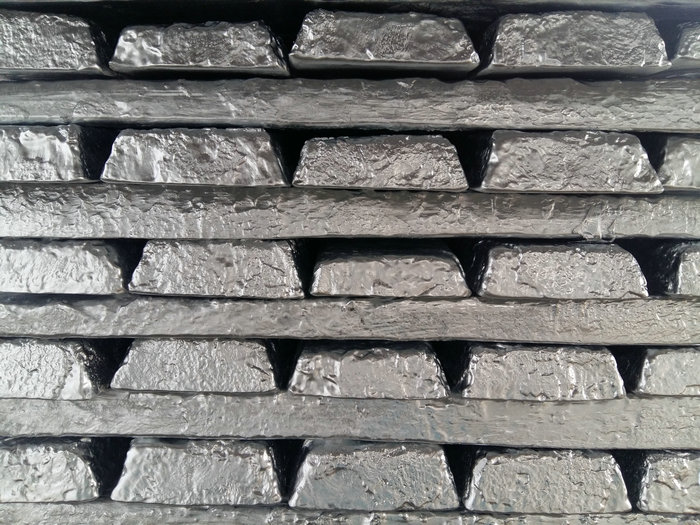
Di fronte al dilemma della scelta tra pressofusione di zinco e pressofusione di alluminio, considerare i seguenti fattori che rendono la pressofusione di zinco l’opzione preferita
Parti con pareti sottili
La pressofusione di zinco è particolarmente adatta per la produzione di parti con pareti sottili grazie alla sua resistenza rispetto ad altri materiali. La natura densa dello zinco garantisce integrità e stabilità strutturale, riducendo l'utilizzo del materiale e i costi di pressofusione.
Condizioni ambientali difficili
La pressofusione di zinco eccelle in condizioni ambientali difficili, in particolare quelle soggette a corrosione. La sua eccezionale resistenza alla corrosione forma uno strato protettivo sulle parti esposte a tali condizioni.
Minore stress residuo
La pressofusione prevede l'applicazione di pressione per iniettare il metallo fuso nello stampo. La pressofusione ad alta pressione può portare a stress residui sulle parti, ma la pressofusione di zinco, che utilizza la pressofusione a bassa pressione, riduce al minimo lo stress residuo.
Stampo pressofuso
Scegliere la pressofusione di zinco è vantaggioso se si lavora con stampi delicati. Gli stampi per pressofusione di zinco possono durare circa dieci volte di più rispetto agli stampi per pressofusione di alluminio.
Produzione più veloce
Le leghe di zinco hanno un basso punto di fusione, consentendo un processo di pressofusione a camera calda con iniezione ad alta pressione. Ciò si traduce in una velocità di ciclo più elevata rispetto ad altri materiali. A differenza della pressofusione dell'alluminio in cui l'operatore fonde l'alluminio all'esterno della macchina prima di versarlo nella macchina a iniezione, nella pressofusione dello zinco, lo zinco viene fuso all'interno della macchina
Considerando questi fattori, la pressofusione di zinco può essere la scelta preferita in vari scenari.
Perché e quando scegliere la pressofusione di alluminio
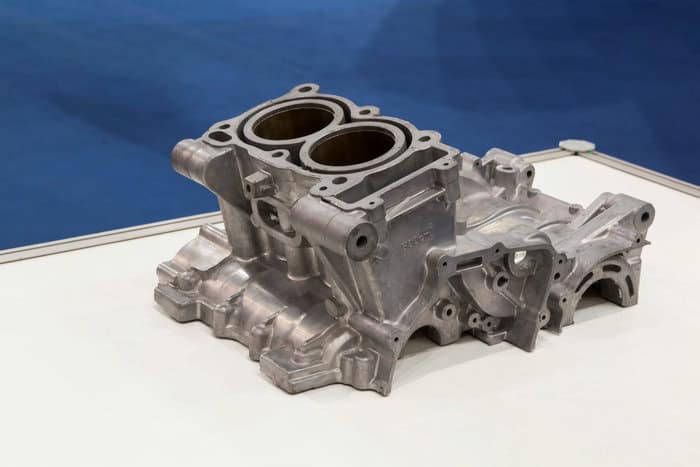
Di fronte alla decisione tra parti pressofuse in alluminio o zinco, ci sono alcune condizioni in cui si dovrebbe dare la preferenza alla pressofusione di alluminio. Considera i seguenti fattori:
Rapporto resistenza/peso
Se stai cercando proprietà leggere e di elevata resistenza alla trazione, è consigliabile prendere in considerazione le parti in alluminio pressofuso. Queste parti sono ben note per la loro capacità di offrire entrambe le caratteristiche. In particolare, l’industria aerospaziale utilizza ampiamente parti pressofuse realizzate in alluminio a causa della loro natura leggera.
Temperature di esercizio elevate
Grazie al loro elevato punto di fusione e alla capacità di resistere alle alte temperature, i getti pressofusi di alluminio sono l'opzione preferita per le applicazioni che comportano temperature operative elevate, come nei processi metallurgici. Questa caratteristica garantisce che le proprietà strutturali e fisiche dei getti rimangano intatte anche se esposti a temperature estreme.
Conduttività elettrica
Grazie alla loro eccellente conduttività elettrica, i pressofusi di alluminio sono la scelta preferita per vari componenti elettronici in pressofusione. Ciò è particolarmente importante in applicazioni come la schermatura EMI, dove le parti devono essere protette dai segnali elettromagnetici.
Ottieni i tuoi pezzi in pressofusione di zinco o alluminio
Avete bisogno di pezzi pressofusi in zinco o alluminio di alta qualità? Non guardare oltre! Moldie è qui per soddisfare tutte le vostre esigenze di pressofusione con precisione, efficienza e qualità di prim'ordine. È la soluzione completa per pezzi pressofusi in zinco e alluminio!
Siamo specializzati nella fornitura di eccezionali servizi di pressofusione per leghe di zinco e alluminio, rivolgendoci a un'ampia gamma di settori e applicazioni.
Che tu abbia bisogno di parti in alluminio leggere e resistenti o di componenti in zinco resistenti alla corrosione, abbiamo la soluzione che fa per te. La nostra etica pressofusione le procedure prevedono l'utilizzo delle migliori materie prime e delle migliori capacità dell'azienda per fornire risultati eccezionali quando ordini da noi in grandi quantità. Visita il nostro sito web per ulteriori informazioni.
Conclusione
Lo zinco e l'alluminio hanno caratteristiche distinte che li rendono adatti a diverse applicazioni. Lo zinco offre vantaggi come alta densità, resistenza alla corrosione e basso punto di fusione, mentre l'alluminio fornisce leggerezza, elevata resistenza e conduttività termica superiore. Comprendere queste differenze consente una selezione informata dei materiali in vari settori e progetti.
Domande frequenti
Le pressofusioni di zinco sono più resistenti delle pressofusioni di alluminio?
Le parti in pressofusione di zinco presentano una resistenza maggiore rispetto alla pressofusione di alluminio. Gli esperti affermano che la pressofusione di zinco supera in resistenza diverse leghe non ferrose comuni. Si dice che le leghe di zinco siano 2,5 volte più resistenti della pressofusione di alluminio.
Quali sono i parametri che differenziano i getti di alluminio da quelli di zinco?
Il peso, la resistenza alla corrosione, il punto di fusione e la conduttività termica distinguono i due getti. La fusione di zinco è caratterizzata da un peso maggiore, un punto di fusione inferiore, una resistenza alla corrosione superiore e una migliore conduttività termica rispetto alle altre.
Cos’è più resistente alla corrosione: zinco o alluminio?
Le parti in pressofusione di alluminio presentano una resistenza alla corrosione inferiore rispetto alla pressofusione di zinco, sebbene ciò possa variare a seconda del livello di pH. Ad esempio, nelle soluzioni alcaline con pH pari a 11, la resistenza alla corrosione della fusione di alluminio è equivalente a quella dello zinco.