Polypropylene (PP) is one of the most popular plastic materials used worldwide. It’s a semi-crystalline, rigid thermoplastic that was initially polymerized in 1951 and is now widely used for various commercial and residential purposes. At roughly 45 metric tons today, the demand for Polypropylene is thought to be the highest it has ever been.
Some sources claim that the material currently has a 45 million metric ton yearly market because of increased global demand, which is anticipated to reach 62 million metric tons by 2020.
In addition, polypropylene materials are generally considered safe; thus, making them suitable for use in different sectors. Moreover, it’s also soft and flexible, making it suitable for several applications, such as making yogurt containers.
Applications Of PP Material
As mentioned before, the material properties of PP plastic make it suitable for various applications. The slick, tactile surface of Polypropylene makes it perfect for:
- Low-friction applications such as machinery gears
- Plastic furniture
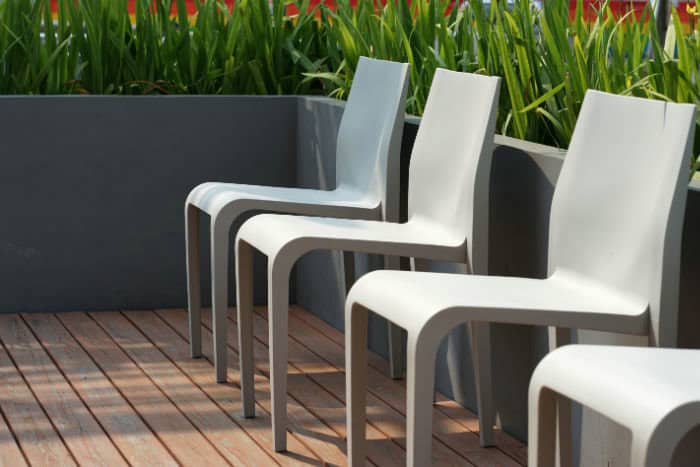
In addition, PP has high chemical resistance and is thus not susceptible to corrosion, making it a great option for packing the following:
- First-aid products
- Bleaches
- Cleaning substances
Further, PP has a well-deserved reputation for hardness and longevity thanks to its exceptional fatigue resistance and flexibility. Polypropylene also has excellent insulating qualities, making it safe for the plastic casing of cables and electrical equipment.
In its fiber form, Polypropylene may be used for a far larger range of products than only tote bags, such as the following:
- Ropes
- Twine
- Tape
- Carpets
- Upholstered furniture
- Apparel
- Camping gear
Polypropylene also works particularly well for the marine industry because of its waterproof qualities. Further, its flexibility, waterproof qualities, strength, and resistance to mold, bacteria, and chemical corrosion are all valued in the medical industry.
Additionally, Polypropylene cleans effectively and can withstand steam sterilization techniques. This makes PP suitable for making the following medical devices:
- Specimen bottles
- Drug containers
- Syringes
- Petri dishes
Another sector where Polypropylene is also frequently utilized is the automotive industry. It’s used for battery casings, trays and drink holders, bumpers, interior accents, instrument panels, and door trims.
Chemical And Physical Properties
Polypropylene has several characteristics that make it ideal for several applications. Some of its primary characteristics are:
- Transmissivity: Despite having the ability to be made transparent, Polypropylene is typically produced with an opaque hue. Applications where some light transfer is crucial or has aesthetic value, might use Polypropylene. The preferable options for polymers with high transmissivity are acrylic and polycarbonate.
- Chemical resistance: Polypropylene doesn’t react easily with weak bases and acids, making it an ideal material for containers containing such liquids as cleaning solutions, first aid supplies, and more.
- Fatigue resistance: When subjected to significant torsion, bending, and flexing, Polypropylene maintains its shape. Making living hinges is a beneficial application of this characteristic.
- Elasticity and toughness: In general, Polypropylene is thought of as a “tough” material because, like all materials, it exhibits elasticity over a particular range of deflection but also experiences plastic deformation early in the deformation process. The ability of a material to deform (plastically, not elastically) without breaking is referred to as toughness in engineering.
- Insulation: Polypropylene is excellent for electronic components because of its high electrical resistance.
Additionally, PP exhibits no stress-cracking issues at higher temperatures and provides great electrical and chemical resistance. While PP’s characteristics and those of polyethylene are similar, some key distinctions exist.
Material Properties Of Polypropylene:
These include a lower density, higher rigidity and hardness, and a higher softening point (PP doesn’t melt below 160oC; Polyethylene, a more popular plastic, will anneal at roughly 100oC). All commercially produced polypropylene resin contain additives to preserve the polymer during production and improve end-user performance.
Thus, the main material properties of PP materials include the following:
- Melting point: The melting point of homopolymers runs between 160 to 165 degrees Celsius and 135 to 159 degrees Celsius for copolymers.
- Density: PP is one of the lightest polymers among all common plastics. It is a good alternative for lightweight applications because of its capability. These are the densities for different polymers:
- 0.904 to 0.908 g/cm3 homopolymer
- 0.904 to 0.908 g/cm3 for the random copolymer.
- 0.898 to 0.900 g/cm3 for impact copolymer
- Chemical resistance: As mentioned above, PP is highly resistant to chemical reactions. It is resistant to diluted and concentrated acids, alcohols, and bases. It’s also resistant to aliphatic hydrocarbons, esters, aldehydes, and ketones. Further, it has limited resistance to oxidizing agents, aromatic and halogenated hydrocarbons, and both.
Subsequently, the low melting point also makes it highly flammable.
Types of Polypropylene
There are two main types of Polypropylene available in the market. These are:
Polypropylene Homopolymer
This is the general-purpose grade that is most frequently used. It exclusively has propylene monomer, which is present as a semi-crystalline solid. The most common uses are packaging, textiles, pipelines, healthcare, and electrical applications.
Polypropylene Copolymer
This family contains the following:
- Block copolymers: In this category, there is more ethene content (between 5 and 15%). Co-monomer units are organized in a predictable pattern (or blocks). Therefore, the regular pattern makes thermoplastic tougher and less brittle than the random copolymer. These polymers are appropriate for uses, including industrial ones that require great strength.
- Random copolymer: This is created by mixing ethene with propene to form a polymer. It has Ethene units randomly inserted into the polypropylene chains, typically up to 6% by mass. These polymers are adaptable and optically clear, making them perfect for items that need to look great and applications that require transparency.
The type chosen for use depends on its properties and suitability.
Polypropylene Derivatives
Here are the primary characteristic examples of polypropylene derivatives:
- Expanded Polypropylene (EPP): It is a closed-cell, extremely-low density foam made of beads. Three-dimensional polymer foam items are made using EPP. EPP bead foam provides a better strength-to-weight ratio, great impact resistance, superior thermal insulation, and resistance to chemicals and water.
EPP is utilized in a variety of products and applications, including consumer goods, packaging, construction goods, and automobiles.
- Bio-based Polypropylene: It is a bio-based variant of Polypropylene, and the feedstocks used to make its monomer bio-based propylene are renewable. The bio-based component might range from 30% to 100%.
- Polypropylene terpolymer: It is made up of propylene segments bonded together by the co-monomers ethylene and butane, which appear at random locations along the polymer chain.
The transparency of PP terpolymer is superior to PP homo. Additionally, the co-monomer addition lessens the polymer’s crystalline homogeneity, making it appropriate for sealing film applications.
These characteristics of derivatives are essential to manufacturers who use Polypropylene as a commodity plastic.
Advantages Of Polypropylene
The following are the advantages of using PP material:
- Polypropylene is extremely difficult to snap since it can tolerate twisting motions up to 360 degrees without snapping. It is easily produced, reasonably priced, and widely accessible in many different nations and cultures.
- Its durability and adaptability as a packaging material and choice for hinges and bottle caps joined to the main bottle by a thin layer of plastic are enhanced by high chemical and fatigue resistance.
- Since it can be made as an opaque or transparent thermoplastic and employed where some light transfer is necessary, it can provide excellent color variety. Because of its lower density, it can be employed in applications where weight reduction must be a top priority.
- Because it is impermeable and incredibly resistant to absorbing moisture, Polypropylene has additional packing advantages and versatility.
- Due to its high flexural strength and semi-crystalline structure, it is also resistant to general wear and tear, making it perfect for products that must withstand more significant amounts of physical stress.
- Additionally, it is resistant to germs, rot, mildew, and mold.
These benefits are essential when deciding on whether or not to use PP material.
Disadvantages Of Polypropylene
Though PP material is generally great for use in different sectors, it also has some disadvantages, such as the following:
- The inability of Polypropylene to be easily recycled is a major drawback when it comes to protecting the environment and the world’s resources.
- It undergoes an irreversible chemical change when it burns.
- Polypropylene that has already melted and been formed would burn if you attempted to re-heat it; it wouldn’t liquefy again.
- Substantially more expensive recycling or reconditioning techniques must be considered when using PP material.
- Due to its low melting point, Polypropylene is also highly flammable, has a limited tolerance for higher temperatures, and is vulnerable to oxidation and UV damage.
- While Polypropylene’s glossy sheen makes it convenient to handle and aesthetically beautiful, it also makes it more difficult for other surfaces and materials, like paints and glues, to adhere to.
- Polypropylene cannot be used to construct a joint or hinge without alternative bonding techniques, like welding.
Therefore, the drawbacks of Polypropylene must also be considered when choosing a material to use in different applications.
Safety And Toxicity Of Polypropylene
Although Polypropylene is produced using some potentially harmful chemicals, it is usually recognized as a safe finished product. It’s frequently used in plastic packaging for food, drink, and medical supplies.
Polypropylene products may be reused safely and are robust enough to survive typical wear and tear for numerous uses, despite the fact that it is not widely regarded as an eco-friendly material due to challenges in the recycling process.
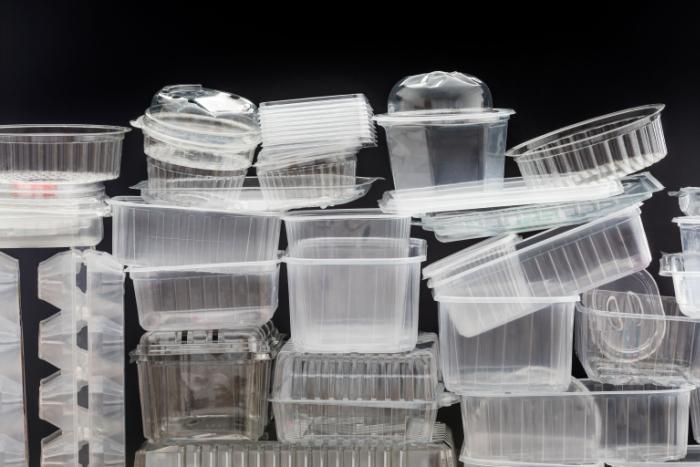
Polypropylene is used to make the following items because of its safety:
- Food containers
- Baby bottles
- Hot beverage cups
- Disposable utensils such as cups and plates
- Straws
According to research, when plastic is scratched or heated, chemicals from the containers, plates, and bottles leak into meals. Polypropylene is less harmful than other plastics since it doesn’t contain bisphenol A, or BPA, as it is more popularly known.
BPA, a synthetic estrogen, is employed in stiff plastics rather than more flexible ones like Polypropylene.
Polypropylene Processing
There are several methods of polypropylene processing, such as injection molding, blow molding, extrusion, and 3D printing.
Injection Molding
During the injection molding process of Polypropylene, the melt temperature is set between 200 to 300 °C and 10 to 80 °C for the mold. High mold temperature will enhance the part’s brightness and beauty.
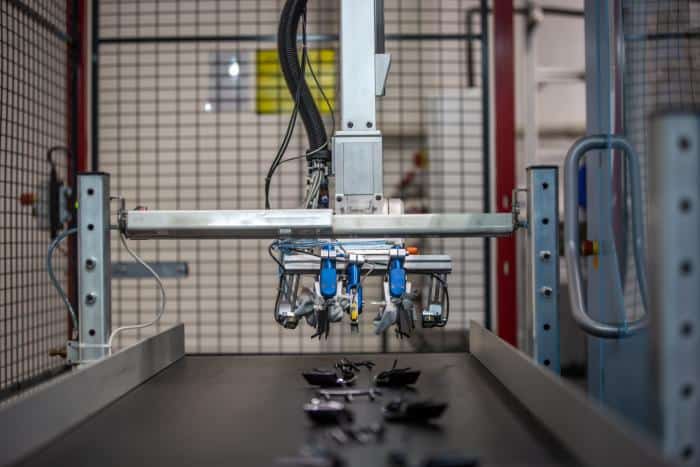
If stored properly, drying is not required. Further, mold shrinkage ranges from 1.5 to 3%, depending on the processing circumstances, the polymer’s rheology, and the thickness of the finished product.
Extrusion
This process is used for making cables, tubes, and blow-and-cast films. The melting temperature has to be within the range of 200–300 °C with a cylinder compression ratio: of 3:1 and temperatures of 205 to 180 °C. When done, the parts should be placed for regrinding instead of pre-drying for three hours at 105-110°C (221-230°F).
3D Printing
Polypropylene is a tough and rigid material that’s difficult to print in 3D, but its components can still be manipulated.
Today, a number of producers have enhanced PP’s physical characteristics or even developed mixes with increased toughness making it appropriate for 3D printing applications.
Therefore, it is advised to carefully review the supplier’s documentation for printing temperature, printing bed, etc., while 3D printing with Polypropylene.
3D printing can be used to make the following polypropylene pp items:
- Prototypes
- Complicated models
- Functional models
However, the chemical formula for mixing Polypropylene with other substances to make it susceptible to 3D printing must be accurate.
Why Polypropylene Is Popular
Applications for Polypropylene are found in both domestic and commercial settings. It stands out as a valuable material for a variety of uses thanks to its special qualities and capacity to adapt to different production techniques.
The dual functionality of Polypropylene as a plastic and a fiber is another important quality (like those promotional tote bags that are given away at events, races, etc.).
Since Polypropylene can be produced in various ways and for various uses, it quickly began to displace many of the traditional alternatives, especially in the packaging, fiber, and injection molding sectors. It has maintained its expansion over the years and is still a significant participant in the global plastics business.
Conclusion
Polypropylene is often confused with plastic. However, the main distinction between Polypropylene and plastic is that whereas plastic material is typically opaque, it is possible to manufacture crystal transparent material from Polypropylene. For instance, when choosing a material for a bag to package an item, we frequently consider the material’s characteristics.
A bag that is completely transparent is required if we wish to expose the product. In this situation, plastic bags are not a wise solution because they are opaque. However, Polypropylene remains one of the best materials for this use.