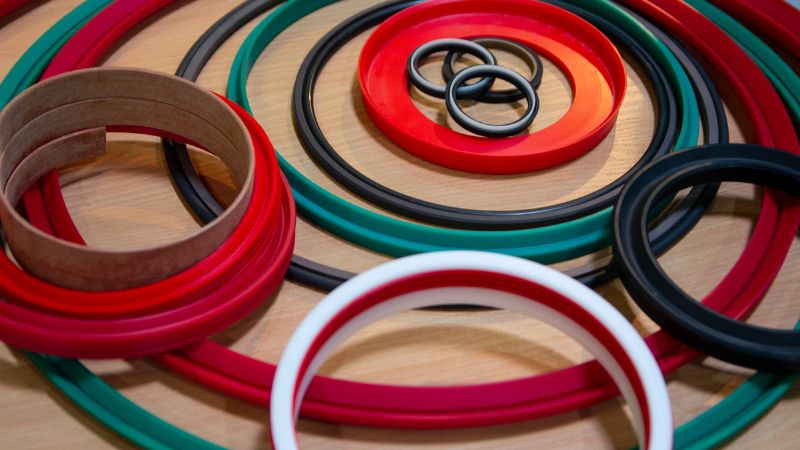
Rubber injection molding is a versatile and efficient manufacturing process that has revolutionized the production of rubber mold parts across various industries. This advanced technique combines precision, speed, and cost-effectiveness to create complex rubber components with tight tolerances and excellent consistency.
As demand for high-quality custom rubber mold products continues to grow in sectors such as automotive, medical, aerospace, and consumer goods, understanding the intricacies of rubber injection molding becomes increasingly important for manufacturers and engineers alike.
In this comprehensive guide, we will delve into the fundamental aspects of rubber injection molding, exploring the process itself, the types of molds used, and the wide range of parts that can be produced. From the initial material selection to the final product, we’ll examine each step of the manufacturing process, highlighting the advantages and challenges associated with this innovative technique.
What is Rubber Injection Molding?
Rubber injection molding is a method where molten rubber is injected into a mold. First, the rubber material is heated until it’s soft. Then, it is injected under high pressure into the mold cavity.
Once inside the mold, the rubber cools and hardens into the desired shape. This technique is ideal for producing items with intricate designs, like gaskets and seals.
What are the Benefits of Rubber Injection Molding?
Rubber injection molding is highly efficient. It can handle large production runs quickly, making it cost-effective for mass production. The method produces minimal waste due to its precision.
With this process, you can achieve tight tolerances and complex shapes that other methods might struggle with. Versatility is another key; rubber injection molding works with various rubber types, enhancing product quality and durability.
Additionally, this method provides high repeatability, ensuring each part is consistent. This advantage is valuable for maintaining quality in products like O-rings and seals, which require durability and precision.
What are the Types of Rubber Used in Rubber Mold Injection?
Natural Rubber
Natural rubber is derived from the latex of rubber trees and is known for its excellent elasticity, resilience, and tear strength.
- Properties: High tensile strength, good elongation, excellent friction and abrasion resistance
- Applications: Tires, shock absorbers, seals, and vibration dampeners
Synthetic Rubbers
Nitrile Rubber (NBR)
Nitrile rubber is a copolymer of butadiene and acrylonitrile.
- Properties: Excellent resistance to oils, fuels, and many solvents; good abrasion resistance
- Applications: Oil seals, gaskets, hoses, and automotive parts
Hydrogenated Nitrile Butadiene Rubber (HNBR)
HNBR is a modified version of NBR with improved heat and chemical resistance.
- Properties: High resistance to petroleum-based oils and chemicals, excellent heat resistance
- Applications: Automotive seals, belts, and gaskets in high-temperature environments
Ethylene Propylene Diene Monomer (EPDM)
EPDM is a synthetic rubber made from ethylene, propylene, and a small amount of diene.
- Properties: Excellent resistance to weathering, ozone, and heat; good electrical insulation
- Applications: Weather stripping, roofing membranes, and electrical insulation
Silicone Rubber
Silicone rubber is an inorganic synthetic elastomer with a silicon-oxygen backbone.
- Properties: Wide temperature range (-55°C to 300°C), excellent electrical properties, biocompatibility
- Applications: Medical devices, electrical insulation, and high-temperature seals
Fluorosilicone
Fluorosilicone is a specialized form of silicone rubber with added fluorine atoms.
- Properties: Combines the temperature resistance of silicone with improved fuel and oil resistance
- Applications: Aerospace and automotive fuel system components
Neoprene (Polychloroprene)
Neoprene is a synthetic rubber produced by polymerization of chloroprene.
- Properties: Good resistance to weathering, oils, and flames; moderate chemical resistance
- Applications: Wetsuits, gaskets, hoses, and electrical insulation
Styrene-Butadiene Rubber (SBR)
SBR is a copolymer of styrene and butadiene.
- Properties: Good abrasion resistance, aging resistance, and crack resistance
- Applications: Tire treads, conveyor belts, and footwear
Fluorocarbon Rubber (Viton)
Fluorocarbon rubber is known for its exceptional chemical and heat resistance.
- Properties: Excellent resistance to oils, fuels, and acids; high-temperature capability
- Applications: Chemical processing equipment, aerospace seals, and automotive fuel systems
Butyl Rubber
Butyl rubber is a copolymer of isobutylene with a small amount of isoprene.
- Properties: Very low permeability to gases, good flex properties, and vibration damping
- Applications: Inner tubes, tire inner liners, and pharmaceutical stoppers
Urethane Rubber (Polyurethane)
Urethane rubber is a class of polymers with urethane linkages.
- Properties: High tensile strength, excellent abrasion resistance, and good oil resistance
- Applications: Industrial rollers, gaskets, and seals in high-wear applications
Thermoplastic Elastomers
Thermoplastic Elastomers (TPE)
TPEs are a class of copolymers that combine the properties of thermoplastic and elastomeric materials.
- Properties: Recyclable, flexible processing, wide range of hardness options
- Applications: Soft-touch grips, overmolded components, and flexible consumer products
Thermoplastic Vulcanizate (TPV)
TPV is a blend of polypropylene and fully cured EPDM rubber.
- Properties: Improved durability compared to TPEs, good chemical resistance
- Applications: Automotive weather seals, fluid handling components, and outdoor equipment
What are the Essentials of Ruber Injection Mold Design?
You need to consider the intricacies of mold creation and the specific steps involved in transforming raw rubber into a finished product.
Mold Design Essentials
Creating a mold is one of the first steps in rubber injection molding. You need to ensure that your mold design is precise. CNC machining can help with dimensional tolerance, providing high precision for complex shapes.
Ventilation is also important. Proper air escape routes prevent defects like air pockets. Your mold should include a well-designed mold cavity that allows for smooth flow. Use a metal mold for durability and heat conduction during manufacturing. Good mold design leads to better product quality.
What is the Rubber Molding Process?
Rubber injection molding process starts with heating the rubber material until it becomes soft.
Vulcanization is crucial, as it strengthens the rubber by forming cross-links.
Cooling is the next phase. Here, the rubber hardens into its final shape. Each step of this process needs to be precise to keep the quality high. Automation can help streamline this and improve efficiency.
The Different Types of Rubber Mold Injection
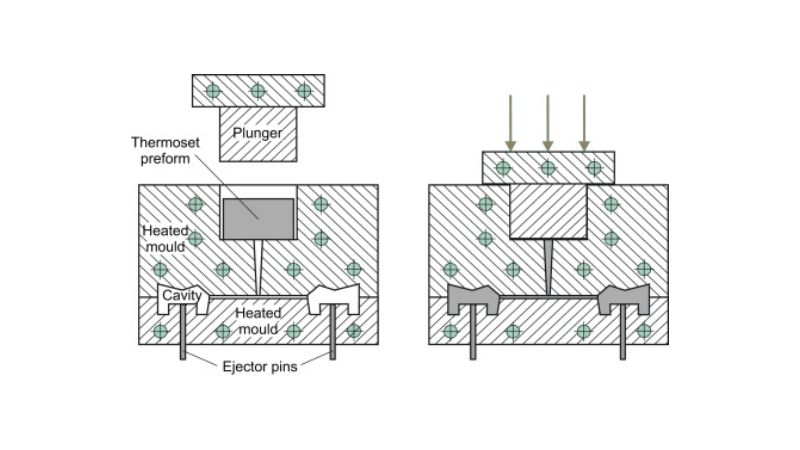
Rubber Injection Molding
Rubber injection molding is a process that closely resembles plastic injection molding. It’s particularly suitable for high-volume production of complex rubber parts with tight tolerances.Process Details:
- The rubber compound is fed into a heated barrel, typically in strip or pellet form.
- A screw mechanism inside the barrel melts and mixes the rubber until it reaches a liquid state.
- The liquid rubber is then injected at high pressure (often 15,000 to 30,000 psi) into a closed mold cavity.
- The mold is maintained at a high temperature (usually between 150°C and 200°C) to facilitate curing.
- After curing, the mold opens, and the finished part is ejected.
Additional Advantages:
- Consistent part quality due to precise control over injection pressure and temperature
- Minimal material waste as excess material can often be reused
- Automation-friendly, allowing for 24/7 production capabilities
- Ability to produce parts with varying wall thicknesses
Compression Molding
Compression molding is one of the oldest and most straightforward rubber molding processes. It’s particularly effective for producing large, relatively simple parts.Process Details:
- A pre-measured amount of rubber compound (often called a preform) is placed in the lower half of a heated mold cavity.
- The mold is closed using a hydraulic press, typically applying pressures between 1,000 and 2,000 psi.
- As the mold closes, the rubber is compressed and flows to fill the mold cavity.
- Heat and pressure are maintained for a specific time to allow the rubber to cure fully.
- Once cured, the mold opens, and the part is removed.
Additional Advantages:
- Excellent for producing parts with uniform wall thickness
- Lower tooling costs compared to injection molding
- Suitable for molding large parts that might be challenging for injection molding
- Can accommodate inserts and reinforcing materials easily
Transfer Molding
Transfer molding is a hybrid process that combines elements of both injection and compression molding. It’s particularly useful for producing multiple small parts simultaneously or parts with complex geometries.
Process Details:
- A measured amount of rubber compound is placed in a chamber (called a pot) above the mold cavity.
- A plunger pushes down on the rubber, forcing it through small channels (called sprues) into the mold cavity.
- The rubber fills the mold cavity under pressure, typically between 1,000 and 5,000 psi.
- Heat is applied to cure the rubber, usually at temperatures between 150°C and 200°C.
- After curing, the mold opens, and the parts are ejected.
Additional Advantages:
- Better control over material flow compared to compression molding
- Can produce parts with more complex geometries than compression molding
- More suitable for inserting metal components or reinforcements than injection molding
- Generally faster cycle times than compression molding for small parts
How to Optimize Production and Quality
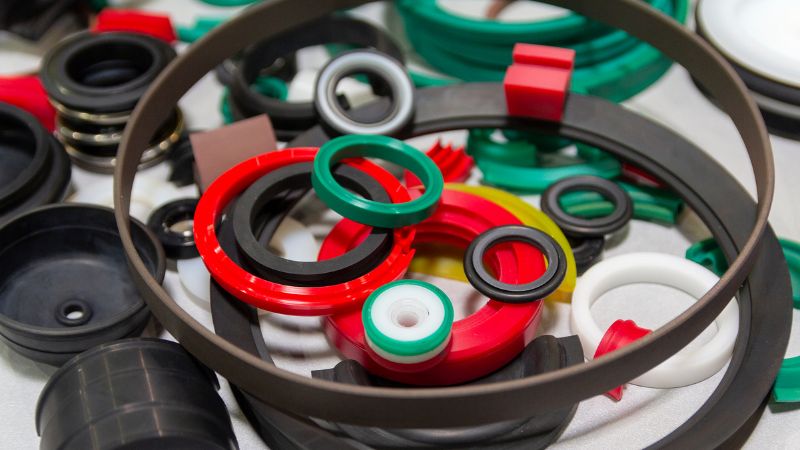
Improving rubber injection molding involves reducing cycle time and ensuring consistent quality. Focusing on these aspects can enhance efficiency and product dependability in high-volume production.
Cycle Time Reduction
Cycle time is crucial for high-volume production. By minimizing it, you can produce more parts in less time, boosting efficiency. Automation and robotics can help in this area by speeding up repetitive tasks and reducing human error. Adjusting the vulcanization time based on energy balances is another approach that has shown positive results. This allows for dynamic control of the process, tailoring it to specific needs.
Regular monitoring and adjustments help maintain a swift pace without sacrificing quality. By understanding which areas can be sped up without compromising the outcome, you can make significant gains in productivity.
Ensuring Consistent Quality
To achieve consistent quality, you must focus on accurate and precise manufacturing. Dimensional accuracy ensures that each component fits perfectly, reducing waste and rework. Implementing quality control mechanisms throughout the manufacturing process helps catch errors early. This can include sensor technology, which monitors pressure and strain during production.
Automation plays a role here, too, by maintaining steady parameters, thus improving product quality. Training your team on best practices and involving them in quality checks can further enhance dependability. By concentrating on these key areas, you make sure that every piece meets high standards.
Applications and Performance of Rubber Injection Products
Rubber injection molding is used in many industries due to its ability to produce intricate shapes and durable components. It offers advantages like chemical and corrosion resistance, making it suitable for varied applications. Performance is influenced by factors like material choice and manufacturing precision.
Industries and Applications
Injection molding rubber products are widely applied in the automotive, medical, and consumer goods industries. You will find it in automotive applications for making molded parts such as gaskets, o-rings, and vibration isolators. These components ensure safety and enhanced vehicle performance.
In medical devices, this process is key in producing rubber diaphragms and seals that meet strict healthcare standards. It is also used in making various consumer goods like rubber bumpers, offering both protection and aesthetic appeal.
Performance Factors
The performance of rubber injection molded products hinges on several important factors. Durability is a critical quality, influenced by the choice of materials which need to withstand wear and tear. Chemical resistance is essential in applications exposed to harsh substances, ensuring the product’s longevity without degradation.
Mechanical strength is another vital factor, supporting structural integrity even under stress. In environments prone to moisture or chemicals, products need corrosion resistance to maintain their function. Proper manufacturing techniques allow components to achieve complex shapes and precise dimensions, further enhancing reliability and performance.
Frequently Asked Questions
What factors influence the price of a rubber injection mold?
Several factors affect mold prices, including the complexity of the mold design, the type of rubber used, and the production volume. Additionally, precision requirements and material costs can also play a significant role in determining the overall price.
What should I consider when selecting a rubber injection molding machine?
When choosing a machine, you should consider its clamping force, shot size, and whether it can handle the specific type of rubber you plan to use. Other factors include the speed, efficiency, and ease of maintenance of the machine.
What are the common sizes available for rubber injection molds?
Rubber injection molds come in a variety of sizes to cater to different production needs. Standard sizes are often available, but custom sizes can also be produced based on specific project requirements.
Are there different rubber molding methods, and how do they compare?
Yes, there are several methods, including compression molding and transfer molding. Injection molding is praised for its efficiency and ability to produce complex designs. Each method has its own benefits and may be more suitable for different applications depending on the desired outcome and material used.