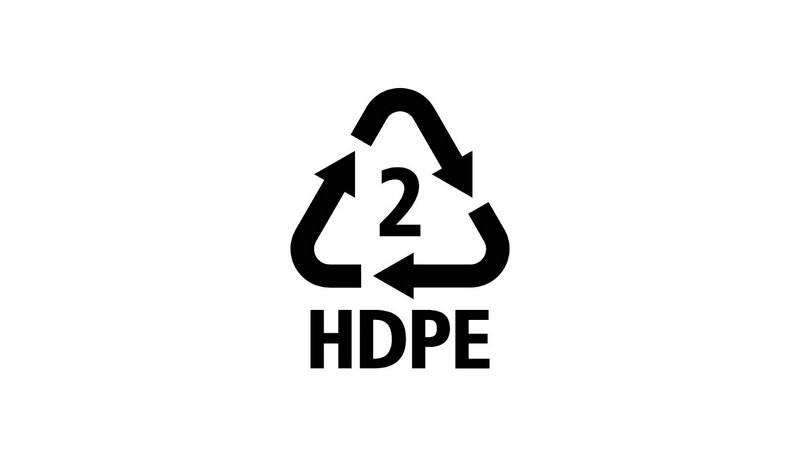
You may not be familiar with HDPE and injection molding. HDPE molded parts are commonly used in industrial applications, and injection molding can produce parts of varying shapes and sizes.
In this comprehensive article, we will delve into the world of HDPE injection molding, covering all the essential aspects you should know.
We will begin by exploring the unique properties of HDPE that make it suitable for injection molding, including its high strength, moisture resistance, and thermal properties. We will then discuss the injection molding process itself, including the key steps involved, such as melting, injecting, and cooling the HDPE.
What is HDPE?
High-density polyethylene (HDPE) or polyethylene high density (PEHD) is a widely used thermoplastic polymer that is known for its high tensile strength and excellent chemical resistance.
Commonly available in pellet form for injection molding applications, HDPE offers a versatile range of properties that make it suitable for products ranging from common consumer goods to industrial piping systems.
One of the key advantages of high-density polyethylene is its durability and toughness. With high impact resistance and stress cracking, HDPE products can withstand heavy loads and high-stress environments. This makes it an ideal material for applications such as chemical containers, pipe systems, and plastic lumber that require both strength and chemical resistance.
Why Choose HDPE as Mold Injection Material
Advantages of HDPE Injection Molding:
- Cost-effective: HDPE is a relatively inexpensive commodity resin compared to other plastics, making it an economical choice for high-volume injection molding.
- High strength-to-density ratio: HDPE has an excellent strength-to-density ratio, providing good mechanical properties while being lightweight. This makes it suitable for applications requiring toughness and durability.
- Chemical resistance: HDPE offers good resistance to many chemicals, including acids, alcohols, bases, and esters. This makes it suitable for products exposed to harsh chemicals.
- Moisture resistance: HDPE has excellent moisture resistance, making it ideal for products that will be exposed to water or humidity.
- Versatility: HDPE can be easily colored, painted, printed on, or laser-engraved, allowing for a wide range of customization options to meet specific design requirements.
- Recyclability: HDPE is a recyclable material, which can help manufacturers meet sustainability goals and reduce environmental impact.
However, HDPE plastic also has some disadvantages, like limited temperature resistance or flammability. If you are considering whether to use HDPE as an injection molding material, it’s important to evaluate your product’s specific requirements and the properties of HDPE to determine if it’s a good fit.
The Process of HDPE Plastic Injection Molding
The HDPE injection molding process involves several key steps.
First, HDPE resin in pellet form is fed into the barrel of the injection molding machine, where it is heated and melted to a moldable state. The molten HDPE is then injected under high pressure into a mold cavity, which is clamped shut by the machine.
As the hot plastic fills the mold, it is subjected to high shear forces that help mix and homogenize the material.
Once the mold is filled, the HDPE cools and solidifies into the shape of the mold cavity. Careful control of the cooling rate is critical to prevent warping, distortion, or cracking of the part.
After sufficient cooling time, the mold opens, and the solidified part is ejected. The mold then closes, and the process repeats for the next part.
Things Worth Knowing in the HDPE Injection Molding Process
Several important factors must be considered and controlled during HDPE injection molding to ensure high quality parts.
The melt temperature, injection pressure, injection speed, mold temperature, and cooling time are key process parameters that influence the final part properties. The mold design, including wall thickness, gate and runner system, and cooling channels, is also critical.
Compared to other plastics, HDPE has a relatively high coefficient of thermal expansion, which can lead to shrinkage and warpage issues if not properly accounted for.
- Melt Temperature: The recommended melt temperature range for HDPE is typically between 400-535°F (200-280°C). For high molecular weight grades, a slightly narrower range of 392-482°F (200-250°C) is suggested to minimize degradation
- Injection Pressure: Injection pressures for HDPE typically range from 10,000-15,000 psi (70-105 MPa). The pressure required depends on part geometry, wall thickness, and flow path. Thin-walled parts may need pressures up to 26,000 psi (180 MPa).
- Injection Speed: A fast injection speed is generally recommended for HDPE, especially for thin-walled parts, to ensure complete mold filling before the melt cools and freezes off.
- Mold Temperature: The mold temperature for HDPE ranges from 50-95°F (10-35°C) for parts with wall thickness over 0.24 in (6 mm), and up to 175°F (80°C) for thinner parts under 0.24 in (6 mm). Higher mold temperatures provide a glossier surface finish but increase cooling time. The mold temperature should be uniform to minimize differential cooling shrinkage and warpage.
- Cooling Time: Cooling time is the longest portion of the injection molding cycle for HDPE, often 80-85% of the total cycle time. Typical cooling times range from 10 seconds for 0.08 in (2 mm) thick parts to over 30 seconds for 0.16 in (4 mm) thick parts. Premature ejection can cause warpage and distortion.
- Coefficient of Thermal Expansion: HDPE has a relatively high coefficient of linear thermal expansion (CLTE) compared to other plastics, typically around 6-8 x 10^-5 in/in/°F (10-14 x 10^-5 cm/cm/°C). This means HDPE parts have high mold shrinkage, typically 1.5-4%, depending on the grade and processing conditions.
The Applications of HDPE Products
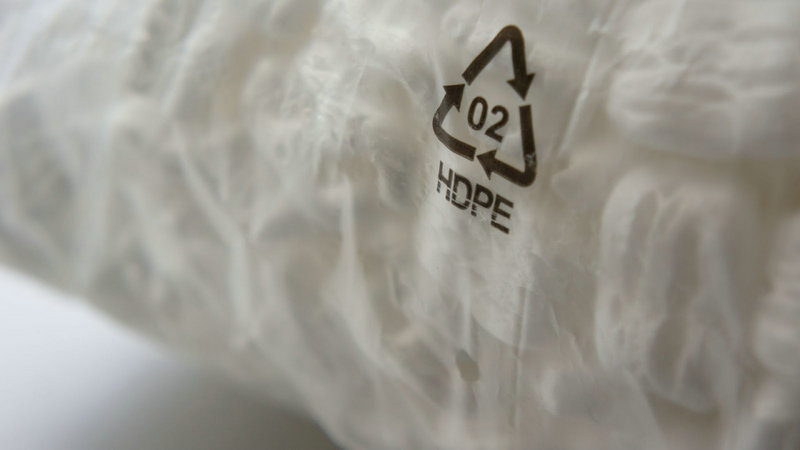
- Packaging and Containers
- Food and beverage containers, such as milk jugs, shampoo bottles, and cereal box liners
- Chemical containers for cleaning products, detergents, and industrial chemicals
- Cosmetic and personal care packaging, like face wash, lotion, and medicine bottles
- Pipes and Piping Systems
- Water and gas pipes for residential, commercial, and industrial use
- Underground and above-ground piping applications
- Replacement for concrete and steel pipes in various industries
- Construction and Infrastructure
- HDPE pipes for water mains, sewers, and drinking water lines
- Plastic lumber as a substitute for traditional wood in decking and boardwalks
- Agriculture
- Irrigation pipes, tube well pipes, and drip irrigation systems
- Pesticide spraying systems
- Greenhouse covers, walk-in tunnels, and mulching films
- Healthcare and Medical Applications
- Medical products such as patches, personal protective equipment, and packaging films
- Food-grade HDPE is safe for direct contact with food and beverages
- Consumer Goods and Household Products
- Toys, utensils, buckets, and kitchenware
- Garbage containers, ice boxes, and housewares
- Industrial Applications
- Processing equipment and machinery components
- Corrosion-resistant liners for tanks and containers
- Flexible HDPE pipes for slurry, effluents, and chemical transport in various industries
- Marine and Outdoor Applications
- Boat components, pool equipment, and marine decking
- UV-resistant outdoor furniture and playground equipment
- Electrical and Electronics
- Wire and cable insulation using crosslinked polyethylene or PE copolymers
In summary, HDPE’s unique properties make it a versatile material suitable for a wide array of applications, ranging from everyday consumer products to specialized industrial uses. Its durability, chemical resistance, and moisture resistance, combined with its cost-effectiveness and recyclability, have made HDPE a popular choice across multiple sectors.
Frequently Asked Questions
Which HDPE injection molding machines are recommended for small businesses?
For small businesses, benchtop or small-scale injection molding machines that offer precision control of temperature and pressure are recommended. Look for machines from reputable manufacturers that cater to small-scale production and offer after-sales support.
What is the difference between HDPE and LDPE?
While HDPE and LDPE are types of polyethylene with similar properties, HDPE has a more linear structure, higher density, greater strength and rigidity, and better heat and chemical resistance. LDPE, on the other hand, is more flexible, transparent, and has a lower melting point, making it suitable for applications requiring these properties.
What other molding methods are commonly used to produce HDPE besides injection molding?
Blow molding, rotational molding, compression molding, and extrusion are also widely used depending on the type of product being manufactured.