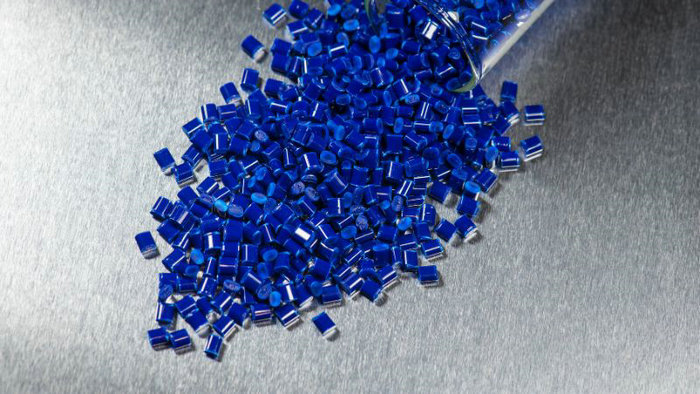
Thermoplastics are one of the most widely used types of plastics today due to their versatility and cost-effectiveness. They can be easily reshaped and remolded multiple times by heating and cooling. This makes them ideal for a variety of manufacturing applications.
There are several key processes used to manufacture thermoplastics on an industrial scale. The main ones are extrusion, injection molding, blow molding, and thermoforming. The exact process used depends on the type of plastic resin and the desired shape and properties of the final product.
This article will give an overall introduction to thermoplastics and how they are manufactured.
Composition of Thermoplastics
When you think about thermoplastics, you’re looking at a world where simple molecules form complex structures. These materials are essential in everything from packaging to automotive parts.
Polymer Basics
Thermoplastic starts with monomers, small molecules that link together like a chain. When heated in a process called polymerization, these monomers create polymer chains. Imagine it as a train where each carriage is a monomer, and the whole train is the polymer.
- Polyethylene (PE): Often used for plastic bags, it’s kind of the poster child for thermoplastics.
- Polyvinyl Chloride (PVC): Pipes and window frames usually get their sturdiness from PVC.
- Polystyrene (PS): Think of packaging and disposable coffee cups, that’s your polystyrene at work.
- Nylon (Polyamide): It’s not just for stockings—gear wheels and cable ties need nylon’s strength too.
- Polypropylene (PP): A go-to for containers and car parts, PP is known for its versatility.
- Polycarbonate (PC): Your glasses could be using PC for that clear but tough quality.
Types of thermoplastic
Some common examples of thermosetting plastics include:
- Epoxy resin – used in coatings, adhesives, composites
- Polyester resin – used in fiberglass composites
- Phenolic resins – used in adhesives, coatings, electrical components
- Melamine formaldehyde – used in tableware, laminates, dry erase boards
- Urea formaldehyde – used in electrical fittings, adhesives
- Silicone – used for seals, gaskets, coatings
Additives and Modifiers
Sometimes, thermoplastics need a bit of a boost. Here’s where additives and modifiers come into play.
- Fillers: They can reinforce strength without breaking the bank.
- Stabilizers: Your outdoor furniture stays solid in the sun thanks to UV stabilizers.
- Plasticizers: PVC gets its flexibility from these, making it great for cables or synthetic leather.
Think of additives as the secret spices that chefs use to perfect their dishes; they fine-tune the properties of your plastics.
Thermoplastics Manufacturing Processes
When you’re looking at how thermoplastics are brought to life, you’ll stumble upon a few key techniques. They all start with raw plastic material, usually in the form of resins, which are then transformed into a variety of products using heat and pressure. Let’s walk through some of the most popular methods.
Injection Molding
In injection molding, you’ve got your plastic granules melted and then injected into a mold under high pressure. It’s a go-to for producing a massive range of items, from car parts to containers. The real deal here is the mold—super precise, often complex, and a bit costly. But once you’ve invested in it, you can pump out tons of parts with consistent quality.
Extrusion
Extrusion is like squeezing toothpaste out of a tube but way hotter and with plastic. It’s continually pushing the melted plastic through a die to shape it into long tubes, rods, or sheets. Extrusion is more about long, continuous shapes, so if that’s what you need, it’s usually more cost-effective than injection molding.
Thermoforming
With thermoforming, you’re heating a plastic sheet until it’s pliable, then draping it over a mold. A vacuum sucks the air out, making the sheet hug the mold tightly. It’s not as detail-oriented as injection molding, but it’s great for larger, thinner items like disposable cups or trays.
3D Printing
And let’s not forget 3D printing. You’re basically laying down layers of melted plastic according to a digital model, creating complex shapes that other methods can’t handle. It’s not as fast as injection molding or extrusion for bulk manufacturing, but for prototypes or bespoke pieces, it’s a game-changer.
Blow Molding
Thermoplastic tubing is extruded and then clamped into a mold while still hot and soft. Compressed air is blown into the tube, inflating it to take the shape of the mold. Used to make hollow plastic containers and parts like bottles, tanks, etc.
Calendering
Thermoplastic sheets are produced by squeezing melted plastic between large rollers to form uniform sheets. Used to produce PVC flooring, plastic films, etc.
Properties and Performance
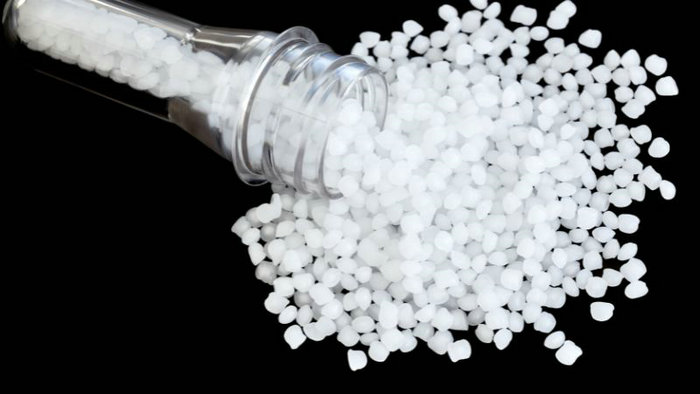
You’re about to get up close with the properties that make thermoplastics a go-to material in various industries. Whether it’s their versatility or durability, these materials are all about top-notch performance.
Physical and Mechanical Properties
Thermoplastics boast a wide range of physical and mechanical properties which can be either amorphous or crystalline in structure, affecting their performance. Amorphous thermoplastics are known for being more pliable and less brittle, while the crystalline types typically offer higher strength and resistance to heat. Most are known for their lightweight nature coupled with significant mechanical robustness. The glass transition temperature is a crucial number for you to watch out for—it tells you when the material will soften under heat, which speaks volumes about its use-case scenarios.
Thermal and Chemical Resistance
These materials aren’t just tough; they’ve got some serious resistance to offer. Thermal stability is a hallmark of thermoplastics, meaning they can maintain their properties over a wide temperature range, from chilly room temperatures upwards. However, the exact range does depend on the specific polymer. Their chemical resistance makes them a hit in environments where they’re exposed to chemicals that could degrade other materials. This resistance, however, can vary based on the polymer’s structure—amorphous or crystalline—so you’ll want to choose wisely depending on what kind of environment your material will face.
Impact and Tensile Strength
The impact resistance of thermoplastics can be remarkably high. Plus, their tensile strength—how much force they can handle before they break—is nothing to scoff at with values like 333 MPa in some fiber-reinforced thermoplastic composites.
Applications in Various Industries
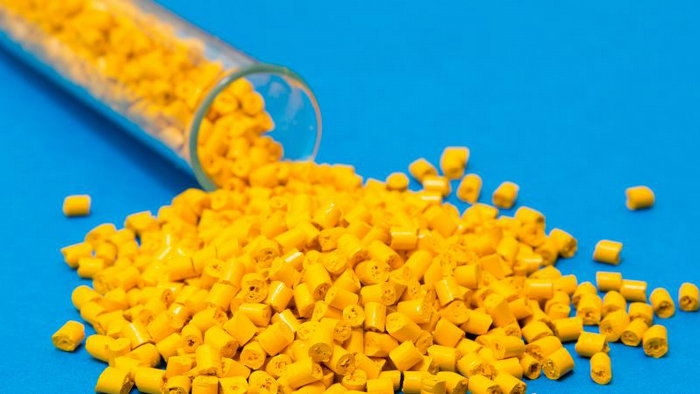
Thermoplastics have wormed their way into pretty much every nook and cranny of modern manufacturing. They’re super versatile, so you’ll spot them in a bunch of different industries. Let’s take a look at some specific sectors where thermoplastics are doing their thing.
Construction and Piping
You’ve got pipes to lay, and thermoplastics are your go-to. PVC and ABS are stars in this game—affordable and easy to install, they make up the guts of many plumbing systems. They resist water, chemicals, and corrosion like champs, which is why they’re everywhere in your home and office.
Automotive and Aerospace
In the automotive world, it’s all about making things lighter and more fuel-efficient. Thermoplastics are the unsung heroes here, helping to reduce weight without skimping on performance. Think of everything from your dash to the fuel line. Even in aerospace, these materials are a big deal for similar reasons—lighter aircraft mean less fuel and more efficiency.
Medical Equipment
When it comes to medical gear, you want materials that are clean and safe. Thermoplastics come to the rescue again, as they’re used in a ton of disposables – like syringes and blood bags.
Packaging Solutions
Check out any supermarket shelf, and you’ll see why thermoplastics are the kings of packaging. Plus, you can mold them into just about any shape or size—handy.
Sustainability and Recyclability
When you’re dealing with thermoplastics, sustainability is a big deal. You’ve got to consider how your plastics are made and what happens to them at the end of their life cycle. Luckily, most thermoplastics are recyclable. This means they can be re-melted and reshaped, reducing the need for new materials and minimizing waste.
- Recycling: It’s pretty straightforward with thermoplastics. Heat them up, and they’ll go back to being liquid, ready to be formed into something new.
Recycling your thermoplastics is usually a win, cutting down on both trash and the demand for virgin resources. But consider this: if your plastics are contaminated or not sorted correctly, that can mess with the recycling process.
Here’s the score:
Factor | Impact on Sustainability |
---|---|
Recycling | Positive effect |
Contamination | Negative effect |
Composting (if viable) | Positive effect |
So, your choices play a big part here. The more you focus on renewables and proper waste management, the better off the environment will be.