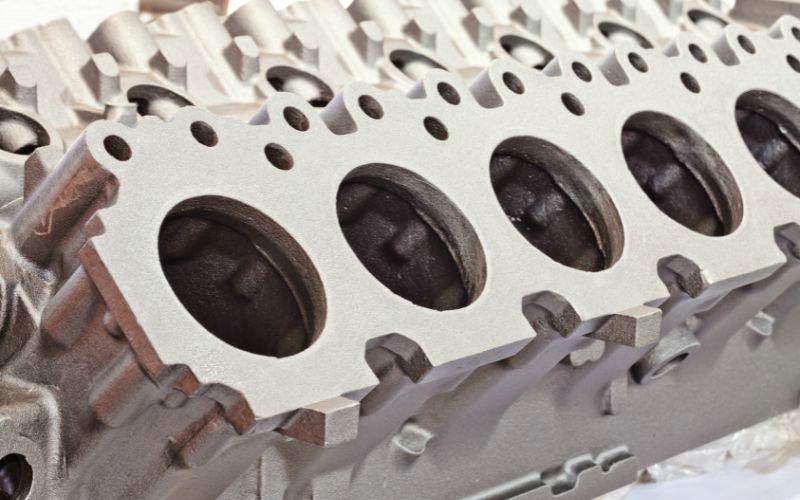
What Is Die Casting?
Die casting is a manufacturing process that involves pouring or injecting molten metal into molds, known as dies. The metal typically used in this process can include zinc, aluminum, and their alloys. Yours is a journey through a procedure widely adopted for its efficiency in high-volume production runs.
When you initiate die casting, metal is melted in a furnace and then injected into the dies under high pressure. This method is popular for its ability to produce parts with precision, intricate details, and excellent surface finish—qualities demanded in sectors like automotive, aerospace, and electronics.
Die casting is highly sought after by manufacturers because of its ability to produce uniform parts with consistent quality. Whether you’re using it to create intricate gearbox components for vehicles or sleek, durable casings for electronics, die casting stands as a pillar of modern manufacturing, especially when precision and volume are of the essence.
Die Casting Process
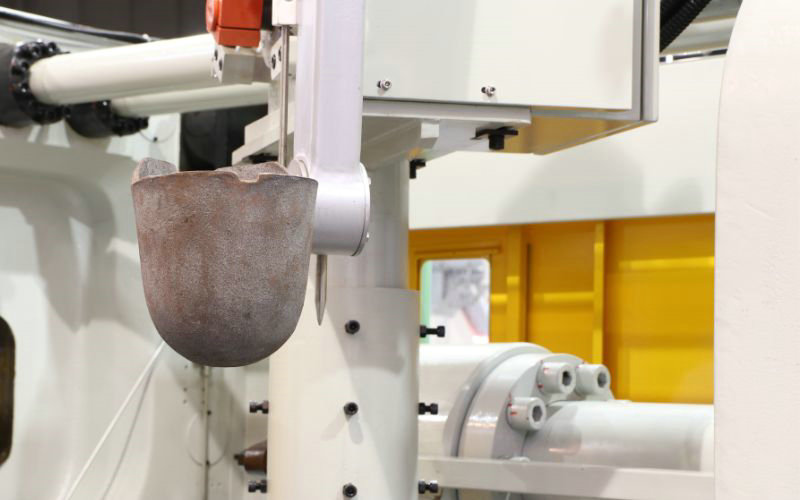
There are three main types of die casting processes: gravity die casting, cold chamber die casting, and hot chamber die casting.
Gravity Die Casting
In gravity die casting, molten metal is poured directly from a ladle into a semi-permanent or permanent die. The cavity fills with no force other than gravity. The advantages of gravity die casting include the ability to produce dense, high-quality castings with excellent mechanical properties suitable for heat treatment. It is cost-effective for small to medium volume production.
Cold Chamber Die Casting
In cold chamber die casting, the melting furnace is located separately from the die casting machine. For each cycle, a precise amount of molten metal is ladled into the machine’s unheated shot chamber; then, a hydraulic plunger forces the metal into the die under high pressures between 2,000-20,000 psi. Cold chamber die casting is used for alloys with higher melting points like aluminum. It produces strong, durable parts but has slower cycle times than a hot chamber.
Hot Chamber Die Casting
In hot chamber die casting, the injection mechanism is submerged in a pool of molten metal, which is fed into the die through a gooseneck and piston. At the start of each cycle, the piston retracts, allowing the gooseneck to fill with molten metal. The piston then forces the metal through the gooseneck into the die at pressures of 1,000-5,000 psi. Hot chamber die casting is used for alloys with low melting points like zinc and magnesium. It enables faster cycle times and can produce intricate parts with reduced porosity.
Die Casting Applications
Automotive: Die casting is extensively employed in the automotive sector. You will find components such as engine blocks, transmission parts, and structural elements made through this process. The ability to produce strong, durable parts quickly and efficiently makes die casting a go-to choice for automotive engineers.
- Engine Components
- Gearboxes
- Car Frames
Aerospace: The aerospace industry values die casting for creating complex parts that require precision and can withstand harsh conditions. Components such as landing gear, cockpit instrumentation, and engine parts are typically die cast.
- Instrumentation Housings
- Landing Gear Parts
- Engine Components
Electronics: In electronics, die casting is used to create items like connectors, housings, and heat sinks. These parts benefit from die casting’s ability to form complex designs with a high level of thermal conductivity.
- Heat Sinks
- Connectors
- Enclosures
What Is Metal Injection Molding?
Metal Injection Molding (MIM) offers you a manufacturing process for producing intricate parts in medium to high volumes. MIM combines the freedom of design and complexity of shapes found in plastic injection molding with the exceptional strength and integrity of metal.
Here’s a concise overview of MIM:
- Materials: Your choice of materials in MIM typically includes ferrous metals such as stainless steel, which provides significant strength and durability to the final product.
- Strength and Precision: MIM parts are known for their impressive strength and precision. They maintain tight tolerances, making them suitable for both industrial and medical applications.
- Complex Geometries and Thin Walls: With MIM, you’re able to create parts with complex geometries and thin walls, which might be challenging or impossible through traditional metalworking processes.
Metal Injection Molding Process
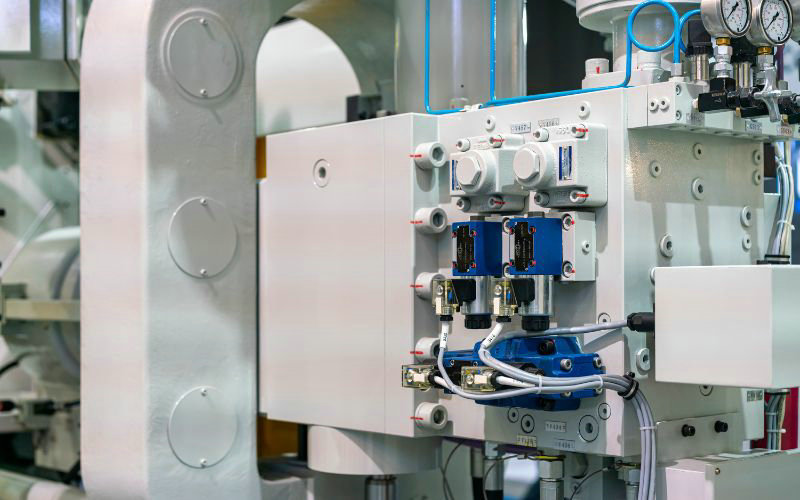
Your understanding of MIM starts with its primary material — a feedstock that consists of fine metal powder and a polymer binder material. Common metals used in this process include stainless steel, titanium, nickel alloys, and copper alloys. In its initial stages, MIM is akin to plastic injection molding; the feedstock is heated until it becomes viscous and can be injected into a mold cavity.
Once your molded part is set, the debinding process begins. This entails removing the majority of the binder, which prepares the part for sintering. During sintering, your part is exposed to high temperatures that bind the metal particles together and ensure integrity.
Post-sintering, you’ll find that the part has shrunk significantly — typically between 15-20%. However, the sintering process enables you to achieve excellent dimensional accuracy and surface finish, often minimizing the need for subsequent machining. MIM is highly cost-effective when it comes to producing small parts in large volumes due to lower material waste and the ability to maintain tight tolerances without extensive finishing work.
Ultimately, metal injection molding offers a unique blend of quality, efficiency, and versatility within manufacturing processes. Its ability to use a variety of metals and achieve specific material characteristics — such as hardness, tensile strength, and temperature resistance — makes it a valuable process across numerous industries.
Metal Injection Molding (MIM) Applications
Metal injection molding (MIM) is precise and cost-effective, and it is suited particularly for the mass production of small- to medium-sized components. You’ll find MIM applications across various industries due to its ability to produce complex shapes with excellent surface finish.
Aerospace and Automotive:
- MIM is ideal for manufacturing parts such as door handles, hinges, and engine components due to its high strength and durability.
Medical and Dental:
- The medical industry benefits from MIM’s precision in creating surgical tools, implants, and brackets which require bio-compatibility.
Consumer Electronics:
- Small components like mobile phone parts or camera assemblies exploit MIM’s prowess in miniaturization and detailed design capabilities.
Firearms Industry:
- MIM is used for fabricating various firearm components, including triggers, hammers, and sight parts that demand strict tolerances and strength.
General Industrial Equipment:
- You’ll find MIM in the production of pump components, connectors, and valves due to its high-volume production capabilities and consistency.
In these applications, MIM provides benefits that include:
- High-density materials with great mechanical properties
- Ability to integrate features like threads, gears, and internal channels without secondary operations
- Production of parts close to final shape, minimizing waste
Die Casting vs MIM: Advantages and Disadvantages
Advantages of MIM over Die Casting
1. MIM can produce small, complex parts with intricate features and thin walls that would be challenging or impossible with die casting.
2. MIM offers a wider range of materials, including ferrous metals, stainless steels, titanium, and nickel alloys. Die casting is typically limited to non-ferrous metals like aluminum, zinc, and magnesium.
3. MIM parts have excellent mechanical properties, high strength, and wear resistance due to the sintering process.
4. MIM provides tighter tolerances and can be accurate to within 0.3mm.
5. MIM has virtually no waste because all material is injected directly into the mold.
Disadvantages of MIM compared to Die Casting
1. MIM is generally more expensive than die casting due to the complex tooling and multiple processing steps.
2. MIM has a lower die lifespan (150k-300k shots) compared to die casting (over 1 million shots).
3. MIM parts can shrink significantly (up to 30%) during sintering, requiring careful mold design. Die casting has much lower shrinkage.
4. MIM has high initial automation and setup costs.
Advantages of Die Casting over MIM
1. Die casting is typically cheaper than MIM, up to 30% less expensive in some cases.
2. Die casting has a longer die life (over 1 million shots) compared to MIM (150k-300k shots).
3. Die casting requires no secondary operations after the part is ejected from the mold.
4. Die casting can accommodate inserts and parts made of other materials embedded into the casting.
Disadvantages of Die Casting compared to MIM
1. Die casting struggles with producing small, intricate parts with fine features and thin walls.
2. Die casting is limited to mostly non-ferrous metals. Ferrous metals have very high melting points, which reduce the die life.
3. Porosity due to entrapped gases is a common issue in die casting, reducing mechanical strength.
4. Die casting requires costly dies to withstand the high pressure and molten metal temperatures.
In summary, MIM excels at producing small, complex parts with excellent mechanical properties in a wide range of materials. However, it is more expensive and has a longer cycle time than die casting. Die casting is more economical and suitable for simpler, larger parts in non-ferrous metals with faster production times but struggles with intricate features and porosity.
Comparison: Metal Injection Molding vs. Die Casting
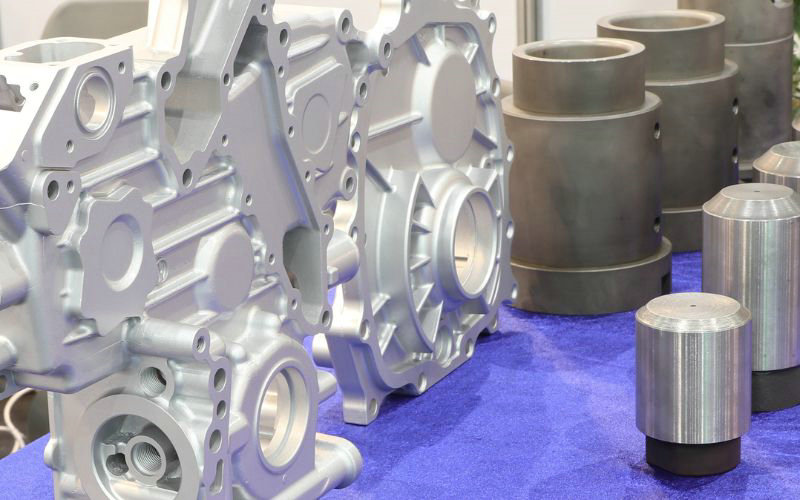
1. Accuracy & Tolerances
Metal Injection Molding (MIM): MIM achieves very precise parts with relatively tight tolerances, typically accurate to within 0.3mm. This precision is due to the fine metal powders used, which allow for detailed and complex geometries.
Die Casting: Die casting generally offers good dimensional accuracy but not as high as MIM. The typical tolerance for die casting is around ±0.0005 inches, which is less precise compared to MIM’s capabilities. Variations in dimensions often require additional trimming to meet specifications.
2. Needed Materials
Metal Injection Molding (MIM): MIM can utilize a wide range of materials, including ferrous and non-ferrous metals, stainless steels, titanium, and nickel alloys. This versatility allows for the production of parts with specific properties tailored to various applications.
Die Casting: Primarily uses non-ferrous metals such as aluminum, zinc, and magnesium. While die casting can use ferrous metals, these materials have very high melting points, which can reduce mold life significantly.
3. Speed Comparison
Metal Injection Molding (MIM): The MIM process involves multiple steps, including mixing, injection molding, debinding, and sintering, which makes it generally slower than die casting. However, once the production is set up, MIM can efficiently produce large volumes of parts.
Die Casting: Known for its rapid production capability, die casting is faster, particularly suitable for high-volume production runs. The process allows for the quick creation of large parts due to its high-pressure injection techniques.
4. Surface Finish
Metal Injection Molding (MIM): Typically provides a high-quality surface finish that often does not require additional post-processing. The sintering process helps in achieving a smooth finish.
Die Casting: Parts usually come out of the mold with a good surface finish but might require some trimming of excess metal. The surface quality is generally considered medium compared to MIM.
5. Manufacturing Costs
Metal Injection Molding (MIM): While the initial setup and tooling costs can be high, MIM can be cost-effective for producing complex parts in large volumes due to reduced waste and minimal post-processing needs.
Die Casting: Generally less expensive in terms of initial costs and is more cost-effective for larger parts and high-volume production. However, the cost-effectiveness decreases for highly complex or smaller parts.
6. Mold Differences
Metal Injection Molding (MIM): Molds used in MIM can be less durable compared to die casting, typically supporting around 150,000 to 300,000 shots. However, MIM molds allow for greater complexity in part design.
Die Casting: Molds are designed to withstand high pressures and temperatures, making them more durable, with a life expectancy of over 1 million shots. However, they offer less flexibility in terms of part complexity compared to MIM molds.