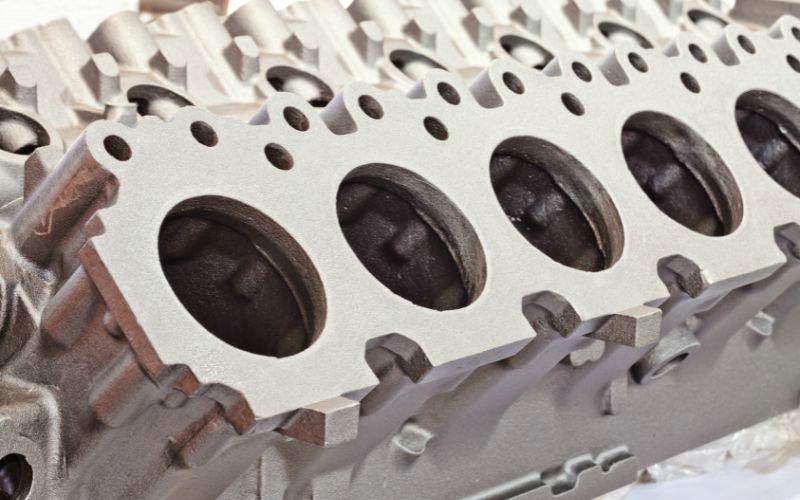
Cos'è la pressofusione?
La pressofusione è un processo di produzione che prevede il versamento o l'iniezione di metallo fuso in stampi, noti come muore. Il metallo tipicamente utilizzato in questo processo può includere zinco, alluminio e relative leghe. Il tuo è un viaggio attraverso una procedura ampiamente adottata per la sua efficienza nelle produzioni di grandi volumi.
Quando si avvia la pressofusione, il metallo viene fuso in un forno e quindi iniettato negli stampi ad alta pressione. Questo metodo è popolare per la sua capacità di produrre parti con precisione, dettagli complessi e un'eccellente finitura superficiale, qualità richieste in settori come quello automobilistico, aerospaziale ed elettronico.
La pressofusione è molto ricercata dai produttori per la sua capacità di produrre parti uniformi con qualità costante. Che tu la utilizzi per creare complessi componenti del cambio per veicoli o involucri eleganti e durevoli per dispositivi elettronici, la pressofusione rappresenta un pilastro della produzione moderna, soprattutto quando precisione e volume sono essenziali.
Processo di pressofusione
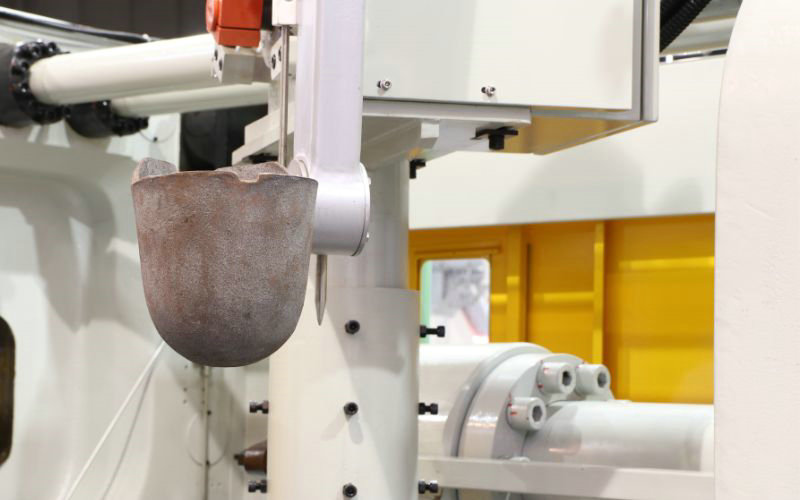
Esistono tre tipi principali di processi di pressofusione: pressofusione a gravità, pressofusione a camera fredda e pressofusione a camera calda.
Pressofusione per gravità
Nella pressofusione a gravità, il metallo fuso viene versato direttamente da una siviera in uno stampo semipermanente o permanente. La cavità si riempie senza altra forza oltre alla gravità. I vantaggi della pressofusione a gravità includono la capacità di produrre getti densi e di alta qualità con eccellenti proprietà meccaniche adatte al trattamento termico. È conveniente per la produzione di volumi medio-piccoli.
Pressofusione a camera fredda
Nella pressofusione a camera fredda, il forno fusorio è situato separatamente dalla macchina di pressofusione. Per ogni ciclo, una quantità precisa di metallo fuso viene versata nella camera di iniezione non riscaldata della macchina; quindi, uno stantuffo idraulico spinge il metallo nello stampo ad alte pressioni comprese tra 2.000 e 20.000 psi. La pressofusione a camera fredda viene utilizzata per le leghe con punti di fusione più elevati come l'alluminio. Produce parti resistenti e durevoli ma ha tempi di ciclo più lenti rispetto a una camera calda.
Pressofusione a camera calda
Nella pressofusione a camera calda, il meccanismo di iniezione è immerso in una vasca di metallo fuso, che viene alimentato nello stampo attraverso un collo di cigno e un pistone. All'inizio di ogni ciclo, il pistone si ritrae, consentendo al collo di cigno di riempirsi di metallo fuso. Il pistone spinge quindi il metallo attraverso il collo di cigno nello stampo a pressioni di 1.000-5.000 psi. La pressofusione a camera calda viene utilizzata per leghe con basso punto di fusione come zinco e magnesio. Consente tempi di ciclo più rapidi e può produrre parti complesse con porosità ridotta.
Applicazioni di pressofusione
Settore automobilistico: La pressofusione è ampiamente utilizzata nel settore automobilistico. Troverai componenti come blocchi motore, parti di trasmissione ed elementi strutturali realizzati attraverso questo processo. La capacità di produrre parti resistenti e durevoli in modo rapido ed efficiente rende la pressofusione una scelta obbligata per gli ingegneri automobilistici.
- Componenti del motore
- Riduttori
- Telai per auto
Aerospaziale: L'industria aerospaziale apprezza la pressofusione per la creazione di parti complesse che richiedono precisione e può resistere a condizioni difficili. Componenti come il carrello di atterraggio, la strumentazione della cabina di pilotaggio e le parti del motore sono generalmente pressofusi.
- Alloggiamenti per strumentazione
- Parti del carrello di atterraggio
- Componenti del motore
Elettronica: Nell'elettronica, la pressofusione viene utilizzata per creare articoli come connettori, alloggiamenti e dissipatori di calore. Queste parti beneficiano della capacità della pressofusione di formare progetti complessi con un elevato livello di conduttività termica.
- Dissipatori di calore
- Connettori
- Recinzioni
Che cos'è lo stampaggio a iniezione di metalli?
Lo stampaggio ad iniezione di metalli (MIM) offre un processo di produzione per la produzione di parti complesse in volumi medio-alti. MI M combina la libertà di progettazione e la complessità delle forme tipiche dello stampaggio a iniezione di materie plastiche con l'eccezionale resistenza e integrità del metallo.
Ecco una panoramica concisa di MIM:
- Materiali: La scelta dei materiali in MIM include in genere metalli ferrosi come l'acciaio inossidabile, che fornisce notevole resistenza e durata al prodotto finale.
- Forza e precisione: Le parti MIM sono note per la loro forza e precisione impressionanti. Mantengono tolleranze strette, rendendoli adatti ad entrambi industriale E medico applicazioni.
- Geometrie complesse e pareti sottili: Con MIM è possibile creare parti con geometrie complesse e pareti sottili, cosa che potrebbe risultare impegnativa o impossibile attraverso i tradizionali processi di lavorazione dei metalli.
Processo di stampaggio ad iniezione di metalli
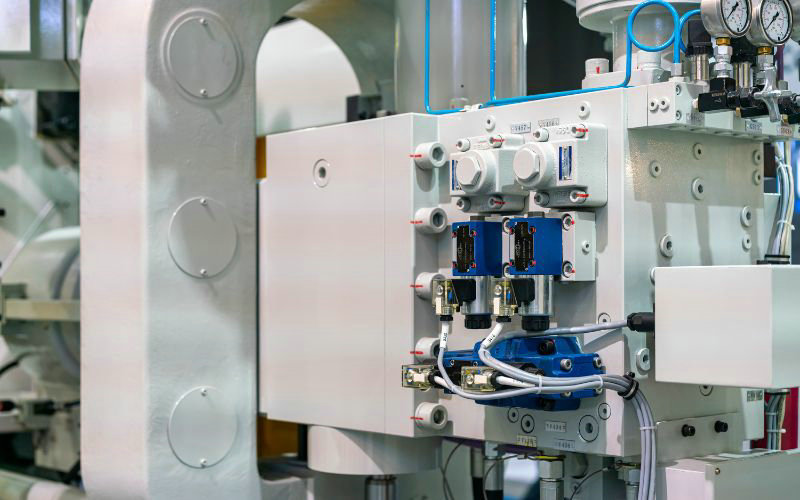
La tua comprensione del MIM inizia con il suo materiale principale: a materia prima costituito da polvere metallica fine e un materiale legante polimerico. I metalli comuni utilizzati in questo processo includono acciaio inossidabile, titanio, leghe di nichel e leghe di rame. Nelle sue fasi iniziali, il MIM è simile allo stampaggio a iniezione di materie plastiche; la materia prima viene riscaldata fino a diventare viscosa e può essere iniettata nella cavità dello stampo.
Una volta impostata la parte stampata, inizia il processo di deceraggio. Ciò comporta la rimozione della maggior parte del legante, che prepara la parte per la sinterizzazione. Durante la sinterizzazione, la parte è esposta a temperature elevate che legano insieme le particelle metalliche e ne garantiscono l'integrità.
Dopo la sinterizzazione, scoprirai che la parte si è ridotta in modo significativo, in genere tra 15-20%. Tuttavia, il processo di sinterizzazione consente di ottenere un'eccellente precisione dimensionale e finitura superficiale, spesso riducendo al minimo la necessità di lavorazioni successive. Il MIM è estremamente conveniente quando si tratta di produrre piccole parti in grandi volumi grazie al minor spreco di materiale e alla capacità di mantenere tolleranze strette senza estesi lavori di finitura.
In definitiva, lo stampaggio a iniezione di metalli offre una miscela unica di qualità, efficienza e versatilità nei processi di produzione. La sua capacità di utilizzare una varietà di metalli e di ottenere caratteristiche specifiche del materiale, come durezza, resistenza alla trazione e resistenza alla temperatura, lo rende un processo prezioso in numerosi settori.
Applicazioni di stampaggio ad iniezione di metalli (MIM).
Lo stampaggio a iniezione di metalli (MIM) è preciso ed economico ed è particolarmente adatto per la produzione in serie di componenti di piccole e medie dimensioni. Troverai applicazioni MIM in vari settori grazie alla sua capacità di produrre forme complesse con eccellente finitura superficiale.
Aerospaziale e automobilistico:
- MIM è ideale per la produzione di parti come maniglie di porte, cerniere e componenti del motore grazie alla sua elevata resistenza e durata.
Medicina e odontoiatria:
- L'industria medica trae vantaggio dalla precisione di MIM nella creazione di strumenti chirurgici, impianti e attacchi che richiedono biocompatibilità.
Elettronica di consumo:
- Piccoli componenti come parti di telefoni cellulari o gruppi di fotocamere sfruttano l'abilità di MIM nella miniaturizzazione e nelle capacità di progettazione dettagliata.
Industria delle armi da fuoco:
- Il MIM viene utilizzato per fabbricare vari componenti di armi da fuoco, inclusi grilletti, martelli e parti di mira che richiedono tolleranze e resistenza rigorose.
Attrezzature industriali generali:
- Troverai MIM nella produzione di componenti per pompe, connettori e valvole grazie alle sue capacità e coerenza di produzione in grandi volumi.
In queste applicazioni, MIM offre vantaggi che includono:
- Materiali ad alta densità con grandi proprietà meccaniche
- Capacità di integrare funzionalità come filettature, ingranaggi e canali interni senza operazioni secondarie
- Produzione di pezzi prossimi alla forma finale, riducendo al minimo gli scarti
Pressocolata vs MIM: vantaggi e svantaggi
Vantaggi del MIM rispetto alla pressofusione
1. MIM può produrre parti piccole e complesse con caratteristiche complesse e pareti sottili che sarebbero difficili o impossibili con la pressofusione.
2. MIM offre una gamma più ampia di materiali, inclusi metalli ferrosi, acciai inossidabili, titanio e leghe di nichel. La pressofusione è generalmente limitata ai metalli non ferrosi come alluminio, zinco e magnesio.
3. Le parti MIM hanno eccellenti proprietà meccaniche, elevata robustezza e resistenza all'usura grazie al processo di sinterizzazione.
4. Il MIM offre tolleranze più strette e può avere una precisione fino a 0,3 mm.
5. MIM non presenta praticamente alcuno spreco perché tutto il materiale viene iniettato direttamente nello stampo.
Svantaggi del MIM rispetto alla pressofusione
1. Il MIM è generalmente più costoso della pressofusione a causa della complessità degli utensili e delle molteplici fasi di lavorazione.
2. Il MIM ha una durata dello stampo inferiore (150.000-300.000 scatti) rispetto alla pressofusione (oltre 1 milione di scatti).
3. Le parti MIM possono ridursi in modo significativo (fino a 30%) durante la sinterizzazione, richiedendo un'attenta progettazione dello stampo. La pressofusione ha un ritiro molto inferiore.
4. MIM presenta costi iniziali di automazione e configurazione elevati.
Vantaggi della pressofusione rispetto al MIM
1. La pressofusione è generalmente più economica della MIM, in alcuni casi fino al 30% meno costosa.
2. La pressofusione ha una durata dello stampo più lunga (oltre 1 milione di scatti) rispetto al MIM (150.000-300.000 scatti).
3. La pressofusione non richiede operazioni secondarie dopo l'espulsione della parte dallo stampo.
4. La pressofusione può accogliere inserti e parti costituiti da altri materiali incorporati nella fusione.
Svantaggi della pressofusione rispetto al MIM
1. La pressofusione ha difficoltà a produrre parti piccole e complesse con caratteristiche fini e pareti sottili.
2. La pressofusione è limitata principalmente ai metalli non ferrosi. I metalli ferrosi hanno punti di fusione molto elevati, che riducono la durata dello stampo.
3. La porosità dovuta ai gas intrappolati è un problema comune nella pressofusione, poiché riduce la resistenza meccanica.
4. La pressofusione richiede stampi costosi per resistere all'alta pressione e alle temperature del metallo fuso.
In sintesi, MIM eccelle nella produzione di parti piccole e complesse con eccellenti proprietà meccaniche in un'ampia gamma di materiali. Tuttavia, è più costoso e ha un tempo di ciclo più lungo rispetto alla pressofusione. La pressofusione è più economica e adatta a parti più semplici e più grandi in metalli non ferrosi con tempi di produzione più rapidi ma presenta problemi con caratteristiche complesse e porosità.
Confronto: stampaggio a iniezione di metalli e pressofusione
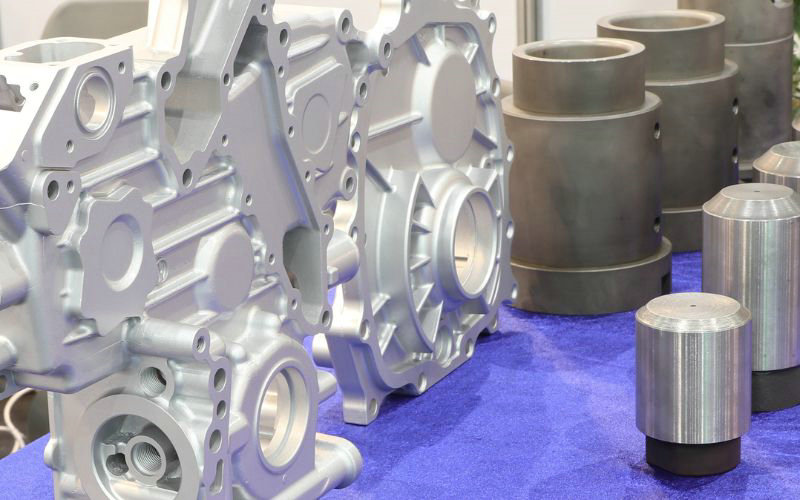
1. Precisione e tolleranze
Stampaggio ad iniezione di metalli (MIM): MIM realizza parti molto precise con tolleranze relativamente strette, in genere con una precisione entro 0,3 mm. Questa precisione è dovuta alle fini polveri metalliche utilizzate, che consentono geometrie dettagliate e complesse.
Pressofusione: La pressofusione offre generalmente una buona precisione dimensionale ma non così elevata come MIM. La tolleranza tipica per la pressofusione è di circa ±0,0005 pollici, che è meno precisa rispetto alle capacità di MIM. Le variazioni nelle dimensioni spesso richiedono rifiniture aggiuntive per soddisfare le specifiche.
2. Materiali necessari
Stampaggio ad iniezione di metalli (MIM): MIM può utilizzare un'ampia gamma di materiali, inclusi metalli ferrosi e non ferrosi, acciai inossidabili, titanio e leghe di nichel. Questa versatilità consente la produzione di parti con proprietà specifiche su misura per varie applicazioni.
Pressofusione: Utilizza principalmente metalli non ferrosi come alluminio, zinco e magnesio. Sebbene la pressofusione possa utilizzare metalli ferrosi, questi materiali hanno punti di fusione molto elevati, che possono ridurre significativamente la durata dello stampo.
3. Confronto di velocità
Stampaggio ad iniezione di metalli (MIM): Il processo MIM prevede più fasi, tra cui miscelazione, stampaggio a iniezione, deceraggio e sinterizzazione, il che lo rende generalmente più lento della pressofusione. Tuttavia, una volta avviata la produzione, MIM può produrre in modo efficiente grandi volumi di parti.
Pressofusione: Noto per la sua capacità di produzione rapida, la pressofusione è più veloce, particolarmente adatta per cicli di produzione di grandi volumi. Il processo consente la creazione rapida di parti di grandi dimensioni grazie alle sue tecniche di iniezione ad alta pressione.
4. Finitura superficiale
Stampaggio ad iniezione di metalli (MIM): Fornisce in genere una finitura superficiale di alta qualità che spesso non richiede ulteriore post-elaborazione. Il processo di sinterizzazione aiuta a ottenere una finitura liscia.
Pressofusione: Le parti escono solitamente dallo stampo con una buona finitura superficiale, ma potrebbero richiedere una rifinitura del metallo in eccesso. La qualità della superficie è generalmente considerata media rispetto al MIM.
5. Costi di produzione
Stampaggio ad iniezione di metalli (MIM): Sebbene i costi iniziali di installazione e attrezzaggio possano essere elevati, il MIM può essere conveniente per la produzione di parti complesse in grandi volumi grazie alla riduzione degli scarti e alle minime esigenze di post-elaborazione.
Pressofusione: Generalmente meno costoso in termini di costi iniziali ed è più conveniente per parti più grandi e produzione in grandi volumi. Tuttavia, il rapporto costo-efficacia diminuisce per parti altamente complesse o più piccole.
6. Differenze di stampo
Stampaggio ad iniezione di metalli (MIM): Gli stampi utilizzati nel MIM possono essere meno durevoli rispetto alla pressofusione, in genere supportano da 150.000 a 300.000 colpi. Tuttavia, gli stampi MIM consentono una maggiore complessità nella progettazione delle parti.
Pressofusione: Gli stampi sono progettati per resistere a pressioni e temperature elevate, rendendoli più durevoli, con un'aspettativa di vita di oltre 1 milione di colpi. Tuttavia, offrono meno flessibilità in termini di complessità delle parti rispetto agli stampi MIM.