Compression molding is a manufacturing process commonly used to produce items made from plastic or composite materials. It involves placing raw material, usually in pellet or granular form, into a pre-heated mold cavity. Once the material is loaded, the mold closes with great force, compressing the material until it takes on the shape of the cavity. This process allows for high-volume, low-cost production of complex parts that would otherwise be difficult or expensive to make.
Compression molding has been used for decades across many industries to create everything from toys and plastic bottles to electrical components. Despite its widespread application, many are still unfamiliar with the specifics of how it works and the advantages it provides. This guide aims to serve as a friendly introduction to the compression molding process and explore the key benefits it offers manufacturers. We’ll look at the basic steps involved, from heating and loading the raw material to cooling and ejecting the finished part. We’ll also discuss how compression molding enables tight tolerances, complex geometries and smooth surface finishes – all at high speeds. By the end, you’ll have a better understanding of this important manufacturing technique.
Understanding Compression Molding
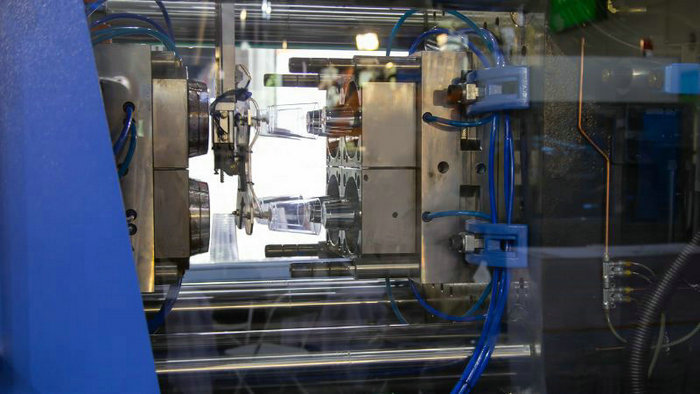
History of Compression Molding
Compression molding has been a reliable method of manufacturing various products made of thermosets, thermoplastics, elastomers, and natural rubbers since the early 1900s. The process has been adopted across numerous industries for its simplicity and efficiency. Its origin can be traced back to the manufacturing of Bakelite, an early plastic material.
Compression Molding vs. injection Molding
When comparing compression molding to injection molding, you’ll notice some key differences. Here’s a brief overview of the two processes to help you understand their distinctions:
- Compression Molding:
- Process: Uncured rubber or softened plastic material is placed into an open, heated mold cavity. The mold is then closed, applying pressure to distribute the material evenly and ensure that it takes the desired shape.
- Cost-effectiveness: Compression molding is often more cost-effective for producing large, simple rubber parts, typically at a lower per-part cost than injection molding.
- Surface Quality: The main advantage of compression molding is its flexibility in producing diverse products with high precision and quality. This process results in good surface quality and dimensional accuracy, making it especially suitable for creating high-volume, temperature-resistant components.
- Injection Molding:
- Process: Molten plastic or rubber material is injected into a mold cavity under high pressure, filling the cavity to create the desired shape.
- Cost-effectiveness: While the initial setup costs can be higher for injection molding compared to compression molding, the process enables rapid production of large volumes of intricate parts.
- Surface Quality: Injection molding also yields good surface quality and dimensional accuracy, but it can typically handle more complex designs and tighter tolerances than compression molding.
Here’s a table summarizing the differences between compression molding and injection molding:
Compression Molding | Injection Molding | |
Process | Heated mold cavity | High-pressure mold cavity |
Cost-effectiveness | More cost-effective for large, simple parts | Economical for high-volume, intricate parts |
Surface Quality | Good | Good |
Complexity | Suited for simpler parts | Suited for intricate parts |
Process of Compression Molding
In this section, we will explore the process of compression molding, which involves three main phases: preheating, molding, and cooling. The process is commonly used to manufacture various plastic or composite parts by applying pressure and heat.
Preheating Phase
During the preheating phase, you need to prepare a pre-measured and preheated material, such as a thermosetting polymer or thermoplastic compound. The charge is heated to the desired temperature until it reaches a uniform and moldable state. Proper preheating is crucial because it helps to reduce cycle times and ensures even material distribution within the mold during the molding phase.
- Pressure: Typically, low to moderate pressure is applied in this phase
- Heat: The charge is heated to the required temperature
- Temperature: Charge temperature should be carefully monitored
Molding Phase
Once your charge is fully preheated, it’s time to put it into the mold cavity. The mold consists of an upper and lower half, and usually possesses a specific shape that conforms to the desired final product. During the molding phase, you’ll need to:
- Place the preheated charge into the open mold cavity
- Close the mold with a top force or plug member
- Apply sufficient pressure to force the material into contact with all parts of the mold
- Maintain heat and pressure until the material has cured
Just like with preheating, it’s essential to monitor and control temperature, pressure, and curing time throughout the molding phase. This ensures that your final product has the desired properties and dimensions.
Cooling Phase
Finally, after the charge has been molded and cured, it’s time for the cooling phase. You’ll need to gradually reduce the temperature of the mold while maintaining appropriate pressure levels. This step is vital for multiple reasons:
- It prevents the part from deforming or warping as it cools
- It helps to achieve the desired dimensional stability and strength
- It ensures easy mold release for easier demolding
Once your part has cooled down sufficiently and reached its final shape, you can carefully remove it from the mold. The newly formed part should have a high-quality surface finish and match the dimensions of the mold cavity.
Remember, each phase of the compression molding process (preheating, molding, and cooling) plays a crucial role in producing the perfect part. By closely monitoring temperature, pressure, curing time, and other factors, you can achieve excellent results in your compression molding projects.
Mold and Equipment
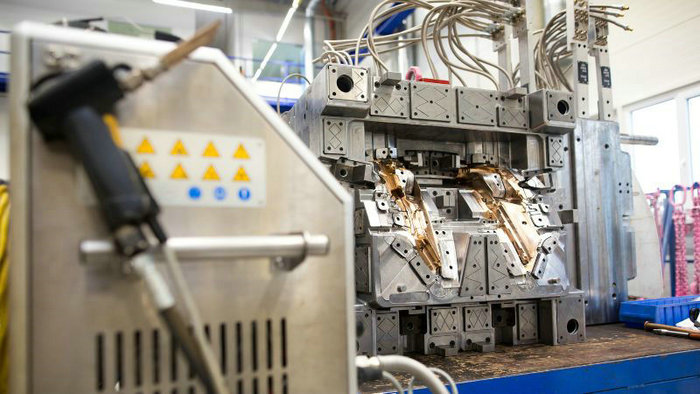
In the compression molding process, the mold plays a crucial role in shaping and forming your desired parts. The mold is typically made of metal, such as steel, and consists of a mold cavity designed to match the shape of your final product.
Tooling is an essential aspect of this process, as it dictates the quality and precision of your molded parts. High-quality tooling ensures that your mold will last for a long period and produce consistent results. Some manufacturers, like Tooling Tech Group, specialize in providing molds for specific applications, such as body panels on the Chevrolet Corvette.
You’ll find that most compression molds are heated to facilitate better material flow and optimize curing, especially when using thermosets. The heat softens the plastic material, allowing it to fill the mold cavity more easily and reducing production time.
To create your molded parts, you’ll need proper equipment, such as a hydraulic press. These presses exert immense pressure on the heated platens, which then transmit the force evenly to the mold and mold material. The required pressure, or clamp tonnage, varies depending on factors like material type and part size.
Here is a list of basic compression molding machines and equipment components typically used in compression molding:
- Heated platens: To apply heat uniformly to the mold, increasing material flow.
- Hydraulic press: To apply pressure to the mold, ensuring proper material distribution and part quality.
- Mold: Custom-designed cavity to match the shape of your final product.
- Tooling: Precision components, like ejector pins, that facilitate mold use and maintenance.
Materials Used in Compression Molding
In compression molding, a wide range of materials are used to create high-quality products. Knowing the options available can help you choose the most suitable material for your project. Let’s look at some materials commonly used in compression molding:
Thermosets and Thermoplastics are two primary types of materials used in compression molding. Thermosets include epoxy, phenolic, melamine, urea, and urethane resins, whereas thermoplastics encompass HDPE, PEEK, and polyphenylene sulfide (PPS).
Elastomers, such as natural rubbers, are also useful for compression molding, providing flexibility and resilience in the final products. These materials can be used across a wide range of industries and applications.
Some popular composite materials used in compression molding include:
- Bulk Molding Compound (BMC): A mixture of resin, pigments, and fillers that offers excellent electrical and thermal insulation.
- Sheet Molding Compound (SMC): Composed of resin, fiber reinforcement, and fillers, SMC provides high strength and lightweight properties.
- Polyester: This material offers good mechanical properties and chemical resistance and is available in various forms, including unsaturated polyester resin (UPR) and vinyl ester resin (VER).
In addition to these options, you can also use materials like aluminum for creating laminate structures, which combine the benefits of metal and composite materials.
Products of Compression Molding
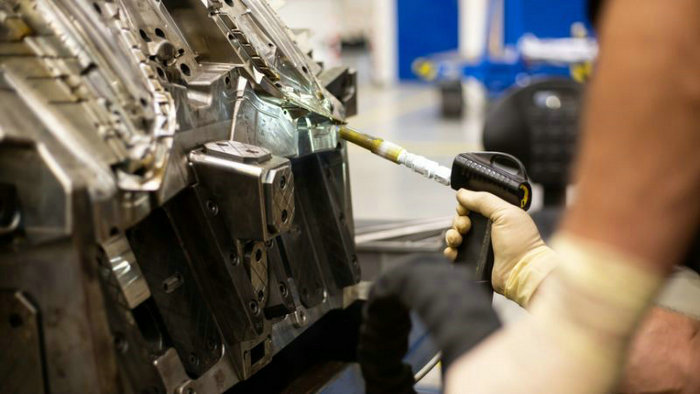
Compression molding is a versatile manufacturing process that creates a wide array of products – from large automotive components to small, intricate parts for various industries. Let’s dive into some of the most common applications and the different types of parts you can create using this method.
In the automotive industry, compression molding is often employed for manufacturing various composite parts and plastic components. These can include bumpers, engine covers, and even structural components, offering benefits like weight reduction, cost efficiency, and design flexibility. One notable benefit is the ability to create large, complex parts in a single process, minimizing the need for additional assembly steps.
The aviation industry similarly utilizes this process to create composite parts for airplanes. Many of these parts require high strength, temperature resistance, and dimensional precision – qualities that compression molding can achieve effectively.
As for kitchenware, compression molding works well in producing essential items such as bowls, plates, and utensils. These products need to be temperature resistant and durable, qualities that can easily be attained through this method. Here’s a quick list of products often created through compression molding:
- Automotive parts: bumpers, engine covers, structural components
- Aviation parts: aircraft interior components, structural elements
- Kitchenware: bowls, plates, utensils
Moving on to other applications, compression molding can be used to create a range of consumer products, from toys to bottles and even household items. The process works well for both large and small-scale production, making it an ideal choice for businesses of various sizes.
Advantages and Disadvantages of Compression Molding
When considering compression molding for your manufacturing needs, it’s important to weigh the advantages and disadvantages of the process.
On the advantages side, compression molding offers:
- Low material waste: Since the process uses pre-measured material charges, there is minimal waste generated during production.
- Low post-processing: Parts created through compression molding often require little or no finishing, which saves time and effort.
- High-volume production: Compression molding is a suitable method for high-volume production because it uses molds that can withstand multiple cycles.
- Quality and strength: The process typically results in parts with good strength and dimensional stability due to the controlled molding pressures.
However, compression molding has its share of disadvantages:
- Higher labor costs: The technique requires more manpower compared to semi-automated processes like injection molding, which, in turn, could increase labor costs.
- Limited material options: Only certain thermosetting plastics can be used with this process, which may limit your choice of materials.
- Post-molding costs: There is a possibility of extra costs being incurred after the molding process due to product finishing or trimming requirements.
- Complexity limitations: Compression molding is not suitable for producing parts with intricate or complicated designs and may result in issues like flash.
Further Analysis
When you’re working with compression molding, there are several factors to consider for optimal production. One critical aspect is choosing the right molding material; popular choices include sheet molding compound (SMC) and bulk molding compound (BMC). These materials typically consist of glass fibers, thermosetting resins, and various additives.
In the process, raw material, often in the form of sheets, pellets, or preforms, is placed in a metal mold. The mold is then heated, and tonnage press applies a precise amount of pressure, melting the material and filling the cavity. It’s essential to design the mold accurately to achieve the desired dimensions and features, such as ribs and undercuts.
Here are some factors to consider in the compression molding process:
- Mold Design: Ensuring proper mold design is critical for high-volume production. The mold must accommodate automated operations and complex geometries, like insert molding and transfer molding.
- Material Handling: Choosing the right method for handling your molding material can significantly affect the process. Typically, sheets with an SMC matrix are easier to handle and automate compared to BMC pellets.
- Flash Control: Flash refers to the excess material that may occur during molding. Proper mold design and tonnage can help reduce flash and minimize the need for post-molding machining.
- Ejector System: An effectively designed ejector system will facilitate the smooth removal of the final product from the mold.
Frequently Asked Questions
What materials are commonly used in compression molding?
In compression molding, thermosetting resins are predominantly used. Some common thermoset materials include phenolics, epoxy, melamine, urea-formaldehyde, and silicone. However, some thermoplastics, such as polyethylene and polypropylene, can also be molded using this process.
How does compression molding work with thermoplastics?
When it comes to thermoplastics, compression molding involves placing preheated material into a heated mold cavity. The mold is closed, and pressure is applied to force the material to take the desired shape. As heat and pressure are maintained, the thermoplastic softens and conforms to the mold cavity, and once it cools down, it hardens, retaining the final shape.
What are the main applications of compression molding?
Compression molding serves various industries and applications. It’s commonly used to produce large, thick, or complex parts like seals, gaskets, automotive parts, electronics housing, and kitchen utensils. The process is also suitable for smaller parts and can be utilized in the manufacturing of electrical components and aerospace parts.
How is compression molding applied to composites?
In the case of composite materials, a combination of fibers (such as carbon or glass) and thermosetting resins are used. Preheated composite material, often in the form of a sheet or pre-preg, is placed into a mold cavity. Under high pressure and temperature, the composite material conforms to the mold, and the resin cures, resulting in a strong, lightweight part with the desired shape.
What are the differences between compression molding and injection molding?
Compression molding and injection molding are two distinct processes with unique advantages and drawbacks. Injection molding involves injecting molten material into a mold under high pressure. It’s typically faster and more precise than compression molding, making it ideal for high-volume production. However, it often comes with higher tooling costs.
On the other hand, compression molding uses preheated material that’s compressed in a heated mold cavity. It’s generally more cost-effective, especially for large, thick, or complex parts. However, cycle times might be longer, and more material waste can occur in comparison to injection molding.
What challenges can be encountered in the compression molding process?
There are several challenges you might face with compression molding. These can include uneven material distribution, void formation, and inadequate curing. To overcome these challenges, it’s crucial to optimize process parameters like mold design, temperature, pressure, and cycle time. Additionally, selecting the right materials and ensuring proper preheating can help reduce issues and improve the overall quality of your molded parts.