Injection molding is a widely used manufacturing process for producing plastic parts by injecting molten material into a mold. The process relies on a critical component called the gate, which controls the flow of molten plastic into the mold cavity. Having the right gate design is essential for the success of your injection molded parts as it affects their cosmetics, cycle times, and various features.
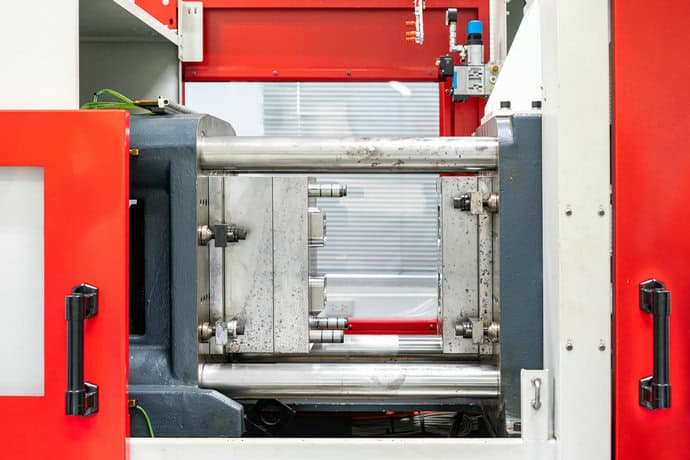
In gate injection molding, the molten plastic flows through a specifically designed opening, often small, before entering the mold cavity. This gateway acts as a pathway for the molten material from the nozzle to the tool’s core. The injection gate design must suit the specific project to avoid potential defects and ensure a high-quality final product.
Key Takeaways
- Injection molding gates control the flow of molten plastic into the mold cavity, contributing to the success of the molded parts.
- The right gate design ensures high-quality final products and minimizes potential defects.
- Gate injection molding impacts various aspects of a part, including cosmetics, cycle times, and specific features.
Basics of Injection Molding
Injection molding is a widely used manufacturing process in which a material, typically plastic or resin, is melted and injected into a mold cavity under high pressure. The material cools and solidifies within the mold, taking on the shape of the cavity. Once the part has cooled sufficiently, it is ejected from the mold, and the process is repeated for the next part.
Various types of gates are used, such as side gates, disc or diaphragm gates, ring gates, and spoke gates. Choosing the right gate type depends on the part’s geometry, application, and required concentricity.
Materials play a significant role in the injection molding process. Common materials used in this process include thermoplastic polymers, thermosetting polymers, elastomers, and even metals in some cases. The choice of material depends on factors such as part design, intended use, and material properties such as strength, flexibility, and resistance to chemicals or heat.
The quality of the molded part is influenced by several factors, including the design of the mold, the quality of the material used, and the process parameters. Careful consideration of these factors can help ensure a successful outcome, with parts meeting desired characteristics such as dimensional accuracy, surface finish, and mechanical properties.
Injection molding can be adapted to suit various manufacturing requirements using different processes, such as co-injection molding, fusible core injection molding, gas-assisted injection molding, and injection-compression molding. Each process has advantages and limitations, and the choice depends on factors such as part complexity, material requirements, and production volumes.
In summary, injection molding is a versatile and efficient manufacturing process for producing parts from various materials, using different gate types and processes suited to specific applications. By understanding the basics of injection molding, you’ll be better equipped to make informed decisions when designing and manufacturing parts with this process.
Structural Components of Injection Molding
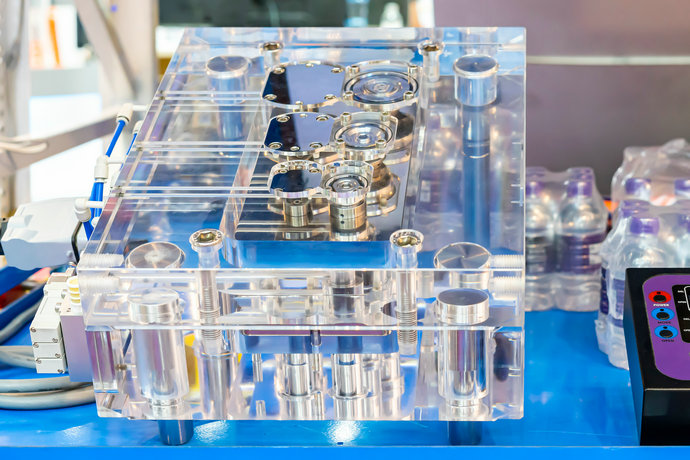
When it comes to injection molding, it’s crucial to understand its fundamental components clearly. This section will explore the main structural elements, including the mold, cavity, sprue, runner, and mold cavity.
The mold is critical in the injection molding process, as it shapes the plastic material into its desired form. Molds can have single or multiple cavities, depending on the complexity and size of the final product.
The cavity is the space within the mold where the molten plastic material is injected. This is where the plastic material takes on the shape of the final product. The number of cavities in a mold affects the production rate and the overall cost.
The sprue is the passage that connects the injection molding machine’s nozzle to the runner system. It’s responsible for transporting the molten plastic into the mold. It is essential to have a well-designed sprue to ensure proper flow and minimize the risk of material defects.
Runners are channels in the mold that guide the molten plastic to the mold cavities. They play a crucial role in the even distribution of material and maintaining consistent pressure throughout the molding process. The runner system can be designed as either a hot or cold runner, each with advantages and disadvantages.
The mold cavity is where the plastic material solidifies and forms the final product. It is vital to design the mold cavity considering the final product’s desired dimensions, tolerances, and surface finishes. This directly affects the product’s quality and performance.
By gaining a solid understanding of these structural components, you can ensure that your injection molding process is efficient accurate, and results in high-quality products.
Understanding the Gate
In injection molding, gates are crucial components that ensure the proper flow of molten plastic into the mold cavity. These gates, specifically designed openings, control the flow, appearance, and cooling of injection-molded parts. Choosing the correct injection molding gate is imperative for maintaining your final product’s quality, precision, and performance.
Several types of gates to consider for your injection molding project, each with specific benefits and applications. Understanding these different gate types is essential to selecting the most suitable option.
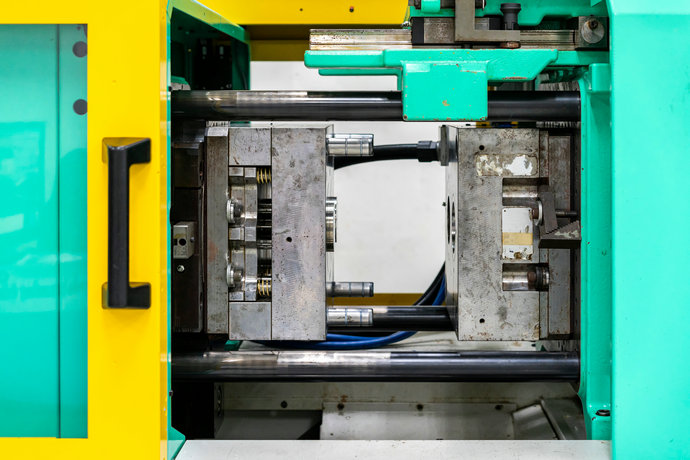
- Sprue gate: This is the simplest type of gate, which connects the molded part directly to the nozzle of the injection machine. While it’s easy to design and use, it can result in high stress and could be better for complex or large parts due to material waste.
- Submarine gate (also known as tunnel gate): This gate type is designed to shear off the molded part during ejection automatically. They are advantageous for automation and require minimal post-molding work, making them ideal for high-volume production.
- Fan gate: Named for its fan-like shape, this gate allows for a more even distribution of molten material, reducing the probability of part defects.
- Edge gate: Placed on the edge of the molded part, this gate ensures better flow inside the mold cavity and is ideal for flat and thin parts.
- Tab gate: Similar to an edge gate, this type reduces the chance of material leakage and is often used for flat, thin parts that need a more focused flow.
- Diaphragm gate (cashew gate): This gate controls the material flow from the center of a molded part, allowing for better control over part shrinkage and warping. It is commonly used for precision parts with complex geometries.
- Ring gate: Used in molding tube-shaped parts, ring gates control material flow around the entire circumference of the part, providing an even distribution.
In addition to these primary gate types, there are sub-gates (smaller gates used in conjunction with a primary gate), valve gates, which help control flow through more precise means, and hot tip gates, which utilize a heated nozzle for specialized, high-precision applications.
A well-selected gate system and design can distinguish between a successful injection molding project and one plagued by part defects, material waste, and inefficiencies. Understanding these gate types and their potential impact on your injection-molded parts will enable you to make informed decisions and achieve optimal results.
Factors Influencing Gate Performance
When working with gate injection molding, it’s essential to consider several factors that can influence the gate’s performance. By paying attention to these factors, you can ensure the quality of your molded components and optimize the effectiveness of your process.
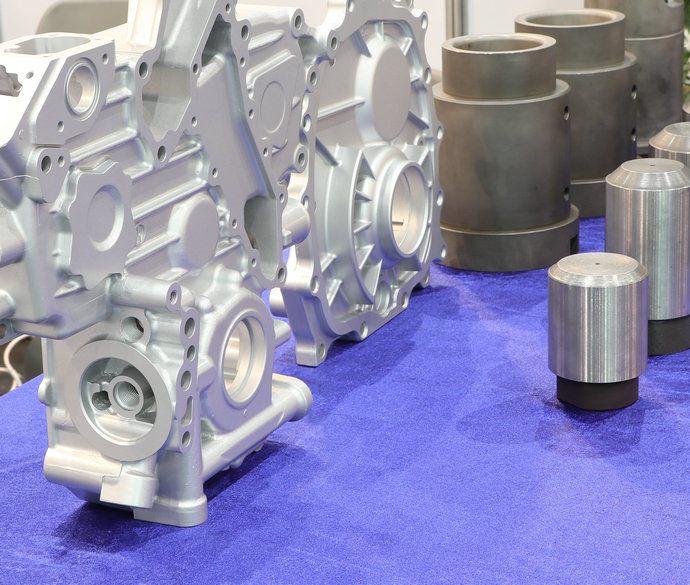
Pressure and Temperature Control: Proper control of the injection pressure and temperature is critical, as these parameters affect the flow of the plastic into the mold. Finding the right balance between these two factors is essential to achieve consistent filling and avoid defects such as warping or sink marks.
Thickness and Filling: The thickness of the gate plays a crucial role in how quickly and evenly the plastic fills the mold cavity. A thicker gate can result in faster filling but may increase shear stress and potential damage to the plastic part. On the other hand, a thinner gate may lead to slower filling and possible short shots.
Taper and Gate Location: The design of the gate can also impact the flow of plastic. A tapered gate allows for a smoother flow, which can help prevent weak spots or fractures in the final part. Additionally, choosing the right gate location is essential for minimizing defects such as injection molding flash or uneven thickness.
Gate Placement: Correct gate placement is vital to ensure good flow and proper filling of the mold cavity. Placing the gate in a location that allows the plastic to flow around the mold’s features can help avoid defects and create a more uniform part.
Fast-Flowing Resins: Using fast-flowing resins can improve the efficiency of the injection molding process by reducing the cycle time. However, working with fast-flowing resins may require more precise control of pressure, temperature, and other process parameters to achieve the desired results while avoiding defects.
By considering these factors, you can optimize the performance of your gate injection molding process and achieve high-quality molded components. Finding the right balance between pressure, temperature, gate thickness, and location is essential for success in this specialized manufacturing area.
Gate Defects and Quality Control
In injection molding, gate defects can significantly impact the quality of your finished part. Understanding various gate-related issues and implementing the appropriate quality control measures are crucial for obtaining a high-quality final product.
One common gate defect is the presence of vestiges. Vestiges are remnants of the gate left on the finished part after trimming, which can be unsightly and negatively affect your final appearance. To minimize vestiges, ensure your gate is trimmed cleanly and with precision. Choosing the right gate type, such as a hot tip or submarine gate, can also help reduce vestige appearance.
Jetting is another injection molding defect sometimes associated with gate design. Jetting occurs when molten material shoots into the mold at high velocities, causing it to solidify prematurely and leading to blemishes or weak spots in your finished part. Adjust the injection velocity or modify the flow channels within your gate design to address jetting issues.
Cycle times play a crucial role in controlling the quality of injection-molded parts. Longer cycle times can lead to increased stress fractures, while shorter cycles may result in incomplete filling, creating blemishes and adversely affecting part quality. Balancing your cycle times can help ensure your parts meet the desired quality standards.
Meticulous inspection and monitoring of your injection molding process can aid in identifying gate-related defects early on, allowing you to address them promptly and maintain optimal part quality.
Also, implementing various quality control methods, such as visual inspections, automated inspection systems, and destructive or non-destructive tests, will provide valuable insights into the efficacy of your gate design and molding process.
Frequently Asked Questions
1. What are the different types of gates in injection molding?
Several types of gates are used in injection molding, such as direct or sprue gates, edge gates, submarine gates, and fan gates. Each type has unique advantages and applications, depending on the component’s design and requirements.
2. How does gate design impact the molding process?
The gate design plays a crucial role in molding by determining molten plastic flow into the mold cavity. A well-designed gate ensures efficient filling, minimizes molding defects, and reduces cycle time. Different gate types have varying benefits, such as promoting a faster flow, controlling sink marks, or allowing for better venting.
3. What factors determine gate placement in injection molding?
Several factors impact gate placement in injection molding, including part geometry, material selection, and desired flow path. Generally, the gate should be placed in an area that allows uniform filling and minimal material pressure, reducing defects and warping. The gate location should also minimize stress on critical areas and ensure any weld lines are in non-critical sections.
4. What are the main functions of gates in injection molding?
Gates serve multiple functions in injection molding, such as controlling the flow of molten plastic to the mold cavity, ensuring proper filling, and allowing the plastic to solidify at an optimal pace. Gates are also responsible for minimizing molding defects, such as air traps, sink marks, and short shots, by directing the plastic melt efficiently.
5. How does gate size influence the final product?
Gate size can significantly impact the final product’s quality and appearance. A smaller gate typically results in a slower flow rate, reducing the risk of sink marks and warping. However, it may also increase cycle time and lead to incomplete filling in specific scenarios. On the other hand, a larger gate allows for faster flow and quicker mold filling but may cause additional stress or defects within the part.
6. What are the advantages of using gate injection molding?
Gate injection molding offers several benefits, such as increased control over the flow of molten plastic, reduced cycle times, and minimized defects. Choosing the appropriate gate design and placement allows you to optimize your molding process to produce high-quality components with fewer issues. Additionally, proper gating can help reduce material waste and improve overall production efficiency.
Order High Quality Plastic Injection Parts from Us
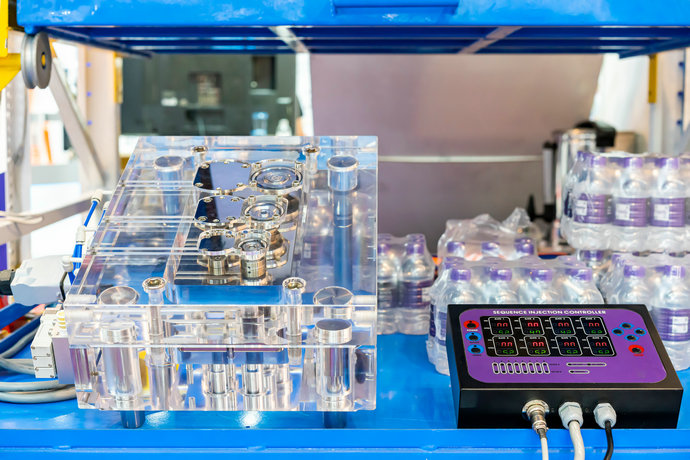
We sell different types of injection molding plastic parts in bulk. To order, you only need to send us a message via the customer contact form on our website. We deliver plastic injection molding products globally and look forward to starting a rewarding business relationship with your company.