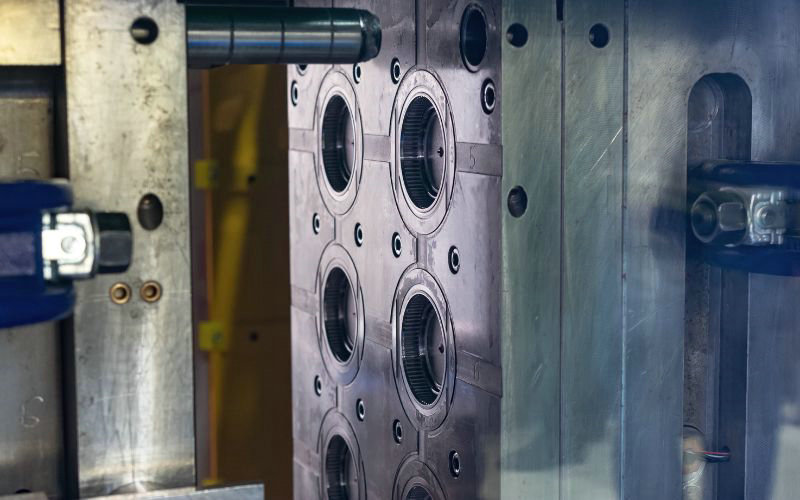
Main Types of Injection Molding Technologies
Injection molding is one of the most widely used manufacturing processes for producing high-quality plastic parts in large volumes. Its versatility, efficiency, and ability to create complex geometries make it an essential technology across various industries, from automotive and medical to consumer goods and electronics.
However, not all injection molding processes are the same. Over the years, several specialized injection molding technologies have emerged to cater to specific application requirements, such as improved strength, reduced weight, or enhanced surface finish. Understanding the advantages and disadvantages of each type of injection molding is crucial for selecting the most suitable process for your project.
In this blog post, we will explore six main types of injection molding technologies: gas-assisted injection molding, thin wall molding, liquid silicone injection molding, metal injection molding, 3D printing, and structural foam molding. We will delve into the benefits and applications of each process, helping you make an informed decision when choosing the right injection molding technique for your product.
So, whether you’re a product designer, engineer, or manufacturer, join us as we uncover the world of advanced injection molding technologies and discover how they can revolutionize your product development process.
Gas-Assisted Injection Molding
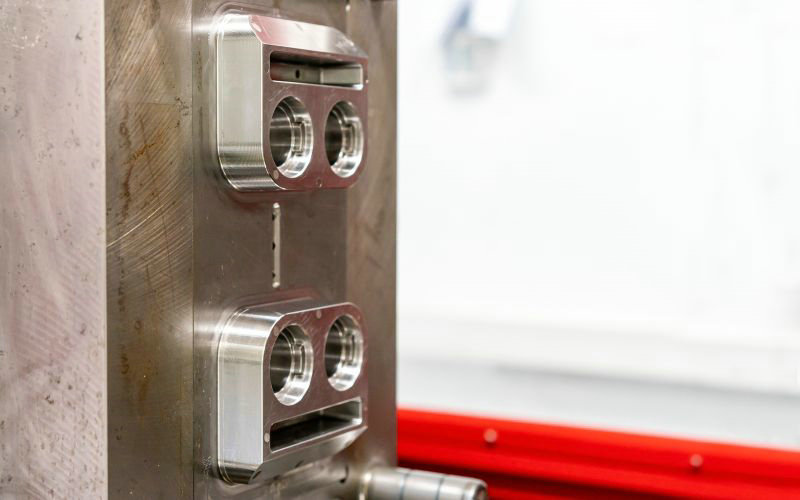
In Gas-Assisted Injection Molding (GAIM), your plastic parts benefit from reduced material stress and improved surface finishes. This process merges traditional injection molding with pressurized gas assistance.
Benefits
- Material Efficiency: You save on material costs as GAIM uses less plastic while still maintaining strength.
- Reduced Warping: Your parts have minimal warping due to more uniform internal pressures during molding.
- Enhanced Design: You can achieve complex geometries and intricate designs that might not be possible with conventional injection molding.
- Faster Cycle Times: Enjoy quicker production runs thanks to reduced cooling times because the parts have less plastic.
Applications
- Automotive Components: Your vehicle’s dashboards and bumpers are ideal candidates for GAIM to balance durability and lightweight design.
- Consumer Goods: Toys and home appliances benefit from the aesthetic and functional qualities that GAIM provides.
- Medical Devices: The process is suitable for making lightweight, strong parts for various medical equipment.
- Furniture: The technology is also used in producing sturdy, yet lightweight, furniture components that require a good surface finish.
Thin Wall Molding
Thin wall molding is a highly specialized form of injection molding that focuses on producing parts with exceptionally thin dimensions. This process demands precise control and rapid injection speeds.
Benefits
- Efficiency: You can achieve faster cooling and cycle times, offering increased production efficiency.
- Material Savings: Reduces material usage which lowers costs and decreases environmental impact.
- High Performance: Parts produced are lightweight yet retain high strength, suitable for demanding applications.
Applications
- Electronics: Ideal for producing thin, lightweight parts like mobile phone casings.
- Packaging: Enables the creation of durable containers with minimal material use, often seen in food packaging.
- Medical Devices: Delivers precision components capable of withstanding stringent medical industry standards.
Liquid Silicone Injection Molding
Liquid silicone injection molding is a process used to create pliable, durable parts with high precision. This method involves high-consistency rubber that can achieve tight tolerances and intricate designs.
Benefits
- Consistency and Quality: The liquid silicone injection molding process offers remarkable consistency in the products manufactured. This is due to the material’s ability to maintain stable mechanical properties throughout its lifespan.
- Versatility: Parts produced using liquid silicone can withstand extreme temperatures, making them suitable for various applications.
Applications
- Medical Devices: You’ll find components made with liquid silicone injection molding in medical applications due to their biocompatibility and sterilizability.
- Automotive Parts: Due to its durability and heat resistance, liquid silicone is also commonly used for gaskets, valves, and seals in the automotive industry.
Metal Injection Molding
Metal Injection Molding (MIM) is a sophisticated process that merges the versatility of plastic injection molding with the strength and integrity of wrought metals. Suitable for the mass production of small, intricate parts, MIM achieves a level of precision that traditional metalworking techniques struggle to meet.
Benefits
MIM allows you to leverage several benefits:
- Precision: Create complex and highly detailed parts that are challenging to produce via other methods.
- Strength: MIM parts are comparable in strength and density to those made with traditional metalworking processes.
- Cost-Effectiveness: Especially for medium to high-volume productions, you can achieve substantial savings due to reduced waste and minimal finishing requirements.
Applications
Your industry may already be harnessing MIM:
- Medical: Surgical instruments, orthodontic appliances, and implantables
- Automotive: Engine components, gearboxes, and sensor housings
- Consumer Electronics: Mobile phone components and computer hardware
3D Printing
In the realm of injection molding, 3D printing has emerged as a transformative approach, enabling rapid prototyping and production of molds with complex geometries that traditional methods struggle with.
Benefits
- Cost-Efficiency: You’ll find significant cost savings due to the minimal waste of material and the elimination of the need for multiple machining processes. Learn about cost efficiency in 3D printing.
- Speed: Prototypes and molds can be produced much faster than traditional methods, often within hours or days, reducing the overall time to market.
Applications
- Prototyping: 3D printing excels in creating detailed prototypes swiftly to test form, fit, and function.
- Production: Although less common, it is possible to produce final production-quality parts, especially for short runs where constructing a traditional mold may not be cost-effective. It is also used for making intricate mold designs that are difficult to achieve with CNC milling.
Structural Foam Molding
When you explore structural foam molding, you are looking into a distinct process that creates parts with a cellular core. This is achieved by integrating a physical or chemical blowing agent within the plastic material. As a result, products manufactured through this method tend to be more robust and lighter in weight.
Benefits
- Enhanced Strength to Weight Ratio: The unique cellular core characteristic of structural foam molded parts provides superior strength to weight ratios. This makes such parts ideal for applications requiring robust performance without the heaviness of solid plastics.
- Reduced Material Use: With structural foam molding, you can achieve the same overall part dimensions while using less material, thanks to the foaming action, which creates a cellular structure within the component and reduces the density.
- Design Flexibility: This type of molding allows for complex geometries and designs that might be challenging or impossible to create with traditional injection molding. By using structural foam molding, designers have greater latitude in draft angles and wall thicknesses.
- High-Dimensional Stability: Because of the low-pressure environment in which the molding process operates, there’s less stress on the parts, leading to higher dimensional stability and superior part quality.
Applications
- Aerospace: Structural foam is used for airframe and aircraft interior components, satellite parts, and large aviation enclosures due to its high strength-to-weight ratio.
- Transportation: The process is ideal for producing large, lightweight parts like commercial vehicle components, ATV bumpers, and autonomous robot structures.
- Industrial equipment: Structural foam is used for trash and recycling carts, agricultural equipment housings, reusable pallets, commercial floor washer covers, and ATM enclosures because of its durability and impact resistance.
- Medical devices: The technology is employed for mobile cart trays, bases, skins, handles, MRI and X-ray equipment panels and doors, diagnostic laboratory equipment enclosures, and surgical arms due to its strength and moldability.
- Consumer products: Structural foam molding creates large, rigid parts for recreational vehicles, outdoor consumer products like grill trays and wheelbarrows, and speaker enclosures.
- Construction: Large panels, carts, and other construction components benefit from structural foam’s ability to produce sizable, lightweight parts.
Advanced Techniques and Future Trends
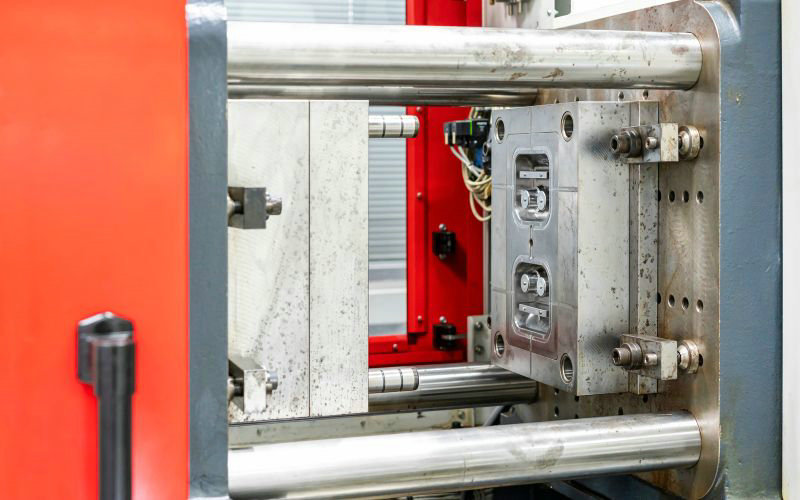
As you navigate the rapidly evolving world of injection molding, you’ll find that conventional injection molding has paved the way for more innovative techniques. One such advancement is insert molding, where components such as metal parts are encapsulated within the plastic during molding, offering enhanced strength and function for your products.
Incorporating 3D printing into injection molding has revolutionized prototype development, allowing for detailed and flexible design before mass production. This can significantly reduce cost considerations as it enables you to perfect designs without expensive tooling for short runs.
Embrace automation to boost efficiency and maintain a high level of precision. Automated systems manage tasks from handling raw materials to operating the molding machinery, which can positively impact production volume and consistency.
Here’s a snapshot of current trends:
- 3D Printing: Rapid prototyping and complex geometries
- Automation: Consistency and speed in production
- Cost Considerations: Reduced waste, optimized resource use
For effective temperature management during molding, designers are innovating with cooling channels that allow the molded parts to cool more quickly and evenly. This speeds up production and improves the crystallinity of materials like polystyrene (PS).
Clamping force plays a critical role in mold closure and part quality. Modern machines offer greater control, optimizing this force based on the specific mold and material—further enhancing the capabilities of post-processing methods to refine and finish your products.
In the dynamic field of injection molding, these emerging trends promise to refine your production process and elevate the quality of your outputs. Embrace them to stay at the forefront of the industry.