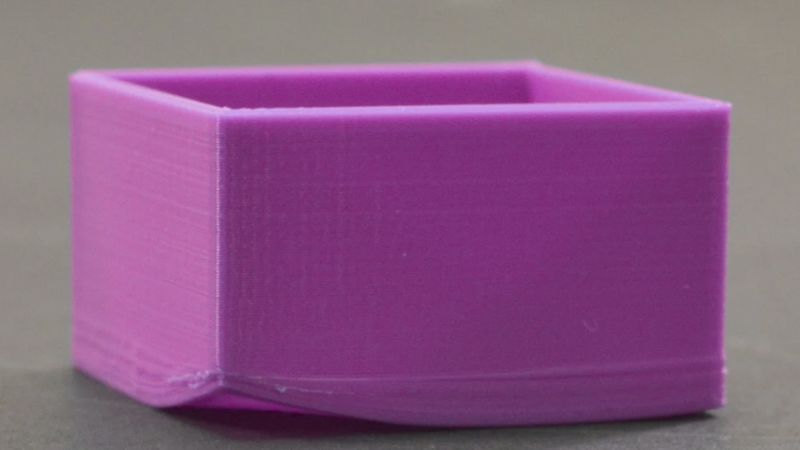
Warpage can be annoying. For manufacturers and product designers alike, it is important to understand the root causes of warpage and implementing effective prevention strategies is crucial for maintaining high-quality output and minimizing production costs.
In this comprehensive guide, we’ll explore the primary factors contributing to warpage in injection molding and provide practical solutions to mitigate this issue.
By applying these insights, manufacturers can improve their production efficiency, reduce scrap rates, and ultimately deliver superior injection-molded parts.
What is Molding Warpage
Warpage is one of the crucial quality issues in plastic injection molding, often leading to dimensional instability in plastic parts.
Warpage refers to the undesirable deviation from the intended product geometry that can occur in plastic parts during the injection molding process. This defect manifests as distortions such as twisting, bending, or curling of the molded part.
The severity of warpage ranges from slight deformations, barely noticeable to the naked eye, to significant distortions that interfere with the part’s function or assembly.
The Impact of Warpage on Molded Products
The presence of warpage in injection molding has substantial implications on the quality and functionality of plastic parts:
- Aesthetic Quality: Visual appeal is compromised, making final products less competitive in the market.
- Dimensional Stability: Warped parts may not fit into assemblies or meet the precise dimensions required for interfacing with other components.
- Functional Deficiencies: Beyond aesthetics, warpage can impair the mechanical performance and structural integrity of the component.
What is the Cause of Warpage in injection molding?
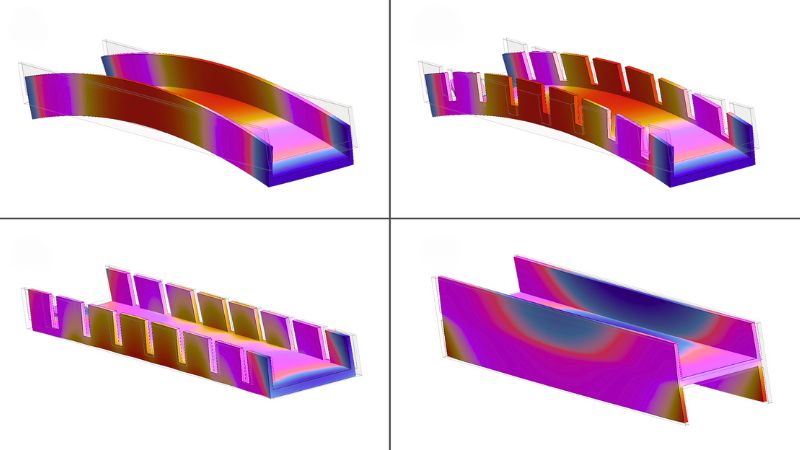
This section explores the intricacies of machine, mold, and material factors contributing to warpage and provides some practical solutions to mitigate these issues.
Machine Errors
Inadequate Injection Pressure or Time
Insufficient injection pressure or hold time can lead to inadequate packing of the mold. This can cause the plastic material to cool and solidify before the mold is properly filled.
Both scenarios result in uncontrolled movement of molecules during cooling, leading to uneven shrinkage and warpage.
Incorrect Barrel Temperature
If the barrel temperature is too low, the resin won’t reach its proper flow temperature, leading to premature solidification, inadequate mold packing, and ultimately, uneven shrinkage and warpage.
Improper Residence Time
Inadequate residence time prevents uniform heat absorption throughout the resin. This can cause under-heated portions of the material to become stiff and solidify prematurely, resulting in incomplete mold packing and warpage.
Excessive Internal Strain
High injection pressures can create internal stresses within the molded part, which can manifest as warpage after ejection from the mold.
Incorrect Screw Forward Time
If the screw forward time is too long, it can lead to over-packing of the mold, creating internal stresses that result in warpage.
Insufficient Cooling Time
Insufficient cooling time can prevent the part from cooling uniformly and completely before ejection, leading to uneven shrinkage and warpage as it continues to cool outside the mold.
Mold Errors
Improper Gate Location and Design
Incorrect gate placement can lead to uneven filling and packing of the mold cavity. This results in inconsistent pressure distribution and cooling rates, causing warpage.
Inadequate Ejector Pin Placement
Poorly positioned or insufficient ejector pins can cause uneven stress when the part is ejected from the mold. This can lead to warpage, especially in parts with complex geometries.
Unbalanced Cooling Circuits
Improperly balanced cooling circuits can cause uneven cooling across cavities, leading to warpage in some parts while others remain unaffected.
Material Selection Errors
High Shrinkage Rates
Materials with high shrinkage rates are more prone to warpage.
For example, semi-crystalline polymers like polyethylene (PE) and polypropylene (PP) have higher shrinkage rates compared to amorphous polymers like polycarbonate (PC) or polystyrene (PS).
Inconsistent Shrinkage
Some materials shrink differently in the flow direction versus the cross-flow direction. This anisotropic shrinkage can lead to warpage, especially in parts with long flow paths.
Crystallinity
Highly crystalline materials are more susceptible to warpage due to their tendency to shrink more during cooling.
Moisture Sensitivity
Some materials, like nylon, are hygroscopic and can absorb moisture from the air. This can lead to inconsistent molding results and potential warpage if not properly dried before processing.
How to Reduce Warpage in Injection Molding?
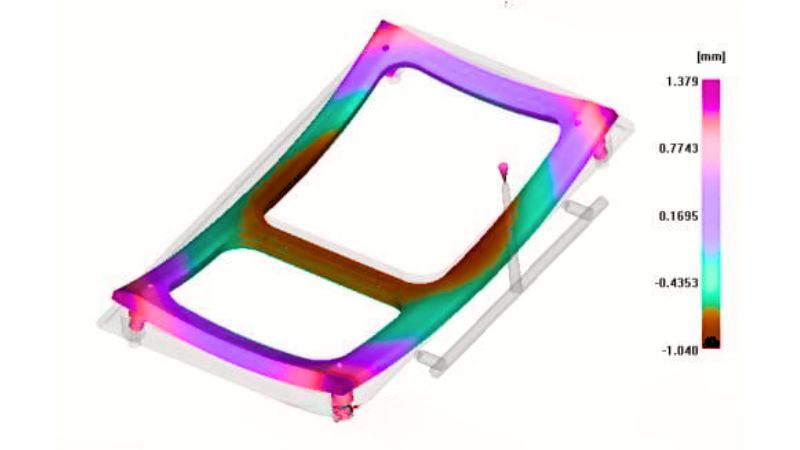
Optimizing processing parameters is crucial, starting with adjusting injection pressure and hold time to ensure proper packing of the mold cavity. This constrains plastic molecules and prevents uncontrolled movement during cooling.
Increasing cooling time allows for complete and even cooling, helping to prevent differential shrinkage rates that often lead to warpage.
Fine-tuning temperature settings is equally important; raising barrel temperature ensures proper material flow while adjusting mold temperature based on resin supplier recommendations promotes uniformity.
Where possible, implementing conformal cooling channels can further enhance even cooling across the part.
Mold Design and Material Considerations
Optimizing gates and runners by using appropriate gate types for specific plastics and product designs, implementing multiple gates for flat parts, and widening gates and runners can significantly improve mold filling.
Proper ejector pin placement is also crucial; ensuring they are wide enough, well-distributed, and located close to areas with the most ejection resistance can prevent warpage during part removal.
Material selection and handling are key factors. Choosing resins less prone to warpage, such as amorphous plastics like polycarbonate and polystyrene instead of crystalline plastics, can make a substantial difference.
For parts using metal inserts, preheating them to around 100°C helps accommodate shrinkage differences between metal and plastic, reducing stress and potential warpage.
Design Optimization and Quality Control
Part design optimization is another critical aspect. Maintaining uniform wall thickness throughout the part promotes even cooling and shrinkage while adding strengthening ribs can improve part rigidity and reduce warpage tendency.
Cooperate with Professional — Moldie
Working with Moldie can lead to quality and efficiency within the molded plastic injection process. We are equipped with the expertise required to handle a diverse array of plastic materials, ensuring that the resulting plastic products marry durability with aesthetics.
Moldie emphasizes precision in its manufacturing techniques. Our approach involves:
- Advanced Mold Design: By optimizing gate size and shape, Moldie helps maintain uniform flow and cooling, resulting in less internal stress and reduced warpage.
- Material Selection: Their knowledge of various plastics allows for an informed choice of material, tailoring the properties to the intended application and mitigating defects.
- Process Optimization: Moldie fine-tunes the mold temperature and cooling rates, as these variables play a pivotal role in the production of high-quality, warp-free components.
We believe such collaboration can significantly elevate the standard of the plastic components produced, ultimately enhancing the end product’s functionality and appearance.