Proper rib design is essential for achieving optimal part strength while maintaining manufacturability and cost-effectiveness. When strategically implemented, ribs can prevent warpage, support isolated features, reduce material consumption, and improve mold flow. However, designing effective ribs requires a thorough understanding of material properties, molding processes, and design principles.
This article delves into the fundamentals of injection molding rib design, exploring key considerations such as rib geometry, material selection, and design guidelines. By mastering these essentials, engineers, and designers can create parts that not only meet strength requirements but also optimize production efficiency and product quality.
What Is Rib?
Ribs are an important design feature in plastic injection molding that increases the strength and support of parts without increasing overall wall thickness.
Ribs are thin, wall-like structures that extend perpendicular to a wall or plane in injection molded parts, which serve to add support and rigidity to the part, increase strength without increasing wall thickness, and replace thick wall sections to avoid defects like sink marks, warpages, and voids.
What is the Purpose of Ribs in Mold Design?
Ribs in injection molding serve several critical purposes in the design of plastic parts:
- Prevent Warpage: Ribs help prevent warpage by reinforcing thin walls. Thick walls can lead to uneven cooling, causing internal stresses that result in warping. By using ribs, parts can have thinner walls that cool more evenly, reducing the risk of warpage.
- Support Other Features: Ribs provide structural support to isolated features, such as bosses, which are used as fastening points. These features require additional support to maintain structural integrity, and ribs connect them to the side walls or provide reinforcement when they are too far from the side walls.
- Reduce Material Use: Strategically placed ribs can increase stiffness in critical areas without increasing the overall thickness of the part. This allows for a lightweight design that uses less material while still meeting strength requirements.
- Improve Mold Flow: Properly designed ribs can enhance the flow of molten plastic into the mold, ensuring better filling and reducing the likelihood of defects. This dual function of improving mold flow while adding strength makes ribs an essential design feature.
What are the Differences Between Ribs and Gussets?
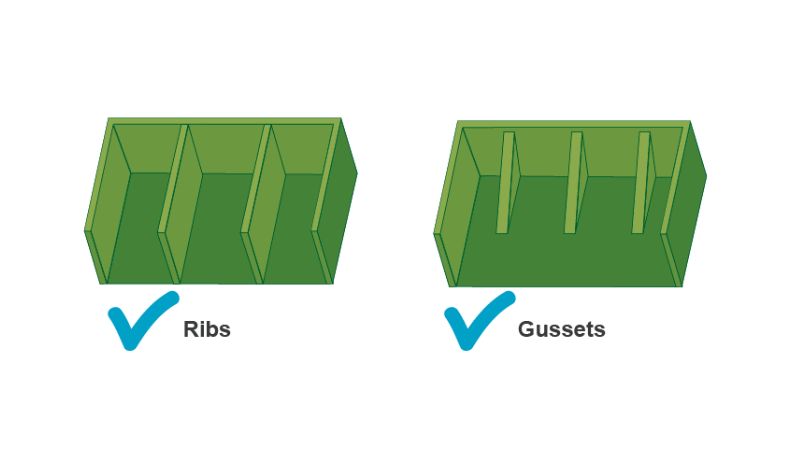
Gussets are like strong pieces of material used to make corners, walls, and connections in structures much stronger. Think of them as special ribs designed to handle stress and spread it out evenly.
Usually shaped like triangles or rectangles, gussets act like strong connectors, holding parts together and making the joints much more stable.
You’ll often find gussets in things like bridges (truss beams) and buildings (lateral bracing systems), where they join diagonal parts and help carry heavy loads. They’re also used in plastic objects to reinforce weak points.
In summary, while both ribs and gussets are used to enhance the structural integrity of a part, ribs primarily add support to flat surfaces. In contrast, gussets focus on reinforcing joints and connections between different components.
What are the Plastic Ribs Design Guidelines?
Rib Thickness
The rib thickness should not exceed 60% of the nominal wall thickness. For glossy materials, it may need to be reduced to 40% to avoid surface defects because thicker ribs can lead to issues such as warping or sink marks, while thinner ribs might not fill properly due to the plastic’s viscosity.
If a rib must vary in thickness, make the transition gradual to minimize stress concentrations and cooling variations, which can cause warpage. Furthermore, the transition distance should be at least three times the change in thickness.
Rib Coring
For unavoidable thick ribs, coring can be used to reduce potential defects.
Rib Height
Limit rib height to three times the rib thickness to prevent underfilling. If necessary, use multiple smaller ribs instead of a single large one.
Rib Spacing
Space multiple ribs at least 2 to 3 times the nominal wall thickness apart. A staggered pattern can help reduce warpage during cooling.
Rib Draft Angle
Apply a draft angle of 0.5 to 1.5 degrees to facilitate easy part ejection. Only crush ribs should be made without a draft angle.
Rib Radii
Include a radius where the rib intersects with the base or sidewall, typically 0.5 to 1 times the wall thickness, to reduce stress concentrations and enhance strength.
The angle of Intersection
Ribs do not always need to intersect side walls at 90 degrees. Angled intersections can enhance stiffness without increasing rib thickness. Remember that care must be taken to prevent excessive thickness at intersections, which can cause sink marks on the opposite surface.
What Materials Are Used to Manufacturing Ribs?
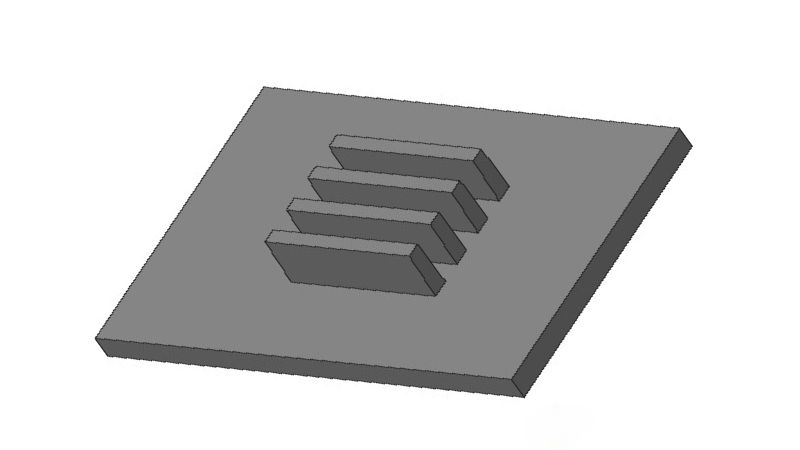
When selecting materials for ribs in injection molded parts, the choice often depends on the specific requirements of the application, such as strength, flexibility, and environmental resistance.
Common materials used for making ribs include:
- ABS (Acrylonitrile Butadiene Styrene):
- Known for its good impact resistance and toughness.
- Suitable for applications requiring strength and rigidity.
- Polycarbonate (PC):
- Offers high impact resistance and clarity.
- Used in applications where transparency and toughness are needed.
- Polypropylene (PP):
- Provides excellent chemical resistance and flexibility.
- Ideal for parts that require fatigue resistance and low moisture absorption.
- Nylon (Polyamide, PA):
- Known for its high strength and wear resistance.
- Suitable for parts exposed to mechanical stress and requiring durability.
- PBT (Polybutylene Terephthalate):
- Offers good chemical resistance and dimensional stability.
- Used in automotive and electrical applications.
- Polystyrene (PS):
- Provides good stiffness and ease of processing.
- Suitable for less demanding applications where cost is a primary concern.
- Polysulfone (PSU):
- Known for its high temperature and chemical resistance.
- Used in applications requiring thermal stability and toughness.
Effective rib design is a crucial aspect of creating strong, efficient, and high-quality injection molded parts. By understanding and applying the principles outlined in this article, engineers and designers can significantly enhance the structural integrity of their plastic components while optimizing material usage and manufacturability.