The heart of Injection molding lies the mold core, a critical component that shapes the internal features of the molded product. Understanding the essentials of injection molding cores is vital for optimizing both product design and quality.
This article delves into the fundamental aspects of mold cores, exploring how they influence the manufacturing process and the final product’s performance. By examining key considerations such as material selection and design strategies, we aim to provide valuable insights for engineers and manufacturers seeking to achieve their best practices in injection molding operations.
First, let’s introduce the basic process of injection molding.
The basic process of injection molding involves several key steps that transform plastic materials into finished products. Here’s a simplified overview:
- Clamping: The process begins by closing the mold, which is typically made of two halves. These halves are clamped together tightly to prepare for injection.
- Injection: Plastic granules or pellets are fed into a heated barrel where they melt. The molten plastic is then injected into the mold cavity through a nozzle, filling the space completely.
- Dwelling: Pressure is applied to ensure the molten plastic fills every part of the mold cavity, ensuring the product matches the mold’s design.
- Cooling: The mold is left to cool, allowing the plastic to solidify into the shape of the mold cavity.
- Mold Opening: Once cooled, the mold halves are opened to reveal the solidified part.
- Ejection: Ejector pins or other mechanisms push the finished part out of the mold, ready for any additional processing or packaging.
What is Injection Molding Core?
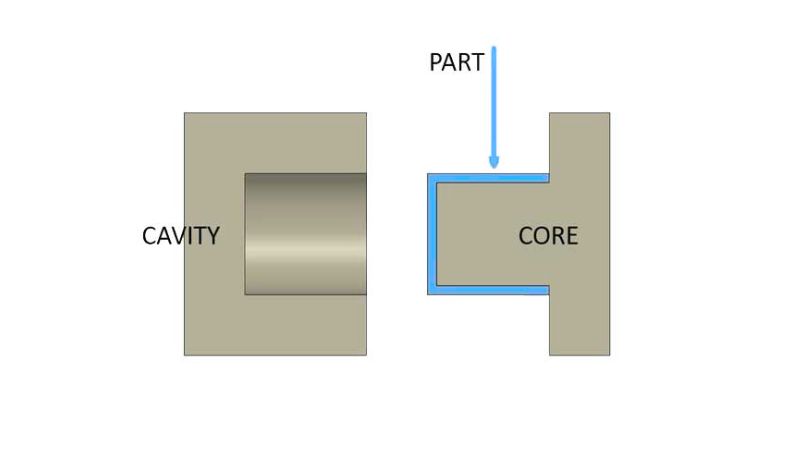
The injection molding core is a solid or movable component within the mold that forms the internal features or voids of the final molded part. It represents the shape and geometry of the desired internal features of the part, such as hollow portions or complex internal structures.
What is the Difference Between Cavity and Core in Mold?
As the core, the cavity is another key mold component in plastic injection molding, which is often polished to a finish that represents the desired final surface finish of the part. They work together to shape the final molded part.
The core shapes the internal features, while the cavity shapes the external features of the part.
The molding core is in the movable half (B-side), which is often involved in the ejection process, and the cavity is in the fixed half (A-side), whereas the cavity is less directly involved.
How to Manufacture the Injection Molding Core?
Choosing the Right Material
Material choice for the core is imperative as it must withstand the high temperatures and pressures of molten plastic without deforming.
The core’s performance directly affects not just the quality but also the efficiency of the injection molding process, leading to parts that meet stringent specifications.
- Steel: High-grade steel is a popular choice for its durability and wear resistance, which makes it ideal for high-volume production. It includes types like stainless steel, P20, and H13.
- Aluminum: Known for its lightweight and quicker heating and cooling properties, aluminum is often used for prototype tools or low-volume production.
- Beryllium-Copper Alloys: Used in areas of the mold requiring rapid heat removal or in parts of the mold with intricate geometries.
- Pre-Hardened Steel: A cost-effective option used in less demanding applications; it doesn’t require additional heat treatment.
- Tool Steel: For high-wear applications, tool steels like D2 or A2 are used, offering robustness and longevity.
Manufacturing Process and Precision
Advanced machining techniques, such as CNC milling and electrical discharge machining (EDM), are instrumental in achieving the high levels of precision required for the cores.
- CNC Milling: Delivers accuracy through computer-controlled machining.
- EDM: Utilized for intricate details and complex geometries.
How Does Mold Core Affect Product Quality?
Core and mold quality variability in injection molding can be attributed to several factors that affect the performance and consistency of the molded parts:
Cause | Description |
Core Shift | Misalignment of the mold core during injection, leading to dimensional inaccuracies. |
Sticking | The core remains lodged in the part during ejection, often due to insufficient draft angles or excessive friction. |
Warping | Dimensional distortions are caused by the core warping under high temperatures and pressure cycles. |
Cracking or Breakage | Core damage is due to stresses and pressures, often resulting from using less durable materials. |
Wear and Tear | Abrasion and erosion from continuous use lead to a decline in surface quality and dimensional integrity. |
Cooling Issues | Inefficient cooling or heat transmission causes longer cycle times and potential warping or dimensional changes. |
Venting Problems | Inadequate venting that traps air and gases, leading to surface flaws, voids, or incomplete part filling. |
Material and Design Variability | Variability in material properties and design complexity affecting mold lifespan and performance. |
Maintenance Challenges | Lack of regular maintenance leads to issues like corrosion, contamination, or deterioration, affecting mold performance and product quality. |
What is Draft Angle?
The draft angle we mentioned in the previous section refers to a slight taper applied to the vertical surfaces of a part in injection molding. This taper helps the part to be easily released from the mold without causing damage.
Typically, a draft angle of 1 to 2 degrees is recommended for most parts, with more drafts needed for deeper or textured surfaces.
There are positive and negative draft angles. A positive draft means the angle is more than the reference angle, aiding in part release. A negative draft can complicate mold design as it may require the mold to be separated into multiple parts for part removal.
How to Choose Core and Cavity Placement in Injection Molding?
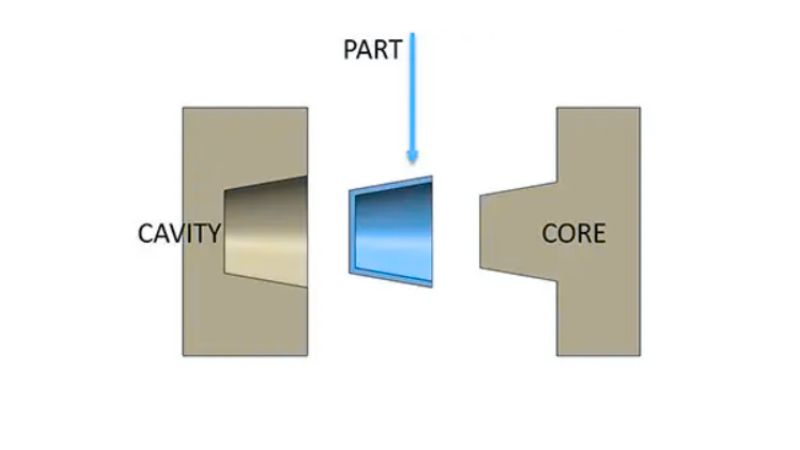
What Affects the Placement of Core and Cavity?
The placement of the core and cavity in injection molding is influenced by several key factors:
Part Design
The complexity and geometry of the part, including features like holes and recesses, dictate core and cavity placement. Protruding features typically require cores, while recessed features are formed by cavities.
Material Properties
The arrangement of the core and cavity in a mold is influenced by the material’s shrink rate, flow characteristics, and injection speed. If a material has a low shrink rate, it can be difficult to ensure the part stays on the side with the ejector pins, requiring special design adjustments.
While most plastics shrink significantly, it’s crucial to understand how the material’s properties might impact the placement of the core and cavity.
Ejection System Layout
After the cooling stage, when the mold is opened, the injection-molded part must always remain attached to the side with the ejector pins.
The design and shape of the ejector system influence the placement of the core and cavity to ensure consistent and reliable ejection of the part.
Symmetry and Gate Location
The sprue is the main channel that carries melted plastic from the injection molding machine into the mold. It usually runs straight into the mold, but sometimes it can go directly into the mold cavity, in which case it’s called a direct sprue gate.
Runners are smaller pathways that branch off from the sprue to distribute the melted plastic to different parts of the mold. This setup allows for the production of multiple parts at once, which is cost-effective, especially for small items.
Gates are the small openings where the plastic enters the mold cavity from the runners. They are narrower than the runners and help control the flow of plastic into the mold.