Injection Molded Part Surface Treatment
Injection Molded Part Surface Treatment
Surface treatments are important in enhancing the aesthetics and functionality of injection molded parts. They can improve the appearance, durability, and performance, making them suitable for various applications.
At Moldie, we specialize in providing high-quality surface finishing solutions for injection molded parts, including electroplate, vacuum coating, paint spraying, printing, laser and crystal label. With our advanced printing technologies, we can deliver vibrant, multi-color designs on a wide range of materials and shapes, bringing your vision to life with exceptional precision and detail.
At Moldie, we specialize in providing high-quality surface finishing solutions for injection molded parts, including electroplate, vacuum coating, paint spraying, printing, laser and crystal label. With our advanced printing technologies, we can deliver vibrant, multi-color designs on a wide range of materials and shapes, bringing your vision to life with exceptional precision and detail.
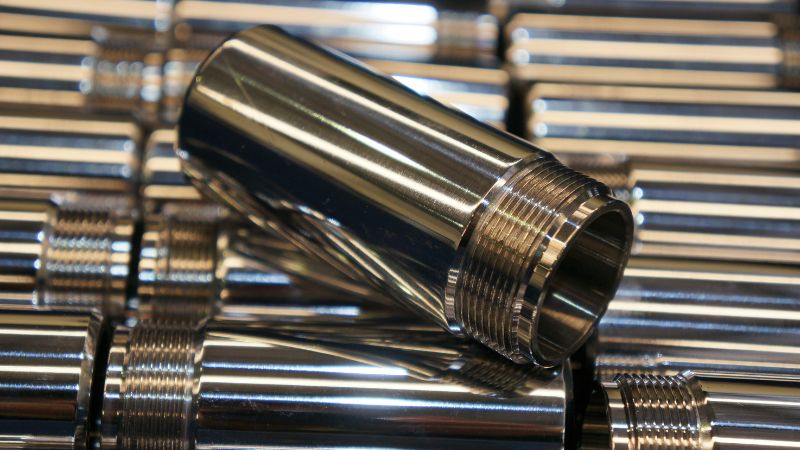
Request a Quote
Electroplate
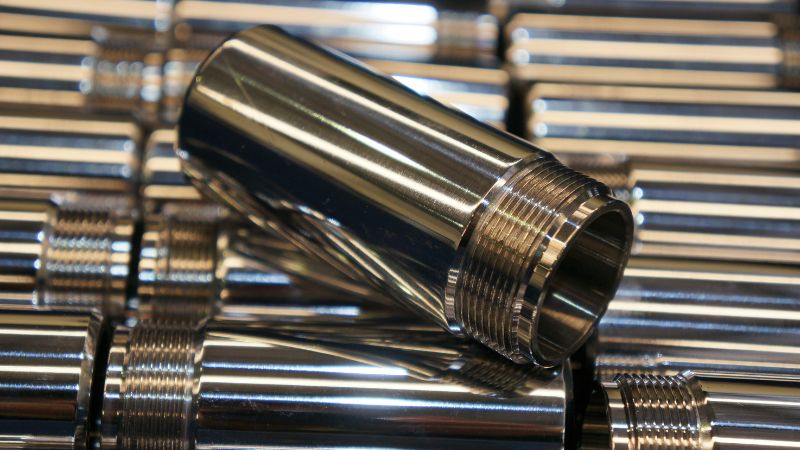
Chrome plating is one of the most popular methods of electroplating. It enhances the mold’s hardness and corrosion resistance.
Bright chromium provides a shiny finish, which is excellent for both functional and aesthetic purposes. When you need a sleek, polished look with added strength, bright chrome is a go-to option.
On the other hand, matte chromium gives a smoother, less reflective surface. This finish is useful when you want a sophisticated look without the gloss.
Moldie Sevice: bright chromium and matte chromium electroplate.
Vacuum Coating
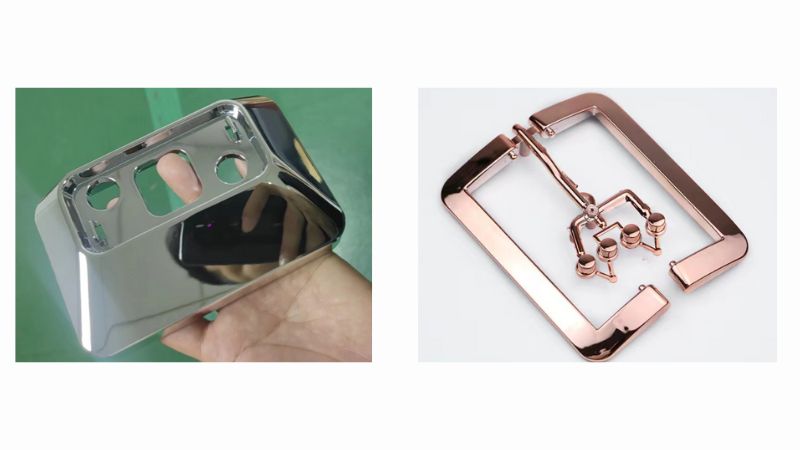
Vacuum coating can create thin films on injection molded parts.
Non-conductive coatings are perfect if you want to ensure that your parts don’t conduct electricity. They are very important in electronic devices.
Conductive coating used to deposit a layer of conductive material on the surface of injection molded parts to improve their conductivity. This technology is mainly used for injection molded parts that need to be conductive, such as electronic product housings, connectors, conductive films, etc.
Common conductive coating materials include copper, silver, gold, and other metal materials, which are usually used for coating. Metal coating has good conductivity and corrosion resistance, but the cost is relatively high.
Moldie Sevice: Indium plate non-conducting coating and aluminum plate conductive coating.
Paint Spraying
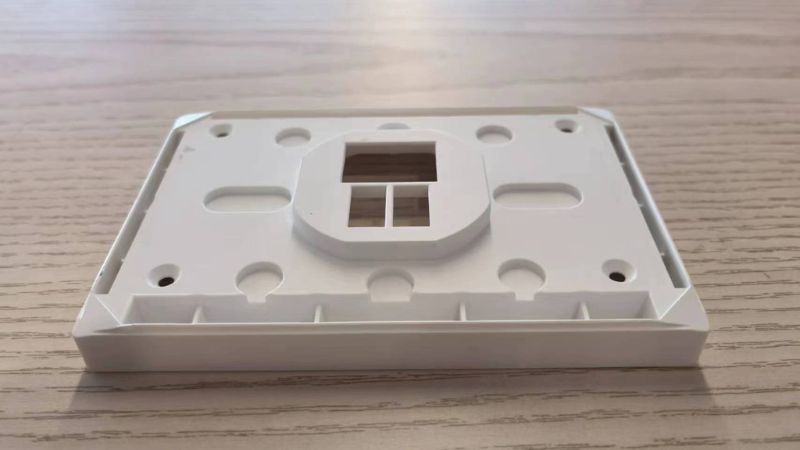
Paint spraying can achieve smooth and uniform finishes for injection molding parts. It involves using a spray gun or atomizer to paint the plastic surfaces.
In this process, paint is atomized into fine droplets. These droplets are then directed onto the part’s surface using compressed air or centrifugal force. This method allows you to achieve a consistent coating, even on complex shapes.
Benefits of Paint Spraying:
- Smooth Finish: Provides a polished look to your parts.
- Uniform Coating: Ensures even coverage across surfaces.
- Efficiency: Covers large areas quickly.
Moldie Sevice: Multiple colors of paint spraying.
Printing
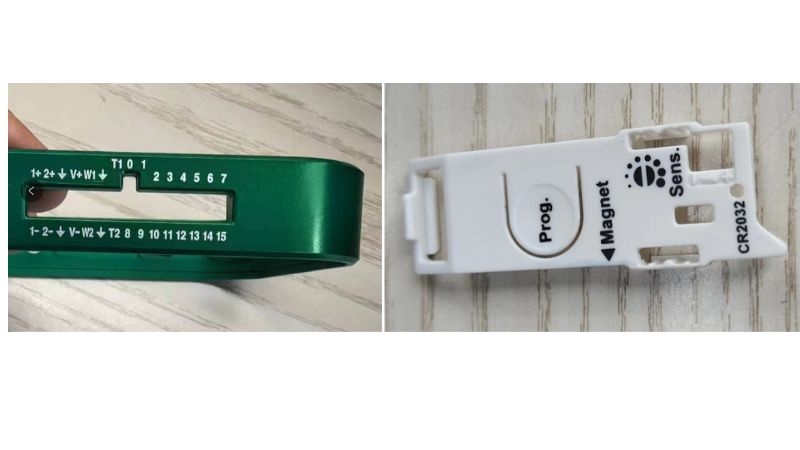
Screen printing is widely used for decorating plastic surfaces. It works by pressing ink through a mesh screen with the help of a squeegee. This method is great for bold colors and large designs. It’s perfect when you want something durable and long-lasting.
Pad printing is another popular option. It uses a silicone pad to transfer ink from an etched plate onto the product. This method is excellent for printing on curved or uneven surfaces. If your parts have a lot of detail or require precision, pad printing might be the best choice.
Moldie Sevice: Multiple colors of screen printing and pad printing.
Laser
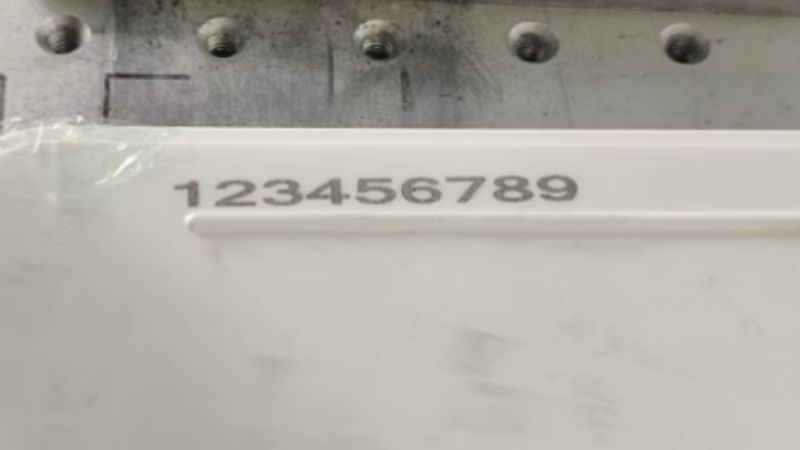
When it comes to laser treatments for injection molded parts, you’re looking at a method that is both precise and versatile. Laser engraving allows you to type or draw on a product. This technique puts details onto the surface and is perfect for adding serial numbers or logos.
The lasers can create intricate designs and patterns. They are used to enhance the appearance of your molded parts.
Moldie Sevice: Black and grey laser treatments.
Crystal Label
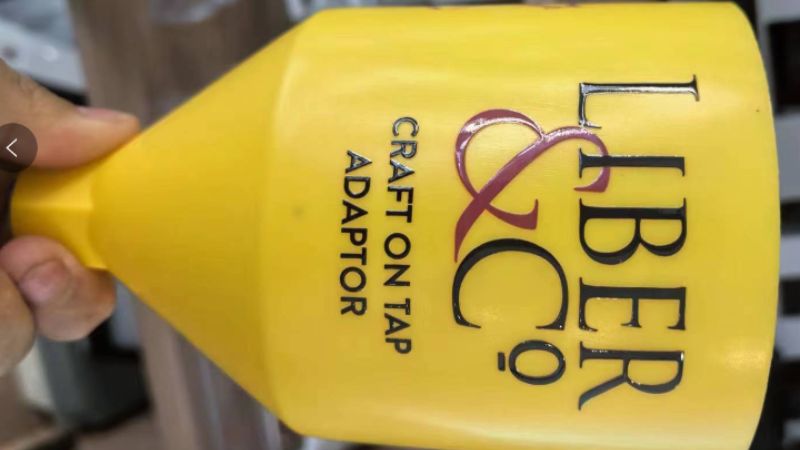
By using crystal labels, you can create translated transparent or translucent layers that showcase intricate designs. This process is perfect for applications where visual impact is key.
These labels are made using special resins during the injection molding process. The resins help achieve a glass-like finish, enhancing the look of your product.
Moldie Sevice: Moldie can create multiple patterns, allowing for infinite design possibilities for your injection-molded parts.