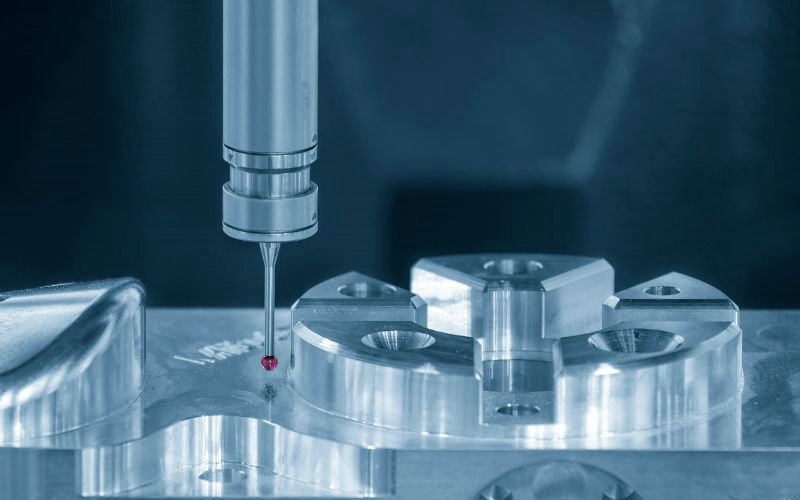
Injection molding is one of the most widely used manufacturing processes for producing high volumes of plastic parts. To ensure consistent part quality and optimal production efficiency, mold temperature is one of the most critical factors to control. The temperature of the mold has a significant impact on the flow behavior of the plastic melt during filling and the cooling rate of the part. If the mold is too cold, the melt will have difficulty filling the cavity completely, leading to short shots or other defects. Conversely, if the mold is too hot, the plastic will take longer to solidify, increasing cycle times. In this post, we’ll help you gain deeper insight into how temperature affects injection molding and specific measures to control mold temperature better.
Explanation of Mold Temperature Control Systems
Components of a Mold Temperature Control System
A mold temperature control system consists of several key components that work together:
- Electronic control system: Processes information from other systems and issues commands
- Mechanical system (circulation pump): Delivers heat from the heating system to the mold
- Liquid level monitoring system: Monitors coolant levels and signals for refills
- Heating system: Heats the coolant to the set temperature
- Cooling system: Removes excess heat, often using plate heat exchangers for indirect cooling
- Temperature sensing system: Measures mold temperature and relays data to the control system
- Pressure relief safety system: Exhausts and relieves pressure if it gets too high
Types of Mold Temperature Controllers
There are two main types of mold temperature controllers based on the heating medium used:
1. Water temperature controllers
– Temperature range generally within 180°C
– Ordinary type: up to 120°C, high-temp type: up to 180°C
2. Oil temperature controllers
– Used for temperatures above 180°C, up to 350°C
– Ordinary type: up to 200°C, high-temp type: up to 350°C
Working Principle
Here’s a simplified explanation of how a water-type mold temperature controller works:
1. The circulation pump pushes water through the system
2. The heating system heats the water to the set temperature
3. Hot water flows through channels in the mold, transferring heat
4. The temperature sensing system measures the mold temperature
5. If the temperature is too low, the control system signals the heater to turn on
6. If the temperature is too high, the cooling system removes excess heat
7. The pressure relief system exhausts coolant if the pressure gets dangerously high
By precisely controlling mold temperature, these systems help minimize defects, optimize cycle times, and improve overall part quality and consistency in injection molding. Investing in a good mold temperature control system tailored to your specific molding requirements can lead to significant manufacturing efficiency gains.
Impact of Mold Temperature on Injection Molding
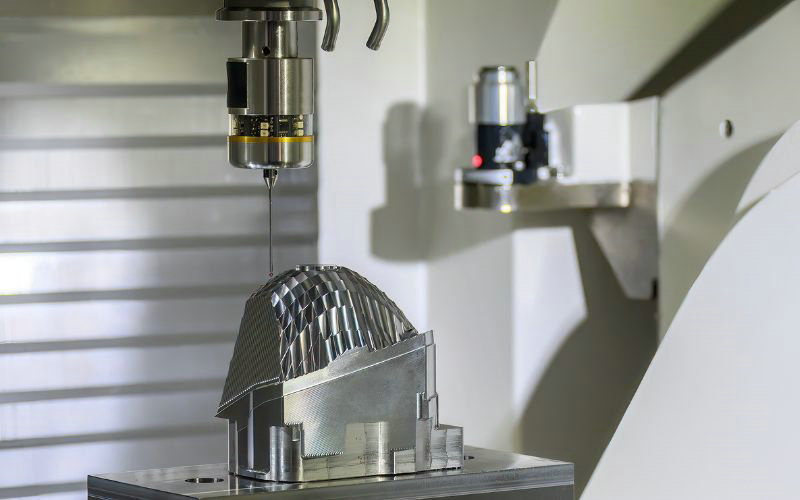
Effects of Low Mold Temperature
1. Poor surface appearance and finish
- A low mold temperature reduces the fluidity of the plastic melt, which can result in incomplete filling and a less glossy surface finish, especially for materials like ABS.
- If the mold temperature is too low for textured surfaces, the melt may not completely fill the fine details of the texture, leading to a poor replication of the mold surface.
2. Increased internal stresses and warpage
- A low mold temperature causes rapid cooling and “freezing” of the molecules, building up internal stresses in the part.
- Uneven cooling and shrinkage due to low mold temperatures can lead to warping and dimensional instability of the molded part.
- Visible weld lines may form on the part surface, reducing its strength.
3. Changes in mechanical properties
- Low mold temperatures can reduce the tensile strength of the molded part compared to higher mold temperatures.
- Rapid cooling at low temperatures may increase the brittleness of the part and lower its impact strength and fatigue resistance.
4. Longer cycle times
- Although low mold temperatures can reduce the cooling time, they require higher injection pressures to fill the cavity due to reduced melt fluidity.
- This can increase the overall cycle time, especially for crystalline materials requiring sufficient cooling for dimensional stability.
Effects of High Mold Temperature
1. Improved surface finish and appearance
- A higher mold temperature allows the plastic to flow more easily and fill fine surface details, resulting in a glossier, more attractive surface finish, especially for materials like ABS.
- The plastic composition is closer to the mold surface at higher temperatures, leading to better texture replication.
2. Enhanced mechanical properties
- Higher mold temperatures can improve the tensile strength of the molded part compared to lower mold temperatures.
- For crystalline plastics, a high mold temperature allows more time for crystallization, increasing the part’s stiffness and heat resistance.
3. Reduced internal stresses and warpage
- High mold temperatures slow down the cooling process, allowing the molecules to relax and orient themselves more uniformly, reducing residual stresses in the part.
- More gradual cooling at higher mold temperatures minimizes differential shrinkage and warping of the molded part.
4. Increased cycle times and potential for defects
- The main drawback of high mold temperatures is the longer cooling time required, which increases the overall cycle time and reduces productivity.
- Excessively high temperatures can cause the plastic to stick to the mold, creating bright spots or other surface defects.
- There is a greater risk of flash and burrs forming if the mold temperature is too high, as the plastic remains molten for longer.
5. Possible degradation of material properties
- Some polymers may experience thermal degradation or oxidation if processed at excessively high mold temperatures, leading to a reduction in molecular weight and mechanical properties.
- The combination of high mold temperature, high melt temperature, and long residence time poses the greatest risk of material degradation during molding.
Measures to Better Control Mold Temperature
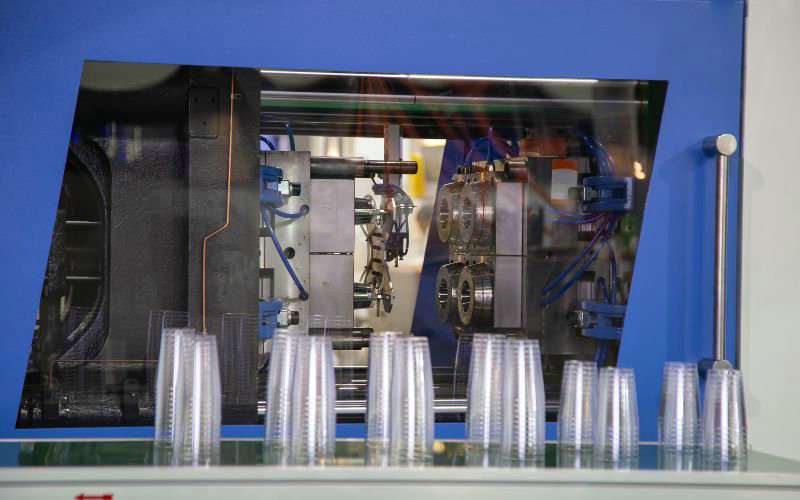
1. Utilize Mold Temperature Controllers
- Mold temperature controllers are essential devices that regulate and maintain precise mold temperatures. They work for both heating and cooling purposes.
- Select a mold temperature controller with sufficient flow rate and pressure capabilities to meet the needs of your specific mold.
2. Monitor Coolant Flow Rates
- An adequate coolant flow rate is critical as it dictates how quickly the mold can be cooled, influencing both product quality and cycle time.
- Check that the flow rate is neither too low, which can cause poor temperature control, nor too high, which can be wasteful and inefficient.
3. Establish Temperature Gradient Control
- Maintain a consistent temperature across the mold to prevent defects. A proper temperature gradient control minimizes internal stresses within the molded part.
- Mold designers should strive for a temperature differential of no more than 5°C between the core and cavity to reduce warpage.
4. Optimize Cooling Channel Design
- The location, depth, and pitch of cooling channels significantly impact mold surface temperature uniformity.
- Aim for uniform mold surface temperature by optimizing cooling channel depth (ideally 1-2.5 times the channel diameter) and pitch (2.5-3 times the channel diameter).
5. Select Appropriate Mold Materials
- The mold material has a profound impact on heat exchange. Consider thermal conductivity when selecting mold materials.
- For high-tolerance applications, copper alloys may be necessary to maintain a low-temperature differential and reduce warpage, while less expensive materials like H13 steel can be used for lower-tolerance parts.
6. Implement Rapid Heating and Cooling Techniques
- Rapid Heat Cycle Molding (RHCM) involves quickly heating the mold above the melting point to facilitate plastic flow, and then rapidly cooling it to accelerate solidification.
- RHCM can improve surface quality and precision, but it is energy-intensive and should be reserved for special applications.
By implementing these measures and continuously monitoring mold temperature performance, injection molders can achieve tighter control over this critical process parameter. This leads to improved part quality, reduced defects, and optimized cycle times for greater manufacturing efficiency.
Injection Molding Temperature for Different Plastics
The following table summarizes the recommended injection molding temperatures for different plastics:
Plastic Type | Material | Melt Temperature (°C) | Mold Temperature (°C) |
---|---|---|---|
Amorphous Plastics | ABS | 210-275 | 50-90 |
PS | 170-280 | 10-60 | |
PMMA | 180-260 | 50-80 | |
PC | 280-320 | 80-120 | |
Semi-Crystalline Plastics | PP | 200-280 | 30-80 |
HDPE | 210-300 | 20-70 | |
LDPE | 160-260 | 20-70 | |
POM | 160-280 | 50-120 | |
PA6 | 230-290 | 40-120 | |
PA66 | 260-300 | 40-120 | |
PBT | 240-275 | 60-100 | |
High-Temperature Plastics | PES | 330-380 | 120-180 |
PEEK | 340-390 | 120-160 |
Note: The optimal molding temperature range depends on the specific grade, additives, part geometry, desired balance of properties, and cycle time. Careful control of both melt and mold temperature is critical to achieve high part quality and manufacturing efficiency in injection molding.