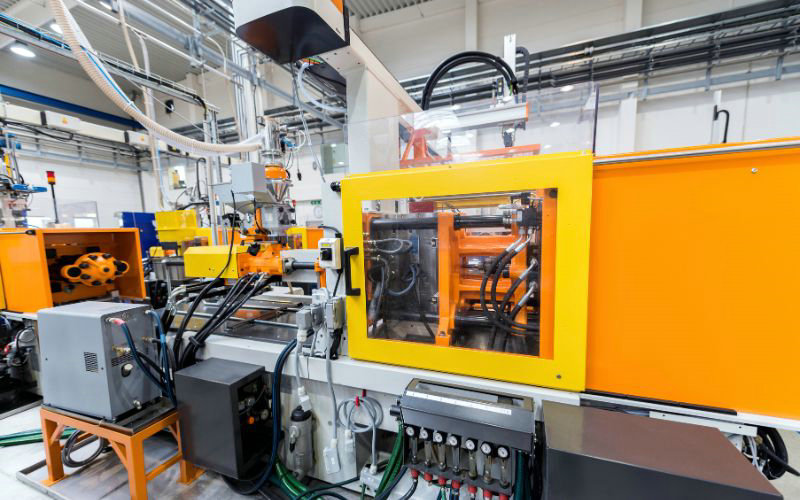
Injection Mold Cooling System Design
The cooling system ensures uniform cooling and efficient temperature control when designing your injection mold. This not only impacts the quality of the molded part but also significantly influences the cycle time and cooling efficiency. Baffles, bubblers, and thermal pins are specialized cooling strategies used to optimize temperature distribution in injection molds, especially in challenging areas that regular drilled channels cannot effectively reach. They enhance heat removal by increasing coolant contact surface area or utilizing phase change heat transfer. Proper design of these features is critical for achieving uniform part cooling and minimizing cycle times. Now let’s delve into their unique functions:
Baffles
- A baffle is a cooling channel drilled perpendicular to a main cooling line, with a blade that separates the channel into two semi-circular passages.
- The coolant flows in one side of the blade from the main line, turns around the tip to the other side, and then flows back to the main line.
- Baffles increase the surface area that coolant can reach in areas that would normally lack cooling.
- The metal sheet forming the baffle can be twisted into a helix shape for 12-50 mm diameters to provide a more homogeneous temperature distribution.
- Single or double-flight spiral cores are another development of baffles.
Bubblers
- A bubbler is similar to a baffle but replaces the blade with a small tube.
- The coolant flows into the bottom of the tube and “bubbles” out the top, then flows down around the outside of the tube back to the main channel.
- Bubblers provide the most effective cooling for slender cores.
- The inner and outer diameters of the bubbler should have a ratio of 0.707 for equal flow resistance.
- Bubblers can also be used to cool flat mold sections that can’t accommodate drilled channels.
Thermal Pins
- A thermal pin is an alternative to baffles and bubblers that consist of a sealed cylinder filled with fluid.
- The fluid vaporizes as it draws heat from the mold and condenses as it releases the heat to the coolant continuously.
- Thermal pins have a heat transfer efficiency of almost 10 times greater than copper or copper alloy inserts.
- Air gaps between the thermal pin and mold should be avoided or filled with a highly conductive sealant for optimal heat conduction.
Different Types of Injection Mold Cooling Systems
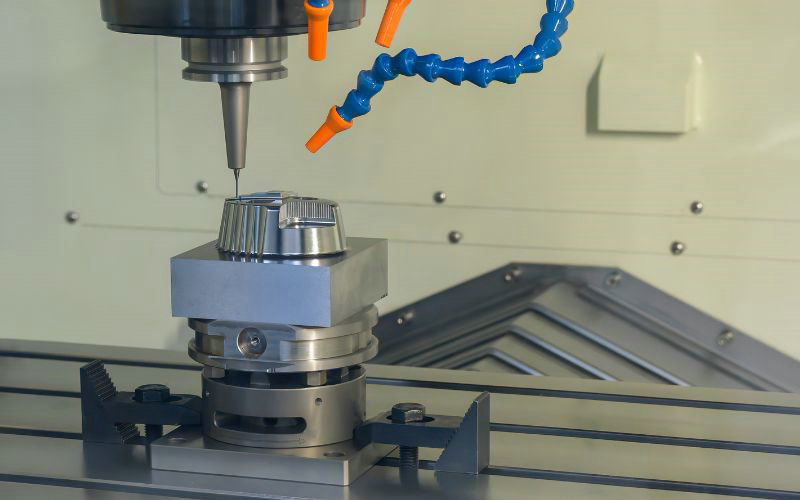
The right cooling system ensures uniform temperature distribution, minimizes warping and shrinkage, and promotes energy efficiency and cooling effectiveness.
Water-Cooled Systems
Water-cooled systems are the most commonly used cooling method in injection molding due to their efficiency and effectiveness in heat removal. These systems circulate chilled water through channels within the mold, absorbing heat from the mold and the molten plastic. This method is particularly effective for intricate molds and temperature-sensitive materials, as it provides excellent temperature control and heat absorption capabilities.
Air-Cooled Systems
Air-cooled systems utilize fans or blowers to dissipate heat from the mold’s surface through convection. This method is simpler and less costly to implement compared to water-cooled systems. Air cooling is suitable for less complex mold designs and materials that are less sensitive to temperature fluctuations. However, it is less efficient at heat absorption and temperature control compared to water-cooled systems.
Oil-Cooled Systems
Oil-cooled systems are used in scenarios where very rapid cooling is required. These systems circulate oil, which can remove heat more efficiently than air. Oil cooling is generally more expensive than water or air cooling but is favored in large injection molding operations or for materials that need a very quick transition from high to low temperatures.
Cryogenic Cooling Systems
Cryogenic cooling systems use extremely low-temperature substances, like liquid nitrogen, to rapidly cool the mold. This advanced method can significantly reduce cooling time and energy consumption but is usually reserved for specialty applications due to the complexities and costs involved.
Mixed-Media Cooling Systems
To tailor thermal management, you may encounter mixed-media cooling systems that blend different cooling mediums, such as air and water. These hybrid systems aim to leverage the benefits of each medium like the quick cooling of water with the simplicity of air systems, optimizing efficiency for specific injection molding applications.
The Impact of Injection Mold Cooling on Molded Products

The cooling phase in the injection molding process plays a crucial role in determining the molded products’ quality, efficiency, and overall success. This phase directly impacts various aspects of the final product, including the molding cycle, modality, dimensional accuracy, and mechanical properties.
Molding Cycle
The cooling time is a significant portion of the injection molding cycle, accounting for about 50% to 80% of the total cycle time. Efficient cooling is essential for reducing the molding cycle time, thereby increasing production efficiency and output. A well-designed cooling system can significantly shorten the cooling time without compromising the quality of the molded product, leading to faster production rates and lower manufacturing costs.
Modality
The modality of a molded product refers to its physical and aesthetic characteristics, including surface finish, warpage, and the presence of defects such as sink marks or weld lines. The cooling phase influences these characteristics by affecting how the material solidifies within the mold. Uniform and controlled cooling can prevent defects and ensure a high-quality surface finish. Conversely, uneven cooling can lead to warpages and other defects compromising the product’s appearance and functionality.
Dimensional Accuracy
Dimensional accuracy is critical for the performance and assembly of injection-molded parts. The cooling phase directly impacts the shrinkage and warpage of the material, which in turn affects the dimensional accuracy of the final product. Proper cooling ensures uniform shrinkage and minimizes warpage, resulting in parts that meet precise dimensional specifications. Factors such as mold temperature, cooling channel design, and cooling medium can be optimized to achieve the desired dimensional accuracy.
Mechanical Properties
The cooling phase also influences the mechanical properties of injection-molded products, such as strength, stiffness, and impact resistance. Rapid or uneven cooling can induce residual stresses within the material, potentially reducing strength and increased susceptibility to cracking or failure under load. Controlled cooling can promote uniform crystallization in semi-crystalline polymers and minimize residual stresses, thereby enhancing the mechanical properties of the final product.
In conclusion, the cooling phase in injection molding is pivotal for ensuring the efficiency of the molding cycle, the quality and modality of the molded products, their dimensional accuracy, and their mechanical properties. A well-engineered cooling system, tailored to the specific requirements of the material and the part being molded, is essential for producing high-quality injection-molded products that meet or exceed performance and aesthetic standards.