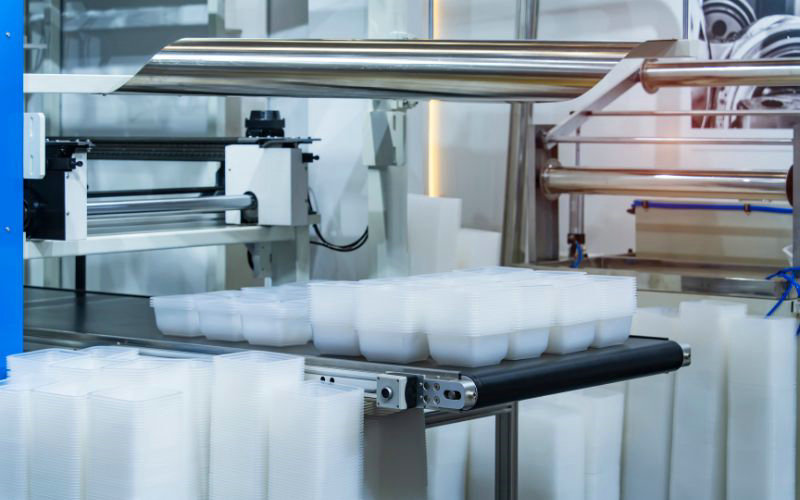
What Are Flow Lines in Injection Molding
Flow lines are a common defect encountered in plastic injection molding. These lines appear as patterns or streaks on the surface of a molded part. To picture them, imagine the wavy lines or ring-like ripples you may see when a stone is thrown into a still pond. Understanding flow lines can help ensure your products’ structural integrity and aesthetic quality.
Flow marks in injection molding do not typically affect the structural integrity of the molded part but can be aesthetically displeasing and may be unacceptable for high-visibility or high-aesthetic applications. Therefore, addressing these issues during the design and production stages is crucial for achieving high-quality injection molded parts.
Causes of Flow Lines or Flow Marks
Flow lines or flow marks can significantly affect the aesthetics and performance of your final product. Understanding the prime culprits behind these anomalies ensures that you can take proactive measures to prevent them. Flow lines are primarily caused by variations in the cooling rate of the plastic as it flows through the mold. Several factors contribute to the formation of flow lines:
Too Low Melting and Molding Temperature
One key factor causing flow lines is the melting and molding temperature. If your material does not reach an adequate temperature, it won’t flow correctly, leading to unsightly lines or marks on your parts. Increasing melting and molding temperatures within recommended guidelines ensures the material maintains fluidity and pressure evenly distributed throughout the mold cavity, minimizing potential flow marks.
Injection Speed
Too Slow Injection Speed:
When the injection speed is too slow, the molten plastic begins to cool before it completely fills the mold cavity. This premature cooling can cause the plastic to solidify at different rates, leading to the appearance of flow lines.
A slower flow allows the material to start solidifying in thinner sections of the mold or areas farther from the gate, which can disrupt the uniform flow of the remaining molten plastic.
Too Fast Injection Speed:
Conversely, a very high injection speed can also contribute to the formation of flow lines. If the plastic is injected too quickly, it can create turbulent flow patterns within the mold. This turbulence can cause variations in how the material cools and solidifies, leading to visible flow lines on the surface of the part.
High speeds can also lead to other issues like jetting or splashing of the molten plastic, which disrupts the smooth flow needed to fill the mold evenly and can result in flow lines.
Mold Design Causes
Uneven Wall Thickness:
Uneven wall thickness in a mold can lead to non-uniform cooling rates of the molten plastic. Thinner sections of the mold cool faster than thicker sections, causing the molten plastic to solidify at different rates. This differential cooling can disrupt the flow of the molten plastic, leading to the formation of flow lines.
Gate Placement and Type:
The location and type of gates in a mold design significantly influence how plastic flows into the mold cavity. Improper gate placement can lead to uneven flow, causing some areas to cool faster than others. This can result in visible flow lines on the finished product. Using fan gates, for example, can help distribute the material more evenly, reducing the likelihood of flow lines.
Mold Venting:
Adequate venting in the mold is essential to allow air to escape as the molten plastic fills the mold cavity. Poor venting can trap air, creating pressure pockets that disrupt the flow of plastic and contribute to the formation of flow lines.
How to Fix Flow Lines on Plastic Parts
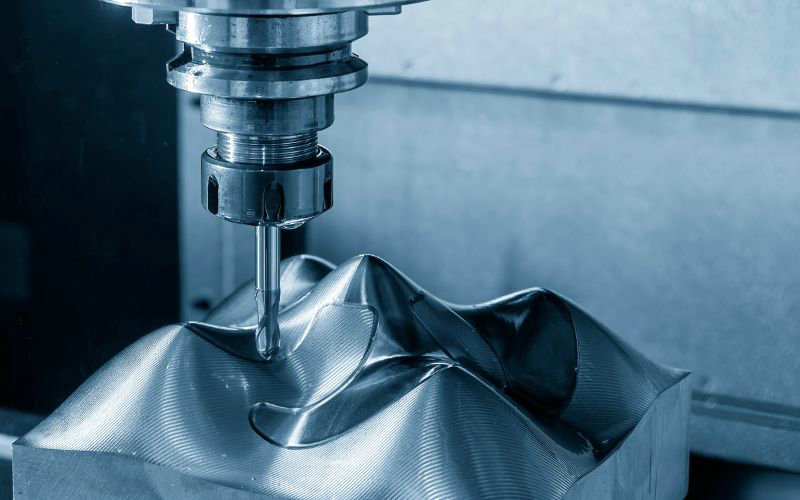
Post-Processing Techniques
If flow marks cannot be entirely eliminated through process and design adjustments, various post-processing methods can be used to minimize their visibility. These include:
- Texturing the Mold Surface: Adding a texture to the mold surface can help disguise flow marks, making them less noticeable on the final product.
- Painting and Coating: Applying paint or a coating can effectively cover up flow marks, improving the aesthetic quality of the part.
- Polishing and Sanding: Mechanical finishing processes like sanding or polishing can smooth out the surface, reducing the visibility of flow marks.
Simulation Tools
Using injection molding simulation software can help predict the occurrence of flow marks and other defects, allowing for preemptive adjustments to the mold design, material selection, and processing parameters.
Implementing these strategies requires carefully balancing machine settings, mold design, and material properties. Each adjustment should be tested and validated to ensure that it does not introduce other defects or compromise the structural integrity and functionality of the molded parts.
How to Avoid Flow Lines in Injection Molding
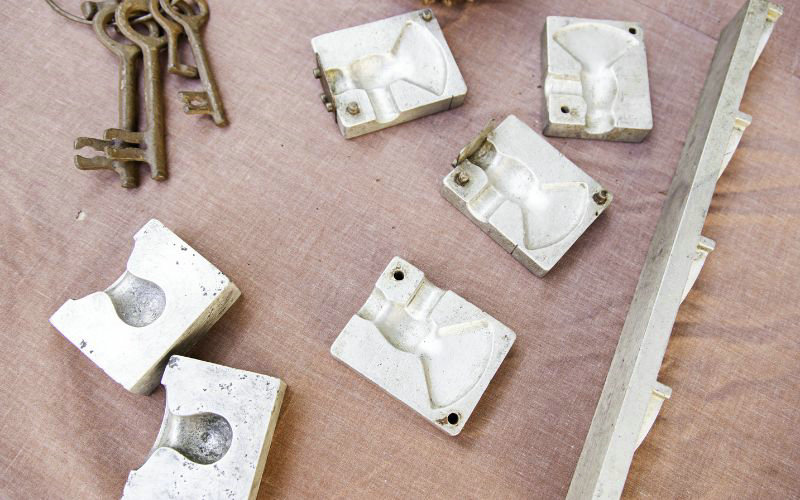
Adjust the Temperature Parameters
1. Temperature of the Mold: Increasing the mold temperature can prevent the plastic from cooling too rapidly upon contact with the mold cavity, which helps reduce the formation of flow lines.
2. Material Temperature: Properly setting the temperature of the molten plastic is crucial. The plastic may not flow evenly if the temperature is too low, leading to flow lines. Conversely, too high a temperature can cause degradation of the plastic.
3. Nozzle and Barrel Temperature: Adjusting the nozzle and barrel temperatures can also impact the plastic flow. Ensuring these are optimized for the specific material being used can help maintain a consistent flow and reduce the occurrence of flow lines.
Control the Injection Speed
1. Optimal Speed Setting: The speed at which the molten plastic is injected into the mold needs to be fast enough to fill the mold before the material starts cooling but not so fast that it causes turbulence or other defects like jetting or splashing.
2. Multi-Stage Injection Speeds: Implementing multi-stage injection speeds can be beneficial. Starting with a faster initial injection to quickly fill the mold, followed by a slower speed to pack the mold, can help minimize flow lines.
Improve Gate, Sprue, & Runner Design
1. Gate Design: The size, type, and location of gates significantly affect how the plastic flows into the mold. Proper gate design ensures even flow and distribution of plastic, reducing the risk of flow lines. Fan gates, for example, can help distribute the material more evenly.
2. Sprue and Runner Optimization: Ensuring that sprues and runners are appropriately sized and configured helps maintain a steady plastic flow. They should not be too narrow, as this can restrict flow and increase the cooling rate, leading to flow lines.
3. Venting: Adequate venting in the mold allows air to escape as the mold fills, preventing air traps and pressure build-ups that can disrupt the plastic flow and contribute to the formation of flow lines.
By carefully managing these aspects of the injection molding process, manufacturers can significantly reduce the occurrence of flow lines, leading to higher quality and more aesthetically pleasing plastic parts.
Cooperate with Moldie for Injection Molding Services
When you partner with Moldie for your injection molding needs, you access a suite of services backed by industry expertise and precision. Our focus on excellence in both design and production ensures that your projects meet the highest standards.
Material Selection and Precision: Moldie’s knowledgeable team assists you in selecting the optimal materials for your product, resulting in parts that exhibit the required characteristics, such as UV resistance, heat resistance, and the necessary physical properties.
- Opt for materials that offer the right balance between strength and flexibility.
- Ensure that science guides the material selection process for peak performance.
Innovative Molding Technologies: Utilize advanced molding technologies operated by computer systems to achieve consistent quality. The company’s sophisticated equipment allows for precise control over injection pressure and nozzle diameter, crucial factors in producing defect-free parts.
- Injection pressure is finely tuned to ensure uniform flow and wall thickness.
- The nozzle diameter matches the material flow requirements, enhancing the molding process.
Mold Design and Fabrication: Moldie excels in creating molds that consider your design’s complexities.
- Molds are engineered for durability and engineered to maintain uniform wall thickness in your products.
- A strategic approach to mold construction leads to repeatable accuracy and quality.
Your partnership with Moldie translates into cost-effective, high-quality injection molding services that meet your specific requirements. Their commitment to precision and scientific methodology positions them as a leading provider in the global mold industry.