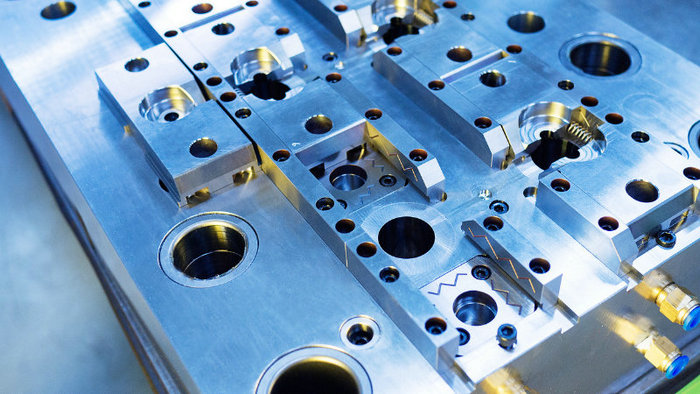
Introduction to Clear Plastic Injection Molding
When you want to create transparent plastic parts with high clarity, clear plastic injection molding is a trusted manufacturing process you’ll come across. This method is incredibly versatile and used across a variety of industries—from automotive to consumer goods. The essence of injection molding lies in its ability to shape plastic into durable, clear components such as lenses and light fixtures.
Materials in Clear Plastic Molding
When considering clear plastic molding for your projects, your selection of materials will significantly influence the final product’s properties such as clarity, strength, and resistance to UV rays and chemicals.
Acrylic (PMMA) Properties
Acrylic, also known as PMMA (Polymethyl Methacrylate), is a popular plastic for injection molding for its excellent optical light transmittance and UV resistance. It is a non-toxic resin that is somewhat brittle but can be polished to maintain its clear finish.
Polycarbonate (PC) Advantages
Polycarbonate (PC) boasts remarkable impact resistance, making it an ideal injection molding material for products like safety goggles and heat shields. Its strength is that it doesn’t compromise on transparency, offering great clarity for various applications.
Polyethylene (HDPE) and its Uses
High Density Polyethylene (HDPE) is a thermoplastic known for its strength and used in products that demand a durable yet somewhat flexible structure, such as bottles and containers. It’s also non-toxic, making it safe for food-related applications.
Other Resins for Transparency
Beyond the primary materials mentioned, there are other resins like PET and PEI that deliver transparency. While PET is frequently used in beverage bottles and packaging, PEI can handle high-temperature applications, often utilized in aerospace engine components.
Thermoplastics vs. Engineering Plastics
Thermoplastics like Acrylic and HDPE are commonly used for injection molding due to their ease of processing and versatility. On the other hand, engineering plastics such as Polycarbonate offer advanced properties like enhanced impact resistance suitable for more demanding applications.
Additives and Modifiers
To enhance certain qualities of clear plastics, additives and modifiers like UV stabilizers and colorants can be incorporated. These substances can improve a resin’s UV resistance, alter its flexibility, and introduce various colors while maintaining transparency.
Here is the summarization:
Material | Key Properties | Typical Applications |
Acrylic (PMMA) | Excellent optical clarity, UV resistance, high strength | Lenses, lighting fixtures, transparent parts |
Polycarbonate (PC) | High impact strength, good optical clarity | Safety goggles, automotive parts, heat shields |
Polyethylene (HDPE) | Tough yet flexible, excellent chemical resistance | Bottles, food containers |
PET | Good clarity, high strength, moisture barrier | Packaging, beverage bottles |
Polyetherimide (PEI) | Withstands high temps, good clarity, chemical resistance | Engine parts, aerospace applications |
Thermoplastics | Easy to process, versatile | General purpose injection molding |
Engineering plastics | Advanced properties like impact or heat resistance | Demanding applications like automotive |
Design and Engineering of Clear Plastic Parts
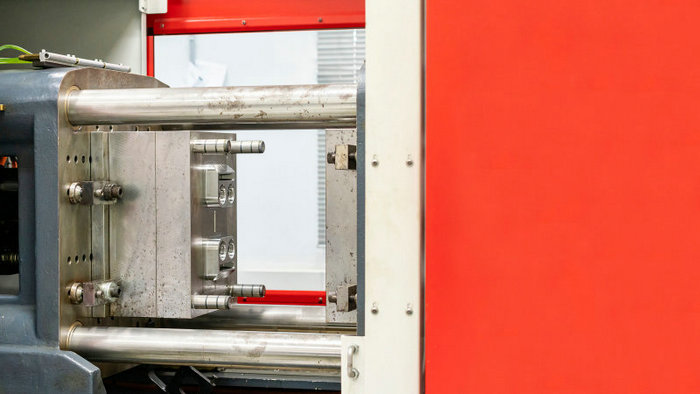
When designing clear parts, the focus on achieving high clarity and transparency is paramount. Addressing material properties and structural considerations plays a crucial role in the optical clarity and durability of the finished product.
Ensuring Optimal Clarity
For the ultimate optical clarity and light transmission in your clear molded parts, material selection is critical. You’ll want to choose materials that are inherently clear, such as acrylic and polycarbonate, which allow for maximum transparency and minimal haze. Factors like wall thickness must be carefully managed to prevent defects like sink marks, which can detract from clarity. Keep your wall thickness uniform to maintain the best optical properties and prevent uneven surfaces that can cause distortion.
Addressing Material Properties
Selecting the right material also involves considering how the plastic will interact with its environment. Be aware of potential chemical exposure, as transparent parts are often used where visibility of the content is crucial, and substances like moisture, solvents, acids, and other corrosive materials may come into contact with the plastic. For instance, acrylic is more brittle but offers excellent clarity, while polycarbonate is more durable but can absorb moisture which might affect dimensional stability.
Structural Considerations
Your clear plastic parts need to withstand the demands of their application. To ensure dimensional stability and avoid stress cracking, you must design with potential load and environmental conditions in mind. This entails considering factors such as reinforcement ribs which should be designed to avoid thick sections that cool inconsistently, causing internal stresses.
Aesthetics and Finish
Finally, the aesthetic appeal of your clear plastic part is influenced by the surface finish. You have options ranging from a high-gloss polish to a subtle matte finish. But regardless, a smooth and consistent finish is essential for maintaining aesthetic and scratch resistance. Remember, surface imperfections are more noticeable in clear plastics, so attention to detail during the polishing or texturing phase is crucial for a cosmetic grade finish.
Manufacturing Process and Machinery
For a smooth product surface finish, a meticulous focus is needed on raw materials, hardware, mold, and even product design throughout the entire injection process. Strict, or sometimes special, requirements are often applied. Transparent plastic materials, which typically have a high melting point and poor fluidity, often require fine-tuned process parameter modifications. This includes adjustments to mold temperature, injection pressure, and injection speed to ensure complete mold injection. These adjustments also aid in completely mitigating product deformation or cracking that could result from internal stress.
This section will provide an in-depth look at the injection procedures and specialized injection molding machines critical to producing clear injection molded components.
Injection Molding Equipment
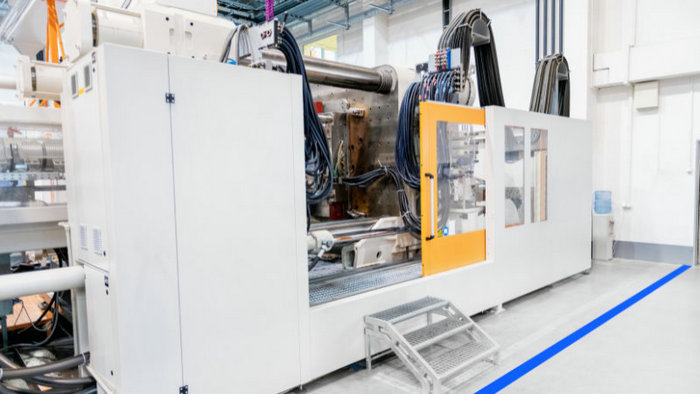
Choosing the right injection molding equipment is crucial for manufacturing high-quality clear plastic parts. You’ll need a machine that can handle the specific plastic material you use, such as acrylic, for its dimensional stability and scratch resistance. The machine must offer precise control over injection speed and pressure to ensure a clear finish. It’s common to use CNC machining during the creation of complex mold designs, as it provides the design flexibility and precision required for high-quality outputs.
Injection Molding Process
1. Materials Prep:
Clear plastic pellets or resin in the required formulation are dried to remove moisture. This prevents defects in the final part.
- Clear plastic pellets are fed from dryers that remove moisture absorbed during storage.
- Dryers use heat and desiccant to lower moisture content to less than 0.1%.
- Proper drying is crucial to prevent small bubbles and cracks from forming during melting and molding from trapped moisture vaporizing.
2. Injection Unit:
The dried plastic is fed into the injection unit – a large barrel with a rotating screw. Heaters raise the plastic to its melting point.
- Plastic pellets enter the injection unit, which consists of a heated barrel and an Archimedes screw.
- The barrel is lined with individually controlled heating zones to gradually raise the plastic’s temperature.
- As the screw rotates, it conveys the plastic forward while melting and mixing it using shear force and conducted heat.
- Additives like UV stabilizers and lubricants are thoroughly dispersed at this stage for uniform properties.
3. Melting and Mixing:
As the screw turns, it melts and mixes the plastic uniformly. Any additives are dispersed thoroughly for consistent properties.
4. Mold Clamping:
The precision-machined mold halves are brought together and clamped tightly to prevent leakage of molten plastic. Multi-cavity molds can produce multiple parts at once.
- The mold, made of steel for its heat conductivity, consists of top and bottom halves with the part designs.
- Clamping units exert tons of force to bring the mold halves tightly together, sealed by a parting line.
- Multi-cavity molds have several sets of cavities to produce multiple parts simultaneously.
5. Injection:
Under high pressure, the molten plastic is injected into the mold cavities through a sprue and runner system. Air is vented to avoid bubbles.
- When plastic is fully melted and homogeneous, it is injected under high pressure, 500-1500 psi.
- It flows through narrow injection channels called runners and sprues into each mold cavity.
- Air trapped is vented out special vents to avoid bubbles in the parts.
6. Cooling:
Cooling channels in the mold carry heat-transferring fluids to solidify the plastic within the mold.
- Cooling lines circulated water or glycol inside the mold to rapidly draw heat from the plastic.
- Typical cooling times are 10-60 seconds depending on material and part thickness.
- Proper cooling ensures plastic solidifies with a uniform molecular structure.
7. Ejection:
Once solidified, the mold opens and ejector pins push the finished part out of the mold. Excess plastic is still attached to sprues and runners.
- Mold opens and ejector pins push parts out when fully solidified and still warm but rigid.
- Excess plastic remains attached to sprues and runners outside the mold.
8. Trimming:
In a separate station, the sprues and runners are cut/broken away from the parts to give the final shape.
- Parts are transferred to an automatic trimming station.
- Sprue and runner stubs are cut or broken away from the parts.
- This gives the final dimensions and surfaces to the parts.
9. Quality Checks:
Parts undergo visual and mechanical tests to ensure dimensional accuracy and absence of defects before packaging.
- Parts undergo gauging for dimensions and visual inspection for defects.
- Testing may include tensile or impact tests on sample parts.
- Only conforming parts are packed for shipment.
Challenges in Clear Plastic Molding
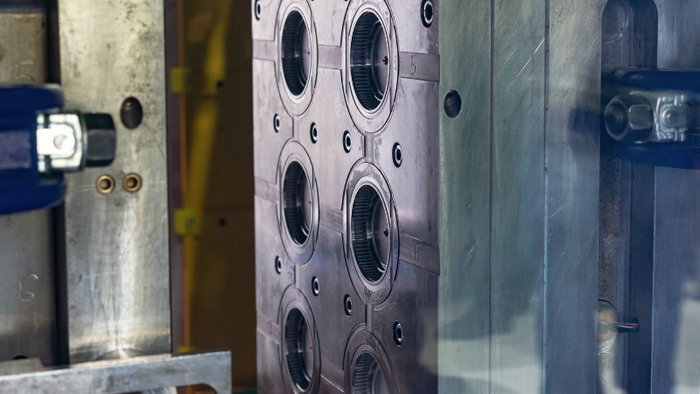
When it comes to clear plastic injection molding, achieving flawless results poses several significant challenges. From ensuring uniformity in thickness to managing reactions with chemicals, each step demands precision to maintain the aesthetics and functionality of your transparent parts.
1. Maintaining Product Consistency
Achieving dimensional stability is crucial; however, sink marks in thicker sections can affect consistency. To ensure uniform wall thickness and maintain clarity, molders must carefully balance fill times and cooling rates. Additionally, rates of thermal expansion can vary, potentially altering the dimensions and properties of your transparent parts.
2. Management
Temperature control is essential for clear plastic molding. Extreme temperatures can introduce stress, which diminishes clarity. Precise mold temperature management during processing prevents defects such as haziness or discoloration, ensuring the transparent quality of your parts.
3. Dealing with Shrinkage and Warping
As the molded parts cool, shrinkage and warping can occur, compromising the part’s integrity and transparency. Adjustments to the cooling process and mold design help mitigate these issues and maintain the exact desired shapes.
4. Chemical Compatibility
Choose materials that can withstand exposure to various chemicals, including acids, corrosive materials, and solvents without losing clarity. Chemical resistance ensures that the clear plastics retain their appearance and structure when in contact with these substances.
5. Impact and Stress Resistance
Clear plastics can sometimes be more brittle, leading to cracking under impact or stress. Identifying materials with high impact resistance and adjusting the injection molding process to enhance the strength can prevent such failures and improve the durability of your clear plastic products.
Environmental Considerations
In the realm of clear plastic injection molding, your attention to environmental factors is crucial. This includes not just using eco-friendly materials but also adhering to safety and regulatory standards, reducing waste, and considering biodegradable options.
- Recycling and Bioplastics:Biodegradable and recycled plastics are at the forefront of sustainable practices in your industry. Consider using biodegradable polymers like PLA for your projects, which offer a reduced environmental footprint. Additionally, implementing recycling programs for post-industrial and post-consumer plastics can also contribute to sustainability.
- Reducing Waste in Manufacturing: Waste minimization in manufacturing is not just good for the environment; it can also reduce your costs. Optimize your production processes to conserve raw materials and energy. Technologies that facilitate closed-loop manufacturing systems can capture and repurpose waste products, which is a stride toward sustainable manufacturing.
- Regulatory Compliance and Safety: Adhering to regulations is non-negotiable. The manufacturing processes must comply with environmental, health, and safety standards. Understand and follow the guidelines set by regulatory bodies to ensure non-toxic, safe, and sustainable products.
Frequently Asked Questions
What is the process for injection molding clear plastic parts?
The injection molding process for clear plastic parts involves precision in tooling design and preparation of raw materials. Detailed planning is essential to ensure the transparency and quality of the final product.
What are the best materials for creating transparent plastic items?
Polycarbonate and acrylic are popular choices for their clarity and strength. Each material offers different benefits, such as acrylic being scratch-resistant and polycarbonate being impact-resistant.
How do you ensure clarity and prevent cloudiness in plastic injection molding?
To ensure clarity and prevent haze, use high-quality resins and maintain proper control over the molding process. Regular equipment maintenance and thorough material preparation help in reducing defects.
What are the challenges of working with clear hard plastic in injection molding?
One major challenge is avoiding blemishes, such as bubbles or streaks, which are more visible in clear plastics. Controlling the molding environment and process parameters is crucial to address these issues.
How can you add threads to injection molded plastic components?
Threads can be directly molded into the parts or machined post-molding. Molded-in threads require careful design and precision engineering to ensure the threads’ integrity and functionality.
What factors affect the strength and durability of clear plastic materials in injection molding?
Material selection, part design, and molding conditions all play a role. The presence of impurities, stress concentrations, and improper processing parameters can compromise the strength and durability of the finished part.