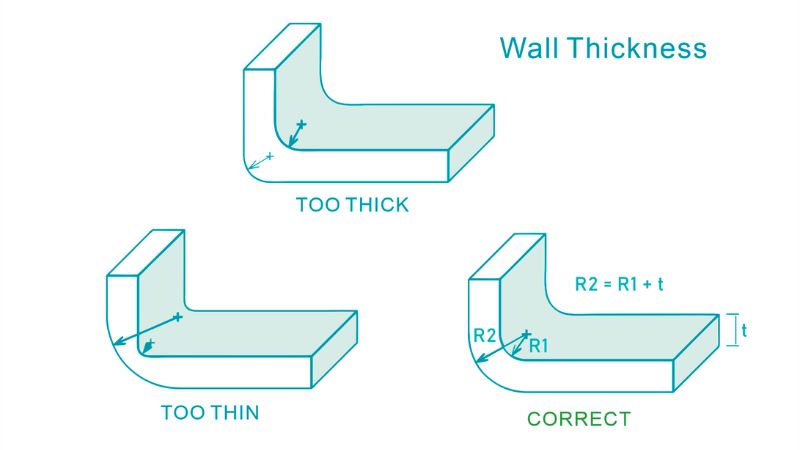
From understanding the basics of wall thickness to navigating material-specific considerations, this guide covers essential aspects that designers, engineers, and manufacturers need to know.
This comprehensive guide explores the importance of proper wall thickness design in injection molding, offering insights into best practices, common challenges, and solutions for optimizing part production.
What is Wall Thickness in Injection Molding
Wall thickness is a critical design consideration in the injection molding process, which refers to the cross-sectional thickness of the plastic part being molded.
It is one of the most important design considerations in injection molding because it significantly impacts the manufacturability, cost, quality, and performance of the final part.
What Influences the Wall Thickness
Two key factors influence the wall thickness in injection molding plastic material and parts structure.
- Size and shape – Larger parts generally require thicker walls for structural integrity, while smaller parts can have thinner walls. Complex shapes may need variable thicknesses.
- Plastic material – – Different plastics have varying flow characteristics and cooling rates. Materials with lower viscosity or higher melt flow rates can generally be used with thinner walls.
Here is a chart for you to check the optimal wall thickness for various materials:
Material | Recommended Wall Thickness Range |
ABS | 0.045 – 0.140 in (1.14 – 3.56 mm) |
Acetal (POM) | 0.030 – 0.120 in (0.76 – 3.05 mm) |
Acrylic (PMMA) | 0.025 – 0.500 in (0.64 – 12.7 mm) |
Nylon (PA) | 0.030 – 0.115 in (0.76 – 2.92 mm) |
Polycarbonate (PC) | 0.040 – 0.150 in (1.02 – 3.81 mm) |
Polyethylene (PE) | 0.030 – 0.200 in (0.76 – 5.08 mm) |
Polypropylene (PP) | 0.025 – 0.150 in (0.64 – 3.81 mm) |
Polystyrene (PS) | 0.035 – 0.150 in (0.89 – 3.81 mm) |
What are the Problems with Wall Thickness?
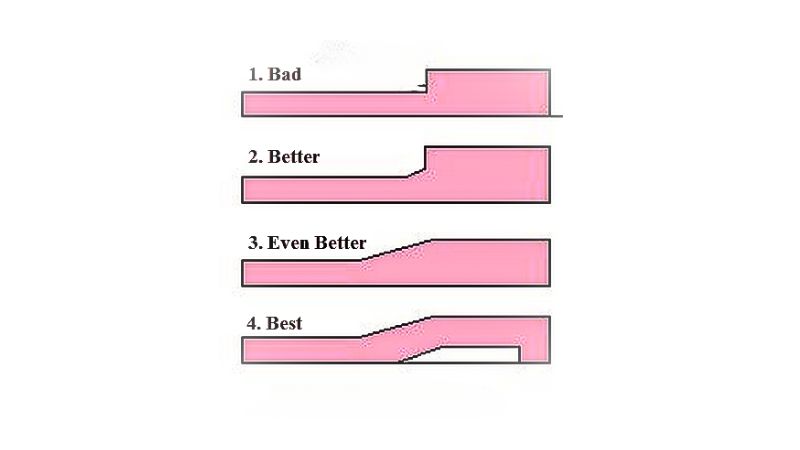
Incorrect wall thickness for injection molding can lead to several defects in the final product:
Defect | Cause | Result |
Warpage | Uneven wall thickness | Different cooling rates lead to internal stresses, causing warping or twisting. |
Sink marks | Thicker sections | Slow cooling allows the surface to sink inward, creating small depressions |
Flow lines | Variations in wall thickness | Different flow rates of molten plastic cause visible streaks or lines on the surface |
Short shots | Thin to thick transitions | Premature cooling prevents the complete filling of thicker areas |
Voids | Thick sections | Air trapping or vacuum pockets form internal voids |
Jetting | Too thin walls | Rapid plastic flow causes snake-like patterns on the part surface |
Structural weakness | Inconsistent wall thickness | Compromises part strength and integrity |
Dimensional inaccuracies | Thickness variations | Uneven cooling leads to parts not meeting specified dimensions |
Increased internal stress | Varying wall thicknesses | Different cooling rates result in higher internal stresses |
Surface defects | Improper wall thickness | Causes surface imperfections like ripples or waviness |
Design Considerations for Achieving Uniform Wall Thickness
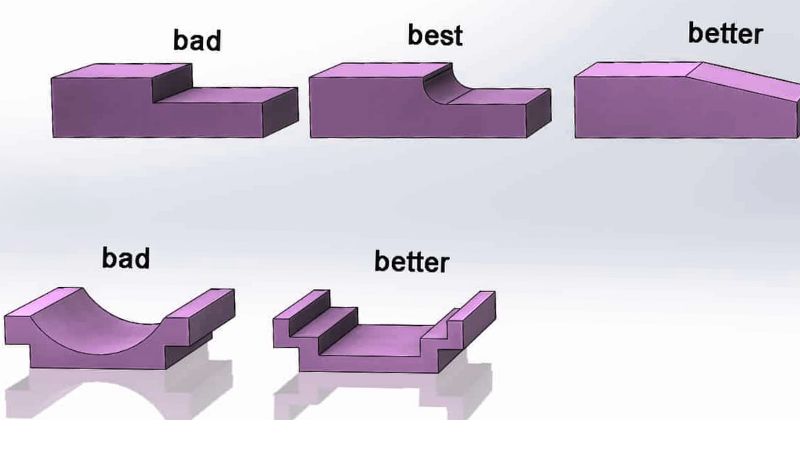
Design for manufacturability (DFM) analysis aids in identifying the optimal uniform thickness to minimize internal stress and improve consistency.
Utilizing Draft Angles to Improve Mold Filling
Draft angles are integral to the design of injection molded components, serving to facilitate easier release of the finished part from the mold. Incorporating a draft angle is not merely a good practice; it’s pivotal for promoting uniform wall thickness.
A recommended external draft angle of 0.5-1.5 degrees and an internal angle of 0.5 degrees can greatly enhance the mold filling process.
These slight angles allow the material to flow more smoothly and prevent the formation of inconsistent wall thicknesses, which are often the root of various defects within the part.
Addressing Internal Stresses Caused by Non-Uniform Wall Thickness
Disparities in wall thickness can lead to internal stresses within the part as it cools and solidifies. Sections of thicker wall thickness cool at slower rates, causing differential rates of shrinkage that can warp or distort the part.
A uniform thickness throughout the piece is imperative to evenly distribute these stresses and avert potential quality issues.
When designing parts, one must consider the high-risk areas and apply a consistent wall thickness to mitigate internal stress formation.
Recommended Thickness – Minimum
The minimum wall thickness depends on the specific plastic material being used and the size/complexity of the part.
In general:
For small parts and efficient high-volume production, a minimum wall thickness of 0.025-0.030 in (0.64-0.76 mm) is recommended.
For larger parts, a minimum of 0.040-0.050 in (1.0-1.3 mm) is suggested.
The practical minimum wall thickness for conventional injection molding ranges from 0.030-0.040 in (0.76-1.0 mm).
Some specialized thin-wall molding applications can achieve walls as thin as 0.010 in (0.25 mm), but this requires high pressures and limits part size.
Recommended Thickness – Maximum
Excessively thick walls should be avoided in injection molding when possible, as they can lead to defects and inefficiencies.
The general guidelines are:
Most injection molded parts have a maximum wall thickness of 0.125-0.250 in (3.2-6.4 mm).
Walls thicker than 0.250 in (6.4 mm) have a higher risk of sink marks, voids, residual stresses, and warpage.
In some specialized applications, wall thicknesses up to 4.5 in (114 mm) are possible but require very long cycle times.
As a best practice for efficiency and quality, a maximum wall thickness of 0.125-0.160 in (3.2-4.0 mm) is recommended for most parts.
How to Solve Wall Thickness Issues in Molded Parts
Dealing with Thick Wall Sections in Injection Molded Parts
To mitigate this, it’s advisable to maintain a wall thickness that facilitates quick cooling but also delivers sufficient strength. For instance, with PA6 material at 8mm thickness, the total injection molding cycle is approximately 93 seconds, with cooling taking around 70 seconds.
To overcome the challenge of extended cycle times due to thicker walls, employing a technique known as core out can be beneficial. This involves creating hollow sections in the thick wall without compromising the part’s integrity or strength.
How to Handle Thin Walls Without Compromising Part Integrity
Product designers are recommended to design parts with the minimum wall thickness necessary without compromising part integrity.
Thinner wall design requires a thorough understanding of the material’s flow characteristics to prevent defects.
Factors such as injection pressure, mold temperature, and the inclusion of design elements like ribs or gussets can help support thin-walled parts, enhancing their moldability and reducing the potential for warp, sink, or bubbles.