Персонализирано леене под налягане
С най-добрите инструменти за обработка ние експертно изработваме части, за да отговарят на вашите изисквани толеранси и стандарти за качество. Ние тестваме всички продукти, за да гарантираме, че отговарят на спецификациите за вашата индустрия и приложение.
Нашите възможности и капацитет ни позволяват да предоставяме най-добрите в класа услуги за леене под налягане по поръчка. Ние работим в тясно сътрудничество с всеки клиент, за да разберем неговия проект и да ги напътстваме при избора на правилните персонализирани форми и дизайни.
Независимо дали имате нужда от малка партида прототипни части или пълномащабно производство, ние предоставяме персонализирани решения, съобразени с вашите нужди. Нашият опит в персонализираното формоване ни позволява постоянно да произвеждаме висококачествени компоненти, които поддържат успеха на вашия бизнес.
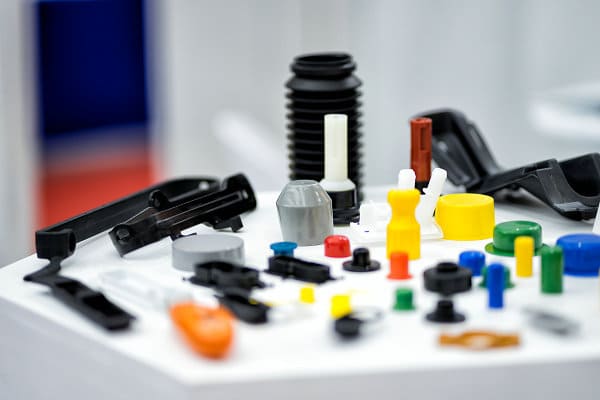
Поискайте оферта
Персонализирано леене под налягане
Шприцоването е рентабилен производствен процес за големи обеми пластмасови части по поръчка. Процесът на леене под налягане включва вмъкване на разтопена пластмаса в инструмент за формоване и отстраняване на втвърдената част след това. Цикълът се повтаря няколко пъти, намалявайки разходите за формоване и по този начин цената на всяка единица.
Тъй като процесът на леене под налягане използва подобен инструмент за формоване за всяка част, той осигурява постоянно качество във всеки продукт. Освен това, леенето под налягане има голямо разнообразие от лакове, материали, козметика и цветове в сравнение с 3D печат или CNC машинна обработка.
Услугите за шприцване на пластмаса по поръчка на Moldie са единствени по рода си. Ние предлагаме изключителни услуги, които надминават очакванията на нашите клиенти. След като получим вашата поръчка, ние намираме подходящия доставчик за шприцоване, който да формира частите по желания от вас начин на подходяща цена и без компромис с дизайна.
Освен това предлагаме гъвкави услуги. Разполагаме със сложни инструменти, екип от професионалисти и ресурси, които предоставят персонализирани части за клиенти в различни индустрии. Освен това работим в кратки срокове. Всички наши процеси са рационализирани. Това гарантира, че ще получите поръчката си в желаното време.
Предимствата на индивидуалното шприцване
Пластмасовото шприцоване предлага множество предимства, включително следните:
1. Това е рентабилно
Пластмасовото шприцване е автоматизиран процес. Следователно разходите за труд са относително ниски в сравнение с други методи за производство на пластмаса. Също така, леенето под налягане произвежда частите на високо ниво с висока производителност, като по този начин намалява производствените разходи поради своята ефективност.
2. Пластмасовото леене под налягане предлага подобрена здравина
Получените пластмасови шприцовани части от процеса на шприцване имат повишена здравина. Това е така, защото можете да използвате пълнители в шприцформи. Тези пълнители намаляват плътността на пластмасата по време на формоването и добавят по-голяма здравина към формованите части.
3. Предлага гъвкавост по отношение на материала и цвета
В днешно време много материали са съвместими с процеса на формоване под налягане на пластмаса. С всички налични опции можете лесно да изберете материал с подходящите химични, физични и механични свойства. Освен това можете да оцветите пластмасите с помощта на няколко системи за оцветяване.
4. Пластмасовото леене под налягане поддържа сложни геометрии с тесни допуски
Персонализираното леене под налягане позволява генерирането на големи обеми и последователни, сложни части. За да увеличите максимално ефективността на шприцоването на голям обем и да оптимизирате точността и качеството на вашите порции, трябва да имате предвид елементите на дизайна. С подходящ дизайн можете постоянно да произвеждате висококачествени части.
С леенето под налягане можете бързо да получите повтарящи се части с тесни допуски, осигурявайки ви прецизни продукти за множество приложения и сравними с машинните части с ЦПУ.
5. Води до намалени отпадъци
Процесът на шприцоване на пластмаса генерира по-малко материални отпадъци след производството в сравнение с конвенционалното производство. Освен това можете да смилате и рециклирате всяка отпадъчна пластмаса за бъдеща употреба.
6. Персонализираните пластмасови корнизи предлагат няколко покрития
Повечето от формованите части имат мека повърхност, почти същата като желания краен вид. Гладкият външен вид обаче е подходящ само за някои приложения. В зависимост от свойствата на материала, методът на леене под налягане произвежда покрития, които не се нуждаят от вторични действия. Можете да добавите уникални текстури, да имате матови покрития или да имате гравюри.
7. Осигурява висока повторяемост
Друго значително предимство на персонализираното шприцоване е, че е много повторяемо. След като създадете своята форма, можете да генерирате множество подобни части, преди да поддържате инструмента си. Това води до ниска производствена цена.
8. Той е много ефективен с бързо производство
Инжекционното формоване по поръчка е сред най-бързите производствени методи. Производството е високо, което го прави по-ефективен и рентабилен. Най-вече скоростта зависи от сложността на дизайна и размера на вашата форма, но типичната форма отнема около 5-20 минути.
Това насърчава производството на повече форми за ограничено време, като по този начин увеличава маржовете на печалба. Освен това някои форми имат множество кухини, което води до производство на повече части в един цикъл на формоване.
Възможности за леене под налягане
По отношение на персонализираните възможности за шприцване на пластмаса, ние сме горди да бъдем сред водещите компании за леене под налягане, които предоставят уникални и точно дефинирани части, които могат да подобрят машините и процедурите в различни основни компании в световен мащаб.
Нашите възможности за леене под налягане ни позволяват да произвеждаме ясно оформени части, които не могат да бъдат създадени с помощта на други методи. Ние използваме машини с много кухини, единични и фамилни машини, за да произвеждаме висококачествени шприцовани продукти рентабилно.
Освен това работим в тясно сътрудничество с вас, за да планираме и организираме иновативни решения. Ние сме експерти в преобразуването на метал в пластмаса, издръжливостта и дизайна на компонентите, като намаляваме производственото време и разходите, като същевременно повишаваме ефективността. Известни сме с нашата специфична процедура за намаляване на разходите и времето за изпълнение и увеличаване на производствените възможности на различни индустрии.
Процес на леене под налягане
Персонализираното шприцване на пластмаса се нуждае от три основни елемента – суров пластмасов материал, машина за леене под налягане и форма. Формите за шприцване на пластмаса са съставени от високоякостни стоманени и алуминиеви елементи, програмирани да функционират в две половини. Всяка половина се сглобява вътре в машината за формоване, за да образува персонализирана пластмасова част.
След това машината инжектира разтопена пластмаса във формата, където тя се втвърдява, за да образува крайния продукт. Персонализираният процес на леене под налягане следва стриктни спецификации и се постига в следните стъпки:
1. Затягане
Първата стъпка от метода на леене под налягане е затягането. Обикновено шприцформите са направени от две половини. В тази стъпка машината затваря тези половини, преди пластмасата да бъде поставена във формата, за да предотврати отварянето на матрицата по време на стъпката на инжектиране.
2. Инжектиране
В тази стъпка сурова пластмаса, обикновено под формата на малки пелети, се вкарва в машината за леене под налягане в секцията на захранващата зона на възвратно-постъпателния винт. Температурата и компресията загряват пластмасовия материал, докато винтът предава пластмасовите пелети през нагретите зони на цевта на машината.
Количеството разтопена пластмаса, предадено към предната част на винта, се измерва точно, тъй като това е количеството, което ще образува крайната част след инжектирането.
Когато подходящото количество разтопени пластмасови пелети пристигне в предната част на винта и формата е добре захваната, машината я вкарва във формата, като я задвижва до последната част на кухината под високо налягане.
3. Охлаждане
След като разтопената пластмаса докосне вътрешните повърхности на формата, тя се охлажда. Методът на охлаждане втвърдява формата и здравината на прясно формованата пластмасова част. Времето за охлаждане, необходимо за всяко формовано пластмасово парче, зависи от дебелината на стената, термодинамичните свойства на пластмасата и необходимостта от размери на персонализираните части.
4. Изтласкване
След охлаждане машината освобождава и отваря пластмасовата шприцформа. Устройството е снабдено с механични механизми, които работят с компоненти, разработени в пластмасовата шприцформа за отстраняване на частта. На този етап изработената по поръчка част се изтласква и формата е готова за следващия ход, когато новата част бъде напълно извадена.
Персонализирани пластмасови материали за леене под налягане
Персонализираните пластмасови материали за леене под налягане се категоризират по следните начини:
1. Твърди пластмасови материали
По-долу са някои материали в тази категория:
- Полиакриламид (PARA)
Това се смесва главно с пълнежи като минерални влакна или стъкло. Той генерира твърди секции с ниско пълзене и по-бавна скорост на водопоглъщане от найлона. PARA е перфектен за структурни елементи в медицинската електроника и ръчни устройства.
- Поликарбонат (PC)
PC е лек, прозрачен и издръжлив материал, алтернативен на стъклото. Поради неговата висока издръжливост и изключителна устойчивост на удар, повечето индустрии използват персонални компютри в различни приложения, включително електронни устройства, лещи, оборудване за безопасност и др.
- Полиетилен (PE)
Това е потребителски полимер, който можете да избирате въз основа на плътността, което го прави сред най-използваните пластмаси в света. Можете да имате ниска плътност (LDPE), висока плътност (HDPE) или полиетилен терефталат (PET, PETE).
PE пластмасите имат висока еластичност, устойчивост на абразия и химическа устойчивост. Те се използват най-добре за шприцване на по-големи предмети, често използвани в бутилки, филми, тръби, опаковки и др.
- Акрилонитрил бутадиен стирен (ABS)
Това е аморфен термопластичен материал с ниска точка на топене. Съвместим е с оцветители и съдържа безброй опции за текстури и покрития. ABS е много устойчив на удар и здрав. Въпреки това има слаба устойчивост на силно триене, UV лъчи, разтворители и атмосферни елементи. Освен това отделя тежък дим при изгаряне.
ABS се използва най-добре в потребителски стоки, електронни компоненти и покрития, спортно оборудване и автомобилни части.
- Полипропилен (PP)
Това също е друга често използвана пластмаса в световен мащаб. Основно е подобен на PE, но е по-устойчив на топлина и малко по-твърд. При леене под налягане можете да рециклирате този материал и да го комбинирате с други пластмасови материали. Поради ниската си плътност, PP се използва за контейнери за съхранение, живи панти за пластмасови бутилки, електрически инструменти и спортни стоки.
- Термопластичен полиуретан (TPU)
TPU е известен със своята устойчивост на масла, абразия и химикали и способността си да се справя с високи температури. Предлага се в различни степени, включително медицински, индустриални и търговски. По този начин той е най-подходящ за колела, обувки, медицински устройства и електронни корпуси.
- Полифталамид (PPA)
PPA е подгрупа от найлони, които обикновено имат ниска абсорбция на влага и високи точки на топене. Използва се в автомобилни и индустриални приложения, тъй като може да устои на силни химикали. Освен това е добър в корпусите на фаровете и горивните колектори.
- Поливинилиден флуорид (PVDF)
Това е високотемпературен, химически инертен материал. Поради ниското си триене, PCDF се използва в лагери, тръби, водопроводни части, изолация на електрически проводници и обработка на химикали.
- Термопластичен полиолефин (TPO)
TPO има добра химическа устойчивост и е гъвкав, но има по-ниска температурна устойчивост от PP.
- Стирен акрилонитрил (SNA)
SNA е полистирол, който е прозрачен и топлоустойчив. Популярен е в кухненските съдове, дръжките на вратите и домакинските стоки.
- Поливинилхлорид (PVC)
Това е цялостна твърда пластмаса, използвана в гарнитури, опаковки за нехранителни стоки и водопроводни инсталации.
- Полифенилен сулфид, Ryton (PPS)
PPS е високоефективен термопласт, който е силно устойчив на разтворители.
- Ацетал полиоксиметилен (POM)
Този има висока устойчивост на износване, ниско триене и добра устойчивост на влага.
- Полистирен-полифенилови етери (PS-PPE)
PS-PPE показва висока устойчивост на топлина и пламък. Освен това има якост на опън и висока твърдост дори когато е подложен на високи температури.
- Акрилонитрил стирен акрилат (ASA)
Този материал е почти същият като ABS, но има по-висока устойчивост на избледняване и затова се използва за външни цели.
- Полиетилен с ниска плътност (LDPE)
Гъвкав и твърд материал, който не реагира на алкохоли, киселини и основи. Най-подходящ е за щракващи се капаци, контейнери с общо предназначение и тави.
- Целулозен ацетат (CA)
CA е гъвкав материал, който може да се използва във филми, очила или контакт с храни.
- Полимер с течни кристали (LCP)
LCP предлага уникални функции за тънкостенни компоненти и микроформоване. Това е често срещано в медицински устройства и електрически връзки и съединители.
- Полиетилен с висока плътност (HDPE)
Има перфектно съотношение на якост към тегло и химическа устойчивост. HDPE се използва най-вече за изолатори на съединители, контейнери за храна и резервоари за гориво. Може да се използва и във външно оборудване, като например детски площадки.
- Полиамид 6/6, найлон 6 (PA 6/6)
Това осигурява повишена механична якост, отлична устойчивост на топлина, твърдост и химическа устойчивост.
- Полибутилен терефталат (PBT)
Това е популярен електронен изолатор с полиестерна основа. Прилага се най-вече в автомобилостроенето като опция за по-дълго износване на найлон.
- Полиетер етер кетон (PEEK)
PEEK осигурява изключителна якост на опън, която надхвърля повечето пластмаси. Поради тази причина се използва най-вече като лека алтернатива на металните части при приложения с високо напрежение и високи температури.
- Поликарбонат-акрилонитрил бутадиен стирен (PC-ABS)
Както подсказва името, това е комбинация от PC и ABS, която води до инженерна термопластмаса с по-висока якост, която е по-гъвкава от обикновения поликарбонат.
- Полиетеримид (PEI)
Това е известно със своята висока устойчивост на пламък и топлина. Прилага се в повечето медицински цели и е по-рентабилен от PEEK.
- Полиетерсулфон (PES)
PES е твърда и прозрачна пластмаса, която е биосъвместима, стерилизирана и химически инертна. Подходящо е за оборудване, което влиза в контакт с храни, като компоненти на кафе машина. Приложимо е и в индустрии с висока химическа експозиция като автомобилостроенето и космическото производство.
- Полициклохексилендиметилен терефталат (PCT)
Този материал има добра устойчивост на околната среда и ниска абсорбция на влага. Използва се най-вече в превключватели и конектори.
- Поликарбонат-полиетилен терефталат (PC-PET)
Това е комбинация от PC и PET, за да се получи продукт, който е здрав и химически устойчив и може да се използва като заместител на PC-ABS. Издържа на агресивни химикали и разтворители, което го прави идеален за приложения в здравеопазването и спортна екипировка.
- Поликарбонат-полибутилен терефталат (PC-PBT)
Това има сходни характеристики с PC-PET и е популярно в електронни кутии.
- Полиетилен терефталат (PET)
Известен също като PETE, PET е здрава, лека и прозрачна PE смола, използвана в бутилки за сода, буркани, опаковки за храни и др. PET е безопасен за храни и може да се рециклира с код на смола 1.
- Високоустойчив полистирен (HIPS)
Това е универсална, икономична и устойчива на удар пластмаса, направена от каучук и кристален стирен. HIPS е подходящ за хранителни компоненти поради нетоксичните си свойства.
- Полиметилметакрилат (PMMA)
PMMA е подобна на холове пластмаса, която е прозрачна и има добри характеристики на износване. Той е най-подходящ за употреба на открито.
- Полимлечна киселина (PLA)
Това е екологична пластмаса за многократна употреба, която има ниска температура на встъкляване. Популярен е в приложения с кратка употреба.
- полиамид (найлон)
Найлонът осигурява отлични електрически свойства, устойчивост на топлинно износване и химикали и здравина. Медицинската и автомобилната промишленост често използват найлон за персонализирани пластмасови шприцовани части.
2. Еластомерни и каучукови формовани материали
- Термопластични вулканизати (TPV)
TPV е твърд термопластичен материал, съдържащ части от мека напречно свързана гума, разпръснати по цялата му полимерна матрица. TPV осигурява гладко усещане, висока степен на компресия и матово покритие. Прилага се в брони, приложения под капака, уплътнения, ботуши и втулки.
- Термопластичен полиуретан (TPU)
TPU е известен със своята добра чистота, средна до висока твърдост, добро износване, разкъсване, устойчивост, абразия и умерена компресия. Той е идеален за приложения на открито, включително колела за скейтборд, гъвкави гуми, защитни калъфи, устойчиви на атмосферни влияния уплътнения и медицински устройства.
- Полиетер блок амид (PEBA)
PEBA е изработена от твърди полиамидни блокове, които се колебаят с меки еластомерни блокове. Има добра устойчивост на удар, пълзене и умора при огъване. Освен това има ниски компресионни комплекти и може да се развива добре при високи температури. Пяните PEBA се използват в спортно оборудване, подплънки, стелки за обувки, електроника и медицинско оборудване.
- Термопластичен еластомер (TPE)
Това е широка група от еластомери, които действат като термореактивен материал с еластичност и висока гъвкавост, но се държат като термопласт по време на формоване.
- Течна силиконова гума (LSR)
Силиконите са гъвкави гумени материали с висока устойчивост на топлина, невероятна гъвкавост и осигуряващи храна и биосъвместимост. LSR се използва в потребителски продукти, автомобилостроене, космическа индустрия и медицински устройства.
- Етилен пропилей диен мономерен каучук (EPDM)
Това е сред най-функционалните каучукови еластомери с превъзходна химическа и топлинна устойчивост и свойства за уплътняване на влагата. Обикновено се използва в електрически изолатори, уплътнения, автомобилни уплътнения и О-пръстени.
Класове форми за шприцване
Имаме следните класове форми за формоване:
1. SPI Mold Класификация
Конвенционалните инструменти за шприцформи са описани от класове от клас 105 (прототип) до клас 101 (производство в голям обем). Тези класове форми подпомагат управлението както на доставчиците на леене под налягане, така и на клиентите по отношение на общите изисквания и обхват на инструменти. По-долу е схема на различните класове:
- Клас 105 мухъл
Това е матрица под 500 цикъла и е генерирана по възможно най-евтиния начин за създаване на минимално количество прототипни части. Този клас се нарича още инструменти от клас V.
- Клас 104 мухъл
Този клас е под 100 000 цикъла и е нископроизводителна форма. Използва се само за ограничено производство, за предпочитане с неабразивни материали.
- Клас 103 плесен
Това е под 500 000 цикъла и е популярно за ниски до средни производствени изисквания. Това е и най-популярният ценови диапазон.
- Клас 102 плесен
Това е първокласна матрица на висока цена, използвана за средно до високопроизводителни инструменти. Той е идеален за абразивни материали или участъци, изискващи голяма толерантност.
- Клас 101
Това е над 1 000 000 цикъла и е проектирано за изключително високо производство. Това е матрицата с най-висока цена и е създадена само с висококачествени материали.
Персонализирани покрития на шприцформи
Предлагат се различни варианти на повърхностно покритие за формовани по поръчка пластмасови части. Процесите на повърхностно довършване за леене под налягане могат да помогнат за намаляване или увеличаване на грубостта на детайла. Например по-грубите покрития са идеални за определени механични части, докато лъскавата текстура пасва на естетически части като играчки.
Обществото на пластмасовата промишленост (SPI) разработи индустриални стандарти за пластмасови покрития за леене под налягане, както е посочено по-долу:
1. Гланцово покритие на повърхността за леене под налягане
Формованите пластмасови части могат да бъдат направени по-лъскави, като се използва довършителен процес като полиране с диамант. При такъв метод компания за леене под налягане използва насипен абразивен материал върху работно колело. След това те използват това върху части с минимална агресия, произвеждайки части с възможно най-лъскавите покрития.
2. Полугланцово покритие на повърхността за леене под налягане
Това покритие е подходящо за части, които се нуждаят от малко блясък. Използва се шкурка с песъчинки. Този процес работи добре с голям брой пластмаси за леене под налягане. Използва се и за производство на части с висока естетика, подходящи за потребителски продукти.
3. Матово шприцоване на повърхността
Този процес включва премахване на следи от машинна обработка от формовани части, без да се генерира гланцово покритие. Идеален е за части, които нямат естетическа стойност, но се нуждаят от последователно повърхностно покритие. Предлага висококачествена повърхностна текстура на мухъл и не показва никакви забележими следи.
4. Текстурирано покритие на повърхността за леене под налягане
В някои случаи може да се нуждаете от много грубо покритие, за да увеличите триенето, като например при механична употреба. В такъв случай можете да използвате процес на пясъкоструене, за да приложите грапава повърхност. Пясъкоструенето използва сгъстен въздух, за да насочи абразивния материал към детайла със сила, заграпавявайки повърхността му.
Други обичайни покрития включват следното:
- Шлифоване
- Анодиране
- Галванопластика
- Полиране
- Силово покритие
- Рисуване
С правилното персонализирано пластмасово формовано покритие със сигурност ще имате издръжливи персонализирани пластмасови части. Работата с нас ви позволява да постигнете това и да впечатлите клиентите си. Нашият екип от експерти е добре запознат с всички покрития и може да предложи подходящи термопластични материали и покрития за конкретни продукти. Затова си партнирайте с нас днес и спечелете конкурентно предимство с най-добрите услуги.
Инспекции на качеството и опции за довършителни работи за персонализирани формовани части
Когато поискате оферта за леене под налягане, можете да изберете от следните опции в зависимост от нуждите на вашето приложение:
1. Предлагат се инспекции на качеството за производствени поръчки при поискване
Имате следните опции:
- Инспекция на CMM в процеса и мониторинг на машината
- Научен доклад за развитието на процеса на формоване
- Първа инспекция на артикул (FAI) и доклад за капацитета на процеса с GD&T
- Проектиране за обратна връзка за технологичност (DFM)
2. Постобработка
При тази опция имате:
- Тампонен печат
- Сглобяване на компоненти
- Вложки с резба
- Лазерно гравиране
- Текстуриране на мухъл
Често задавани въпроси
1. Защо пластмасовите форми за шприцване струват толкова много?
Различни фактори допринасят за високата цена на пластмасовите шприцформи. Един от основните фактори са самите форми. За да произвеждате висококачествени пластмасови части, трябва да използвате висококачествена шприцформа. Формите за шприцване на пластмаса са изработени от машинно обработени елементи, генерирани от различни метали като закалени стомани за формовки и алуминий за самолети.
След това формите се проектират и създават от експерти, известни също като производители на форми. Тези хора са прекарали няколко години в учене на занаята на производство на калъпи. По този начин те са добре запознати с този процес на производство на висококачествени форми. Тяхното възнаграждение допринася за високата цена на пластмасовите шприцформи.
Освен това, производителите на форми се нуждаят от много скъпи инструменти, за да изпълняват работата си, като CNC машини, авангарден софтуер, прецизни приспособления и инструменти. Други фактори, които допринасят за високата цена на шприцването на пластмаса по поръчка, включват следното:
Дизайн на мухъл
Персонализираният дизайн за леене под налягане оказва значително влияние върху цената му. Процедурата за шприцване на пластмаса по поръчка изисква голям натиск, когато машината инжектира пластмасата в кухините на формата. Без високото налягане шприцованите части няма да имат желаните повърхностни покрития и могат да бъдат с неправилни размери.
Изисквания за конструкцията на матрицата
Друг важен фактор, свързан с високата цена на шприцформите, са изискванията за конструкцията на матрицата. Конструкцията трябва да е точна, за да може шприцформата да функционира правилно по време на процедурата за шприцване на пластмаса по поръчка. Въпреки че формите са очертани като две половини, сърцевина и страна на кухина, няколко прецизни части обикновено представляват всяка половина.
Почти всеки от прецизно обработените елементи на матрицата, които ще сглобят и произведат вашите персонализирани формовани части, са оборудвани с толеранси от 0,025 mm или +/-0,001''. Конвенционалната копирна хартия е с дебелина 0,089 мм или 0,0035 инча. Следователно, производителят на форми трябва да бъде много прецизен, за да нареже вашата копирна хартия на три ултратънки парчета и точно да изгради вашата форма.
Сложността на частта
Колкото по-сложна е вашата част, толкова по-скъпа ще бъде вашата шприцформа. Освен това формата може да бъде много твърда или дори невъзможна за модифициране, след като е създадена чрез пресоване. Това прави предизвикателство за вас да промените дизайна.
Формовъчни материали
За да може вашата форма да издържи на натиска, на който е подложена по време на персонализираната процедура за леене под налягане, тя трябва да бъде изработена от алуминий и стомана с най-високо качество. Освен това, той трябва да бъде направен така, че да издържа на силите на затягане и инжектиране.
2. Как да разберете дали леенето под налягане е правилният процес за даден продукт?
Различни фактори влияят върху решението ви дали персонализираното шприцване е подходящо за вас. Тези фактори включват вашия бюджет, броя на необходимите части, геометрията на частта и приложението на частта.
3. Колко време отнема изграждането на нова форма?
Може да отнеме средно 8-10 седмици, в зависимост от сложността на дизайна и кухините на формата.
4. Ще се поддържат ли формите от моя страна между производствените серии?
По-малко вероятно е формите да се поддържат между производствените серии. Това обаче може да зависи от фактори като материал за шприцоване, условия на работа, времена на цикъла и време между производствените серии. Можете да използвате тези фактори, за да определите дали можете да поддържате формите си по всяко време.