Цустом Ињецтион Молдинг
Са врхунским алатима за машинску обраду, ми стручно израђујемо делове који одговарају вашим захтеваним толеранцијама и стандардима квалитета. Ми тестирамо све производе како бисмо били сигурни да су усклађени са спецификацијама за вашу индустрију и примену.
Наше могућности и капацитет нам омогућавају да пружимо најбоље у класи услуге бризгања по мери. Блиско сарађујемо са сваким клијентом како бисмо разумели њихов пројекат и водили га у одабиру правих прилагођених калупа и дизајна.
Било да вам је потребна мала серија прототипних делова или производња у пуном обиму, ми пружамо персонализована решења прилагођена вашим потребама. Наша стручност у обликовању по мери омогућава нам да доследно производимо висококвалитетне компоненте које подржавају успех вашег пословања.
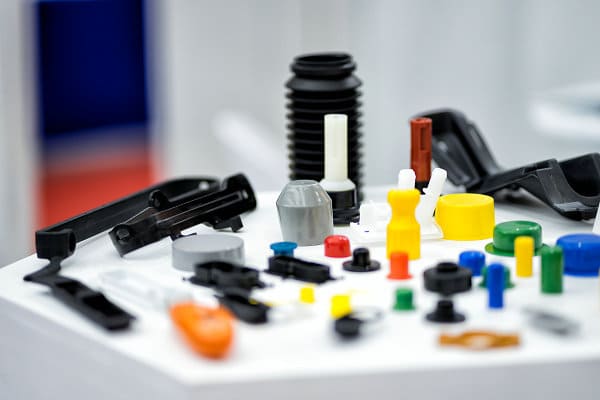
Затражите понуду
Цустом Ињецтион Молдинг
Ињекционо ливење је исплатив производни процес за велике количине прилагођених пластичних делова. Процес бризгања подразумева уметање растопљене пластике у алат за калуп и уклањање очврслог дела након тога. Циклус се понавља неколико пута, смањујући цену калупа, а самим тим и цену сваке јединице.
Пошто процес бризгања користи сличан алат за калупе за сваки део, обезбеђује доследан квалитет у сваком производу. Поред тога, бризгање има широк избор полира, материјала, козметике и боја у поређењу са 3Д штампањем или ЦНЦ обрадом.
Услуге бризгања пластике Молдие по мери су јединствене. Нудимо изузетне услуге које превазилазе очекивања наших купаца. Након што примимо вашу поруџбину, налазимо одговарајућег добављача бризгања који ће обликовати делове на начин на који желите по одговарајућој цени и без угрожавања дизајна.
Поред тога, нудимо флексибилне услуге. Имамо софистициране алате, тим професионалаца и ресурсе који обезбеђују персонализоване делове за клијенте у различитим индустријама. Осим тога, радимо у кратком року. Сви наши процеси су поједностављени. Ово осигурава да добијете своју поруџбину у жељеном року.
Предности прилагођеног бризгања
Ињекционо бризгање пластике нуди бројне предности, укључујући следеће:
1. То је исплативо
Ињекционо бризгање пластике је аутоматизован процес. Због тога су трошкови рада релативно ниски у поређењу са другим методама производње пластике. Такође, бризгање производи делове на високом нивоу са великом излазном стопом, чиме се смањују трошкови производње због своје ефикасности.
2. Ињекционо бризгање пластике нуди побољшану чврстоћу
Настали пластични делови од ливеног бризгања из процеса бризгања имају повећану чврстоћу. То је зато што можете користити пунила у калупима за бризгање. Ова пунила смањују густину пластике током обликовања и дају већу чврстоћу обликованим деловима.
3. Нуди флексибилност у материјалу и боји
Данас су бројни материјали компатибилни са процесом бризгања пластике. Са свим доступним опцијама, лако можете одабрати материјал са одговарајућим хемијским, физичким и механичким својствима. Осим тога, пластику можете обојити помоћу неколико система за бојење.
4. Ињекционо преливање пластике подржава сложене геометрије са уским толеранцијама
Прилагођено бризгање омогућава генерисање великих и конзистентних, сложених делова. Да бисте максимизирали ефикасност бризгања велике запремине и оптимизовали тачност и квалитет ваших порција, морате узети у обзир елементе дизајна. Са одговарајућим дизајном, можете доследно производити висококвалитетне делове.
Са бризгањем, можете брзо да добијете поновљиве делове са уским толеранцијама, пружајући вам прецизне производе за бројне примене и упоредиве са деловима ЦНЦ машина.
5. Води до смањења отпада
Процес бризгања пластике ствара мање отпада након производње него конвенционална производња. Такође, можете поново самлети и рециклирати било коју отпадну пластику за будућу употребу.
6. Прилагођено пластично обликовање нуди неколико завршних обрада
Већина обликованих делова има меку завршну обраду, скоро исту као и жељени коначни изглед. Међутим, глатки изглед је погодан само за неке апликације. У зависности од својстава материјала, метода бризгања даје завршне слојеве којима није потребна секундарна радња. Можете додати јединствене текстуре, имати мат завршну обраду или имати гравуре.
7. Пружа високу поновљивост
Још једна значајна предност прилагођеног бризгања је што се може поновити. Након што направите свој калуп, можете да генеришете бројне сличне делове пре него што одржавате свој алат. Ово резултира ниским трошковима производње.
8. Веома је ефикасан уз брзу производњу
Прилагођено бризгање је међу најбржим производним методама. Производни учинак је висок, што га чини ефикаснијим и исплативијим. Углавном, брзина зависи од сложености дизајна и величине вашег калупа, али типичан калуп траје око 5-20 минута.
Ово промовише производњу више калупа у ограниченом времену, чиме се повећавају профитне марже. Поред тога, неки калупи имају више шупљина, што доводи до тога да се више делова производи у једном циклусу обликовања.
Могућности бризгања
Што се тиче прилагођених могућности бризгања пластике, поносни смо што смо међу водећим компанијама за бризгање пластике које обезбеђују јединствене и прецизно дефинисане делове који могу да унапреде машине и процедуре у различитим кључним компанијама широм света.
Наше могућности бризгања омогућавају нам да производимо делове јасног облика који се не могу направити другим методама. Користимо машине са више шупљина, појединачне и породичне машине за економично производњу висококвалитетних бризганих производа.
Поред тога, блиско сарађујемо са вама на планирању и организовању иновативних решења. Ми смо експерти за конверзију метала у пластику, издржљивост и дизајн компоненти, смањујући време и трошкове производње уз повећање ефикасности. Познати смо по нашој посебној процедури за смањење трошкова и времена испоруке и повећање производних могућности различитих индустрија.
Процес бризгања
За бризгање пластике по мери потребна су три основна елемента – сирови пластични материјал, машина за бризгање пластике и калуп. Калупи за бризгање пластике се састоје од челичних и алуминијумских елемената високе чврстоће програмираних да функционишу у две половине. Свака половина се склапа унутар машине за калупљење да би формирала прилагођени пластични део.
Након тога, машина убризгава растопљену пластику у калуп, где се учвршћује и формира коначни производ. Прилагођени процес бризгања следи строге спецификације и постиже се у следећим корацима:
1. Стезање
Први корак методе бризгања је стезање. Генерално, калупи за бризгање су направљени од две половине. У овом кораку, машина затвара ове половине пре него што се пластика убаци у калуп како би спречила отварање калупа током корака убризгавања.
2. Ињекција
У овом кораку, сирова пластика, типично у облику малих пелета, се убацује у машину за бризгање у делу зоне напајања клипног вијка. Температура и компресија загревају пластични материјал док завртањ преноси пластичне пелете кроз загрејане делове цеви машине.
Количина истопљене пластике која се преноси на предњи део завртња је тачно мерена, јер је то количина која ће формирати завршни део након убризгавања.
Када одговарајућа количина истопљених пластичних пелета стигне на предњи део шрафа, а калуп је добро стегнут, машина га убацује у калуп, гурајући га до последњег дела шупљине под високим притиском.
3. Хлађење
Када растопљена пластика додирне унутрашње површине калупа, хлади се. Метода хлађења учвршћује облик и жилавост свеже обликованог пластичног дела. Време хлађења које је потребно за сваки пластични обликовани комад зависи од дебљине зида, термодинамичких својстава пластике и потребе за димензијама прилагођених делова.
4. Избацивање
Након хлађења, машина се откључава и отвара калуп за бризгање пластике. Уређај је опремљен механичким елементима који раде са компонентама развијеним унутар калупа за бризгање пластике за уклањање дела. У овој фази, прилагођени део се истискује, а калуп је спреман за следећи потез када се нови део потпуно избаци.
Прилагођени материјали за бризгање пластике
Прилагођени материјали за бризгање пластике су категорисани на следеће начине:
1. Чврсти пластични материјали
Испод су неки материјали из ове категорије:
- полиакриламид (ПАРА)
Ово се углавном меша са испунама као што су минерална влакна или стакло. Генерише круте делове са малим пузањем и споријом стопом апсорпције воде од најлона. ПАРА је савршен за структурне елементе у медицинској електроници и ручним уређајима.
- Поликарбонат (ПЦ)
ПЦ је лаган, провидан и издржљив материјал алтернатива стаклу. Због своје велике издржљивости и екстремне отпорности на удар, већина индустрија користи рачунаре у неколико апликација, укључујући електронске уређаје, сочива, сигурносну опрему итд.
- полиетилен (ПЕ)
Ово је полимер потрошачког квалитета који можете изабрати на основу густине, што га чини једном најкоришћенијом пластиком широм света. Можете имати ниске густине (ЛДПЕ), високе густине (ХДПЕ) или полиетилен терефталат (ПЕТ, ПЕТЕ).
ПЕ пластика има високу еластичност, отпорност на абразију и хемијску отпорност. Најбоље се користе за бризгање већих предмета, који се често користе у боцама, филмовима, цевима, амбалажи итд.
- акрилонитрил бутадиен стирен (АБС)
Ово је аморфни термопластични материјал са ниском тачком топљења. Компатибилан је са бојама и садржи безброј текстура и опција за завршну обраду. АБС је веома отпоран на ударце и робустан. Међутим, има слабу отпорност на високо трење, УВ зраке, раствараче и временске елементе. Такође, приликом сагоревања ослобађа јак дим.
АБС се најбоље користи у роби широке потрошње, електронским компонентама и облогама, спортској опреми и аутомобилским деловима.
- полипропилен (ПП)
Ово је такође још једна пластика која се често користи широм света. Углавном је сличан ПЕ, али је отпорнији на топлоту и нешто тврђи. У бризгању овај материјал можете рециклирати и комбиновати са другим пластичним материјалима. Због своје мале густине, ПП се користи за контејнере за складиштење, живе шарке за пластичне боце, електричне алате и спортску опрему.
- Термопластични полиуретан (ТПУ)
ТПУ је познат по својој отпорности на уља, абразију и хемикалије и својој способности да се носи са високим температурама. Долази у различитим класама, укључујући медицинске, индустријске и комерцијалне. Дакле, најбоље одговара точковима, ципелама, медицинским уређајима и електронским кућиштима.
- полифталамид (ППА)
ППА је подгрупа најлона који обично имају ниску апсорпцију влаге и високе тачке топљења. Користи се у аутомобилској и индустријској примени јер може да одоли јаким хемикалијама. Поред тога, добар је у кућиштима фарова и разводницима горива.
- Поливинилиден флуорид (ПВДФ)
Ово је хемијски инертан материјал високе температуре. Због свог малог трења, ПЦДФ се користи у лежајевима, цевима, водоводним деловима, изолацији електричних жица и руковању хемикалијама.
- Термопластични полиолефин (ТПО)
ТПО има добру хемијску отпорност и флексибилан је, али има нижу температурну отпорност од ПП.
- Стирен акрилонитрил (СНА)
СНА је полистирен који је провидан и отпоран на топлоту. Популарно је у кухињском посуђу, квакама на вратима и кућним производима.
- поливинил хлорид (ПВЦ)
Ово је свеобухватна крута пластика која се користи за обрезивање, паковање непрехрамбених производа и водовод.
- Полифенилен сулфид, Ритон (ППС)
ППС је термопласт високих перформанси који је веома отпоран на раствараче.
- ацетал полиоксиметилен (ПОМ)
Овај има високу отпорност на хабање, ниско трење и добру отпорност на влагу.
- Полистирен-полифенил етри (ПС-ППЕ)
ПС-ППЕ показује високу отпорност на топлоту и пламен. Штавише, има затезну чврстоћу и високу крутост чак и када је изложен високим температурама.
- Акрилонитрил стирен акрилат (АСА)
Овај материјал је скоро исти као АБС, али има већу отпорност на бледење и стога се користи за спољашње сврхе.
- Полиетилен ниске густине (ЛДПЕ)
Флексибилан и чврст материјал који не реагује на алкохоле, киселине и базе. Најприкладнији је за затвараче, посуде опште намене и тацне.
- целулозни ацетат (ЦА)
ЦА је флексибилан материјал који се може користити у филму, наочарима или у контакту са храном.
- Полимер са течним кристалом (ЛЦП)
ЛЦП нуди јединствене карактеристике за компоненте са танким зидовима и микро-преливање. Уобичајено је у медицинским уређајима, електричним интерконекцијама и конекторима.
- Полиетилен високе густине (ХДПЕ)
Има савршен однос снаге и тежине и хемијску отпорност. ХДПЕ се углавном користи за изолаторе конектора, посуде за храну и резервоаре за гориво. Такође се може користити у спољној опреми као што су игралишта.
- Полиамид 6/6, најлон 6 (ПА 6/6)
Ово обезбеђује повећану механичку чврстоћу, одличну стабилност на топлоту и крутост и хемијску отпорност.
- полибутилен терефталат (ПБТ)
Ово је популаран електронски изолатор са полиестерском базом. Углавном се примењује у аутомобилској индустрији као опција за дуже ношење најлона.
- полиетар етер кетон (ПЕЕК)
ПЕЕК пружа изванредну затезну чврстоћу која превазилази већину пластике. Из тог разлога, углавном се користи као лагана алтернатива металним деловима у апликацијама са високим стресом и високим температурама.
- Поликарбонат-акрилонитрил бутадиен стирен (ПЦ-АБС)
Као што име говори, ово је комбинација ПЦ-а и АБС-а која резултира инжењерском термопластиком веће чврстоће која је флексибилнија од обичног поликарбоната.
- полиетеримид (ПЕИ)
Ово је познато по својој високој отпорности на пламен и топлоту. Примењује се у већини медицинских употреба и исплативији је од ПЕЕК-а.
- полиетерсулфон (ПЕС)
ПЕС је чврста и провидна пластика која је биокомпатибилна, стерилизујућа и хемијски инертна. Погодан је за опрему за контакт са храном као што су компоненте апарата за кафу. Такође је применљив у индустријама са високом хемикалијом као што су аутомобилска и ваздухопловна индустрија.
- Полициклохексилендиметилен терефталат (ПЦТ)
Овај материјал има добру еколошку стабилност и ниску апсорпцију влаге. Углавном се користи у прекидачима и конекторима.
- Поликарбонат-полиетилен терефталат (ПЦ-ПЕТ)
Ово је комбинација ПЦ-а и ПЕТ-а да би се добио производ који је чврст и хемијски отпоран и који се може користити као замена за ПЦ-АБС. Отпоран је на јаке хемикалије и раствараче, што га чини савршеним за примену у здравству и спортску опрему.
- Поликарбонат-полибутилен терефталат (ПЦ-ПБТ)
Ово има сличне карактеристике као ПЦ-ПЕТ и популарно је у електронским кућиштима.
- Полиетилен терефталат (ПЕТ)
Такође познат као ПЕТЕ, ПЕТ је јака, лагана и прозирна ПЕ смола која се користи у боцама соде, теглама, амбалажи за храну итд. ПЕТ је безбедан за храну и може се рециклирати са шифром смоле 1.
- Полистирен високог утицаја (ХИПС)
Ово је свестрана, економична пластика отпорна на ударце која је направљена од гуме и кристалног стирена. ХИПС је погодан за компоненте за храну због својих нетоксичних својстава.
- Полиметил метакрилат (ПММА)
ПММА је пластика налик на хале која је прозирна и има добре карактеристике хабања. Најбоље је за употребу на отвореном.
- Полимлечна киселина (ПЛА)
Ово је еколошки прихватљива пластика за вишекратну употребу која има ниску температуру преласка стакла. Популарно је у апликацијама кратке употребе.
- полиамид (најлон)
Најлон пружа одличне електричне особине, отпорност на топлотно хабање и хемикалије и снагу. Медицинска и аутомобилска индустрија често користе најлон за прилагођене делове бризгане пластике.
2. Еластомер и гума обликовани материјали
- Вулканизатори термопласта (ТПВ)
ТПВ је тврди термопластични материјал који садржи делове мекане попречно повезане гуме раширене по целој полимерној матрици. ТПВ пружа гладак осећај, високу компресију и мат завршну обраду. Примењује се у одбојницима, апликацијама испод хаубе, заптивкама, чизмама и ушицама.
- Термопластични полиуретан (ТПУ)
ТПУ је познат по својој доброј чистоћи, средњој и високој тврдоћи, добром хабању, кидању, отпорности, хабању и умереној компресији. Идеалан је за примену на отвореном, укључујући точкове за скејтборд, флексибилне гуме, заштитне навлаке, заптивке отпорне на временске услове и медицинске уређаје.
- Полиетер блок амид (ПЕБА)
ПЕБА је направљена од тврдих полиамидних блокова који варирају са меким еластомерним блоковима. Има добру отпорност на ударце, пузање и замор савијања. Штавише, има ниске компресије и може добро да напредује под високим температурама. ПЕБА пене се користе у спортској опреми, подметачима, улошцима за ципеле, електроници и медицинској опреми.
- Термопластични еластомер (ТПЕ)
Ово је широка група еластомера који делују као термосет са еластичношћу и великом савитљивошћу, али се понашају као термопласт током обликовања.
- Течна силиконска гума (ЛСР)
Силикони су флексибилни гумени материјали високе отпорности на топлоту, изванредне свестраности и обезбеђују храну и биокомпатибилност. ЛСР се користи у потрошачким производима, аутомобилској индустрији, ваздухопловству и медицинским уређајима.
- Етилен пропилен диен мономер гума (ЕПДМ)
Ово је један од најфункционалнијих гумених еластомера са супериорном отпорношћу на хемикалије и топлоту и карактеристикама заптивања влаге. Обично се користи у електричним изолаторима, заптивкама, аутомобилским заптивкама и О-прстеновима.
Класе калупа за бризгање
Имамо следеће класе калупа за обликовање:
1. СПИ класификација калупа
Конвенционални алати за калупе за бризгање описани су класама од класе 105 (прототип) до класе 101 (производња великог обима). Ове класе калупа помажу у управљању и добављачима и купцима за бризгање калупа у погледу општих захтева и обима алата. Испод је преглед различитих класа:
- Калуп класе 105
Ово је калуп испод 500 циклуса и генерисан је на најјефтинији могући начин да би се створила минимална количина прототипних делова. Ова класа се такође назива алатима класе В.
- Калуп класе 104
Ова класа је испод 100.000 циклуса и представља калуп ниске производње. Користи се само за ограничену производњу, пожељно са неабразивним материјалима.
- Калуп класе 103
Ово је испод 500.000 циклуса и популарно је за потребе ниске до средње производње. То је такође најпопуларнији распон цена.
- Калуп класе 102
Ово је првокласан и скуп калуп који се користи за алате средње до високе производње. Идеалан је за абразивне материјале или делове којима је потребна велика толеранција.
- Разред 101
Ово је преко 1.000.000 циклуса и дизајнирано је за изузетно високу производњу. То је најскупљи калуп и направљен је само од материјала врхунског квалитета.
Прилагођене завршне обраде калупа за убризгавање
Доступни су различити избори површинске обраде за прилагођене пластичне делове. Поступци завршне обраде површина за бризгање могу помоћи у смањењу или повећању грубости дела. На пример, грубље завршне обраде су идеалне за одређене механичке делове, док се сјајна текстура уклапа у естетске делове попут играчака.
Друштво пластичне индустрије (СПИ) осмислило је индустријске стандарде за завршне обраде пластичне бризгане пластике, као што је наведено у наставку:
1. Сјајна површина за бризгање
Обликовани пластични делови се могу учинити сјајнијима коришћењем процеса завршне обраде као што је полирање дијамантом. У таквој методи, компанија за бризгање користи лабави абразивни материјал на радном точку. Након тога, они то користе на деловима са минималном агресивношћу, производећи делове са најсјајнијом могућом завршном обрадом.
2. Полу-сјајна завршна обрада за бризгање
Ова завршна обрада је погодна за делове којима је потребан сјај. Користи се брусни папир. Овај процес добро функционише са великим бројем пластике за бризгање. Такође се користи за производњу високо естетских делова погодних за потрошачке производе.
3. Мат површина за бризгање
Овај процес укључује уклањање трагова обраде са обликованих делова без стварања сјајне завршне обраде. Идеалан је за делове којима недостаје естетска вредност, али им је потребна конзистентна завршна обрада површине. Нуди висококвалитетну текстуру површине калупа и не приказује никакве приметне трагове.
4. Текстурирана површина за бризгање
У неким случајевима, можда ће вам требати веома груба завршна обрада да бисте повећали трење, као у механичкој употреби. У таквом случају можете користити процес пескарења за наношење грубе површине. Пескарење користи компримовани ваздух за усмеравање абразивног материјала на део са силом, чинећи његову површину храпавом.
Друге уобичајене завршне обраде укључују следеће:
- Брушење
- Анодизирање
- Галванизација
- Полирање
- Повер цоатинг
- Сликарство
Са одговарајућом пластичном завршном обрадом по мери, сигурно ћете имати издржљиве пластичне делове по мери. Рад са нама омогућава вам да то постигнете и импресионирате своје купце. Наш тим стручњака је добро упућен у све завршне обраде и може предложити одговарајуће термопластичне материјале и завршне обраде за одређене производе. Стога, сарађујте са нама данас и стекните конкурентску предност уз најбоље услуге.
Инспекције квалитета и опције завршне обраде за прилагођене ливене делове
Када тражите понуду за бризгање калупа, можете изабрати неку од следећих опција у зависности од потреба ваше апликације:
1. Доступне су провере квалитета за производне наруџбе на захтев
Имате следеће опције:
- Инспекција ЦММ-а у процесу и надзор машина
- Извештај о развоју процеса научног обликовања
- Инспекција првог артикла (ФАИ) и извештај о могућностима процеса са ГД&Т
- Дизајнирање за повратне информације о производности (ДФМ)
2. Накнадна обрада
Под овом опцијом, имате:
- Тампон штампа
- Склоп компоненти
- Уметци са навојем
- Ласерско гравирање
- Текстурирање калупа
ФАКс
1. Зашто пластични калупи за бризгање коштају толико?
Различити фактори доприносе високим трошковима калупа за бризгање пластике. Један од главних фактора су сами калупи. Да бисте произвели пластичне делове врхунског квалитета, морате користити висококвалитетни калуп за бризгање. Калупи за бризгање пластике су направљени од машински обрађених елемената генерисаних од различитих метала као што су каљени челици за калупе и алуминијум намењен за авионе.
Калупе затим дизајнирају и креирају стручњаци, познати и као произвођачи калупа. Ови људи су провели неколико година учећи занат израде калупа. Дакле, они су добро упућени у овај процес производње висококвалитетних калупа. Њихова накнада доприноси високој цени калупа за бризгање пластике.
Штавише, произвођачи калупа захтевају веома скупе алате за обављање својих послова, као што су ЦНЦ машине, најсавременији софтвер, прецизна опрема и алати. Други фактори који доприносе високој цени прилагођеног убризгавања пластике укључују следеће:
Моулд Десигн
Прилагођени дизајн бризгања има значајан утицај на његову цену. Прилагођена процедура бризгања пластике захтева велики притисак када машина убризгава пластику у шупљине калупа. Без високог притиска, бризгани делови неће имати жељену завршну обраду и могу бити неисправни у димензијама.
Захтеви за конструкцију калупа
Други значајан фактор повезан са високим трошковима калупа за бризгање јесу захтеви за конструкцијом калупа. Конструкција мора бити прецизна да би калуп за бризгање правилно функционисао током прилагођеног поступка бризгања пластике. Иако су калупи оцртани као две половине, језгро и страна шупљине, неколико прецизних делова обично чине сваку половину.
Скоро сваки од прецизно обрађених елемената калупа који ће саставити и произвести ваше прилагођене обликоване делове је инструментиран на толеранције од 0,025 мм или +/-0,001''. Конвенционални папир за копирање је дебљине 0,089 мм или 0,0035 инча. Због тога, произвођач калупа мора бити веома прецизан да исече ваш папир за копирање на три ултра танка дела и прецизно изгради ваш калуп.
Сложеност дела
Што је ваш део сложенији, то ће ваш калуп за ињекције бити скупљи. Такође, калуп може бити веома тврд или чак немогуће модификовати након што је направљен компресијским обликовањем. Ово вам чини изазовом да промените дизајн.
Моулд Материалс
Да би ваш калуп одолео притисцима којима је подвргнут током прилагођеног поступка бризгања, мора бити направљен од алуминијума и челика врхунског квалитета. Поред тога, мора бити направљен да издржи силе стезања и убризгавања.
2. Како знате да ли је бризгање прави процес за производ?
Различити фактори утичу на вашу одлуку о томе да ли је прилагођено бризгање одговарајуће за вас. Ови фактори укључују ваш буџет, број потребних делова, геометрију дела и примену дела.
3. Колико времена је потребно да се направи нови калуп?
Може потрајати у просеку 8-10 недеља, у зависности од сложености дизајна и шупљина калупа.
4. Да ли ће се калупи са моје стране одржавати између циклуса производње?
Мање је вероватно да ће се калупи одржавати између производних циклуса. Међутим, ово може зависити од фактора као што су материјал калупа за бризгање, услови рада, времена циклуса и време између производних циклуса. Можете да користите ове факторе да бисте утврдили да ли можете да одржавате своје калупе у било ком тренутку.